industry insights
Featured Articles
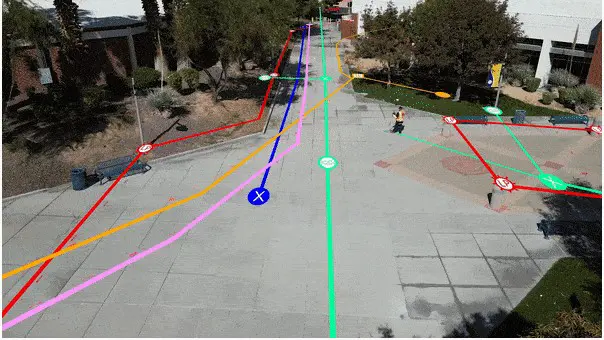
Is Utility Mapping Worth the Cost?
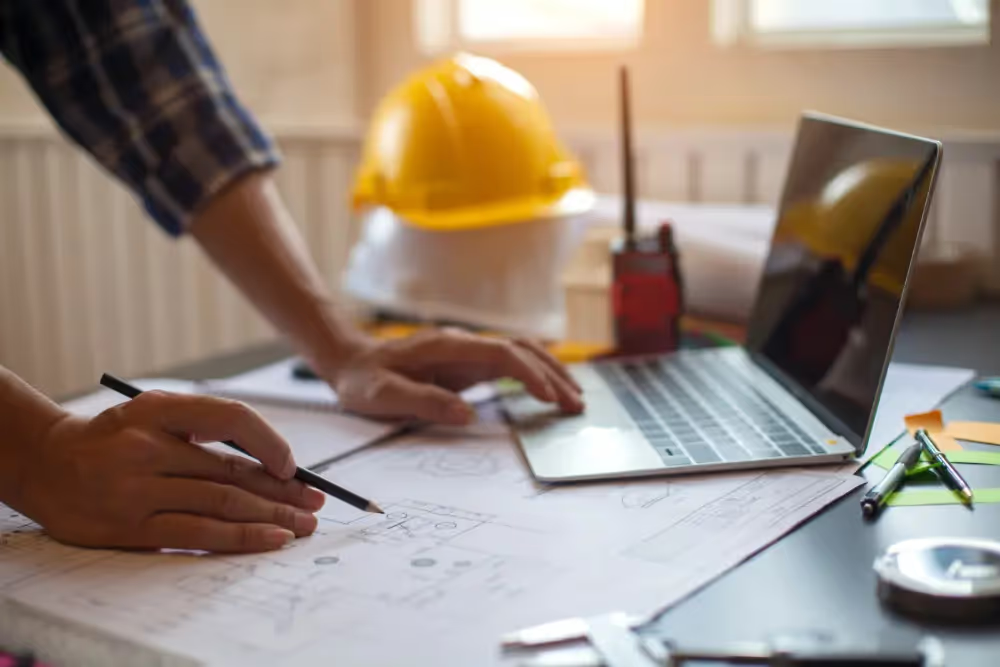
Why Do You Need Updated As-Builts on Your Next Project?
industry insights
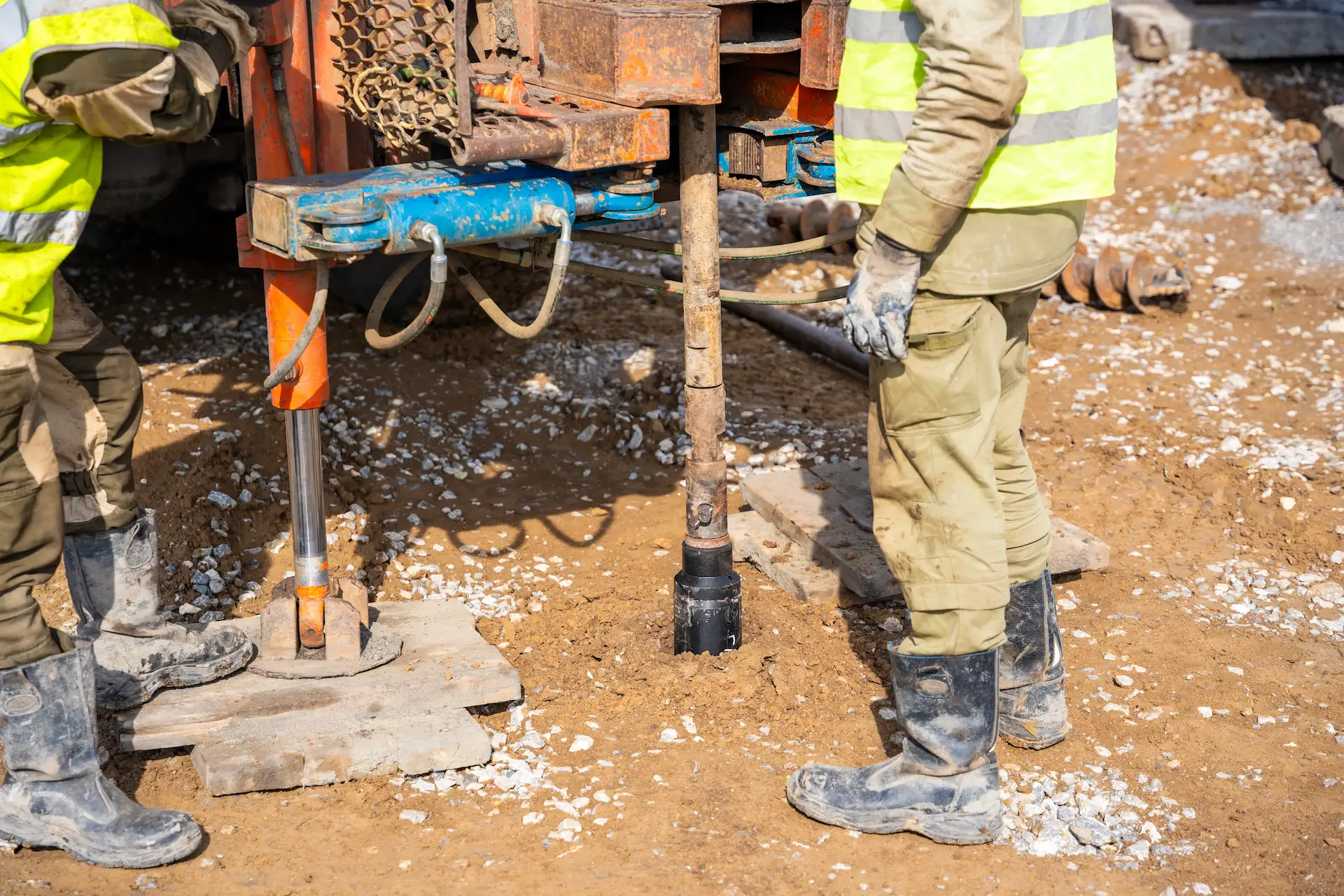
What Are Soil Borings & How Are They Conducted?
Understanding what lies beneath the surface of the earth is a critical piece of planning in the fields of construction, environmental due diligence, and geotechnical engineering.
Conducting soil borings is one of the most reliable methods for gaining this insight. Soil borings provide essential data about subsurface conditions, helping engineers, architects, and developers make informed decisions about site suitability, foundation design, and environmental impact.
What Are Soil Borings?
Soil borings are a geotechnical investigation technique used to collect soil samples from below the ground surface. These samples are analyzed to determine the physical and mechanical properties of the soil, such as composition, density, moisture content, strength, and bearing capacity. The information gathered is crucial for designing safe and effective foundations for buildings, roads, bridges, and other infrastructure.
Soil borings are also used in environmental assessments to detect contamination, monitor groundwater, and evaluate the suitability of land for agricultural or industrial use.
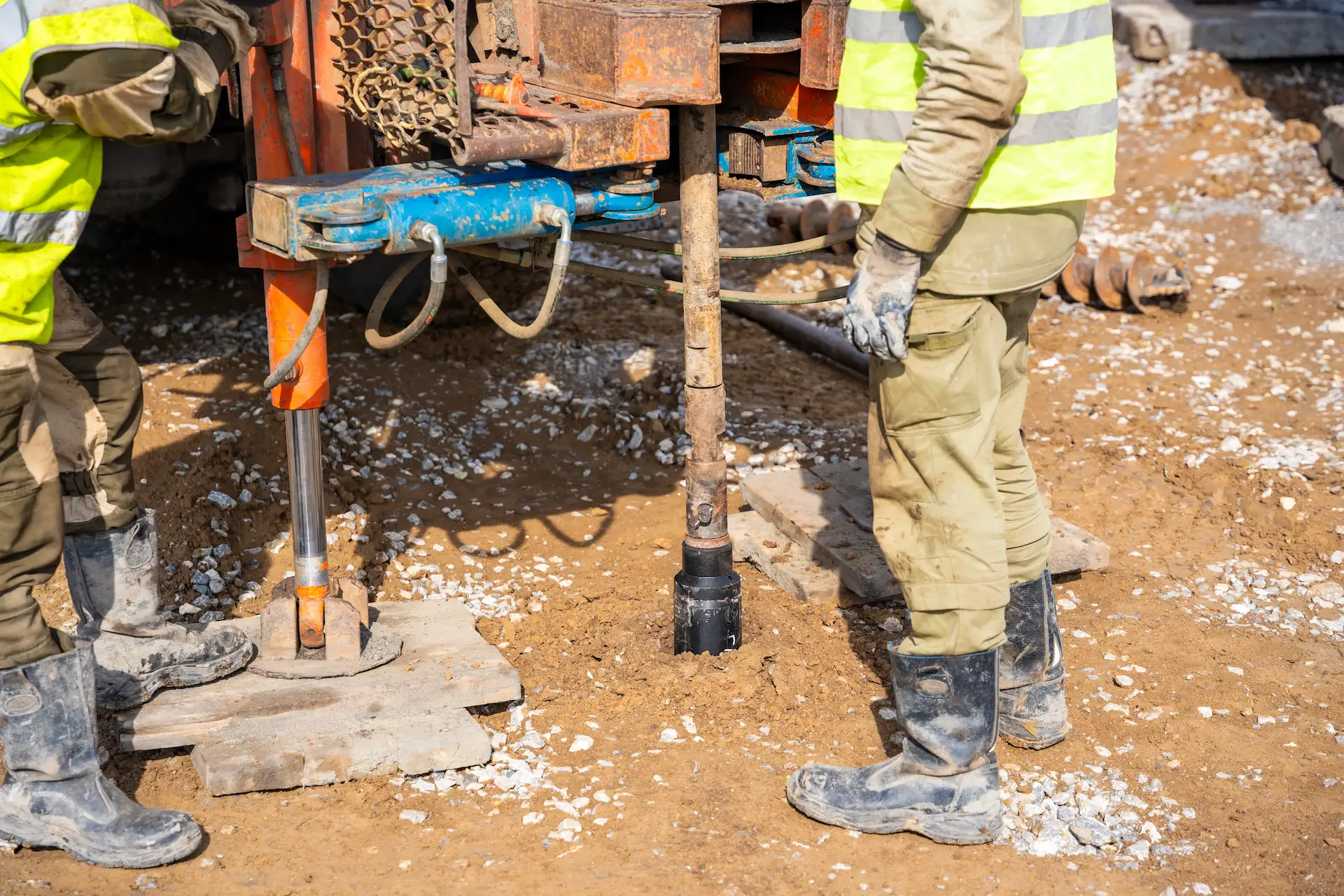
Why Are Soil Borings Important?
The subsurface conditions of a site can vary significantly, even within a small area. Without proper investigation, construction projects risk encountering unexpected soil behaviors such as settlement, liquefaction, or slope instability. These issues can lead to structural failure, costly delays, or environmental hazards.
Soil borings help to:
- Assess soil stability and load-bearing capacity
- Identify groundwater levels and flow
- Detect the presence of contaminants
- Inform the design of foundations and earthworks
- Ensure compliance with building codes and environmental regulations
Types of Soil Boring Methods
Several methods are used to conduct soil borings, each suited to different site conditions and project requirements. The most common include:
Auger Boring
This method uses a helical screw blade (auger) to drill into the ground. It is typically used for shallow borings in soft to medium soils. There are two main types:
- Hand augers are used for depths up to 10-15 feet
- Power augers are used for deeper or more resistant soils
Auger boring is relatively quick and cost-effective but may not be suitable for very hard or saturated soils.
Rotary Drilling
Rotary drilling uses a rotating drill bit to cut through soil and rock. It is often used for deeper borings and can penetrate a wide range of soil types. The drill bit is lubricated and cooled with drilling fluid (mud or water), which also helps to bring cuttings to the surface.
This method allows for continuous sampling and is ideal for complex geotechnical investigations.
Percussion Drilling
Also known as cable tool drilling, this method involves repeatedly dropping a heavy bit to break up soil and rock. The loosened material is then removed from the borehole. While slower than rotary drilling, percussion drilling is effective in hard or boulder-laden soils.
Wash Boring
Wash boring uses a jet of water to loosen soil, which is then removed by a suction pump. It is commonly used in soft soils and for preliminary investigations. However, it does not provide undisturbed samples, limiting its usefulness for detailed analysis.
The Soil Boring Process: Step-by-Step
Conducting a soil boring involves several key steps, typically carried out by a geotechnical engineering firm:
1. Site Preparation
Before drilling begins, the site is surveyed and cleared. The boring locations are selected based on the proposed construction layout and known geological conditions. Permits may be required, especially in urban or environmentally sensitive areas.
2. Drilling and Sampling
The drilling rig is set up at the designated location. As the borehole is advanced, soil samples are collected at regular intervals – usually every 2 to 5 feet or at changes in soil strata.
There are two main types of samples:
- Disturbed samples, which are suitable for classification and basic testing
- Undisturbed samples, which preserve the soil structure and are used for strength and compressibility tests
Sampling tools include split-spoon samplers, Shelby tubes, and piston samplers, depending on the soil type and required data.
3. Standard Penetration Test (SPT)
One of the most common in-situ tests performed during soil borings is the Standard Penetration Test (SPT). It involves driving a split-spoon sampler into the soil using a standardized hammer and recording the number of blows required to penetrate a set depth. The resulting "N-value" provides an indication of soil density and strength.
4. Groundwater Monitoring
As the borehole is drilled, groundwater levels are observed and recorded. In some cases, temporary or permanent monitoring wells are installed to track fluctuations over time.
5. Logging and Documentation
Throughout the boring process, a detailed borehole log is maintained. This log includes:
- Depth and type of each soil layer
- Sample locations and types
- SPT results
- Groundwater observations
- Any anomalies or obstructions encountered
This documentation forms the basis for the geotechnical report.
6. Laboratory Testing
Collected samples are sent to a geotechnical laboratory for further analysis. Common tests include:
- Grain size distribution
- Atterberg limits (plasticity)
- Moisture content
- Shear strength
- Consolidation and compaction characteristics
These tests provide the data needed to model soil behavior under load and design appropriate foundations.
Interpreting the Results
The final deliverable of a soil boring investigation is a geotechnical report. This report synthesizes field and lab data to provide:
- Soil profiles and stratigraphy
- Engineering properties of each soil layer
- Recommendations for foundation design
- Assessment of potential risks (e.g., settlement, liquefaction)
- Construction considerations (e.g., dewatering, excavation support)
This report is a critical tool for engineers and architects, guiding decisions that affect safety, cost, and long-term performance.
GPRS offers nationwide, precision utility locating services to help ensure the success of your soil boring projects.
Utilizing state-of-the-art subsurface investigation technology such as GPR scanning and EM locating, our SIM-certified Project Managers provide you with complete and accurate data bout the built world beneath your project site, so you can excavate without the risk of costly and potentially dangerous subsurface damage.
All this data is at your fingertips 24/7 thanks to SiteMap® (Patent Pending), GPRS’ project & facility management application that provides accurate existing conditions documentation to protect your assets and people.
From soil boring clearances to skyscrapers, GPRS Intelligently Visualizes The Built World® to keep your projects on time, on budget, and safe.
What can we help you visualize?
Frequently Asked Questions
What do I get when I hire GPRS to conduct a utility locate?
Our Project Managers flag and paint our findings directly on the surface. This method of communication is the most accurate form of marking when excavation is expected to commence within a few days of service.
GPRS also uses a global positioning system (GPS) to collect data points of findings. We use this data to generate a plan, KMZ file, satellite overlay, or CAD file to permanently preserve results for future use. GPRS does not provide land surveying services. If you need land surveying services, please contact a professional land surveyor.
Please contact us to discuss the pricing and marking options your project may require.
Can GPRS Project Managers distinguish between different underground utilities that they locate?
In most situations, we can identify the utility in question without any problems, although it is not always possible to determine what type of utility is present. When this happens, we attempt to trace the utility to a valve, meter, control box, or other signifying markers to determine the type of utility buried.
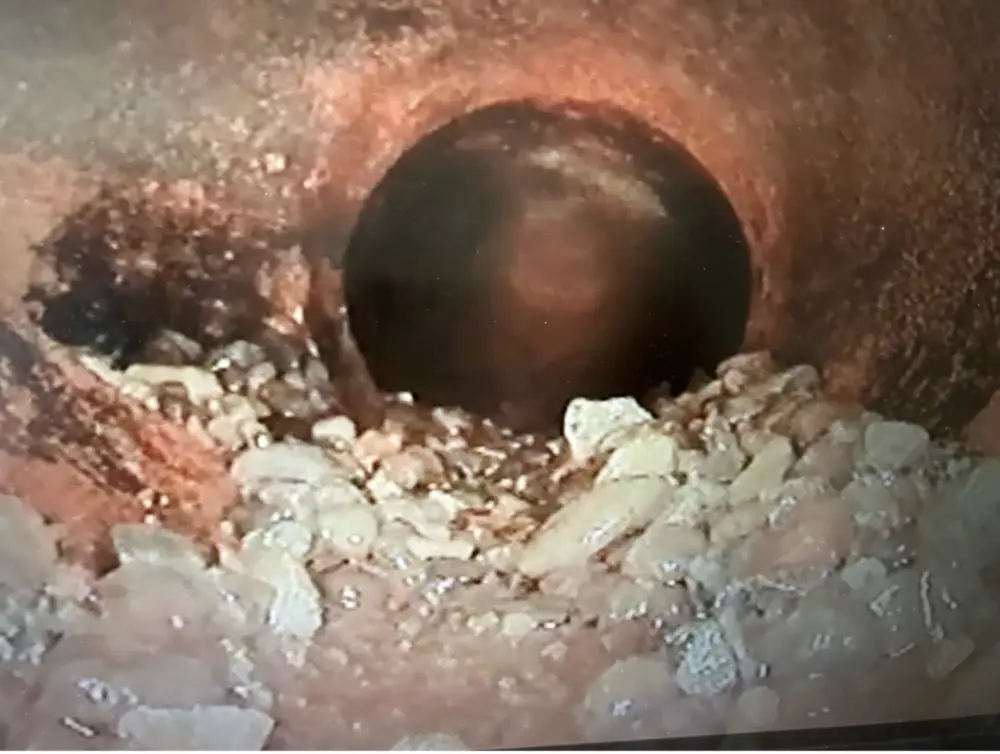
GPRS VPI Services Help New High School Address Cracking Sewer System
When students at Rainier Beach High School in Seattle, Washington, returned from spring break this past school year and entered their brand new, four-story school building, the sanitary sewer lines running underneath the campus would have been the last thing on their minds.
But about a year before the new, 297,000 s.f. school building opened, those pipes were all that contractor Lydig Construction could think about. That’s because they’d discovered that the building’s concrete slab was slowly sinking into the ground, cracking open the new cast iron pipes as it went.
Lydig and the school district needed to pinpoint the location of each break in the pipelines, and they needed an accurate map of the entire buried sewer system, so they could effectively plan a permanent repair. While a plumber working on the project had sewer inspection equipment of their own, however, they had been unable to obtain the data the contractor needed.
So Lydig called GPRS.
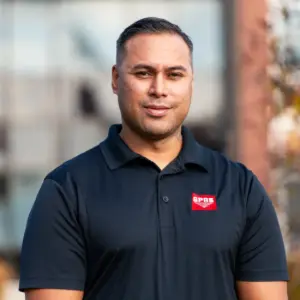
Project Manager Robert Rasmussen deployed a combination of a remote-controlled sewer inspection crawler and push-fed sewer scope to provide the contractor with a NASSCO-certified report of their sewer system, complete with photo and video evidence of every defect.
Rasmussen worked together with the contractor, returning to the site several times over the course of a week to inspect and map more segments of the system.
He’d access the system from inside the school by feeding his push-fed scope into the cleanouts. Then, when he couldn’t continue any further due to sediment buildup in the lines, he’d deploy his remote-controlled crawler from a manhole outside and try to meet up with where the scope had run into the blockage. As Rasmussen provided the contractor and plumber with the precise location of each area where water, sediment, and other debris was entering the cracked pipes, a jetting company would use the data to clear the lines so that he could proceed further.
“I was able to pinpoint where all the breaks were in the pipelines, and where all the pea gravel and dirt was coming in from the breakage,” Rasmussen said. “And then I was able to locate all the pipelines.”
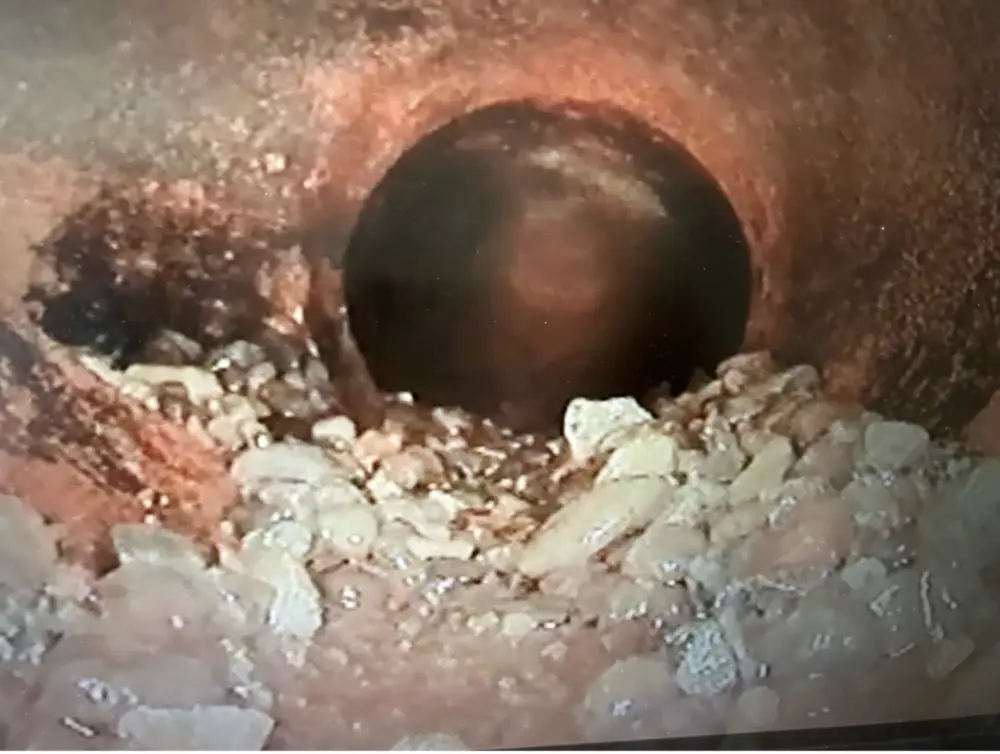
In total, Rasmussen inspected 105 linear feet of sewer line. Both his push-fed sewer scope and remote-controlled crawler were equipped with sondes: instrument probes that emit a signal detectable from the surface with an electromagnetic (EM) locator. This allowed Rasmussen to map the sewer system while he was locating defects.
The data Rasmussen collected at Rainier Beach High School helped Lydig and the school district effectively repair the damaged sanitary sewer lines and reroute them to protect from future damage. When students and faculty did finally get to enjoy their new building, they could focus on academics and athletics – and not on what was going on beneath their feet.
“[The client was] very impressed,” he said. “They initially called me out for just one day, to scope some of the lines that their plumbers found and couldn’t really investigate. Then two days after that, they called me back out on site and it ended up being like three or four days of me being out there scoping, to see where the real problem was. Every single one of those new cleanouts and pipelines, they were filled with rock and sediment.”
Whether you need help assessing a brand-new sanitary sewer system, or a decades-old storm line, GPRS’ comprehensive suite of sewer inspection services can help ensure your infrastructure keeps working for you.
We offer video pipe inspection (VPI) using the remote-controlled crawlers and push-fed scopes to create comprehensive NASSCO reports that detail every defect located, ranked by severity and identified with photo and video evidence. You’ll know what needs fixed immediately and exactly where you need to dig to enact those repairs.
NASSCO stands for the National Association of Sewer Service Companies, and they are the industry-leading provider of training and certification programs focused on assessing, maintaining, and rehabilitating underground sanitary sewer and stormwater lines. Every GPRS Project Manager that conducts sewer inspection services has achieved NASSCO certification in pipeline (PACP), manhole (MACP), and lateral (LACP) assessments. So when you hire GPRS, you always know you’re getting the best trained sewer inspection company near you.
Additionally, GPRS can inspect your sewer system using dye tracing or smoke testing, to assess things like flow direction and determine if there are any illegal or incorrect hookups to your lines.
From sewer lines to skyscrapers, GPRS Intelligently Visualizes The Built World® to keep your projects on time, on budget, and safe.
What can we help you visualize?
Frequently Asked Questions
What size sewer pipes can GPRS inspect?
Thanks to our use of both remote-controlled sewer inspection crawlers and push-fed sewer scopes, we’re able to inspect pipes 2” in diameter and up.
Can you locate sewer pipes in addition to evaluating their integrity?
Yes! Our SIM and NASSCO-certified Project Managers use VPI technology equipped with sondes, which are instrument probes that allow them to ascertain the location of underground utilities from an inaccessible location. This allows them to use electromagnetic (EM) locating to map sewer systems at the same time they’re evaluating them for defects.
What deliverables does GPRS offer when conducting a VPI?
GPRS is proud to offer WinCan reporting to our Video Pipe Inspection clients. Maintaining sewers starts with understanding sewer condition, and WinCan allows GPRS Project Managers to collect detailed, NASSCO-compliant inspection data. GPRS Project Managers not only inspect the interior condition of sewer pipes, laterals, and manholes – they can also provide a map of their location. The GPRS Mapping & Modeling Department can provide detailed GPS overlays and CAD files. Our detailed WinCan/NASSCO reports contain screenshots of the interior condition of the pipe segments that we inspect, as well as a video file for further evaluation, documentation, and/or reference.
Does GPRS offer Lateral Launch Services?
Yes, we offer lateral launch capabilities as part of our standard Video Pipe Inspection services.
.webp)
$500M Hydrogen Retrofit to Transform Coal-Fired Power Plant
In a landmark move for the energy sector, Utah’s Intermountain Power Project (IPP) is undergoing a transformative upgrade that positions it at the forefront of clean energy innovation. As reported by Engineering News-Record (ENR), the IPP Renewed initiative is a testament to the power of regional cooperation and a bold step toward decarbonizing large-scale power generation through the integration of green hydrogen. As the global energy landscape shifts toward sustainability, this project exemplifies how legacy infrastructure can be reimagined to meet the demands of a low-emissions future.
Environmental Impact and Emissions Reduction
The transition from coal to hydrogen-blended fuel represents a significant environmental milestone. By leveraging green hydrogen – produced through electrolysis powered by renewable energy – the IPP Renewed project aligns with California’s stringent emissions regulations and broader climate objectives.
Hydrogen combustion emits only water vapor, eliminating carbon dioxide and other harmful pollutants associated with fossil fuels. As the technology matures and the hydrogen blend increases, the plant’s emissions profile will continue to improve, setting a new standard for utility-scale power generation.
.webp)
A Strategic Shift Toward Hydrogen Power
Commissioned in the 1980s, the IPP has long served as an energy hub for communities across six states. With its 1,800-MW coal-fired units nearing the end of their operational life and power purchase agreements set to expire in 2027, stakeholders faced a pivotal decision. Rather than decommission the site, the Intermountain Power Agency (IPA) and its partners chose to invest in a cleaner, more flexible future.
The centerpiece of this transformation is the installation of two advanced M501JAC gas turbines from Mitsubishi Power, capable of operating on a blend of natural gas and hydrogen. To start, the turbines will run on a 30% hydrogen mix, with a roadmap to transition to 100% green hydrogen by 2045. This shift is expected to reduce carbon dioxide emissions by over 75% compared to traditional coal-fired generation.
Leveraging Unique Geology for Energy Storage
One of the most innovative aspects of the IPP Renewed project is its integration with the Advanced Clean Energy Storage (ACES) Delta hub. Located atop a geologic salt dome, the site offers a natural advantage for underground hydrogen storage. Two massive caverns, each capable of holding 4.5 million barrels of hydrogen, will serve as long-term, seasonal energy reservoirs.
This storage capability is crucial for balancing the intermittency of renewable energy sources. Surplus solar and wind power can be converted into green hydrogen via electrolysis and stored until demand peaks. This method enhances grid reliability and enables a more resilient and sustainable energy system.
Engineering Excellence and Workforce Development
The scale and complexity of the IPP Renewed project are immense. With over five million labor hours logged and more than 2,000 workers on-site, the project has become a model for workforce development in the energy sector. The Industrial Company (TIC), serving as the EPC contractor, implemented an on-site training program to certify workers in real-time, accelerating their progression to journeyman status.
In a notable first, TIC also self-performed heavy equipment hauling using self-propelled modular transport units, eliminating reliance on specialty subcontractors and streamlining logistics. This approach underscores the importance of adaptability and innovation in modern infrastructure projects.
Modernizing Transmission for a Clean Energy Future
Beyond generation, the IPP Renewed initiative includes a $2.7-billion overhaul of the Southern Transmission System, which delivers power from Utah to Southern California. This upgrade involves constructing new DC converter stations and enhancing the 2,400-MW transmission capacity to accommodate the evolving energy mix.
The modernization of transmission infrastructure is a critical enabler of the hydrogen economy. It ensures that clean, dispatchable power generated in Utah can be efficiently delivered to demand centers hundreds of miles away, supporting regional decarbonization goals.
The Role of Utility Locating and Leak Detection
As hydrogen infrastructure expands, utility locating and leak detection becomes paramount. Because hydrogen is the smallest and lightest molecule, it can escape through minute leaks that would be inconsequential for other gases. Accurate utility locating ensures that underground pipelines and storage facilities are mapped with accuracy, reducing the risk of accidental damage during construction or maintenance.
Advanced leak detection technologies, including acoustic sensors and leak detection correlators, are essential for maintaining safety and operational integrity.
How GPRS can Support the Future of Clean Energy Infrastructure
GPRS expertise in subsurface infrastructure plays a vital role in supporting projects of this magnitude. As the energy industry embraces hydrogen and other clean technologies, the need for accurate, real-time data on underground utilities and structural conditions becomes increasingly critical.
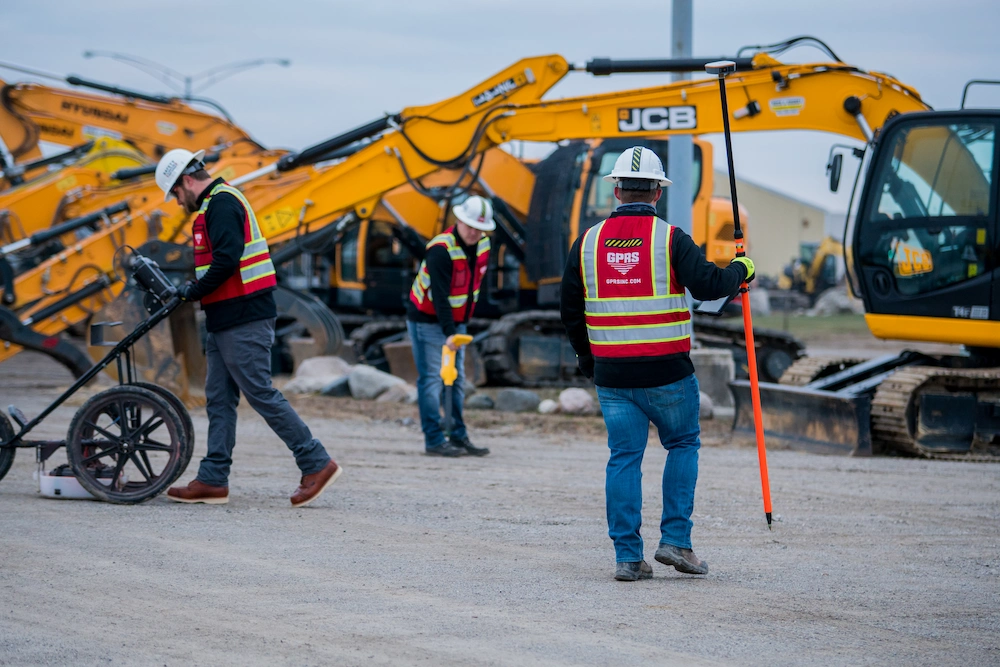
For complex infrastructure projects like the IPP, GPRS offers support services that enhance safety, accuracy, and efficiency. These include utility locating using ground penetrating radar (GPR) and electromagnetic (EM) locating, advanced leak detection, concrete scanning, 3D laser scanning and mapping to create accurate digital models for design and construction planning, and video pipe inspection to assess the condition of sewer and stormwater systems. Projects involving hydrogen power plants and large-scale energy storage require the highest levels of precision and risk mitigation. GPRS services are indispensable for ensuring safe construction, reliable operations, and long-term infrastructure integrity.
As hydrogen power plants and storage hubs become more prevalent, GPRS stands ready to support these projects with the tools and expertise necessary to ensure safety, efficiency, and regulatory compliance. Our commitment to precision and innovation makes us a trusted partner in the transition to a cleaner, more sustainable energy future.
From hydrogen hubs to high-voltage transmission lines, GPRS Intelligently Visualizes The Built World® to keep your infrastructure projects safe, efficient, and on schedule.
What can we help you visualize?
FREQUENTLY ASKED QUESTIONS
Why is utility locating critical for hydrogen infrastructure projects?
Hydrogen facilities require accurate excavation to avoid damaging underground utilities. GPRS uses ground-penetrating radar (GPR) and electromagnetic (EM) locating to identify and map subsurface utilities before construction begins. This helps reduce the risk of utility strikes, supports safe excavation, and ensures compliance with safety regulations.
How does GPRS support leak detection in hydrogen systems?
Hydrogen is colorless, odorless, and highly flammable, which makes early leak detection essential for safety. GPRS’ SIM-certified Project Mangers use acoustic sensors and leak detection correlators to identify leaks in pressurized systems. These technologies help prevent safety incidents, reduce operational downtime, and support compliance with safety standards.
What role does concrete scanning play in hydrogen facility construction?
GPRS can help prevent costly delays and safety risks during hydrogen facility construction by identifying embedded objects before any coring or cutting begins. These objects may include rebar, conduits, and post-tension cables. When locating them in advance, project teams can avoid structural damage and ensure the safe installation of critical systems.
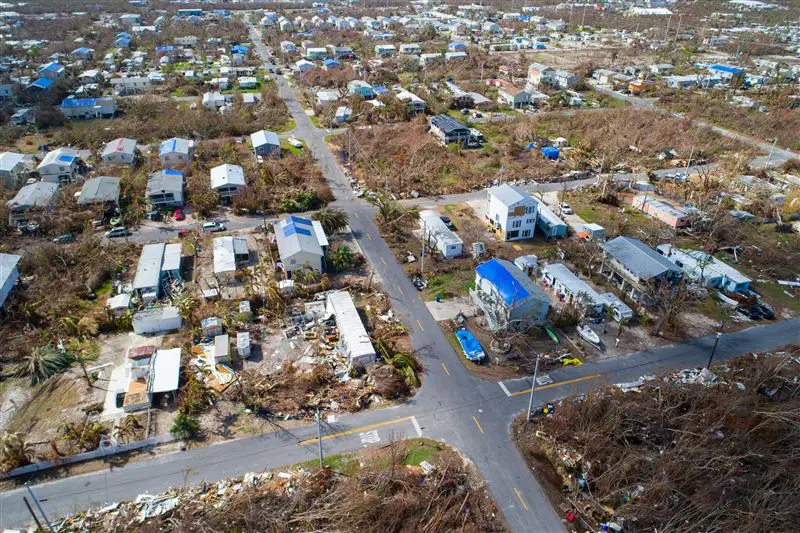
Jacobs Wins $137M Award to Help Rebuild U.S. Virgin Islands After Hurricane Damage
Global professional services firm Jacobs has been awarded a program management contract to rebuild the U.S. Virgin Islands following hurricanes Irma and Maria.
According to a press release on Jacobs’ website, the company was contracted by the Virgin Islands Public Finance Authority to deliver program management services for the “Rebuild USVI” initiative. The contract is valued at $137 million and will see Jacobs work with the U.S. Virgin Islands’ Super Project Management Office on simultaneous, critical infrastructure projects, including hospitals, schools, transit corridors, power, water and wastewater utilities.
"Rebuilding is critical for St. Croix, St. Thomas, and St. John,” said Jacobs Executive Vice President Ron Williams. “The islands are home to nearly 90,000 people who depend on safe schools, reliable transportation, consistent utility services and access to healthcare. Further, with tourism as the economic engine, it's essential we prioritize efforts quickly and make the islands' infrastructure more resilient for the future."
During this three-year-contract, Jacobs – which has a long history of rebuilding critical infrastructure following severe weather events – will also provide advisory and consulting services focused on future project planning, environmental management, logistics, supply chain, and workforce challenges.
The Office of Disaster Recovery (ODR), operating under the Virgin Islands Public Finance Authority, manages the territory’s $23 billion in federal aid allocated following the devastating hurricanes of 2017. While progress has been made in the years since the hurricanes ravaged the islands, there is still much work to be done. Director Adrienne Williams-Octalien reaffirmed ODR’s dedication to the Super Project Management initiative, noting that Jacobs was chosen for the “Rebuild USVI” program due to its strong proposal response, proven expertise, competitive pricing, available resources, innovative approach, and strategic alliances.
Jacobs has supported efforts like the Port of San Francisco Waterfront Resilience Program, which is adapting 7.5 miles of the city's waterfront to be resilient to earthquakes, coastal storms and sea level rise; reinstating vital power infrastructure in the Philippines following devastating earthquakes; returning and maintaining essential services to the Puerto Rican community following Hurricane Maria; and continued on-the-ground assistance with FEMA disaster-related operations throughout the U.S. and its territories.
"We are excited to have Jacobs' support as we continue working to rebuild a stronger, more resilient community while ensuring full compliance with our funding requirements," Williams-Octalien said.
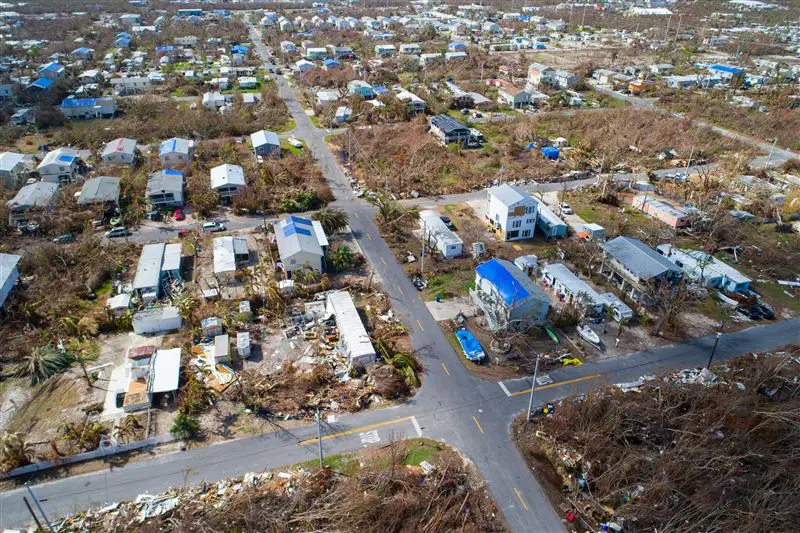
The Importance of Fortifying Our Infrastructure for Extreme Weather – and How GPRS Can Help
The changing climate has altered the landscape of risk for infrastructure globally. Rising temperatures, increased precipitation in some areas, and prolonged droughts in others present complex challenges that existing infrastructure was not originally designed to withstand. These changes have resulted in more frequent and severe weather events, from the flooding of major urban centers to the destructive paths of hurricanes across coastlines.
Elevating building foundations, using water-resistant materials, installing sump pumps and other flood mitigation systems can help protect buildings and their infrastructure from water damage during floods. Non-combustible building materials help reduce wildfire risks in fire-prone regions, and wind-resistant roofing and impact-resistant windows ensure structures can withstand high winds and flying debris in hurricane-prone areas.
Utility or grid hardening, the process of upgrading and strengthening utility infrastructure to make it more resilient to severe weather and other disruptions, can protect these critical utilities from a variety of weather-related issues. Communities across the country are undergrounding their power lines to reduce the risk of outages from wind, lightning strikes, and more.
But anytime you’re putting something new in the ground, it’s vital you’re aware of any buried utilities or other underground infrastructure assets that are already there.
GPRS is the nation’s largest company offering above and below-ground existing conditions documentation. We Intelligently Visualize The Built World® to keep your projects on time, on budget, and safe.
GPRS employs advanced technologies like ground penetrating radar (GPR) and electromagnetic (EM) locating to locate utilities underground, as well as post tension cable, rebar, and conduits and more within concrete slabs.
We geolocate and digitize these findings and deliver them to you through SiteMap® (patent pending), our project & facility management application that provides accurate existing conditions documentation to protect your assets and people.
Available 24/7 from any computer, tablet, or smartphone, SiteMap is a single source of truth for the critical data that allows you to protect your infrastructure from damage, whether you’re hardening a power grid or just conducting regular maintenance.
What can we help you visualize?
Frequently Asked Questions
Does GPRS locate PVC piping and other non-conductive utilities?
Yes, our SIM-certified Project Managers utilize a suite of infrastructure visualization tools, including ground penetrating radar (GPR) and electromagnetic (EM) locating, to find all types of subsurface materials. These tools compensate for each other’s weak points, allowing us to create an accurate, complete picture of your job site.
Will I need to mark out the utilities that GPRS locates?
No, our Project Managers locate and mark all utilities for you when conducting a utility locate. We have a variety of tools and markers we use to highlight the locations of utilities, underground storage tanks (USTs), and other buried items.
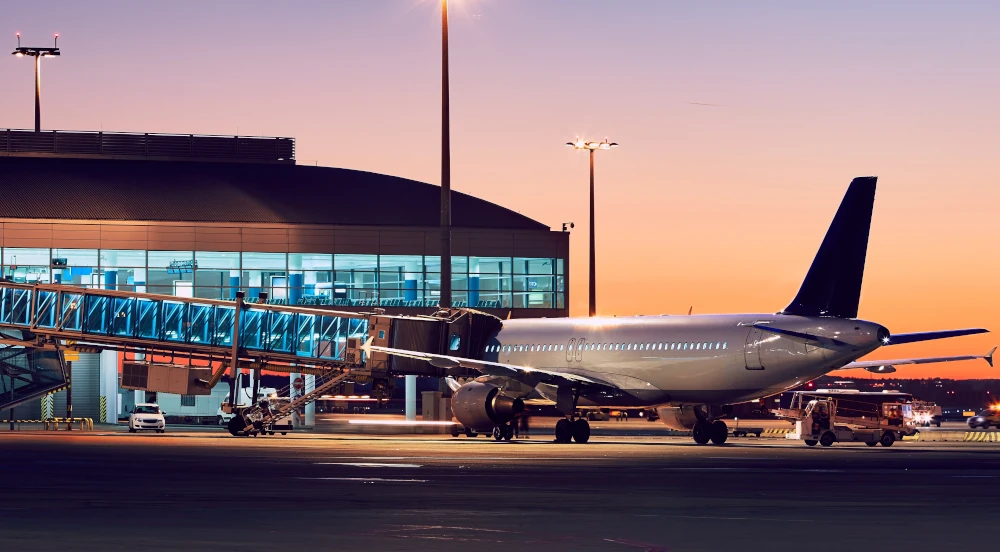
Severed Fiber Line at Jacksonville Airport Causes Radar Outage
Damage to critical buried infrastructure recently caused a scary situation at Jacksonville International Airport (JAX) in Jacksonville, Florida.
On June 20, air traffic controllers briefly lost radar capabilities after contractors cut a buried fiber optic cable during construction work.
According to The Associated Press, controllers were able to continue directing planes across five states in the Southeast because a backup system kicked in as designed. The Federal Aviation Administration (FAA) said no flights were disrupted.
“The FAA said the radar center in Jacksonville, Florida, continued operating but on alert status because its primary communication line went down,” the AP wrote. “A contractor was working on repairing the severed fiber line Friday afternoon. Authorities didn’t specify what caused the severed line or where it happened.”
While this event was, thankfully, resolved without incident, it serves as a reminder of how easily a single mistake when digging or trenching can put lives in danger.
Whether you’re digging just a few inches into the ground or several feet, or conducting your excavation utilizing directional drilling or other trenchless technologies, obtaining accurate utility locating and mapping data prior to breaking ground is the best way to avoid costly and potentially dangerous damage to buried infrastructure.
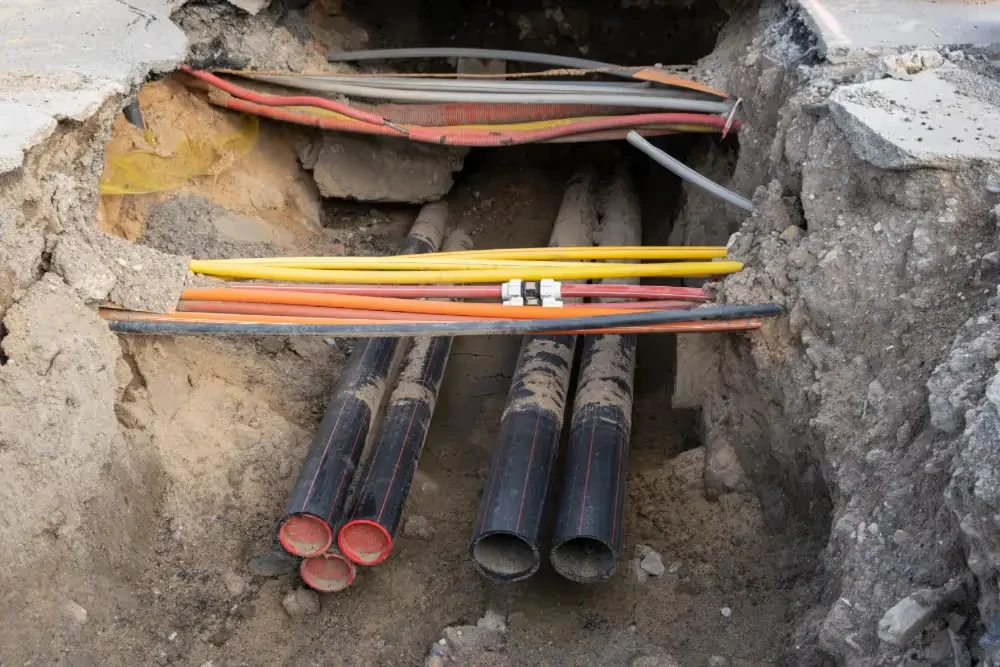
Why Are Fiber Optic Lines Especially Vulnerable?
Unlike metal pipes or electrical lines, fiber optic cables are made of glass or plastic and do not emit electromagnetic signals. This makes them harder to detect using traditional methods. They are often installed with tracer wires within the conduit, allowing for the use of electromagnetic signal tracing. Utility locating companies use electromagnetic (EM) locators to detect these tracer wires.
The Cost of Damaging a Fiber Optic Line
At JAX, the severed fiber optic line likely served as a vital data link for radar systems. The consequences of such damage extend far beyond repair costs. In air traffic control, even a brief radar outage can delay hundreds of flights and jeopardize passenger safety. The FAA and other agencies must then reroute traffic and investigate the incident, pulling resources from other essential operations.
Hiring a professional utility locating company to find and map underground fiber optic cables and all other buried utilities prior to breaking ground is an essential step in mitigating the risk of costly and potentially dangerous subsurface damage.
How Do Utility Locating Services Help Prevent Subsurface Damage?
Utility locating services identify and map underground utilities before any digging or construction begins, helping to avoid accidental strikes that could cause costly damage, service outages, or safety hazards.
Calling your local 811 center should be your first step whenever you’re planning an excavation. Federal law requires you contact 811 to receive the approximate location of all registered utilities within your project area prior to breaking ground. Registered utilities can consist of both private and public lines, but it’s important to remember that not all utilities are registered with 811.
GPRS’ professional utility locating services complement the 811 locate by providing you with accurate and complete data about the buried infrastructure on your job site. GPRS uses a combination of tools, including ground penetrating radar (GPR), electromagnetic (EM) locators, and GPS mapping to detect both public and private utility lines.
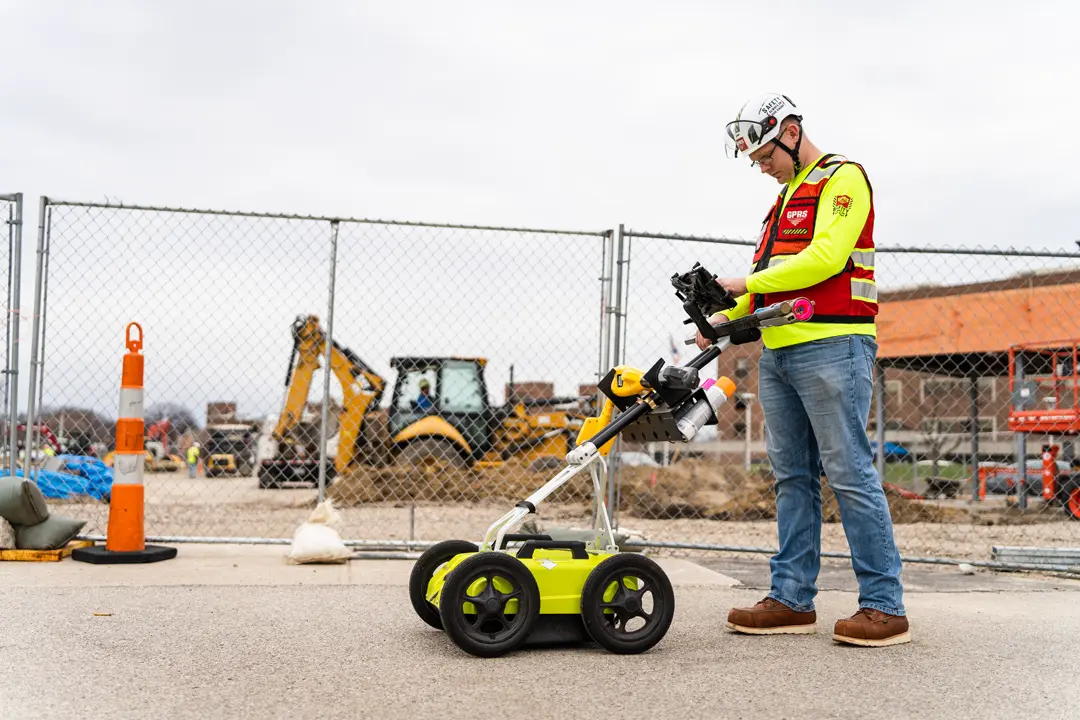
Once utilities have been detected, they’re physically marked at the job site with highly visible, color-coded flags or paint to indicate their type and precise location. These markings serve as a visual guide for construction crews, helping them navigate around underground infrastructure safely and accurately during excavation and construction.
The GPRS Mapping & Modeling team provides digital maps and .KMZ files that can be integrated into construction planning software, ensuring that crews have real-time access to utility layouts.
SiteMap®, (patent pending), powered by GPRS, is our proprietary infrastructure mapping software solution that provides you and your team with 24/7, secure access to the accurate, field-verified data collected by GPRS Project Managers. Accessible from any computer, tablet or smartphone, it is a single source of truth for the critical infrastructure you and your team needs to plan, manage, and build better.
GPRS Intelligently Visualizes The Built World® to keep your projects on time, on budget, and safe.
What can we help you visualize?
Read Also: How is Utility Locating Done?
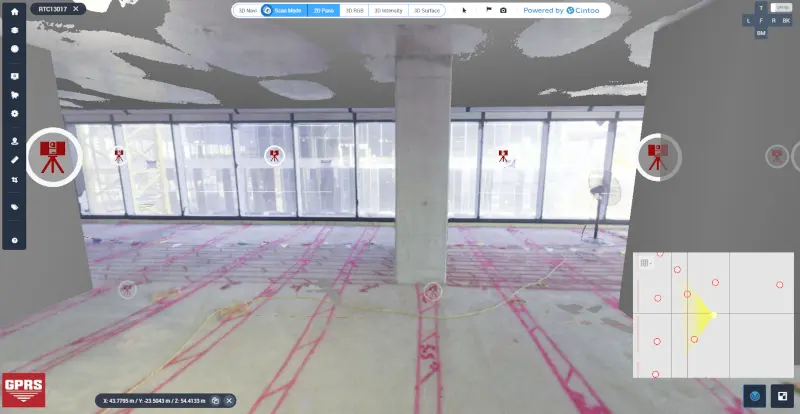
How Does a 3D Laser Scanner Capture Concrete Markings?
A 3D laser scanner captures concrete markings by emitting laser beams that reflect off surfaces and return to the scanner, collecting millions of precise data points that map the concrete markings on site. These data points are compiled into a high-resolution 3D point cloud that maps the shape, texture, and position of everything in view, including paint, chalk lines, or other surface markings. This digital record allows teams to document site conditions, verify layouts, and permanently record markings for future reference.
Not only does the 3D laser scanner provide detailed and accurate records of concrete markings, but it also captures all architectural, structural and MEP features, delivering a comprehensive digital asset for renovation, construction, and analysis.
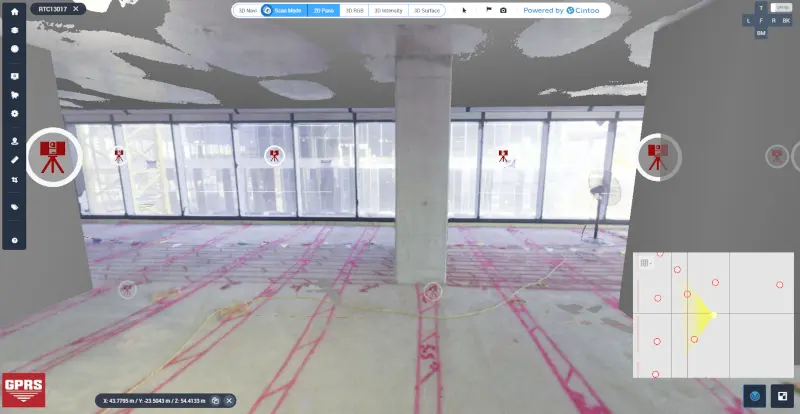
What is the Method of Concrete Scanning?
Concrete scanning uses ground penetrating radar (GPR), which sends radio signals into the concrete to detect subsurface features. The system’s transmitter, receiver, and signal processor work together to identify embedded objects like rebar, conduits, or post tension cables. Trained professionals interpret the reflected signals to map their location, pattern, and depth.
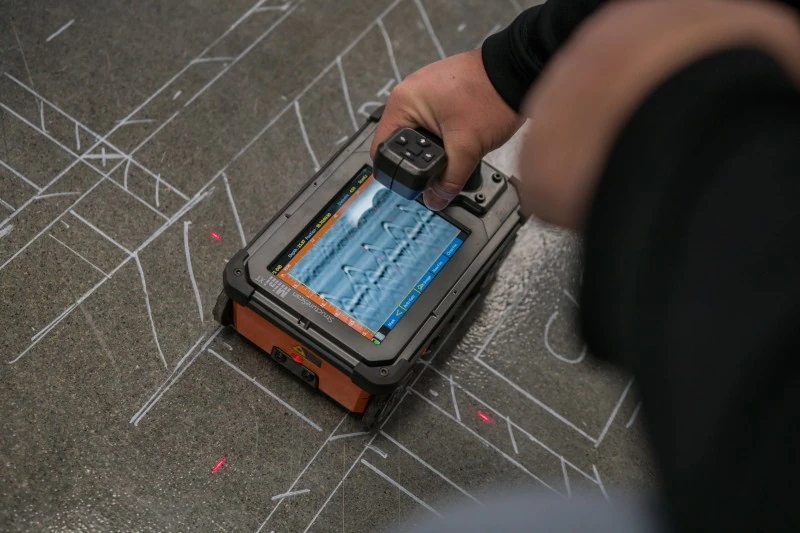
What is the Process of Capturing Concrete Markings with a 3D Laser Scanner?
- Process: After using GPR to identify and mark objects within concrete, such as rebar or utilities, a 3D laser scanner captures these markings in a point cloud.
- Purpose: This process allows for accurate documentation of concrete markings and can be used to generate 2D CAD drawings or 3D models of findings to aid in safe cutting, drilling, or anchoring into concrete.
- Technology: Leica laser scanners, such as the RTC360, utilize LiDAR technology to capture precise site data at high speeds.
- Software: Leica Cyclone or Autodesk Recap can be used to process the captured point cloud, allowing for the extraction of markings and the generation of CAD/BIM deliverables.
- Benefits: Capturing concrete markings with laser scanners like the Leica RTC360 ensures 2-4mm accuracy and helps minimize human error, leading to improved safety and efficiency on construction sites.
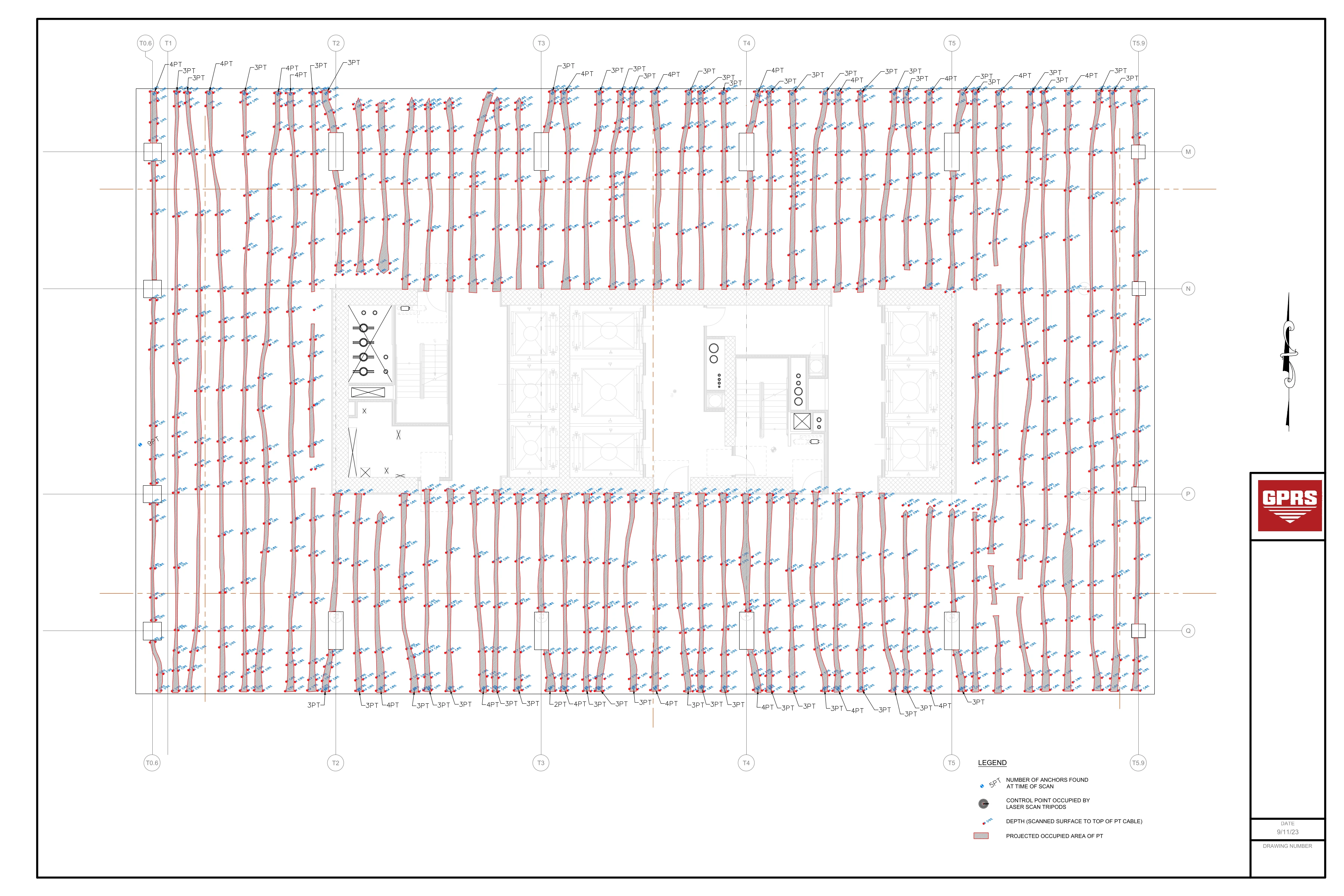
Why Use Leica Laser Scanners to Capture Concrete Markings?
Leica laser scanners are considered among the best in the industry because they combine exceptional speed, accuracy, and ease of use with powerful software integration. For example, the Leica RTC360 laser scanner can capture up to 2 million data points per second and uses advanced features like automatic point cloud registration and HDR imaging to deliver high-quality, colorized scans in under two minutes. Leica’s software makes it easy to turn raw scan data into deliverables like BIM models, CAD drawings, and immersive 3D environments. High-resolution imagery, or TruViews, can be added to the laser scanning process, making it easier to identify and document markings digitally for layout verification or future reference.
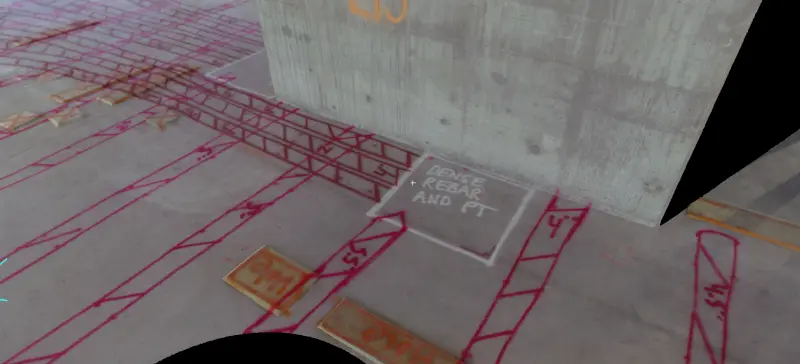
Can GPRS Use a 3D Laser Scanner to Capture Concrete Markings?
Yes, the Project Managers at GPRS are formerly trained to perform concrete imaging services using GPR technology and reality capture services using 3D laser scanners.
GPRS Project Managers complete the most extensive subsurface training program in the industry, called SIM certification. SIM teaches Project Managers how to utilize GPR and EM locating to identify the layout of rebar, post tension cables, buried utilities, and more with 99.8%+ accuracy. Achieving SIM 101 certification, which is required of all GPRS Project Managers, involves completing 80 hours of hands-on classroom instruction and 320 hours of mentorship in the field.
While the technology for underground utility locating and concrete imaging is standardized, the methods of deploying the tools are not. SIM certification ensures the precision and attention to detail necessary for the accurate subsurface investigations that will keep projects on time, on budget, and safe.
The training program for GPRS 3D laser scanning services includes an additional 40 hours of LiDAR training on Leica scanning equipment, plus additional field experience.
GPRS Project Managers have elite training in concrete scanning and reality capture technologies, plus a field-tested methodology to deliver high-quality results tailored to each project’s needs.
GPRS Intelligently Visualizes the Built World® above and below ground as the leading national provider of accurate utility locating, concrete scanning & imaging, reality capture, video pipe inspection, leak detection, and mapping & modeling solutions for the construction, architecture, and engineering industries.
What can we help you visualize?
Frequently Asked Questions
What Types of Concrete Scanning are There?
GPRS provides two specific but different concrete scanning services: elevated concrete slab scanning and concrete slab-on-grade locating. Elevated concrete slab scanning involves detecting embedded electrical conduits, rebar, post-tension cables, and more before core drilling a hole through the slab. Performing a concrete slab-on-grade locating service typically involves scanning a trench line for conduits before conducting saw cutting and trenching to install a sanitary pipe, water line, or something similar.
Who Needs Concrete Scanning?
Clients turn to us for concrete scanning for a range of needs, from verifying the placement of rebar to safely drilling or cutting into post-tension slabs without damaging the tensioned cables.
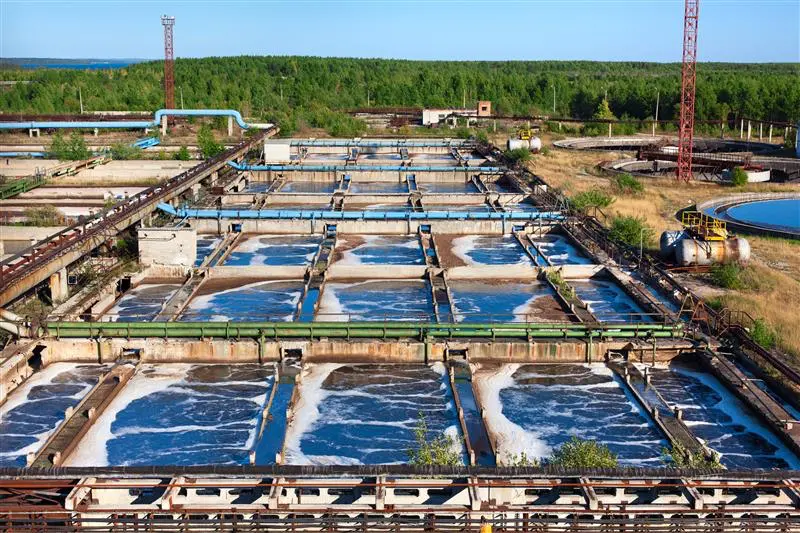
Largest Water Treatment Plant in Arkansas to Receive $230 Million Overhaul
The largest water treatment plant in the State of Arkansas is set to receive a $230 million overhaul.
The Jack H. Wilson Water Treatment Plant in west Little Rock is being renovated to deal with new regulations, changes to its water source and any emerging contaminants while increasing its treatment capacity from 133 million gallons per day to 150 million, according to an article in the Northwest Arkansas Democrat-Gazette.
One of Central Arkansas Water’s two water treatment facilities, the nearly-70-year-old Wilson plant receives water from the Lake Maumelle reservoir. This renovation project is Central Arkansas Water’s biggest ever, according to reporting by Construction Dive, which spoke with Central Arkansas Water spokesperson, Douglas Shackelford.
Construction will be conducted in phases, with the facility remaining operational throughout. Work is expected to take about five years to complete.
“This plant is vital to our system, and so we can’t shut it down. It’s got to be operational while construction is going on,” Shackelford said. “There are four large water basins in the facility, and we will essentially shut down one and renovate that basin and then keep the other three open and working while one is under construction.”
“[New technology is] going to allow us to move the water through it at a faster pace that would allow for the capacity increase,” he continued. That will “help us out in the long run, because obviously, as cities grow and demand goes higher for water, we need to be able to produce it.”
The Max Foote Construction Co. is the project’s construction manager at-risk. Unlike with Design-Build projects, during construction manager at-risk projects, design and construction are separate contracts and criteria other than lowest total construction cost factor into the selection of the construction manager.
“CM-at-Risk allows for the early project involvement of a CM who can partner with the A/E and Agency to provide constructability assistance, estimating, design review and early procurement opportunities,” writes Associated General Contractors (AGC) of America. “Additionally, the start of construction can begin prior to 100% complete design documents. The CM-at-Risk typically also provides detailed cost estimates early in the design phase, so that value engineering and cost reduction ideas can be considered when they are the most easily addressed.”
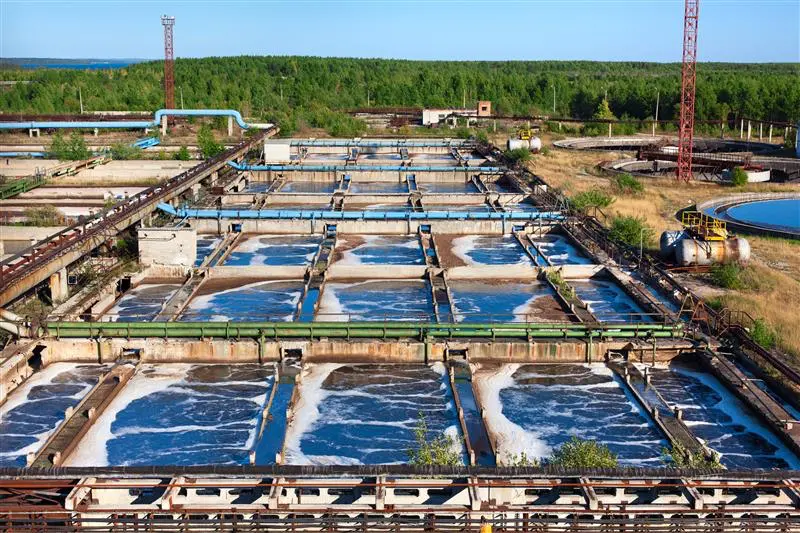
The State of America’s Drinking Water Infrastructure
Arkansas’ investment in its largest water treatment facility comes just as the nation is seeing the first positive signs from recent, widespread investments in critical infrastructure.
America’s infrastructure received its highest-ever grade in the American Society of Civil Engineers’ 2025 Report Card for America’s Infrastructure. The country received an overall grade of “C”, with eight of the 18 categories assessed by ASCE seeing grade increases, and – for the first time since 1998 – no categories receiving a rating of D- or lower.
“For more than two decades, the message behind the unflattering grades was consistent: federal, state, and local governments, in addition to the private sector, have not been prioritizing our interdependent infrastructure systems,” the ASCE wrote in the 2025 report card’s executive summary. “In sum, the bill on our infrastructure systems was past due. We needed to reverse the nation’s growing infrastructure investment gap to remain competitive in the global marketplace, allow local businesses to thrive, and keep our families safely connected. That message grew louder with each evaluation, through our most recent Report Card release in early 2021”.
Drinking water received a grade of C-. This was the same grade it earned in the previous report card released in 2021, with the ASCE noting in the 2025 report the need for additional funding to assess this infrastructure’s shortcomings.
“The nation’s water infrastructure is aging and underfunded,” the ASCE wrote. “More than 9 million existing lead service lines pose health concerns, and in 2023, the Environmental Protection Agency (EPA) determined that the nation’s water infrastructure needs stand at $625 billion over 20 years. That exceeds EPA’s 2018 assessment by more than $150 billion. The 2021 Infrastructure Investment and Jobs Act (IIJA) invested more than $30 billion for drinking water capital improvements, removal of lead service lines, and addressing emerging contaminants such as per- and polyfluoroalkyl substances (PFAS). However, funding shortfalls continue in state revolving funds that support drinking water.”
In addition to the advanced age of much of the U.S.’s water infrastructure, the ASCE outlined other challenges in this sector such as emerging contaminants and the increasingly severe effects of extreme weather.
The ASCE said that the implementation of asset management plans is a critical step needed to address the challenges facing America’s drinking water infrastructure.
“Many drinking water utilities are actively improving infrastructure through innovations such as asset failure prediction technologies, which improve the ability to identify issues before they become failures. Unfortunately, only about 30% of utilities have fully implemented an asset management plan, and just under half are in the process of implementing one.”
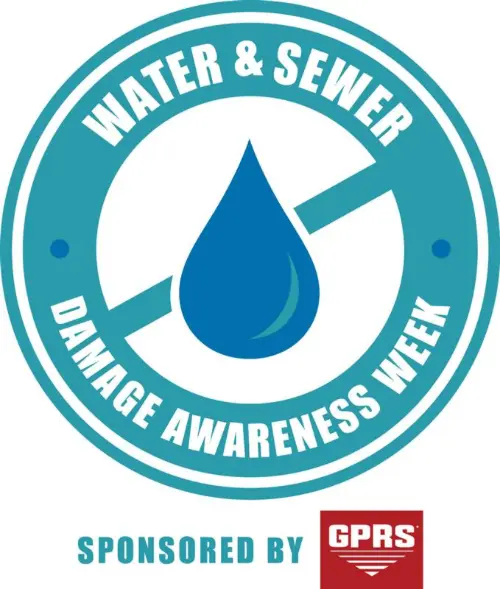
Let GPRS Help You Maintain Your Water Infrastructure
GPRS is committed to helping you maintain the drinking water infrastructure under your care.
We offer pinpoint-accurate leak detection services that utilize acoustic leak detection and leak detection correlators to ensure your water stays where it belongs. And our comprehensive suite of subsurface damage prevention, existing conditions documentation, and construction & facilities project management services help you plan, manage, and build better.
Our commitment to helping you maintain your infrastructure extends beyond the services we offer. GPRS also sponsors Water & Sewer Damage Awareness Week, an annual safety initiative designed to help water and wastewater system operators take a more proactive approach to maintaining their infrastructure.
During this event, our safety experts travel to your job site, office, council meeting – wherever you need us – to deliver free safety presentations to municipalities, engineers, facility managers, property management groups, and anyone else who is ready to regain control of their fresh and wastewater infrastructure.
Click here to schedule your free WSDAW presentation today!
Frequently Asked Questions
How many miles of underground water pipe can GPRS test for leaks in a single day?
While it can depend on a variety of factors, our leak detection Project Managers typically can inspect up to 10 miles of pipe a day on a metallic system (cast iron/ductile) and one contact point (hydrant/valve) per minute.
Can GPRS determine the size of a located leak?
After analyzing thousands of previous leaks detected, we asked clients to send us pictures of the remediation. This information has helped us compare our final leak signal detected with the results of the actual leak. We determine the size of the leak by how far the leak signal travels between contact points and the pitch of the tone received. We do not, however, produce formal leak estimations.
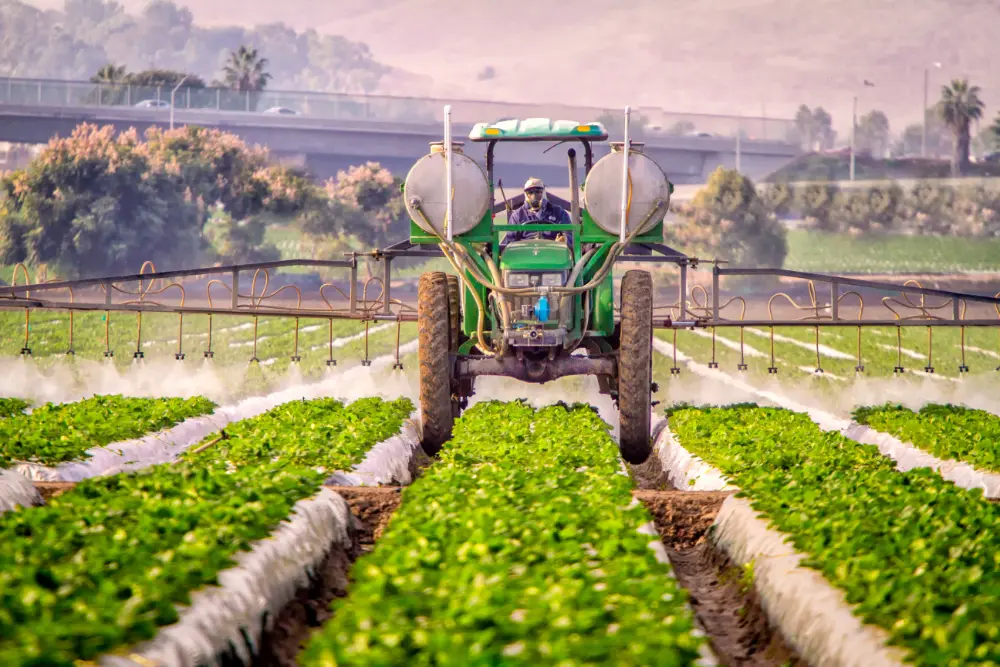
Semi-Volatile Organic Compounds (SVOCs) Explained
Semi-volatile organic compounds, or SVOCs, are – as their name suggests – less volatile than volatile organic compounds (VOCs). But SVOCs still pose significant implications for indoor air quality, environmental contamination, and human health.
What Are Semi-Volatile Organic Compounds?
SVOCs are a class of organic chemicals characterized by their intermediate vapor pressures, typically ranging from 10⁻¹¹ to 10² Pascals at room temperature.
This property places them between VOCs, which readily evaporate into the air, and non-volatile compounds, which tend to remain in solid or liquid form.
SVOCs include a wide variety of chemical families such as:
- Phthalates: Used as plasticizers
- Polybrominated diphenyl ethers (PBDEs): Used as flame retardants
- Polychlorinated biphenyls (PCBs): Formerly used in electrical equipment
- Pesticides (e.g., DDT, chlorpyrifos)
- Polycyclic aromatic hydrocarbons (PAHs): Byproducts of combustion
These compounds are typically found in both indoor and outdoor environments, often persisting in dust, on surfaces, and in the air.
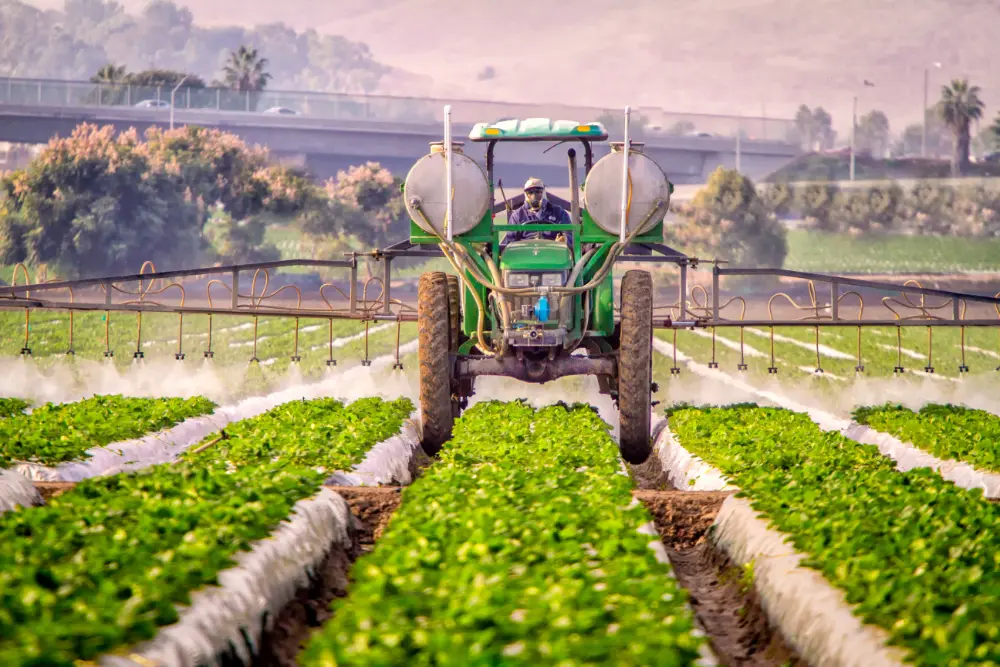
Sources of SVOCs
SVOCs originate from a wide array of sources, both anthropogenic and natural. Common indoor sources include:
- Consumer products: Personal care items, cleaning agents, and air fresheners.
- Building materials: Paints, sealants, adhesives, and vinyl flooring.
- Furnishings: Upholstered furniture, carpets, and electronics.
- Combustion processes: Tobacco smoke, cooking, and heating appliances.
Outdoors, SVOCs are released through industrial emissions, vehicle exhaust, pesticide application, and the degradation of other organic compounds.
Behavior and Fate in the Environment
Unlike VOCs, which tend to dissipate quickly into the atmosphere, SVOCs exhibit a more complex behavior due to their dual-phase nature. They can exist in both the gas phase and adsorbed onto particles or surfaces. This characteristic leads to several important environmental behaviors:
- Partitioning: SVOCs partition between air, dust, water, and surfaces. Indoors, they often accumulate in settled dust and on surfaces like walls and furniture.
- Persistence: Many SVOCs are chemically stable and degrade slowly, leading to long-term environmental presence.
- Bioaccumulation: Some SVOCs, particularly those with high lipid solubility, can accumulate in the fatty tissues of living organisms, magnifying their effects through the food chain.
Health Impacts of SVOCs
Exposure to SVOCs can occur through inhalation, ingestion (especially of dust), and dermal contact. The health effects vary depending on the specific compound, concentration, duration of exposure, and individual susceptibility. Some of the documented and suspected health impacts include:
- Endocrine disruption: Certain phthalates and flame retardants can interfere with hormone systems, potentially affecting reproductive and developmental health.
- Respiratory issues: Inhalation of SVOCs may exacerbate asthma and other respiratory conditions.
- Neurotoxicity: Compounds like PBDEs have been linked to cognitive and behavioral effects, particularly in children.
- Carcinogenicity: Some SVOCs, such as PAHs and PCBs, are classified as probable or known human carcinogens.
Children are particularly vulnerable due to their developing systems and behaviors such as hand-to-mouth activity, which increases ingestion of contaminated dust.
SVOCs in Indoor Environments
Indoor environments are of particular concern because people spend most of their time indoors – at home, work, or school. SVOCs can be released slowly over time from materials and products, leading to chronic low-level exposure. Factors influencing indoor SVOC levels include:
- Ventilation: Poor ventilation can lead to accumulation of SVOCs.
- Temperature and humidity: Higher temperatures can increase SVOC emissions from materials.
- Cleaning practices: Dust removal can reduce SVOC reservoirs, but some cleaning products may also introduce new SVOCs.
Studies have shown that indoor dust can contain significant concentrations of SVOCs, making it a major exposure pathway, especially for young children.
Regulation and Standards
Regulatory oversight of SVOCs varies by region and compound. In the United States, several agencies play roles in monitoring and regulating SVOCs:
- Environmental Protection Agency (EPA): Regulates pesticides and industrial chemicals under laws such as the Toxic Substances Control Act (TSCA).
- Consumer Product Safety Commission (CPSC): Oversees safety of consumer products, including restrictions on phthalates in children's toys.
- Occupational Safety and Health Administration (OSHA): Sets exposure limits for certain SVOCs in workplace settings.
Internationally, the European Union’s REACH regulation and the Stockholm Convention on Persistent Organic Pollutants (POPs) also address SVOC risks.
Mitigation and Exposure Reduction
Reducing exposure to SVOCs involves a combination of source control, environmental management, and personal behavior. Key strategies include:
Source Identification and Substitution
- Choose products labeled as low-emission or free of specific SVOCs
- Avoid materials known to contain phthalates or flame retardants
Improved Ventilation
- Use mechanical ventilation systems or open windows to dilute indoor pollutants
Dust Control
- Regular vacuuming with HEPA filters and wet dusting can reduce SVOC-laden dust
Temperature and Humidity Control
- Maintain moderate indoor temperatures and humidity to limit SVOC emissions
Policy and Advocacy
- Support regulations that limit the use of harmful SVOCs in consumer products and building materials
Future Directions and Research
Ongoing research continues to uncover the complexities of SVOC behavior, exposure pathways, and health effects. Emerging areas of interest include:
- Cumulative risk assessment: Understanding the combined effects of multiple SVOCs and other pollutants.
- Green chemistry: Developing safer alternatives to SVOCs in industrial and consumer applications.
- Advanced monitoring technologies: Improving detection and quantification of SVOCs in various environments.
Semi-volatile organic compounds represent a significant yet often overlooked class of environmental contaminants. Their persistence, ubiquity, and potential for harm underscore the importance of awareness, regulation, and mitigation.
GPRS is the trusted leader for damage prevention in the environmental sector. Our project managers deliver results from the beginning of the initial investigation, throughout delineation and remediation, until project completion. With our nationwide network of Project Managers, we are equipped to mobilize to projects across the United States.
From sewer lines to skyscrapers, GPRS Intelligently Visualizes The Built World® to keep your projects on time, on budget, and safe.
What can we help you visualize?
Frequently Asked Questions
What do I get when I hire GPRS to conduct a utility locate?
Our Project Managers flag and paint our findings directly on the surface. This method of communication is the most accurate form of marking when excavation is expected to commence within a few days of service.
GPRS also uses a global positioning system (GPS) to collect data points of findings. We use this data to generate a plan, KMZ file, satellite overlay, or CAD file to permanently preserve results for future use. GPRS does not provide land surveying services. If you need land surveying services, please contact a professional land surveyor.
Please contact us to discuss the pricing and marking options your project may require.
Can GPRS Project Managers distinguish between different underground utilities that they locate?
In most situations, we can identify the utility in question without any problems, although it is not always possible to determine what type of utility is present. When this happens, we attempt to trace the utility to a valve, meter, control box, or other signifying markers to determine the type of utility buried.
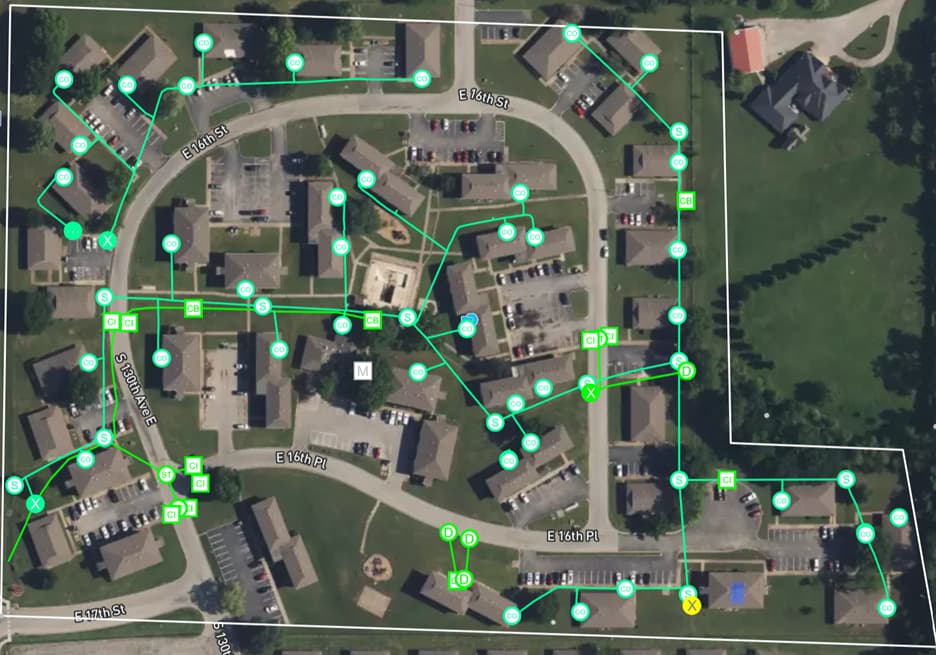
GPRS VPI Services Locate and Assess Conditions of All Sanitary and Storm Sewer Lines Across a 19-Acre Apartment Complex
GPRS helped locate all underground sewer and sanitary lines throughout a 19-acre apartment complex in Tulsa, Oklahoma.
The complex’s facility manager had no existing records of their 1950s-era subsurface infrastructure and was not aware of the current conditions of these lines. They needed an updated map of the built world beneath their feet.
GPRS Project Manager Joe Meyer was tasked with investigating the complex’s sewer and sanitary lines and provide a NASSCO-certified report on all blocked, defective, or obstructed pipes along with the map, so they could effectively plan repairs and maintenance.
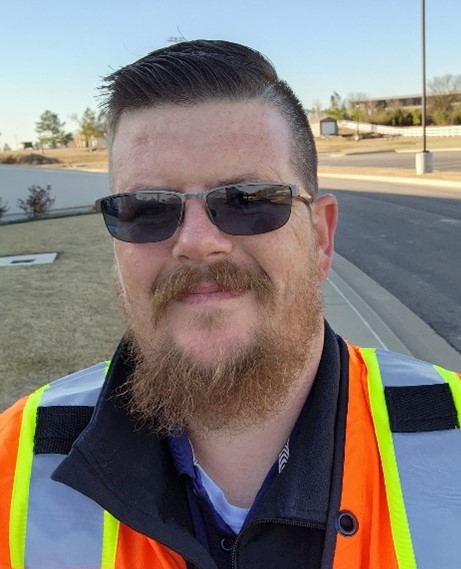
All GPRS Project Managers are NASSCO (National Association of Sewer Service Companies) certified in pipeline (PACP), lateral (LACP), and manhole (MACP) assessments.
GPRS Project Managers use the Envirosight ROVVER X Mainline Crawler to capture photo and video evidence of defects and other issues along sewer and stormwater lines. This remote-controlled rover can crawl as far as 1,640 feet into a sewer line and can adapt to inspect lines from 6” to 96” in diameter.
The ROVVER X SAT Lateral Launch camera can inspect sewer laterals from the mainline to identify any damages or defects, including cross bores, so clients can properly address them.
Push cameras, also known as flexible rodders, are used by GPRS Project Managers to access smaller spaces that crawlers can’t fit in, like vents, cleanouts, and toilet plumbing. The push camera also contains a sonde that can be detected by an electromagnetic (EM) locator to map non-metallic pipes.
“For this job, I inspected and located 3,411 linear feet of underground pipes, including 1,823 feet of sanitary and storm sewer mainline and 1,588 feet of sanitary sewer lateral lines,” Meyer said.
The 75-year-old infrastructure presented challenges Meyer had to overcome, including the design of the pipes.
“There was no sweep to the clean outs, they were straight 90 [degrees], so there was some trouble trying to get the camera to swoop into them,” he explained. “That was a challenge, but I was able to overcome that by using that SAT launcher from the mainline and when I got one halfway, I could meet up with the other [from the other side of the mainline].”
Meyer also found himself getting creative to access manholes that were in difficult to access locations.
“There was a gated swimming pool area that had a manhole right in the corner of the gate,” he said. “I had to set up in a weird way, so that was kind of fun, but I overcame that challenge.”
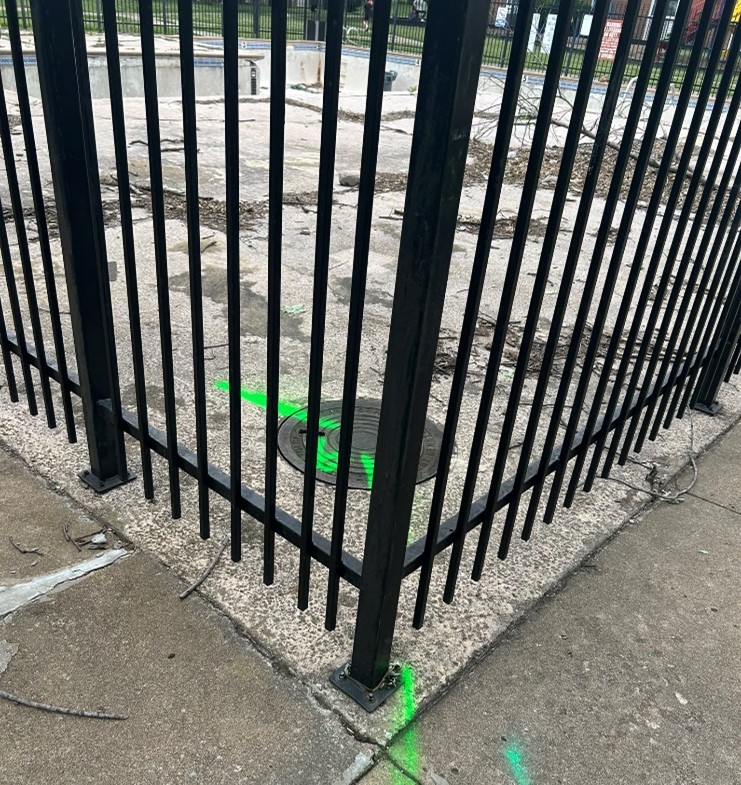
This job was conducted during the first week of June, so Meyer was faced with a fun challenge since summer vacation had begun for the kids in the neighborhood.
“It was right when school got let out, so all my flags disappeared overnight,” Meyer said. “That was pretty funny, so I didn't put any more flags down after that once I knew that they were all fair game. There were tons of kids around and there were some of them having fun watching what I was doing and seeing me test my crawler.”
Once he finished his investigation, Meyer provided the client with a map depicting the location of their sewer and sanitary lines via SiteMap® (patent pending), GPRS’ cloud-based infrastructure mapping platform. With SiteMap, the client can securely access their records 24/7 as they plan any upcoming renovation or restoration projects.
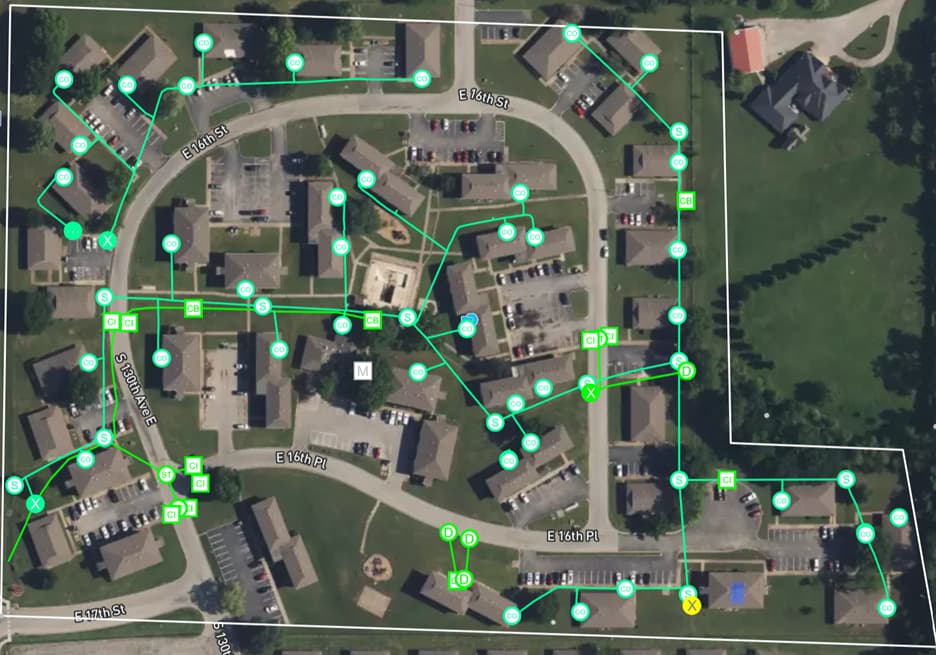
A NASSCO-certified Video Pipe Inspection report was created detailing the condition of the pipes and ranking defects by severity. Meyer did find some obstructions within the pipes that he was able to relay to the client so they can make necessary repairs.
“I found I had three units that did not have an external clean out and I could not access it from the main[line],” Meyer explained. “I also found a few clean outs that were completely full of dirt that maintenance had to come take care of while I was there. And I gave them a list, with priority, of what they can work on, so, all in all, it was helpful for them, even beyond just the mapping.”
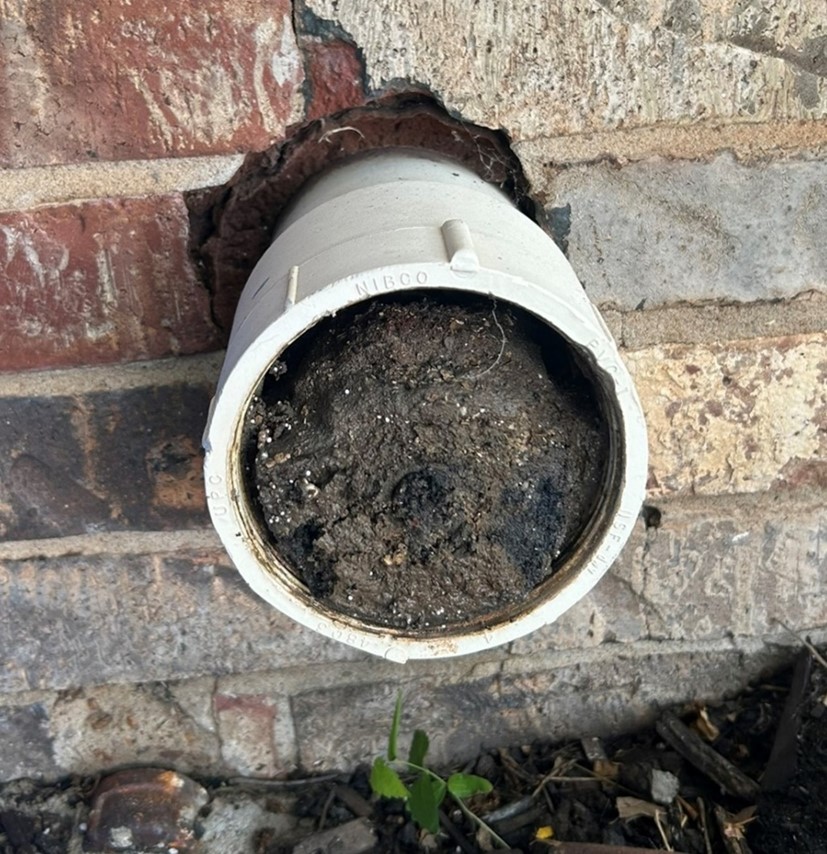
Even, with the hurdles to overcome, Meyer completed his work within the client’s timeline.
“Everything really went well and it went on time as expected,” Meyer explained. “I kept in contact with the site contact and he was appreciative of that.”
From sewer line inspections to skyscraper scans, GPRS Intelligently Visualizes the Built World® to keep your projects on time, on budget, and safe.
What can we help you visualize?
FREQUENTLY ASKED QUESTIONS
What size sanitary sewer and stormwater pipes can GPRS inspect with its Video Pipe Inspection service?
Our elite, NASSCO-certified VPI Project Managers have the capabilities to inspect pipes from 2” in diameter and up.
What deliverables does GPRS offer when conducting a VPI?
GPRS is proud to offer WinCan reporting to our Video Pipe Inspection clients. Maintaining sewers starts with understanding sewer condition, and WinCan allows GPRS Project Managers to collect detailed, NASSCO-compliant inspection data. GPRS Project Managers not only inspect the interior condition of sewer pipes, laterals, and manholes – they can also provide a map of their location. The GPRS Mapping & Modeling Department can provide detailed GPS overlays and CAD files. Our detailed WinCan/NASSCO reports contain screenshots of the interior condition of the pipe segments that we inspect, as well as a video file for further evaluation, documentation, and/or reference.
.webp)
$250M Expansion of South Bay Wastewater Treatment Plant Fast-Tracked in San Diego
In a bold move to address one of the most persistent environmental and public health challenges on the U.S.-Mexico border, PCL Construction and Stantec have announced a $250 million expansion of the South Bay International Wastewater Treatment Plant in San Diego. According to a recent article in Engineering News-Record, the project has been fast-tracked in response to ongoing cross-border sewage flows from Tijuana, Mexico, and represents a landmark in binational infrastructure collaboration and environmental engineering.
The expansion, awarded under a $42.4 million progressive design-build contract, will double the plant’s treatment capacity from 25 million to 50 million gallons per day (MGD). This represents a significant increase from the previously targeted 35 MGD. This upgrade is critical to mitigating the decades-long issue of untreated sewage entering the Tijuana River and flowing into the Pacific Ocean near the South Bay community of Imperial Beach.
.webp)
A Technical Blueprint for Resilient Water Treatment
At a public forum hosted by the U.S. Section of the International Boundary and Water Commission (IBWC) on June 12, Michael Watson, Senior Vice President of Major Projects (Water) at Stantec, and Jeff Newman, Operations Manager at PCL, outlined the technical roadmap for the expansion.
The project scope includes:
• A new integrated headworks system for improved preliminary treatment
• Two new primary sedimentation tanks and 10 secondary sedimentation tanks
• Seven activated sludge tanks to enhance biological treatment
• A new chemical treatment system
• Sludge thickening and storage facilities
• A 12-kV electrical building with upgraded switchgear and transformers provided by San Diego Gas & Electric
“In partnership with PCL, we will work hard to provide the most seamless plant expansion possible,” said Watson. “We believe the repairs and changes we are undertaking will make a measurable difference both now and in the future.”
This expansion is a major milestone for wastewater treatment plant capacity and a model for how modern water treatment infrastructure can be scaled to meet urgent environmental demands.
A Binational Challenge with Global Implications
Mexico’s military has completed the expansion of the Punta Bandera Wastewater Treatment Plant, but concerns remain about long-term capacity and maintenance. With Tijuana’s population doubling over the past two decades, infrastructure resilience is more critical than ever.
The South Bay expansion goes beyond a local project, it’s a model for international cooperation, resilient infrastructure, and environmental justice. It demonstrates how engineering, policy, and technology must converge to solve complex, cross-border challenges.
How GPRS Supports Infrastructure Companies with Precision and Safety
With excavation, retrofitting, and utility integration at the core of the project, GPRS brings essential visibility and verification to ensure construction proceeds safely and without costly delays.
A trusted partner to infrastructure companies across North America, GPRS has demonstrated its value in complex environments, such as a recent California trenching project, helping teams avoid utility strikes and maintain excavation safety.
In projects where excavation, retrofitting, and utility integration are central to success, GPRS supports contractors and engineers by delivering detailed utility mapping and structural scanning before any ground is broken. This helps prevent utility strikes, ensures safe trenching, and allows for confident decision-making during construction. GPRS’ concrete scanning services help identify embedded elements like rebar and post-tension cables, reducing the risk of structural damage during coring or cutting.
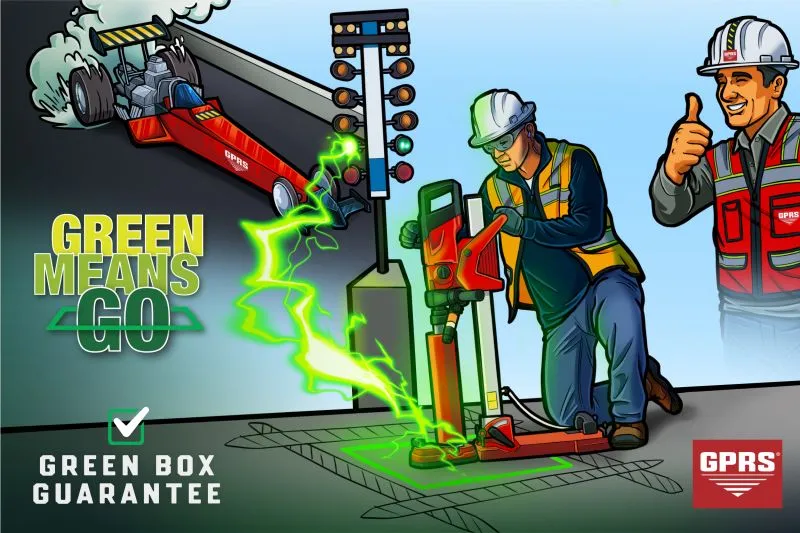
Leak detection is another key consideration in wastewater infrastructure. GPRS uses advanced acoustic technologies to identify leaks in pressurized systems, helping project teams maintain system integrity and avoid environmental or operational setbacks. In addition to acoustic methods, GPRS water loss specialists leverage a full suite of tools – including leak noise correlators, video pipe inspection, ground penetrating radar (GPR), and electromagnetic (EM) locating to accurately detect and pinpoint leaks. This service help clients reduce water loss, avoid costly emergency repairs, and maintain compliance with environmental regulations.
Video pipe inspection (VPI) provides a clear assessment of existing underground pipelines, ensuring that legacy systems are properly evaluated before integration with new components.
All this data is captured and delivered through SiteMap® (patent pending), GPRS’ cloud-based infrastructure mapping and facility management platform. It centralizes utility maps, inspection reports, and 3D models in one secure location. Project teams can access this information anytime, from anywhere, from any computer, tablet or smartphone. Improving coordination between field crews, engineers, and facilities managers, SiteMap also streamlines workflows and reduces the risk of miscommunication.
.webp)
From skyscrapers to sewer lines, GPRS Intelligently Visualizes The Built World® to keep your projects on time, on budget, and safe.
What can we help you visualize?
FREQUENTLY ASKED QUESTIONS
How does utility locating help prevent delays in wastewater treatment plant construction?
Utility locating is essential in large-scale infrastructure projects like wastewater treatment plant expansions. GPRS uses advanced ground penetrating radar (GPR) and electromagnetic (EM) locating technology to accurately map underground utilities before excavation begins. This prevents accidental utility strikes, reduces costly rework, and keeps construction on schedule.
Why is leak detection important in water treatment infrastructure?
Leak detection ensures the integrity of pressurized systems and prevents water loss, contamination, and environmental hazards. In wastewater and water treatment facilities, undetected leaks can lead to regulatory violations and operational inefficiencies. GPRS uses acoustic leak detectors and leak detection correlators to identify leaks early, helping infrastructure companies maintain system performance and avoid costly repairs.
What role does SiteMap® play in managing complex infrastructure projects?
SiteMap is designed to centralize and simplify access to critical subsurface data. It allows project teams to view and manage utility maps, inspection reports, and site documentation in one secure, cloud-based environment. By organizing high-resolution data collected from services like utility locating, video pipe inspection, and concrete scanning, SiteMap enhances coordination, reduces risk, and supports informed decision-making throughout the lifecycle of an infrastructure project.
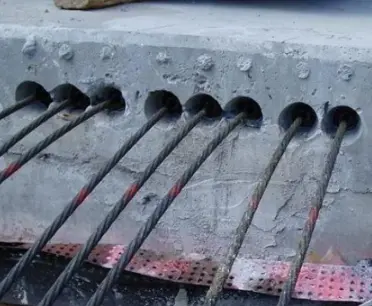
How Post-Tensioned Cables Are Anchored In Concrete Slabs
Post-tensioned (PT) slabs are essential in modern construction, especially high-rise construction, because they offer efficiency, durability, and the ability to span longer distances while reducing material usage.
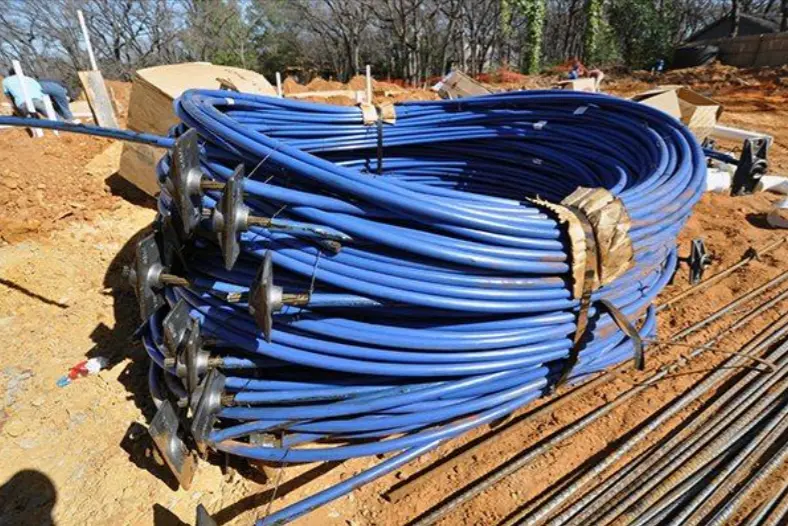
Unlike precast slabs, PT slabs are cast-in-place, meaning the concrete is poured on-site, allowing flexibility in design and construction. Embedded within the slab are post-tensioning cables, made of high-strength steel tendons, which are positioned before the concrete pour and later tensioned. Once the concrete reaches adequate strength (2,500 – 3,000 psi), the cables are anchored and stressed, compressing the slab to enhance its structural integrity. Proper installation and anchoring of PT cables ensure minimal deflection, reduced cracking, and increased load-bearing capacity.
Installation and Sequence of Post-Tensioned Slab Creation
The installation of post-tensioned cables follows a precise sequence to ensure reliable performance. Before any concrete is poured, the post tension tendons are laid out in specific locations and/or patterns. The individual tendons are housed within ducts or sleeves to prevent direct contact with the concrete, to reduce friction during stressing.
The cables are then anchored at their dead end, where they remain fixed, while the live end is left accessible for later tensioning. These are the “spaghetti ends” you can see emerging from the center of a newly poured PT slab to dangle over the side. In truth, the cable can be tensioned from either side, but the dead end generally arrives already seated in its anchor plate from the manufacturer, which will be grouted and capped after tensioning occurs.
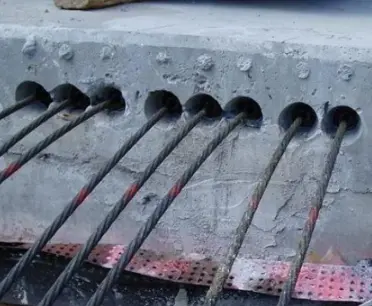
Once the cables are in position – in either a uniform or banded layout – concrete is poured and allowed to cure. The generally required compressive strength for these tendons is 3,500 to 5,000 psi before stressing. Once the concrete has cured, the molds used to frame it are removed and hydraulic jacks are employed at each live end to stretch the tendon to its designed tension level, after which anchors secure the tendons permanently within the slab.
What is the Difference Between Dead End and Live End Anchoring?
Each PT cable features two anchor points:
• The dead end is embedded in the concrete before it is stressed. The dead ends of the tendons are secured by fixed anchor plates, locking them into position to prevent movement.
• The live end is where the “magic” happens because that’s where tensioning occurs. Each live end is exposed post-cure, so that the hydraulic jack can pull them to the necessary force before locking them in place. Once the tendons are secured, the stressing pocket is typically grouted or encased in concrete to protect the anchorage system.
Composition and Specifications of PT Cables & Anchors
Post tension cables are engineered to withstand significant tension forces while maintaining flexibility during installation. They are composed of high-strength steel tendons, ranging in diameter from 3/8" to 1/2", and are encased to reduce friction and shield them from corrosion.
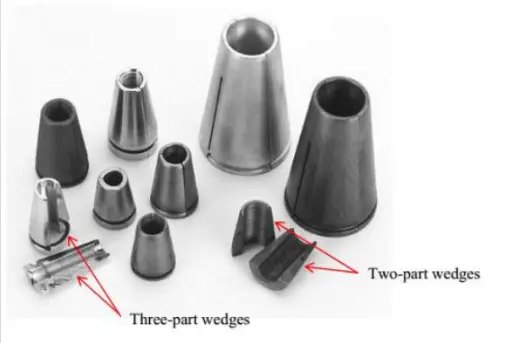
Anchor wedges, plates, and encapsulations are integral components of the system, ensuring a secure attachment to the concrete structure. Grout is applied in bonded post-tensioning systems, to provide added durability and prevent destructive moisture intrusion, particularly in applications requiring long-term exposure to environmental elements.
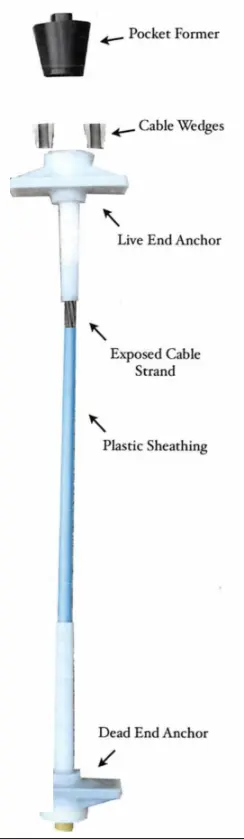
Anchoring Mechanisms and Types of PT Anchors Explained
Anchoring post-tensioned cables requires specialized components to ensure stability and load distribution. At the dead end, fixed anchors secure tendons before tensioning begins, preventing unwanted movement within the slab. The live end allows controlled tensioning, where cables are individually stretched before locking them permanently.
There are several types of PT anchors and components used based on structural requirements.
Pocket formers are devices that form temporary recesses in the concrete to allow for stressing.
Flat plate anchors are frequently used in thin slabs because they offer reliable load distribution while minimizing bulk.
Multi-strand anchors accommodate multiple cables and are common in bridge decks and large-scale concrete structures, due to their need for high-capacity tensioning.
Barrel anchors, which are compact in design, provide effective solutions for space-constrained applications while maintaining performance.
Anchor/Cable Wedges are pieces of tapered, heat-treated, high-strength steel, whose serrations (teeth) penetrate the prestressing steel during the transfer of prestressing force. Anchorage systems sometimes contain two-part or three-part wedges.
Each anchoring method is selected based on load demands, slab thickness, and expected structural movement.
How Do You Reinforce PT Anchors?
Post-tensioned cable anchors experience high localized stresses, so they often require additional reinforcement to maintain stability.
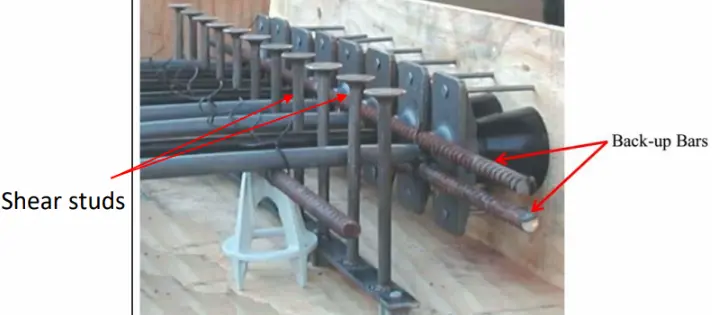
Bursting steel is incorporated around the live-end anchors to mitigate stress concentrations and prevent cracking or failure.
Shear studs enhance anchorage integrity by increasing resistance against movement, especially in applications subjected to dynamic loads.
Back-up bars assist in distributing the force across a broader surface area, reducing stress buildup and improving durability.
Together, these reinforcement strategies ensure the longevity and reliability of post-tensioned slab systems and reduce the risk of long-term degradation.
What Happens After the PT Slab is Tensioned?
When a PT cable is tensioned, it’s generally carrying about 80% of its tensile force. The average PT cable has a tensile strength of 270,000 pounds per square inch (psi). The stressing force for the average ½-inch 270 strand is used, which puts the stressing force at around 33,000 pounds. For comparison, rebar typically yields 60,000 psi.
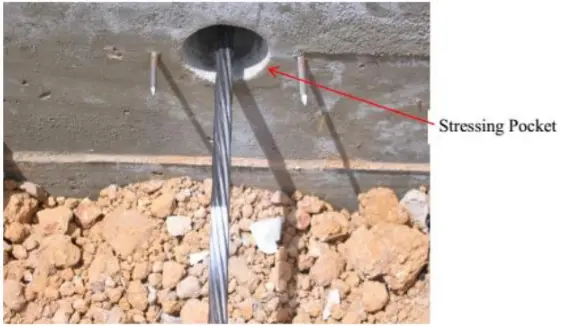
Once tension has been applied to the PT cable, its elongation is measured. A paint mark placed on the cable at end of the slab before it is tensioned allows you to measure the elongation post-tensioning. The area in which this takes place is called the cable’s stressing pocket: the recess created by the pocket that is formed between the stressing or intermediate anchorage and the edge of the concrete that allows nosepiece access for stressing. If you’re checking elongation on the dead end, it is then cut and the pocket grouted over.
Detecting Post-Tensioned Cables Using Ground Penetrating Radar
Ground penetrating radar (GPR) is an effective tool for identifying embedded PT cables within concrete slabs. Unlike the uniform grid-like patterns of rebar reinforcements, post-tensioned tendons display curved profiles, due to their specific placement and stressing process. Anchorage zones, particularly on live ends, generally produce stronger signal reflections. This allows construction engineers and GPRS Project Managers to differentiate between fixed-end anchors, stressing pockets, and the paths of the tendons.
GPR technology is frequently utilized as part of structural assessments, retrofits, and post-construction modifications, to provide contractors accurate locations of all PT slab reinforcements, and to provide safe cutting, coring, and drilling clearances. The cables can also be placed in banded columns for additional reinforcement near pillars and elevator shafts, so it’s vital to know which kind of PT layout you’re dealing with prior to making any cuts into the slab.
The correct anchoring of post-tensioned cables is essential to achieving structural integrity and optimizing the performance of PT slabs. From installation and dead/live end anchoring to reinforcement measures and detection methods, each step in the process plays a critical role in ensuring reliability. Understanding the nuances of post-tensioning is crucial to maximizing efficiency while maintaining compliance with industry standards and keeping work teams safe.
GPRS is the only company in the U.S. that offers the Green Box Guarantee. Since 2017, our Project Managers have maintained a 99.8% accuracy rate in concrete scanning & imaging, so if we mark out a green box that says clear, we guarantee that you will not strike a PT cable or reinforcement. If you do, we’ll pay the material cost to repair it.
Frequently Asked Questions
How does GPR find post tension cables in concrete?
Ground penetrating radar (GPR) is used to locate post tension cables by emitting high-frequency radio waves into concrete and analyzing the reflected signals – that show up on a readout screen as hyperbolas – to identify embedded objects based on their dielectric properties and depth.
Learn more about how GPRS uses GPR, here.
What happens when a post tension cable is accidentally severed?
Severing a post tension cable can cause it to snap back violently due to the high tension, which poses serious safety risks and can compromise the structural integrity of the slab. The average cost to replace a severed post tension cable is between $20,000 and $30,000.
Learn more about GPRS concrete services, here.
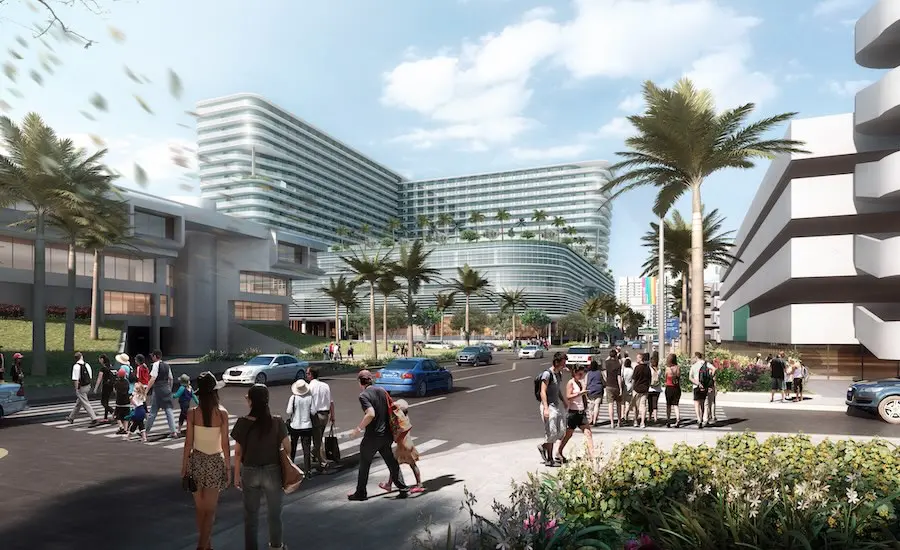
Balfour Beatty Breaks Ground on Miami Beach Hotel
GPRS safety partner Balfour Beatty has begun construction on the Grand Hyatt Miami Beach in Florida.
The $385 million construction services contract calls for the delivery of a 17-story, 996,130 s.f. hotel located at the intersection of 17th Street and Convention Center Drive, which will include 800 guestrooms – including 52 suites – as well as convention and meeting space, and ground floor retail areas.
According to a press release issued by Balfour Beatty, the construction company is undertaking the development on behalf of MB Mixed Use Investment, LLC, a partnership between developers Terra Group and Turnberry.
Once complete, the hotel will serve as the central anchor of the Miami Beach Convention Center District, “transforming the city’s convention center campus into a desirable meeting and convention destination worldwide,” the press release states.
“We are excited to partner with Terra Group and Turnberry, two highly regarded developers in South Florida, to deliver this transformative project for the Miami Beach community,” said Scott Skidelsky, Balfour Beatty’s President of Southeast Buildings Operations. “This project further strengthens our diverse business portfolio in South Florida, where hospitality continues to be an anchor market sector throughout Florida. We look forward to leveraging the experience of our South Florida team, who bring extensive expertise in the successful delivery of high-rise projects, hospitality and convention spaces.”
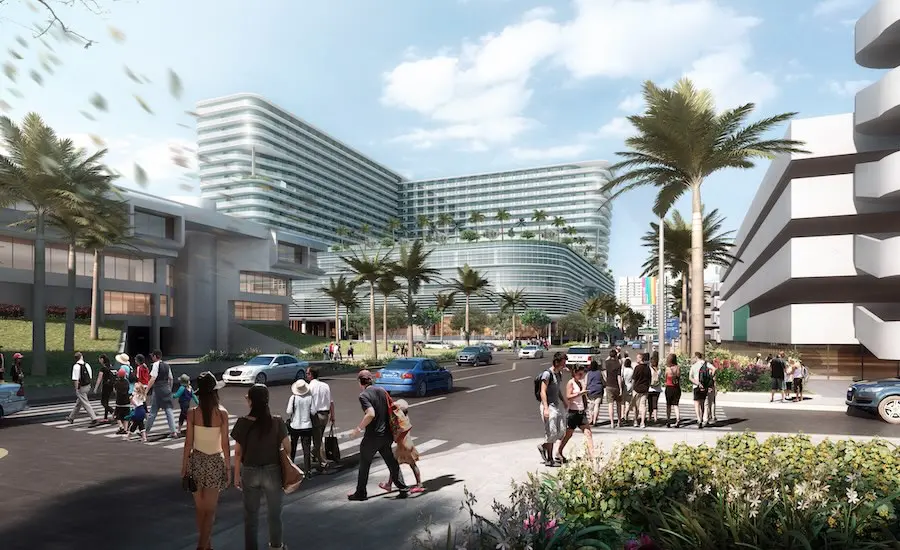
Construction on Grand Hyatt Miami Beach is scheduled for completion in late 2027. Balfour Beatty says the project will employ more than 500 workers at peak construction.
The hotel will feature a resort-style pool deck with panoramic views, five food and beverage outlets including a signature restaurant, a lobby lounge and bar, and fitness and spa facilities. The hotel’s design is being overseen by Arquitectonica and includes a podium with retail and restaurant spaces at street level and a covered drop-off area accessible from two streets.
According to the Miami Beach Convention Center website, the hotel is positioned “to integrate harmoniously with surrounding landmarks such as the New World Symphony and the Miami Beach Botanical Garden.”
“Grand Hyatt Miami Beach is a major investment in our city’s future – bringing jobs, quality year-round tourism, and long-term economic growth,” Miami Beach Mayor Steven Meiner told the MBCC. “Miami Beach remains a sought-after destination for its beauty and growing reputation as a safe, strong, and sophisticated city. This groundbreaking is further evidence that investor confidence in Miami Beach has never been higher.”
“This is a defining moment for our convention and trade show eco system,” added David Whitaker, President & CEO of the Greater Miami Convention & Visitors Bureau (GMCVB). “Grand Hyatt Miami Beach will further strengthen our ability to compete for premier meetings, trade shows and conventions by offering a level of integration and convenience that meeting planners increasingly value. With direct access to our state-of-the-art Miami Beach Convention Center and the vibrant energy of Miami Beach just steps away, this hotel adds an exciting new dimension to the experience we offer.”
According to reporting by Engineering News-Record, funding for the project is being supported, in part, by a $75 million grant awarded through the Miami Beach Redevelopment Agency in late 2024.
Balfour Beatty was selected to construct the hotel in 2023. The firm recently celebrated the completion of the $1.2 billion Broward Convention Center & Hotel and expansion project.
“The company's reputation as a premier hospitality builder in Florida as well as its continued commitment to delivering transformative projects that enhance communities throughout the state were key factors in being selected for this development [in Miami Beach],” Balfour Beatty said in its press release. “Balfour Beatty brings significant hospitality and convention center expertise to the project…”
Whether you’re building a luxury resort in the Sunshine State or a 60,000-seat football stadium in New York State, GPRS supports your construction projects through our comprehensive suite of subsurface damage prevention, existing conditions documentation, and construction & facilities project management services. We offer precision concrete scanning and utility locating, pinpoint-accurate leak detection, NASSCO-certified sewer line inspections, 2-4mm accurate 3D laser scanning, and in-house mapping & modeling tailored to your project’s specific needs.
All this accurate, actionable data is at your fingertips 24/7 thanks to SiteMap® (patent pending), GPRS’ project & facility management application that provides accurate existing conditions documentation to protect your assets and people.
From skyscrapers to sewer lines, GPRS Intelligently Visualizes The Built World® to help keep you on time, on budget, and safe.
What can we help you visualize?
Frequently Asked Questions
Will I need to mark out the utilities that GPRS locates?
GPRS will locate and mark all utilities for you. We have a variety of tools and markers we can use to highlight the locations of utilities, underground storage tanks and whatever else may be hiding.
What is the difference between a design intent and as-built model?
DESIGN INTENT – deliverables will be shown as a "best fit" to the point cloud working within customary standards, such as walls being modeled 90 degrees perpendicular to the floor, pipes and conduit modeled straight, floors and ceilings modeled horizontal, and steel members modeled straight. This will produce cleaner 2D drawings and will allow for easier dimensioning of the scan area. The deliverables will not exactly follow the scan data to maintain design intent standards. Most clients will want this option for their deliverables.
AS-BUILTS – deliverables will be shown as close as possible to actual field capture. If walls are out of plumb, pipes and conduit show sag, floors and ceilings are unlevel, steel members show camber, etc., this will be reflected in the model. This will produce reality-capture deliverables, but 2D drawings may show “crooked” or out of plumb lines, floors will be sloped or contoured, steel members may show camber, twisting or impact damage. Dimensioning will not be as easy due being out of plumbness/levelness, etc. This option should be used when the exact conditions of the scan area is imperative. Clients using the data for fabrication, forensic analysis, bolt hole patterns, camber/sag/deformation analysis, and similar needs would require this option.
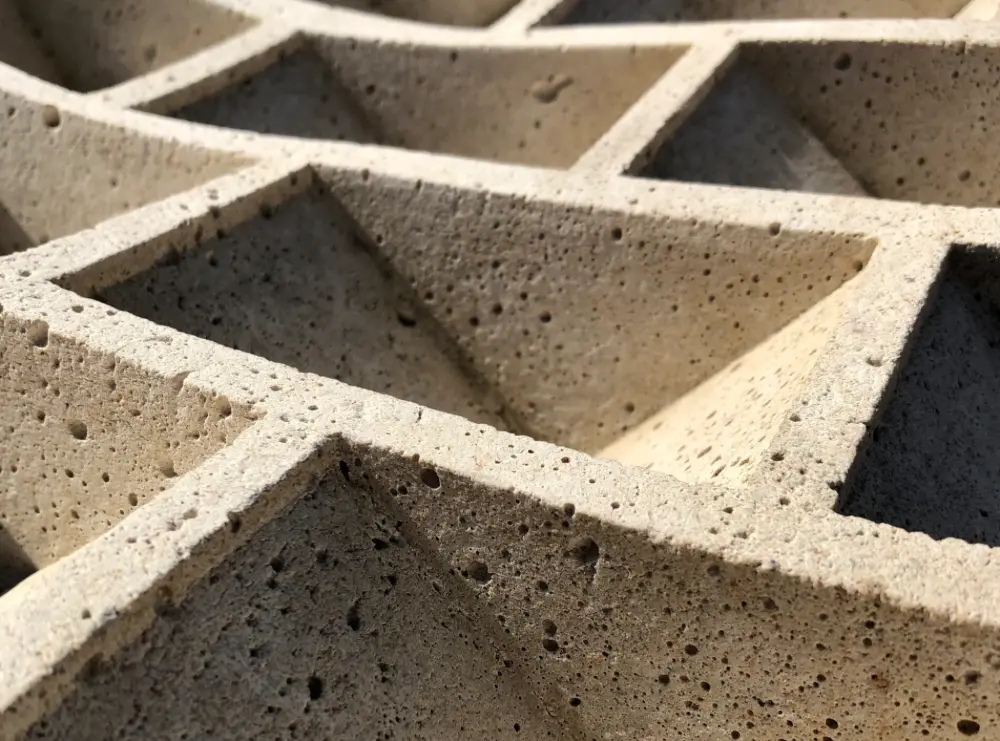
How Sound-Absorbing Acoustic Concretes are Leading a Quiet Revolution in Building Materials
There’s an innovation quietly making waves in the world of construction and materials science.
Sound-absorbing acoustic concrete has emerged as a promising solution for managing noise in urban environments, public infrastructure, and even residential spaces. While concrete has long been valued for its strength and durability, its acoustic properties have traditionally been a drawback. The high density and typically smooth surface of concrete walls and floors block sound transmission but struggle to absorb sound, leading to echoes and reverberations in enclosed spaces.
Now, researchers and engineers are reimagining concrete not just as a structural material, but as a tool for sound control.
What Is Acoustic Concrete?
Also known as sound-absorbing concrete, acoustic concrete is specially engineered and designed to reduce noise by absorbing sound waves rather than reflecting them.
Unlike traditional concrete, which tends to bounce sound back into the environment, acoustic concrete incorporates materials and design features that trap and dissipate sound energy.
This makes it particularly useful in settings where noise pollution is a concern, such as highways, tunnels, train stations, airports, schools, and office buildings.
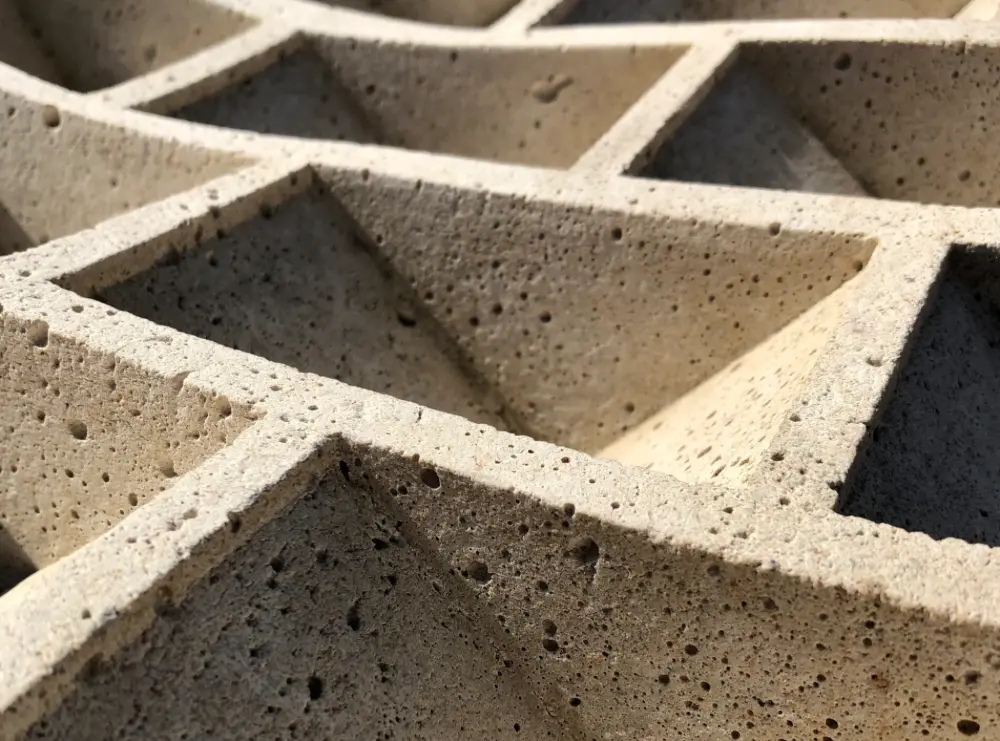
How Does Acoustic Concrete Work?
The sound-absorbing properties of acoustic concrete are achieved through a combination of material composition and structural design. Some key components of its structure are porosity, additive and aggregated materials, the level of perforation, and layered designs.
1. Porosity and Surface Texture
One of the key principles behind acoustic concrete is porosity. By introducing air voids or pores into the concrete matrix, sound waves can enter the material and lose energy as they bounce around within the pores. This process, known as sound attenuation, reduces the amount of noise that is reflected back into the environment.
The surface texture also plays a role. Rough or irregular surfaces scatter sound waves, further reducing their intensity.
2. Additives and Aggregates
Acoustic concrete often includes lightweight aggregates such as expanded clay, perlite, or recycled rubber. These materials not only reduce the density of the concrete but also enhance its ability to absorb sound. Some formulations also incorporate fibers or polymeric materials to improve acoustic performance.
3. Perforated or Layered Structures
In some applications, acoustic concrete is used in layered systems or combined with perforated panels. These designs create cavities or air gaps behind the concrete surface, which act as resonators to absorb specific frequencies of sound – particularly low-frequency noise – which is typically harder to manage.
What Are the Applications of Acoustic Concrete?
The versatility of acoustic concrete makes it suitable for a wide range of applications:
- Highway Noise Barriers: Acoustic concrete panels are used along highways to reduce traffic noise for nearby residential areas.
- Tunnels and Underpasses: These enclosed spaces can amplify sound. Acoustic linings help dampen echoes and improve safety.
- Public Transit Infrastructure: Train stations and subways benefit from reduced reverberation, improving both comfort and communication.
- Architectural Design: In schools, offices, and auditoriums, acoustic concrete can be integrated into walls or ceilings to enhance sound quality and reduce distractions.
- Industrial Facilities: Factories and plants use acoustic concrete to manage machinery noise and protect worker hearing.
Benefits and Limitations
Benefits
- Noise Reduction: The primary benefit is, of course, improved sound control.
- Durability: Like traditional concrete, acoustic variants maintain high strength and weather resistance.
- Fire Resistance: Unlike some synthetic acoustic materials, concrete is non-combustible.
- Sustainability: Some formulations use recycled materials, contributing to greener construction practices.
Limitations
- Cost: Acoustic concrete can be more expensive than standard concrete due to specialized materials and manufacturing processes.
- Weight: While some versions are lightweight, others may still be heavy, limiting their use in certain structures.
- Design Complexity: Achieving optimal acoustic performance often requires precise engineering and testing.
Current State of Innovation
The field of acoustic concrete is still evolving, with ongoing research focused on improving performance, reducing costs, and expanding applications.
Advanced Materials
Researchers are experimenting with nano-materials, bio-based additives, and 3D-printed structures to enhance sound absorption. These innovations aim to fine-tune the acoustic properties while maintaining structural integrity.
Smart Acoustic Panels
Some companies are developing modular acoustic concrete panels that can be easily installed and replaced. These panels may include embedded sensors to monitor environmental conditions or structural health.
Sustainability Integration
There’s growing interest in combining acoustic performance with environmental sustainability. For example, using recycled rubber or plastic waste as aggregates not only improves sound absorption but also diverts waste from landfills.
Urban Planning and Policy
Cities are beginning to incorporate acoustic concrete into noise mitigation strategies. In Europe and parts of Asia, regulations either encourage or mandate the use of sound-absorbing materials in new infrastructure projects.
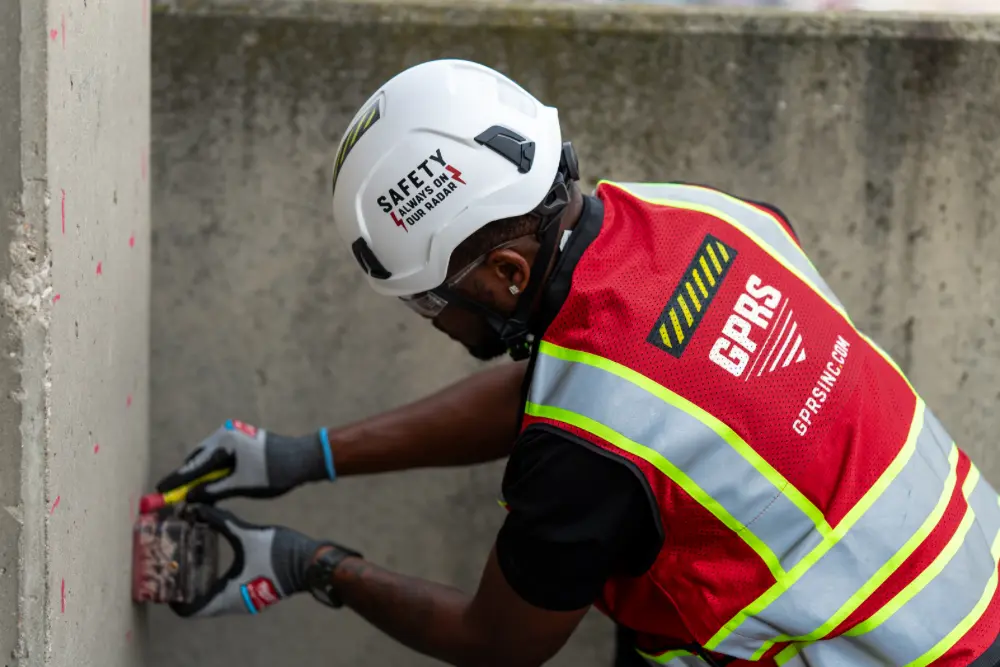
The Road Ahead
As urbanization continues and noise pollution becomes a more pressing concern, the demand for effective and durable sound-absorbing materials is likely to grow. Acoustic concrete offers a compelling solution that blends functionality, resilience, and innovation.
While challenges remain – particularly around cost and scalability – the trajectory of research and development suggests that acoustic concrete will play an increasingly important role in the built environment. Whether it’s making cities quieter, classrooms more focused, or factories safer, this material is helping to shape a more acoustically conscious future.
No matter how soundproof your concrete is, you need to know what’s embedded inside before you cut or core into it.
GPRS ensures the safety of your concrete coring and cutting projects by offering 99.8%+ accurate concrete scanning services that keep you on time, on budget, and safe. We utilize ground penetrating radar (GPR) scanning to find rebar, conduit, post tension cable, and anything else that, if struck by a saw or drill, could have costly and even dangerous consequences.
We are so confident in our SIM-qualified Project Managers that we introduced the Green Box Guarantee, which states that when GPRS places a Green Box within a layout prior to anchoring or coring concrete, we guarantee that the area will be free of obstructions.
If the area isn’t free of obstructions, GPRS will pay the material cost of the damage.
GPRS Intelligently Visualizes The Built World® to keep you on time, on budget, and safe.
What can we help you visualize?
Frequently Asked Questions
What types of concrete scanning are there?
GPRS provides two specific but different scanning services: elevated concrete slab scanning and concrete slab-on-grade locating. Elevated concrete slab scanning involves detecting embedded electrical conduits, rebar, post-tension cables, and more before core drilling a hole through the slab. Performing a concrete slab-on-grade locating service typically involves scanning a trench line for conduits before conducting saw cutting and trenching to install a sanitary pipe, water line, or something similar.
How is GPR used to identify tendons vs. rebar in a post-tensioned slab?
In post-tensioned structures, we typically find one mat of support rebar near the base of the slab. This mat is generally consistently spaced and remains at a constant elevation. Post-tension cables are generally found above this support mat and “draped” throughout the rest of the structure. The elevation of the cable is usually high near the beams and column lines and drapes lower through the span between beams and column lines. Knowledge of these structural differences allows us to accurately differentiate between components. Our Project Managers will leave you feeling confident in our findings and in your ability to drill or cut without issue.
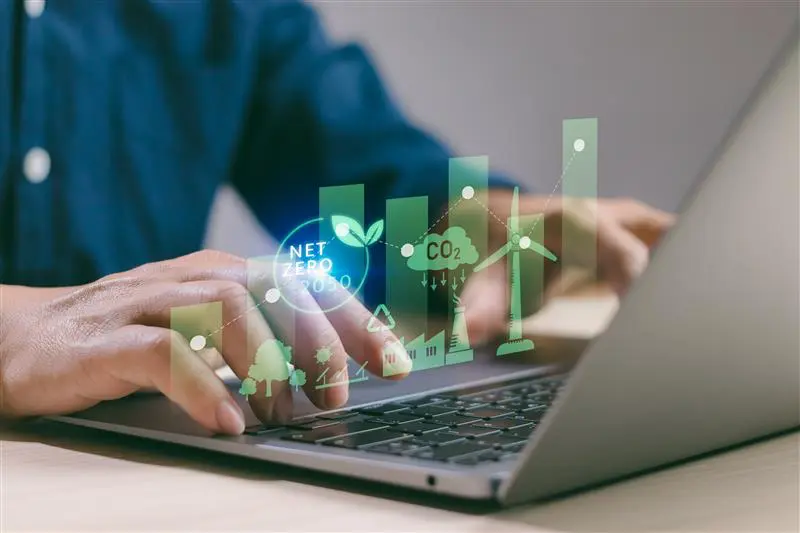
Net Zero Explained
The term "net zero" has become increasingly prominent in discussions about climate change, sustainability, and corporate responsibility.
Governments, businesses, and organizations around the world have made commitments to achieve net zero emissions by various target dates, often by mid-century.
But what does "net zero" actually mean – and why has it become such a central concept in environmental and economic planning?
What Is Net Zero?
At its core, net zero refers to the balance between the amount of greenhouse gases (GHGs) emitted into the atmosphere and the amount removed from it. Achieving net zero means that any emissions produced are offset by an equivalent amount of emissions removed, resulting in no net increase in atmospheric GHG levels.
The most commonly discussed greenhouse gas in this context is carbon dioxide (CO₂), but net zero targets often include other gases such as methane (CH₄) and nitrous oxide (N₂O), which also contribute to global warming.
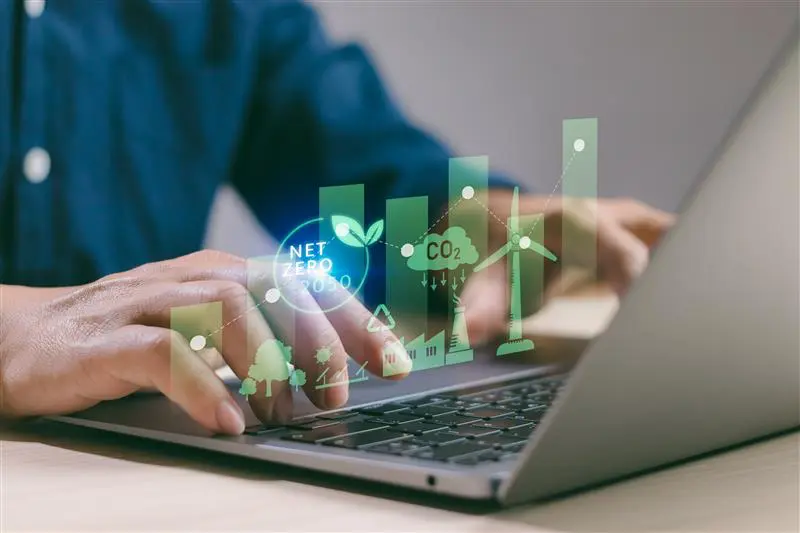
The Net Zero Equation
To reach net zero, entities must either:
- Reduce emissions through cleaner technologies, energy efficiency, and behavioral changes, and/or
- Remove emissions using natural or technological solutions, such as reforestation or carbon capture and storage (CCS).
Why Net Zero?
The idea of net zero gained prominence following the Paris Agreement in 2015, where nearly 200 countries agreed to limit global warming to well below 2°C above pre-industrial levels, with efforts to limit it to 1.5°C.
Scientific assessments, including those by the Intergovernmental Panel on Climate Change (IPCC), suggest that achieving net zero CO₂ emissions by around 2050 is essential to meet these temperature goals.
Motivations for pursuing net zero vary. For some, it is a response to environmental concerns and scientific consensus. For others, it is driven by regulatory requirements, investor expectations, or reputational considerations.
How Is Net Zero Achieved?
Achieving net zero typically involves a combination of strategies:
Emission Reductions
This is the first and most critical step. It includes:
- Transitioning to renewable energy sources like wind, solar, and hydroelectric power
- Improving energy efficiency in buildings, transportation, and industry
- Electrifying transportation and reducing reliance on fossil fuels
- Modifying agricultural practices to reduce methane and nitrous oxide emissions
Carbon Removal
Once emissions are minimized, remaining emissions can be offset through:
- Natural solutions: Planting trees, restoring wetlands, and improving soil management to absorb CO₂.
- Technological solutions: Direct air capture (DAC), bioenergy with carbon capture and storage (BECCS), and other emerging technologies.
Carbon Offsetting
Organizations may purchase “carbon credits” from verified projects that reduce or remove emissions elsewhere. While controversial in some circles, offsets are often used as a transitional tool when direct reductions are not feasible.
Net Zero vs. Carbon Neutral
While often used interchangeably, net zero and carbon neutral are not identical.
Carbon neutrality typically refers to offsetting emissions without necessarily reducing them, whereas net zero emphasizes deep reductions first, with offsets used only for residual emissions.
Additionally, net zero often includes all greenhouse gases, not just CO₂, and considers entire value chains, including indirect emissions from suppliers and product use.
Who Is Committing to Net Zero?
A wide range of entities have made net zero pledges:
- Countries: Over 140 countries, including major emitters like China, the U.S., and the EU, have announced net zero targets.
- Corporations: Thousands of companies, from tech giants to manufacturers, have set net zero goals, often aligned with science-based targets.
- Cities and regions: Local governments are also adopting net zero frameworks to guide urban planning and infrastructure development.
These commitments vary in scope, ambition, and timelines, and are often accompanied by detailed roadmaps and interim targets.
Challenges and Criticisms
Despite its widespread adoption, the net zero concept is not without challenges and criticisms:
Implementation Complexity
Achieving net zero requires systemic changes across energy, transportation, agriculture, and industry. It involves technological innovation, policy support, and significant investment.
Reliance on Offsets
Critics argue that over-reliance on carbon offsets can delay meaningful emission reductions. The quality and permanence of some offset projects are also questioned.
Equity and Justice
There are concerns about how net zero strategies affect different populations. For example, land use for carbon removal could impact food security or indigenous rights. Ensuring a "just transition" is a key consideration.
Accountability and Transparency
Not all net zero pledges are created equal. Some lack clear definitions, interim targets, or verification mechanisms, leading to accusations of "greenwashing."
The Role of Innovation
Innovation plays a crucial role in enabling net zero transitions. Advances in battery storage, hydrogen fuel, carbon capture, and digital monitoring tools are helping to make net zero more achievable and cost-effective. Continued research and development will be essential to address hard-to-abate sectors like aviation, cement, and steel.
Looking Ahead
Net zero is likely to remain a central framework in climate and sustainability discussions for the foreseeable future. As more entities adopt net zero goals, the focus is shifting from pledges to progress – from setting targets to demonstrating measurable outcomes.
The path to net zero is complex and evolving. It involves trade-offs, uncertainties, and diverse perspectives. Whether viewed as a necessary response to climate science or a strategic business decision, net zero represents a significant shift in how societies think about emissions, growth, and responsibility.
GPRS services are designed to support your efforts to achieve net zero, ensuring the success of green construction projects and other related endeavors by mitigating the risks of subsurface damage whenever you need to break ground.
Our precision concrete scanning and utility locating services utilize ground penetrating radar (GPR) and electromagnetic (EM) locating technologies to provide you with a comprehensive understanding of the infrastructure below-ground and embedded within your concrete slabs. We’ve achieved and maintained an industry-leading 99.8%+ accuracy rating on the over 500,000 concrete scanning and utility locating jobs that our SIM-certified Project Managers have completed since our founding in 2001. So, when you hire GPRS, you’re getting a professional concrete scanning and utility locating company that you can trust to keep your projects on time, on budget, and safe.
All the field-verified data we collect for you is at your fingertips 24/7 thanks to SiteMap® (patent pending), our intuitive infrastructure mapping software application that enables seamless communication and collaboration. Available on any computer, tablet, or smartphone, SiteMap allows for the easy, yet secure sharing of vital infrastructure information within your project team, allowing you to plan, design, manage, dig, and ultimately build better.
From skyscrapers to sewer lines, GPRS Intelligently Visualizes The Built World® to keep your projects on time, on budget, and safe.
What can we help you visualize?
Frequently Asked Questions
What are the benefits of concrete scanning?
Hiring a professional concrete scanning company like GPRS prior to cutting or coring through a concrete slab helps mitigate the risk of damaging any subsurface infrastructure when you do cut or core. This helps keep your project on time, on budget, and safe.
What is the difference between scanning an elevated concrete slab, and a concrete slab-on-grade?
Elevated concrete slab scanning involves detecting embedded electrical conduits, rebar, post tension cables, and other subsurface impediments before core drilling a hole through the slab. Performing precision concrete scanning on a concrete slab-on-grade typically involves scanning a trench line for conduits before conducting saw cutting and trenching to install a sanitary pipe, water line, or other, similar utility.
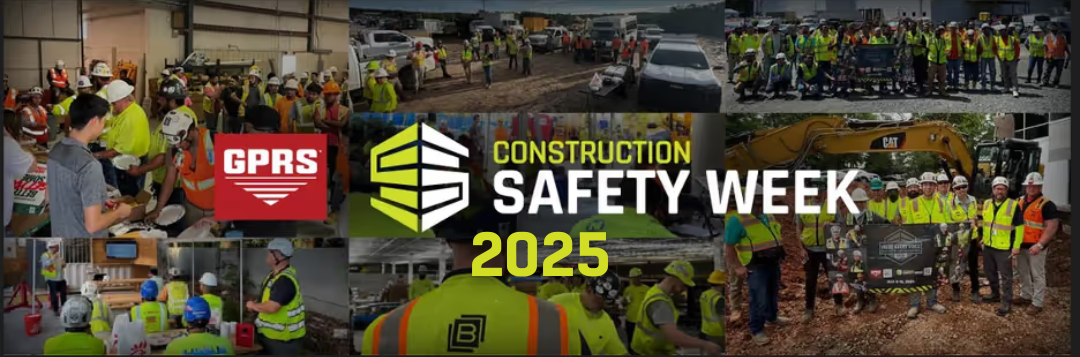
Construction Safety Week 2025: Helping Thousands Stay Safe
The question, “What is your personal safety plan?” has been asked of tens of thousands of construction workers by our GPRS team during Construction Safety Week (CSW) talks across the United States.
At GPRS, safety is our top priority and one of our core values as a company. Because of this, we were so proud to once again sponsor Construction Safety Week in 2025.
In our sixth year as a CSW sponsor, we had the pleasure of meeting with some of the largest general contractors in the nation, including:
- Turner Construction
- Skanska
- Balfour Beatty
- DPR Construction
- Swinerton
- IMC Construction
- Manhattan Construction
- Shook Construction
- AECOM Hunt
- Hunt/Moss
- Brasfield & Gorrie and more!
GPRS Sales Leader Dave Mulcahey had this to say about the week:
“GPRS was proud to sponsor and serve another Construction Safety Week this year. We had the ability to align with many of our national partners in safety and visited so many major jobsites all across the country. We will continue to preach safety in our pursuit of 100% damage prevention, and for us to go home safely every day."
ALL IN TOGETHER
This year’s theme was to PLAN, OWN and COMMIT to safety because we are All In Together. By going All In Together on safety, everyone can work as one with the same goal in mind.
The three pillars of this year’s safety week - Plan, Own & Commit - all have their own purpose and meaning:
- PLAN: Plan each job with precision, purpose, and determination to keep everyone working together and without risk of injury
- OWN: Own your part in the team’s safety and success, so everyone’s voice can be heard and you can build a culture of trust and respect
- COMMIT: Commit fully to executing with excellence to make your team safer and stronger
CSW BY THE NUMBERS
By the end of Construction Safety Week 2025, the GPRS team engaged with over 12,000 attendees at 147 job sites across the country.
At these talks, our team of safety experts imparted essential knowledge and best practices to help each team member on a job site develop a personal safety plan. Our safety experts also brought breakfast or lunch with them for the crews to help keep team members well-fed and engaged.
Since becoming a CSW sponsor in 2020, our team at GPRS has helped more than 65,000 workers develop personalized safety plans tailored to handle many scenarios they might encounter onsite.
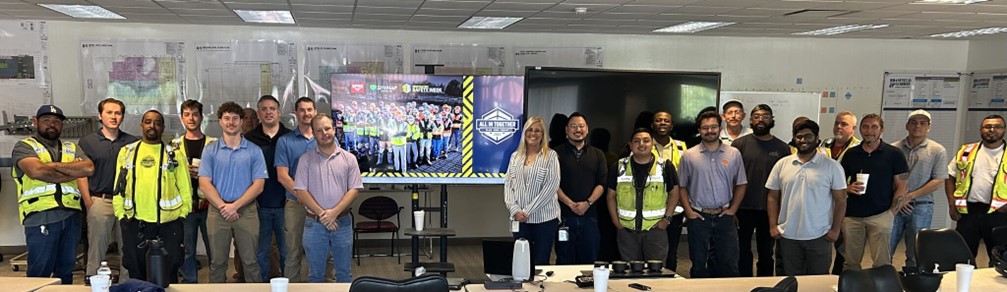
WHY CSW MATTERS
What is talked about and taught during Construction Safety Week is meant to last much longer than seven short days in May. When safety is a top priority on a job site, workers are happier, healthier, and go home at the end of every workday.
Attendees were given the opportunity to cultivate and enhance safety cultures that they can bring back to their team. Attendees’ personal safety plans revolved around:
- Underground utility strikes, and best practices to prevent them
- Heat related illnesses, how to prevent them before they occur, and other climate related risks
- Wearing proper PPE when saw cutting, coring, or drilling through concrete
- Climate related risks on site
- The effects of workers’ mental health on safety and preparedness on the job
LOOKING FORWARD
Construction Safety Week 2025 may now be behind us, but our commitment to safety at GPRS never stops.
Along with CSW, GPRS also sponsors two other major safety events: Water & Sewer Damage Awareness Week in the fall and Concrete Sawing & Drilling Safety Week in the winter. Stay tuned for opportunities to increase your site safety by signing up early for either of these talks!
At GPRS, our mission is to help you Intelligently Visualize The Built World® and keep your projects on budget, on time, and safe. To learn how we can do just that, schedule a service or request a quote today!
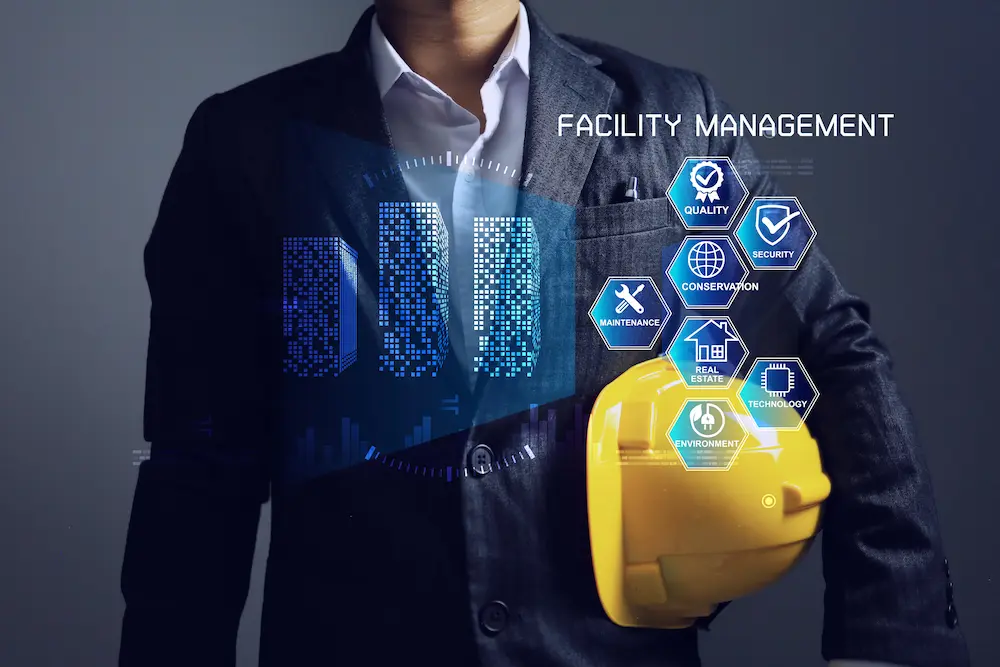
Facility Condition Assessments: A Data-Centric Approach to Proactive Maintenance and Risk Mitigation in CRE
Facilities managers in commercial real estate (CRE) oversee complex portfolios of aging assets, regulatory burdens, and operational demands. While you have many tools at your disposal to effectively run operations, few are as valuable as an accurate facility condition assessment (FCA).
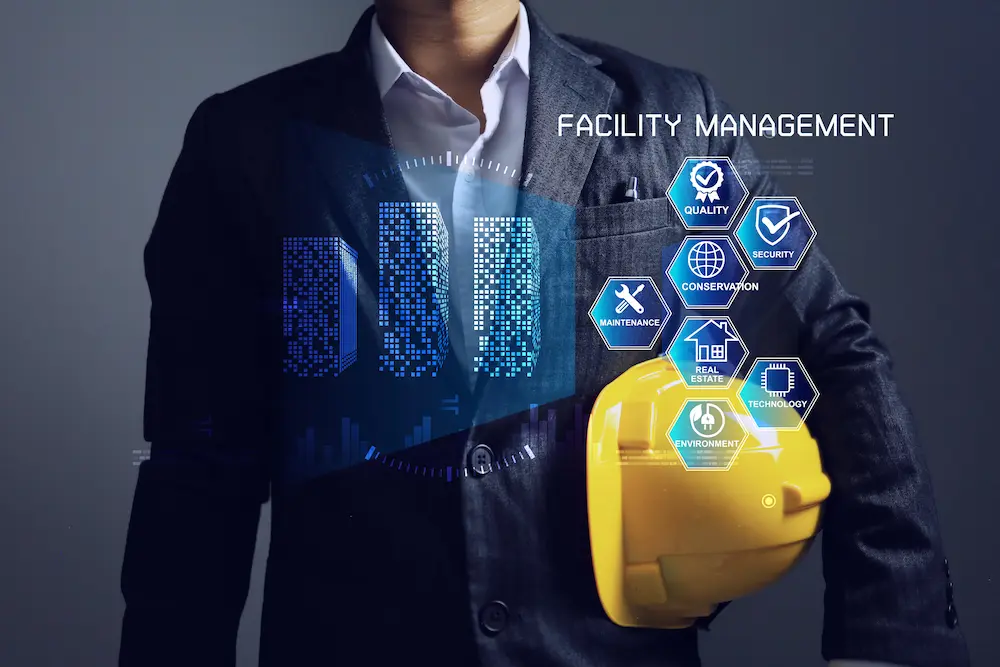
FCAs are not process exercises; they are foundational to strategic facility asset management. When correctly integrated into an operational & maintenance strategy, FCAs allow you to take a proactive approach to maintenance, facilitate risk mitigation measures, and ensure efficient resource allocation. And they are essential to enacting any kind of predictive maintenance strategy.
However, none of that can happen unless you start with precise, comprehensive existing conditions data - aboveground and below – that informs your team, stakeholders, and other decision-makers to act, rather than react, in planning, upgrading, retooling, and managing facilities. This proactive approach is scalable and can be applied to one facility or hundreds because it is built on data standardization and accuracy.
Transitioning from Reactive to Proactive Maintenance
Reactive maintenance is often described as “run-to-failure” because you do not act until trouble arises. On its face, it may appear to provide short-term cost effectiveness, but in reality, it leads to higher long-term operational costs and increased exposure to unplanned asset failures. It is more like trying to close a gaping wound with a Band-Aid. You patch, and reallocate, and patch again, until the dam breaks and so does the system. Then you’re facing large-scale, rolling breakdowns that result in expensive emergency repairs, tenant dissatisfaction, code violations, and shortened asset life cycles, not to mention the damage that can be done to your reputation.
The reactive model keeps you racing to make up for resource inefficiencies and limits your ability to forecast realistic capital needs. Plus, it’s just simple common sense to realize that it requires a lot more effort to run from disaster to disaster than it does to have plans & processes in place to manage disaster before it strikes.
Proactive maintenance, in contrast, uses the data you gain by adopting an FCA to guide scheduled interventions, optimize part replacements, and extend the service life of physical assets. Facilities managers who adopt a data-informed maintenance strategy are positioned to significantly reduce lifecycle costs and better align operational budgets with actual asset performance requirements. This could enable your budgetary needs to gain priority because you are able to present a measured, data-backed case for funds, rather than approaching those holding the purse strings, hat in hand, with your hair on fire thanks to the latest facility or asset failure.
What is the Difference Between Proactive Maintenance and Predictive Maintenance?
While both proactive and predictive maintenance are forward-looking strategies, each has its own processes, level of data dependence, and execution.
Proactive maintenance is a broad spectrum, preventative approach that aims to prevent infrastructure and asset failures before they occur by utilizing existing conditions data, historical trends, manufacturer recommendations, usage intervals, and scheduled inspections and servicing to attack root causes and systemic problems with a goal to reduce wear and tear, avoid unplanned downtime, and extend asset life.
Predictive maintenance can be considered a subset of proactive maintenance that strives to continuously monitor conditions in real time to analyze and anticipate failures before they occur. It is highly technology-driven, relying on sensors, software, and IoT devices to track everything from electrical load and vibration to temperature, and beyond. While predictive maintenance is considered “real-time,” it also gives you an additional infrastructure to manage – that of your data capture devices – which also require their own maintenance plan.
Whether you utilize a proactive or preventative approach, a well-executed FCA provides quantified asset condition metrics such as a Facility Condition Index (FCI), remaining useful life (RUL), and deferred maintenance backlogs. These inputs are essential for creating an intelligent maintenance regime that prioritizes interventions based on criticality, performance degradation rates, and the projected impact of inaction.
Definition of Terms:
Facility Condition Index – To find your FCI, you aggregate the complete cost of any necessary or outstanding repairs, retooling, or renovation requirements against the current replacement value of your infrastructure and building components. Your FCI then becomes a benchmark by which you can differentiate conditions among any facilities group, and is often applied to governmental facilities organizations.
Remaining Useful Life – This term means exactly what it says; it is a determination of how much time you estimate an asset can continue to effectively run prior to requiring significant repair, replacement, or it becomes unusable. There are multiple ways to calculate RUL, but most require you to factor in equipment history, environment, and maintenance records, as well as the asset’s use cadence.
Deferred Maintenance Backlog – Sometimes also referred to as simply the maintenance backlog, it is the aggregated list of all postponed maintenance & repair tasks. It is often helpful to define why the needed repairs were postponed (budgetary constraints, approvals needed, etc.), so that you can prioritize and estimate long-term cost potentials for future budgeting needs.
Risk Mitigation as a Facilities Management Imperative
Commercial facilities carry significant inherent risks: structural, environmental, regulatory, and operational. An FCA serves as a pre-emptive diagnostic tool to identify vulnerabilities like deteriorating electrical systems, outdated HVAC components, or subsurface utility conflicts before they evolve into expensive, disruptive, or hazardous events.
By systematically mapping facility deficiencies and potential failure points, facilities managers can implement tiered response frameworks and emergency preparedness protocols. FCAs also support regulatory compliance by documenting inspection results and providing evidence of due diligence in risk management practices. This capability is particularly valuable in reducing insurance premiums, expediting permitting processes, and shielding ownership from liabilities arising from unsafe conditions or noncompliance.
The Role of Accurate Existing Conditions Data in Facilities Management
The functional value of an FCA is directly proportional to the integrity and accuracy of the data that informs it. Incomplete, outdated, or inaccurate documentation of existing facility conditions can lead to misaligned planning assumptions, cost overruns, delays, and construction rework. The complexity compounds when you realize that you need to assess more than your visible architectural and mechanical systems - you also need to consider the location and condition of critical subsurface infrastructure like water mains, electrical conduits, and sanitary & storm sewer lines.
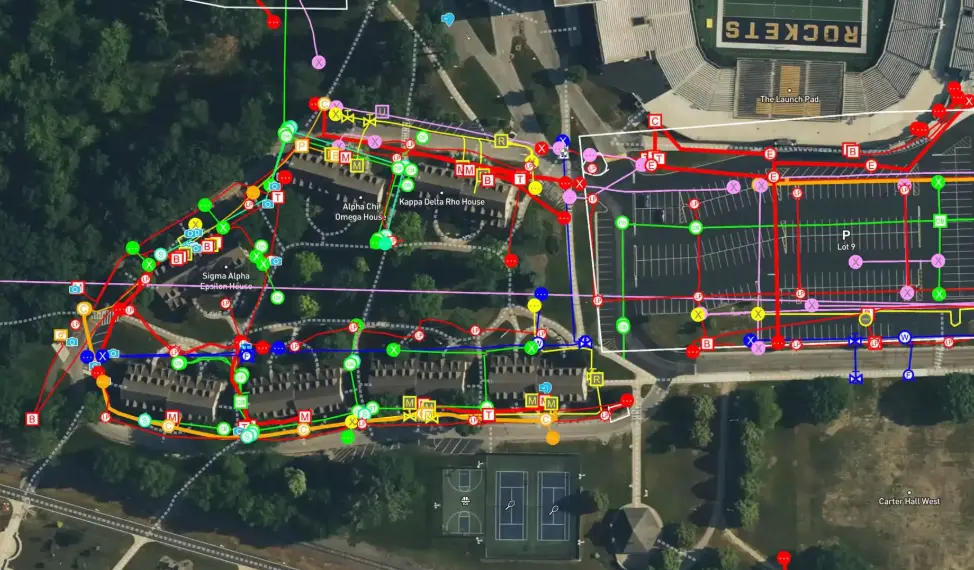
Accurate spatial and performance data, captured using Building Information Modeling (BIM), LiDAR scanning, 3D photogrammetry, and subsurface detection technologies, mitigates these risks. Ground penetrating radar and electromagnetic utility locating methods can yield exceptionally accurate maps of subsurface networks, when performed by SIM-certified professionals, that can greatly reduce the risk of utility strikes and excavation delays.
Aboveground, 3D laser scanning coupled with BIM integration can deliver precise documentation of spatial geometry and system configurations, enabling informed decisions about renovations, space utilization, and load-bearing constraints. These comprehensive datasets can be rendered as a 3D point cloud, CAD drawings, or fully integrated above and below-ground BIM models to foster interdisciplinary collaboration among facility teams, architects, engineers, and contractors by providing a unified reference model throughout the lifecycle of an asset.
Implementation Considerations
To leverage FCAs to their fullest potential, facilities managers must embed assessment practices into a broader data management and planning framework. This includes standardizing inspection protocols, digitizing legacy records, adopting interoperable asset management software, and ensuring cyclical reassessments that account for degradation and environmental impact factors. GPRS’ industry-leading, GIS-based software solution – SiteMap®, is how we deliver our comprehensive utility locating surveys, maps, and aboveground reality capture data to our customers – providing them with a single source of truth for their entire facilities team – whether they manage a single campus, or hundreds of manufacturing plants nationwide.
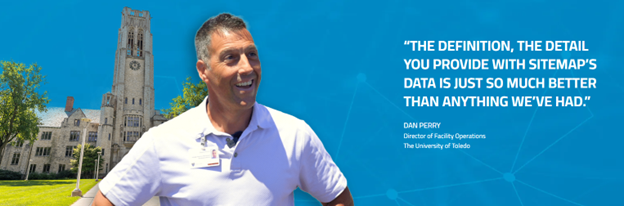
There should be particular emphasis placed on capturing and updating subsurface utility data as part of each assessment cycle. The consequences of neglecting this component are substantial: inaccurate subsurface data can compromise new construction, delay permitting, and dramatically inflate capital project timelines.
Facilities Management Teams Should Prioritize:
- Structuring FCA outputs to integrate directly with Capital Improvement Plans (CIPs) and Computerized Maintenance Management Systems (CMMS)
- Aligning FCA frequency with asset criticality and local regulatory cycles
- Incorporating sustainability metrics to evaluate energy performance and compliance with decarbonization mandates
- Training personnel on new diagnostic technologies and data interpretation methodologies
A Facility Condition Assessment is not a static report: it is a living, strategic asset for your facility. Accurate, comprehensive existing conditions data informs proactive maintenance policies, streamlines capital planning, and mitigates operational and regulatory risks. Above all, it empowers facilities managers to deliver cost-effective, reliable, and compliant environments for tenants and stakeholders alike.
That’s why GPRS Intelligently Visualizes The Built World® for facilities nationwide.
What can we help you visualize?
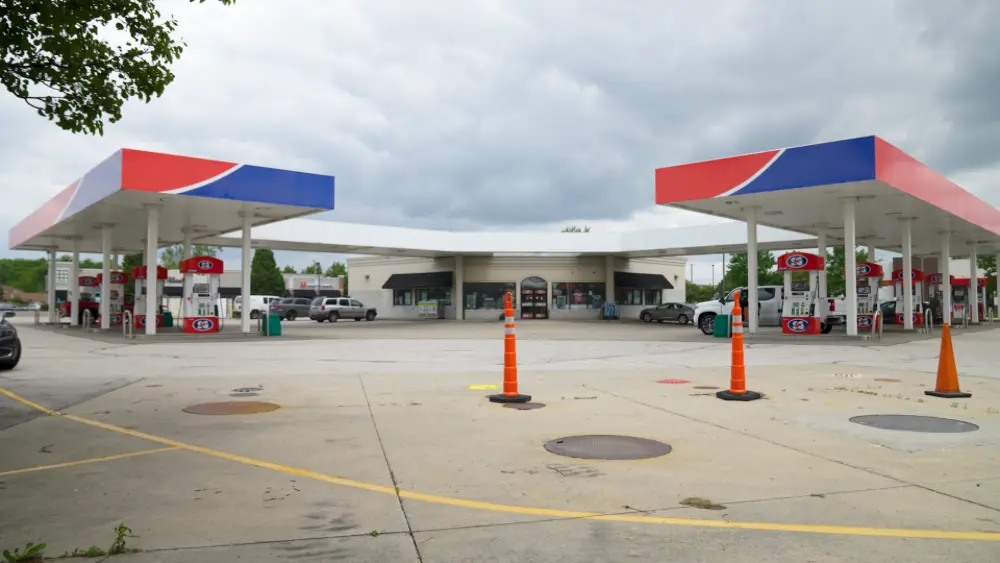
How GPRS Helps Protect San Francisco Bay Gas Stations From Subsurface Damage
From soda fountains to gas pumps, Rebekah Davies is responsible for ensuring a frictionless experience anytime you visit a BP gas station in the San Francisco Bay Area.
As a Site Maintenance Supervisor, Davies oversees every aspect of her stations’ operations outside of the employees.
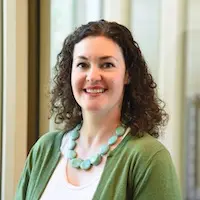
“Anything that’s a capital expense, including plumbing, fuel dispensers, parking lots, the Veeder-Root which makes the tanks run,” she said. “And there are a couple little carve-outs beyond that: the fountain machines that get your soda, the registers that allow you transactions, the car washes. All of that is on me to maintain.”
It’s also Davies’ responsibility to ensure that when excavation occurs at or near one of her stations, it’s conducted safely. BP requires its sites to hire a professional utility locating company to map and mark out buried utilities, underground storage tanks (USTs) and any other subsurface obstructions prior to any excavations penetrating deeper than three inches into the earth.
“And just to make sure we’re covered, we [have] the whole site [marked],” Davies said.
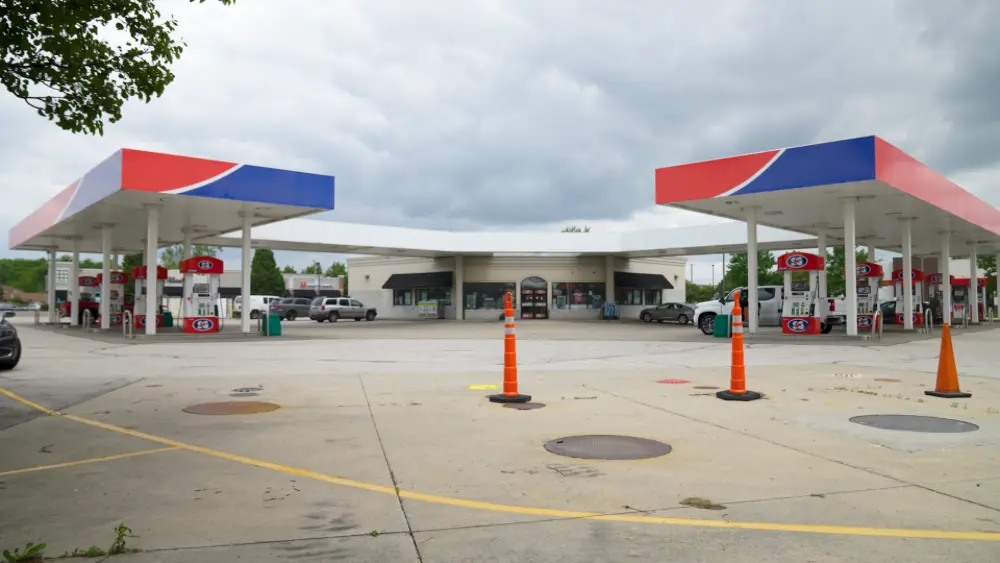
Striking a buried utility while excavating can have devastating consequences – and hitting something underneath a gas station can be even worse. While calling 811 is the first step you should always take to avoid subsurface damage when planning an excavation project, it’s important to remember that not every buried utility belongs to a provider registered with 811 – meaning they won’t know it’s there until you’ve hit it.
GPRS Utility Locating Services complement 811 by fully locating and mapping the buried infrastructure in your project area. Utilizing ground penetrating radar (GPR) and electromagnetic (EM) locating, our SIM-certified Project Managers have achieved and maintain a 99.8%+ rate of accuracy when locating buried utilities.
Davies said she relies exclusively on GPRS to provide utility locating services at her sites.
“The quality of the reports your team provides is always really good,” she said. “I have never had something where I thought ‘Wow, you guys really phoned that in. And the responsiveness – I don’t think it’s ever taken longer than an hour to get a response from somebody to get a job set up, and then it never takes more than a day or two to get the full, detailed report with the photos. There’s never been a point where I thought ‘Wow, I wish this was done better.’”
When you hire GPRS to locate buried utilities, we go above and beyond to ensure you have all the data you need to stay on time, on budget, and safe. This was evident recently when Davies contacted us to scan at one of her stations prior to the re-trenching of the property’s swale, a trench used to manage stormwater runoff and infiltration.
GPRS located utilities for the whole site and uploaded the data collected into SiteMap® (patent pending), our infrastructure mapping platform where Davies has 24/7, secure access to this critical information from any computer, tablet, or smartphone.
This came in handy later when the station was installing new bollards. Davies was able to use the data we’d previously collected to discover that a conduit ran directly beneath where they intended to install the protective structures.
“I was able to know, because you guys had already scanned the whole site, that the conduit we needed to avoid was directly beneath where those bollards needed to go,” Davies said. “So, I already had that information because your team did a really thorough job. Even though it was on the opposite side of the lot from what I was looking at, they chose to do it well and thoroughly and we had zero conflicts [during the bollard installation].”
Thanks to a stringent dig policy and the accurate, actionable data provided by GPRS, Davies says BP’s West Cost Team has had zero ground strikes during their excavation projects.
“Because your team does such a thorough job, I don’t need to be [on-site when utility locating occurs],” she said. “I don’t have to stand there, because I can use the information that I’m given in the report to find out what I need about where things are. So, I don’t need to stand there with [you].”
GPRS Intelligently Visualizes The Built World® to keep your projects on time, on budget, and safe.
What can we help you visualize?
Frequently Asked Questions
What does GPRS give me when I hire you to conduct a utility locate?
Our Project Managers flag and paint our findings directly on the surface. This method of communication is the most accurate form of marking when excavation is expected to commence within a few days of service.
GPRS also uses a global positioning system (GPS) to collect data points of findings. We use this data to generate a plan, KMZ file, satellite overlay, or CAD file to permanently preserve results for future use. GPRS does not provide land surveying services. If you need land surveying services, please contact a professional land surveyor.
Please contact us to discuss the pricing and marking options your project may require.
Can GPRS locate PVC piping and other non-conductive utilities?
GPR scanning is exceptionally effective at locating all types of subsurface materials. There are times when PVC pipes do not provide an adequate signal to ground penetrating radar equipment and can’t be properly located by traditional methods. However, GPRS Project Managers are expertly trained at multiple methods of utility locating.
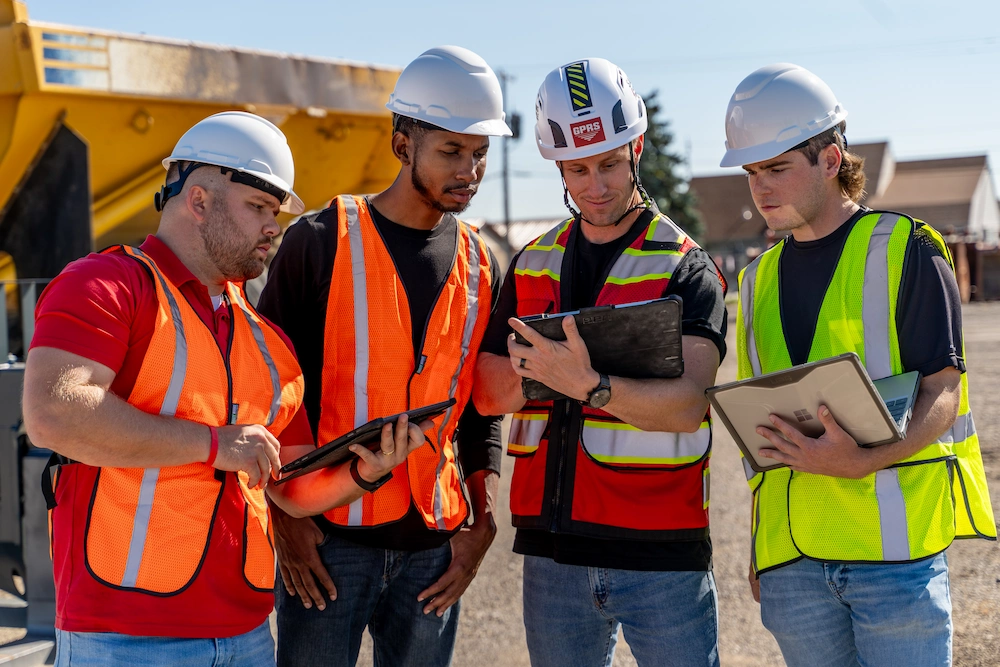
Top Four Trends Reshaping Facilities Management
Facilities management (FM) is entering a new era of innovation and impact.
As companies place greater emphasis on sustainability, operational efficiency, and long-term resilience, the tools and strategies that support facilities management must evolve accordingly. Over the next five years, four transformative trends will redefine the facilities management landscape. GPRS stands ready as a trusted partner, empowering companies to navigate and lead this evolution with confidence.
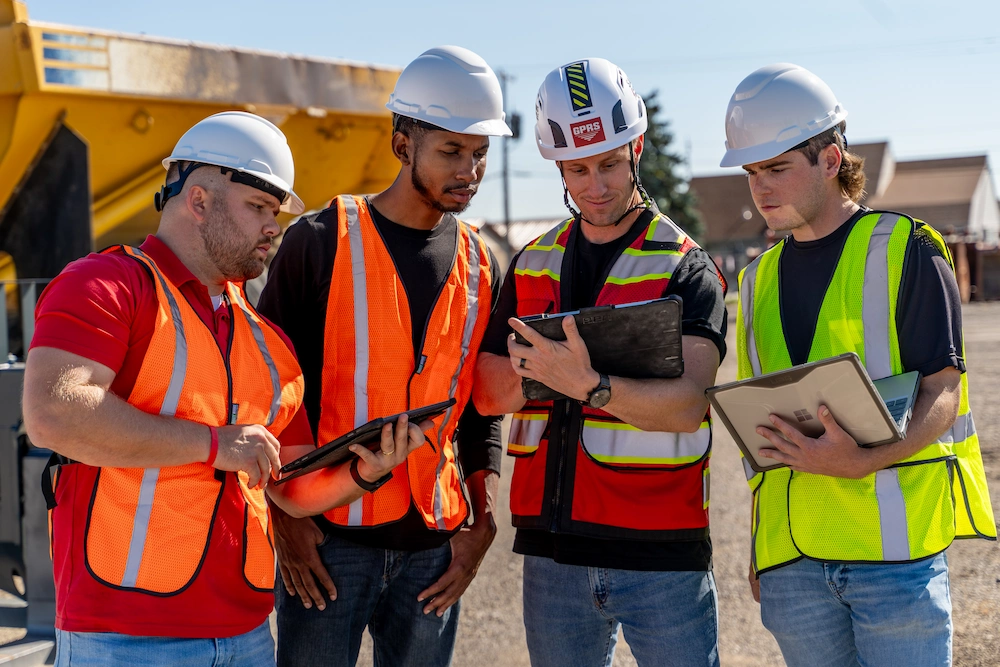
These trends are unlocking new possibilities for how facilities are planned, maintained, and optimized. From digital integration to data-driven decision-making, the facilities management industry is profoundly shifting. Backed by cutting-edge technologies and a commitment to precision and reliability, GPRS is empowering facility teams to stay ahead of the curve and meet tomorrow’s challenges with confidence.
1. Sustainability and ESG Goals Are Shaping the Future of Facilities Management
Environmental, Social, and Governance (ESG) Goals are now essential in how facilities are planned, built, and managed. Companies must show progress in areas like cutting greenhouse gas emissions, reducing waste, using energy wisely, and protecting land.
Facility managers need to include sustainability in every stage of a building’s life – from design and construction to daily operations and upgrades. They also need accurate, current data to meet rules, earn green building certifications (like LEED), and plan for the future.
Sustainable facilities management means using better materials, limiting harm to the environment, and making sure upgrades support ESG goals. As more companies aim for net-zero emissions and climate readiness, facilities teams must be ready with tools and systems that support these goals without risking safety or performance.
2. Technology Integration: Turning Static Records into Smarter Tools
The facilities management industry is undergoing a profound digital transformation, driven by the adoption of technologies like Internet of Things (IoT), artificial intelligence (AI), and digital twins. These innovations empower teams to move beyond reactive maintenance, enabling predictive strategies, real-time system monitoring, and data-driven scenario planning that reduce risk and optimize performance.
IoT sensors embedded in building systems provide continuous insights into everything from HVAC efficiency to water consumption. AI-powered analytics interpret this data to detect anomalies and recommend proactive maintenance. Digital twins – virtual models of physical assets – offer facility managers an immersive way to visualize, simulate, and manage infrastructure. From energy modeling to emergency preparedness, these tools redefine how facilities are operated and maintained.
The success of these technologies, however, depends on the accuracy and completeness of the foundational data they rely on. Without a reliable understanding of existing conditions, even the most advanced digital tools can fall short; leading to misinformed decisions, operational inefficiencies, and missed opportunities.
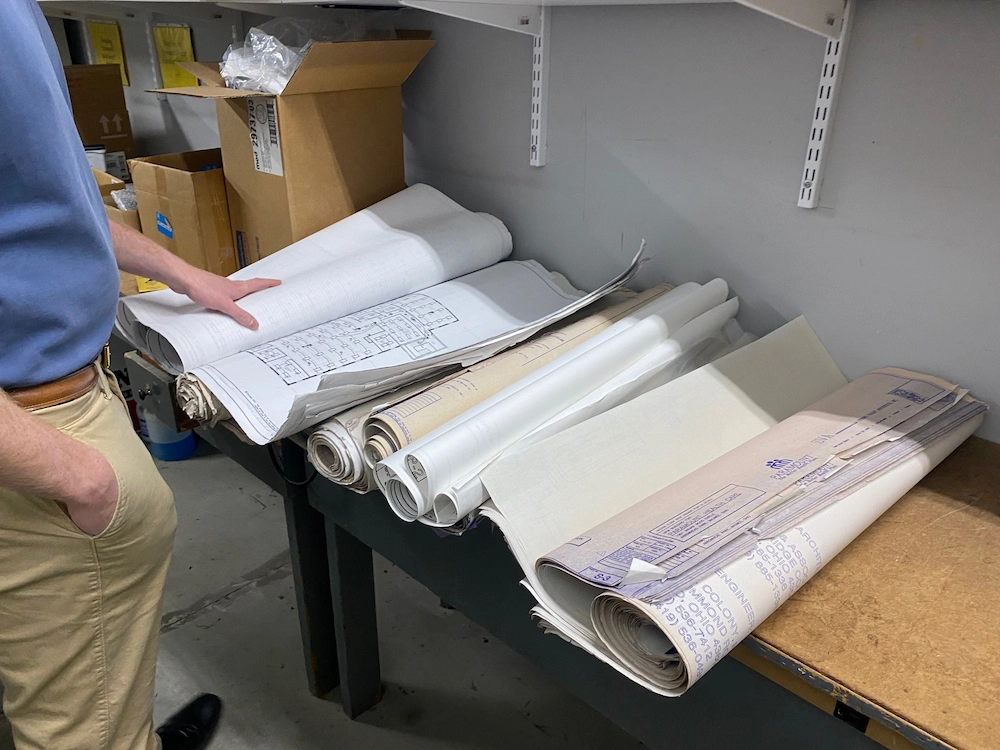
That’s where SiteMap®(patent pending), powered by GPRS, becomes indispensable. As a cloud-based, interactive infrastructure mapping and facility management platform, SiteMap transforms outdated utility records into dynamic, visual data that integrates seamlessly into digital ecosystems. It serves as a single source of truth for both aboveground and subsurface infrastructure, fostering collaboration across departments and external partners. Whether deployed independently or as part of a broader digital twin strategy, SiteMap ensures that facilities teams have the accurate, accessible data they need to lead the next generation of facilities management.
3. Labor Shortages Require Smarter, Scalable Solutions
Staffing challenges are transforming how facilities teams operate. As the availability of skilled tradespeople declines and experienced professionals retire, many organizations are rethinking how they preserve institutional knowledge and maintain continuity.
This shift comes at a time when facilities are becoming more complex. Managing aging infrastructure, integrating advanced technologies, and staying compliant with evolving regulations require specialized expertise, yet the incoming workforce isn’t growing fast enough to meet demand.
To adapt, facilities teams are embracing smarter, more scalable tools that reduce dependence on individual expertise and make critical infrastructure data accessible to everyone. Intuitive software platforms, mobile-enabled systems, and visual data tools are helping teams better understand and manage complex environments with greater ease and efficiency.
By digitizing and centralizing facility data, organizations can capture and retain institutional knowledge – ensuring it’s readily available to new team members without relying on outdated paper records or informal handoffs. These tools can accelerate onboarding, standardize workflows, and enhance teamwork across departments and contractors.
In today’s evolving workforce landscape, access to accurate, comprehensible infrastructure data is no longer optional – it’s essential for maintaining productivity, safety, and long-term resilience.
4. Economic Pressures Demand Smarter Tools
Financial realities are reshaping how facilities are managed. As material costs rise, labor remains in short supply, and capital budgets tighten, facilities teams are challenged to deliver greater value with fewer resources. At the same time, leadership is placing increased focus on return on investment (ROI), operational efficiency, and sustainable cost control.
This evolving landscape encourages a more strategic approach to facilities management – one that emphasizes data-driven planning, proactive maintenance, and risk reduction. Whether it’s a renovation, system upgrade, or new construction, every project must be carefully planned and executed to ensure efficiency, avoid delays, and prevent unnecessary expenses.
Facilities managers are also being called upon to make investment decisions backed by clear, measurable data. Reliable infrastructure information is essential for accurate budgeting, forecasting, and performance tracking. Without it, companies risk the chance of running into unexpected costs such as utility strikes, change orders, or compliance issues that can impact both timelines and margins.
To meet these demands, companies are embracing technologies that enhance visibility, streamline operations, and reduce inefficiencies. With the right tools in place, teams can plan with confidence, stay on schedule, and make the most of every dollar invested.
How GPRS Supports the Future of Facilities Management
As facilities management becomes data-driven and complex, access to accurate, centralized infrastructure information is more important than ever. GPRS is meeting this need head-on – empowering facilities teams with the tools, technology, and expertise to manage above and belowground infrastructure with greater accuracy, accessibility, and efficiency.
GPRS supports the future of facilities management by delivering accurate infrastructure data, collected through specialized services like utility locating, concrete scanning, video pipe inspection, and 3D laser scanning. Every data point is verified in the field by our highly trained Project Managers and backed by our 99.8% accuracy rate. Because when it comes to safety and planning, precision matters. That commitment is further reinforced by our industry-exclusive Green Box Guarantee, which promises obstruction-free areas for cutting or coring because we stand behind the accuracy of our work. This level of confidence and accountability is what sets GPRS apart.
All verified data is then seamlessly integrated into SiteMap, where it’s organized, visualized, and continuously updated – giving teams the clarity they need to make informed decisions, reduce risk, and collaborate more effectively.
GPRS also plays a role in supporting Facility Condition Assessments (FCA) by delivering the accurate, field-verified infrastructure data teams need to evaluate asset health, plan upgrades, and maintain compliance with ESG and safety standards. Because every data point is collected by GPRS Project Managers using advanced technologies and backed by our 99.8% accuracy rate, facilities teams can trust the insights they rely on for long-term planning.
The Future of Facilities Management Starts with GPRS
The next five years will bring transformative change to facilities management. Sustainability goals, digital transformation, workforce shifts, and economic pressures will all influence how facilities are built, maintained, and optimized. To stay ahead, facility managers need tools that are powerful and purpose-built for the challenges they face.
GPRS is your partner. With industry-leading accuracy, advanced field services, and a commitment to complete infrastructure visibility, GPRS equips facilities teams to build smarter, safer, and more resilient environments.
What can we help you visualize?
FREQUENTLY ASKED QUESTIONS
What makes GPRS a trusted partner in modern facilities management?
GPRS stands out for our commitment to precision, safety, and innovation. With a 99.8% accuracy rate, GPRS ensures that facility teams have reliable data for planning and operations. Our Green Box Guarantee provides added confidence by promising obstruction-free areas for cutting or coring. This level of accountability helps organizations reduce risk, avoid costly errors, and maintain compliance with safety and ESG standards.
What services does GPRS provide to support facilities management teams?
GPRS offers a comprehensive suite of services designed to give facilities teams complete visibility into their infrastructure. These services include utility locating, concrete scanning, video pipe inspection, and 3D laser scanning. Each service is performed by highly trained Project Managers and backed by a 99.8% accuracy rate. This ensures that teams can plan upgrades, renovations, and maintenance with confidence – reducing risk, avoiding costly errors, and improving overall project outcomes.
How does SiteMap® support smarter infrastructure management?
SiteMap transforms outdated utility records into dynamic, visual data. It centralizes both aboveground and subsurface infrastructure information, making it accessible and actionable for facility teams. SiteMap enhances collaboration, supports predictive maintenance, and ensures that decisions are based on accurate, field-verified data.