Applications for 3D Laser Scanning
Laser scanning is applicable in many industries due to its precision, efficiency, and versatility. By employing this 3D technology at the onset of a project, AEC professionals can capture and access precise data, drawings, and models to minimize conflicts and expedite design planning, prefabrication, asset management, and facility modifications. Below are ten useful applications for 3D laser scanning.
1. Building Renovations
3D laser scanning documents the as-built details of a building, capturing the exact layout, dimensions, and locations of architectural, structural, MEP features, walls, windows, doors, stairs, roof, railings, exposed columns, beams, equipment, piping, ducts, and more. The technology delivers contractors and engineers precise point clouds that can be exported and crafted into 2D CAD drawings and 3D BIM models to ensure that planned renovations seamlessly integrate with the building's existing structure.
By overlaying proposed renovation plans onto the 3D scan data, potential conflicts or clashes can be identified and addressed early in the planning phase. Whether you’re renovating a stadium, theatre, historic building, church, school, etc., 3D laser scanning provides comprehensive as-built data for any site, adding value to the planning, design, and execution phases of any renovation project.
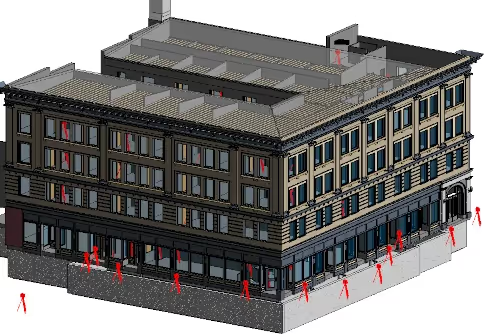
2. Architectural Design
3D laser scanning aids in the architectural design process by delivering accurate existing conditions to create design models, monitor construction progress, and verify as-built accuracy. 3D laser scanning quickly and accurately provides comprehensive as-built documentation of a building or site unmatched by other technologies. In most cases, point clouds are accurate to 2-4mm, and the as-builts created from those LiDAR scans are accurate to 6mm.
From walls and windows to HVAC, mechanical, electrical, and plumbing features, 3D laser scanning can accurately identify and document all visible elements of a structure. 3D laser scanning lets your architectural team focus on design rather than capturing and modeling existing conditions.
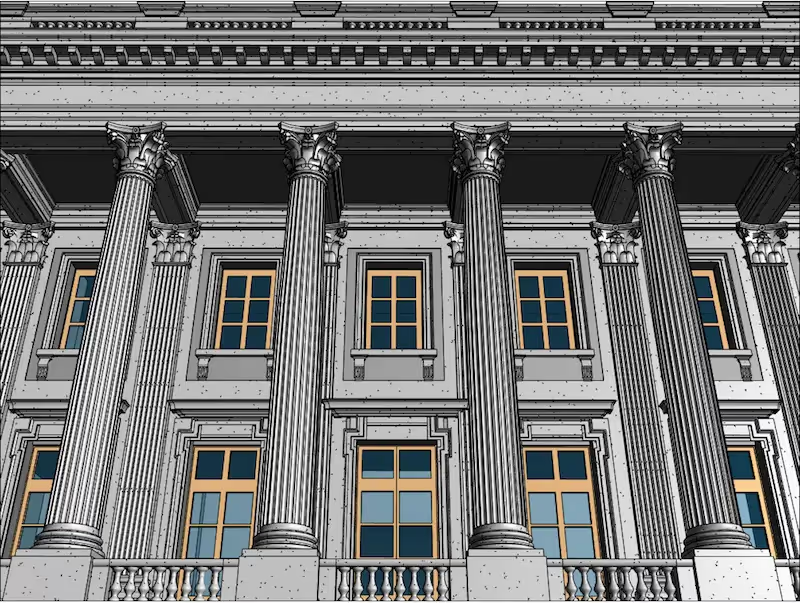
3. Maintenance, Retrofitting, or Expansion of a Power Plant
As power plants evolve to meet changing regulatory requirements or adopt new technologies, retrofitting existing infrastructure is often necessary. 3D laser scanning provides highly detailed and accurate representations of the plant's as-built conditions, including structural components, equipment, piping, boilers, generators, turbines, pumps, condensers, heat exchangers, and more.
This comprehensive documentation serves as a reliable reference for maintenance, retrofitting, and future expansion projects. Precise 2D CAD drawings and 3D building information models (BIM) provide data for engineers to plan new designs around existing infrastructure, mitigating potential clashes and interferences. 3D laser scanning allows engineers and maintenance personnel to conduct virtual walkthroughs of the plant without physically entering hazardous areas. Also, by identifying areas prone to corrosion, wear, or structural degradation, proactive maintenance schedules can be developed to prevent unplanned downtime and extend the lifespan of critical components.
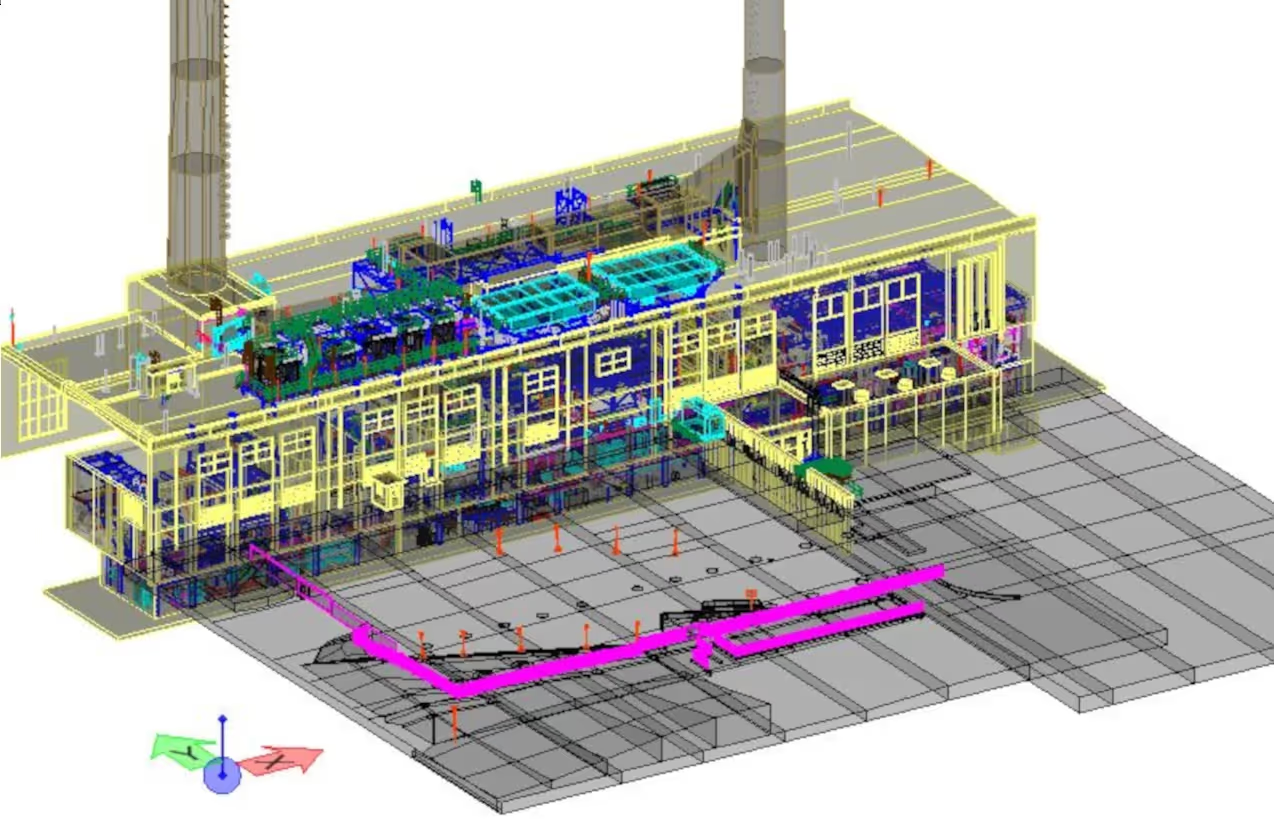
4. Modifications, Expansion, or Maintenance of a Manufacturing Plant
As-built data of existing structures, equipment, piping, or manufacturing processes can be precisely captured with 3D laser scanning for facility modifications, expansions, and maintenance. Intelligent 3D models can be created from the point cloud data for planning, fabrication, and clash-detection. Verified accurate measurements will aid in production, machinery, or process changes to optimize plant layouts. Virtual fit-outs guarantee installations will integrate seamlessly with existing conditions, comply with safety regulations, and reduce risk.
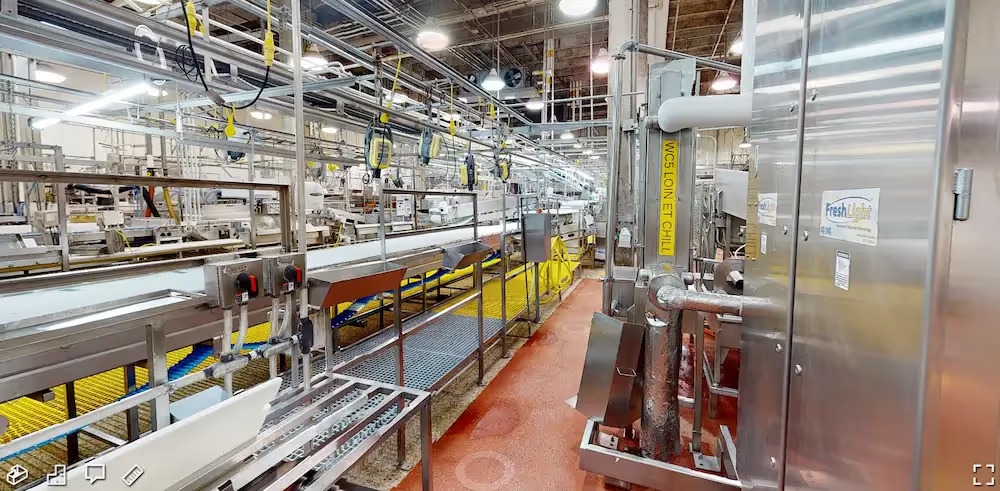
5. Measure Floor Flatness and Floor Levelness
3D laser scanning is the best way to measure floor flatness (FF) and floor levelness (FL) with precision, efficiency, and accuracy. Highly detailed point cloud data from 3D laser scanning can be used to determine FF and FL values on concrete floor and flatwork.
Color elevation maps can be quickly produced from the point cloud data to visualize floor flatness and identify the high and low points in concrete and calculate the boundaries of any areas that need to be adjusted. The data points collected maintain their coordinates and can be easily communicated to the project team. Fast and accurate cut and fill calculations can be computed.
Contractors can fix elevation discrepancies with speed and accuracy. Laser scanning produces a colorized elevation map of the entire floor. This way if questions arise, stakeholders can be educated on the standards and the project is validated with data.
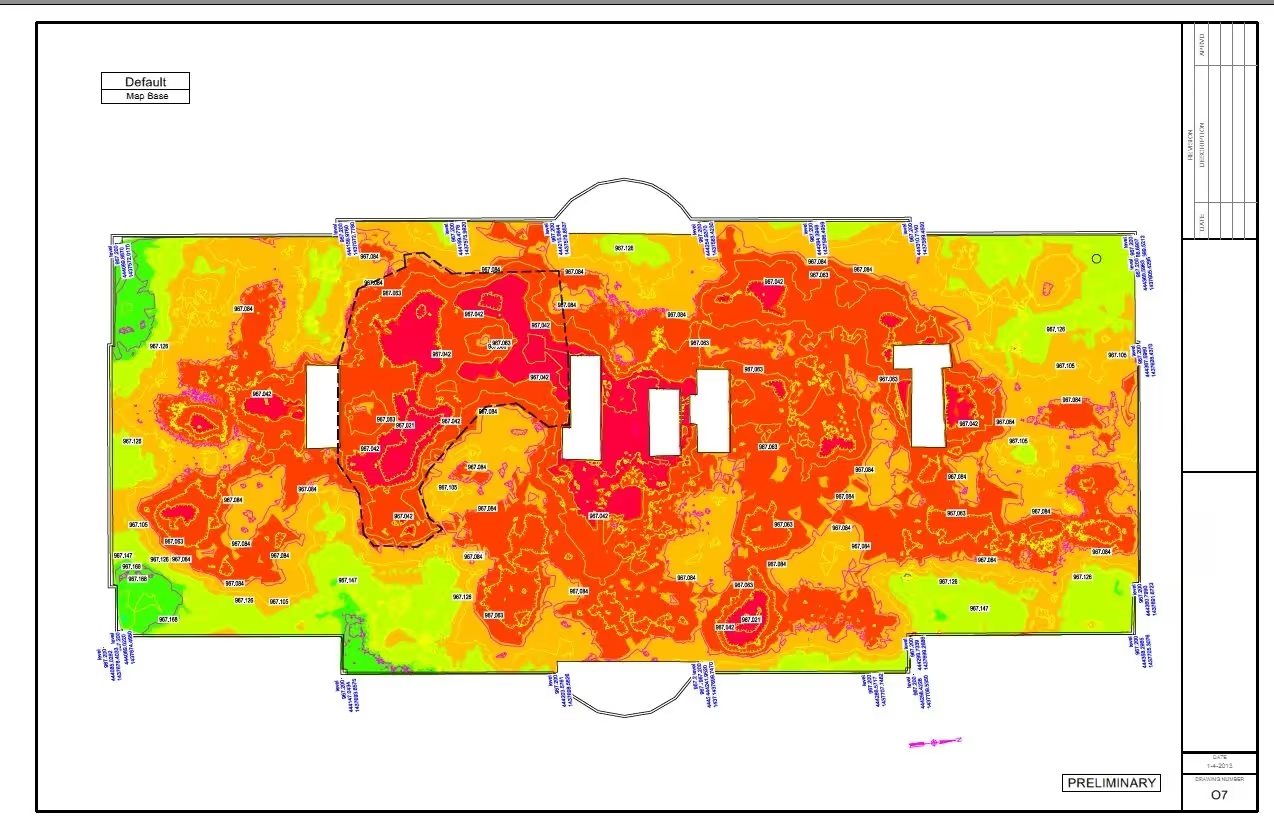
6. Create a Digital Twin 3D Model
A digital twin is a 3D model that accurately represents a building or site’s existing physical space, assets, and processes. It is a real-time, accurate digital representation of the existing conditions of every component and system, including architectural, structural, and MEP features, walls, windows, doors, stairs, roof, railings, exposed columns, beams, equipment, piping, ducts, utility and concrete locate markings, and more. Clients can virtually walk-through a project site to plan for building improvements, increase efficiencies, and optimize workflows.
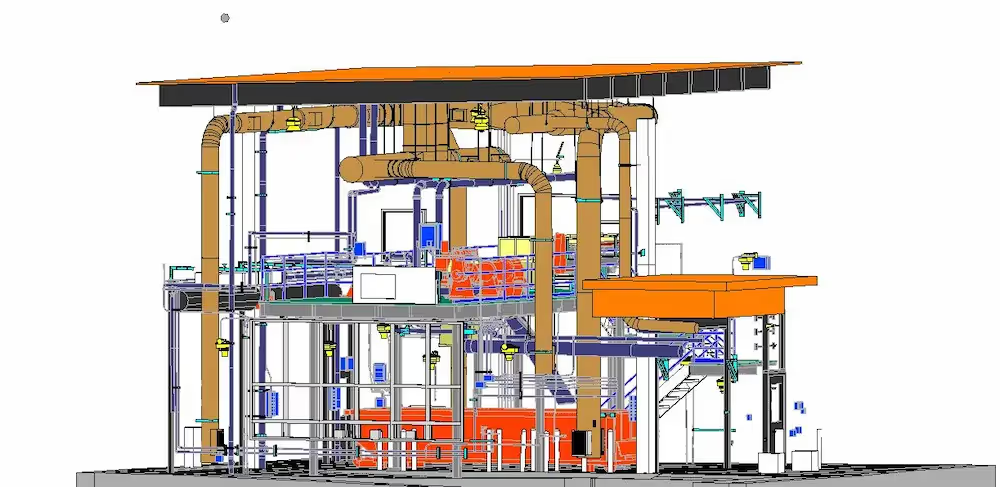
7. Retrofitting Pipes and Equipment into an Existing Facility
When plants retrofit new piping, equipment, vessels, valves, and flanges, etc., into an existing facility, it’s important they have accurate existing conditions data to complete virtual interference checks and ensure there are no clashes. The infrastructure of agricultural facilities, water and wastewater treatment plants, healthcare and pharmaceutical facilities, energy and utility companies, oil and gas facilities, government and defense facilities, telecom companies, etc., can be captured with 2–4-millimeter accuracy. With careful planning and the as-built data, 2D CAD drawings and 3D models created from 3D laser scan data, new designs can be precisely engineered, minimizing installation delays, rework, change orders, and costs.
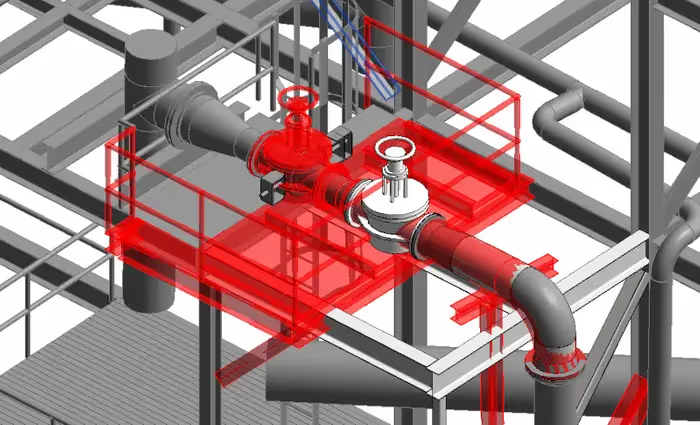
8. Obtain 2D CAD Drawings for a Building Permit
To get a building permit, you will need to submit a set of construction documents that show the details and specifications of your design. 3D laser scanning captures 2-4mm accurate layout, dimensions, and locations of your project requirements in the form of a point cloud. Point clouds can be transformed into custom deliverables such as 2D CAD drawings, site plans, plan views, floor plans, elevations, sections, details, isometric drawings, and reflected ceiling plans to obtain a building permit.
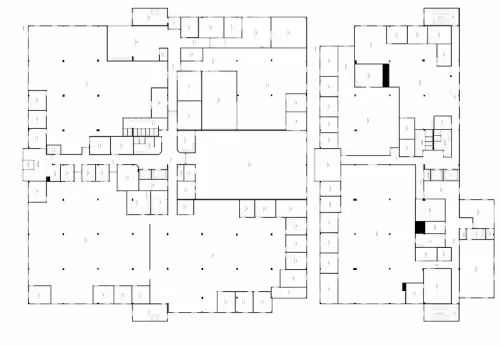
9. Obtain a 3D Mesh Model
3D mesh models are highly detailed and realistic renderings of buildings, objects, or sites and are often used in areas where high image quality and accuracy are required, such as in the film and video game industry, architectural visualization, or product design. The point cloud from 3D laser scanning can be used to create a volumetrically accurate, high density and high resolution .fbx, .stl, .obj, and .ply mesh model. Meshes allow users to view the object’s geometry inside a CAD environment without having to navigate a point cloud. Meshes capture the fine elements and spatial details of objects, such as airplanes, cars, boats, monuments, and statues that can be difficult to reproduce in CAD. Mesh files of stadiums and arenas have been used to develop mixed reality experiences during sporting events.
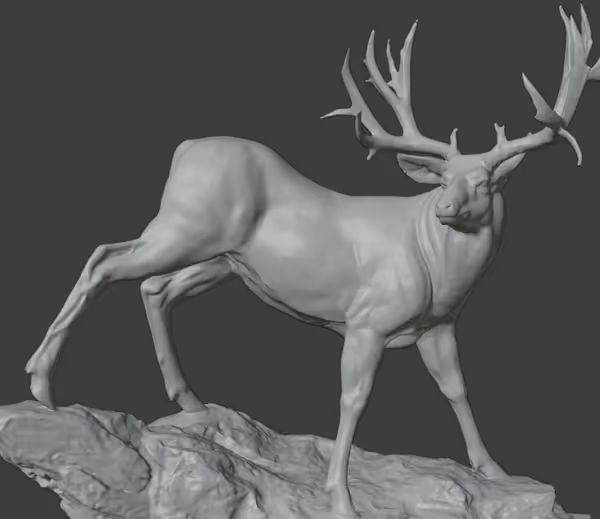
10. Update P&IDs
A piping and instrumentation diagram, or P&ID, is a schematic drawing of instruments, control systems, and pipelines used in any process development plant. It depicts the connection between piping, equipment, vessels, heat exchangers, pumps, instruments, valves, and process components. P&IDs are applied to industrial and engineering projects, such as steam and electric boilers, and display piping components, such as valves and equipment. 3D laser scanning can accurately capture the as-built conditions of a plant and create a 2D CAD drawing or 3D BIM model to document the existing P&ID equipment, piping, and the flow of control and control devices. It can be used for referencing the process plant and is also used for modification and maintenance.
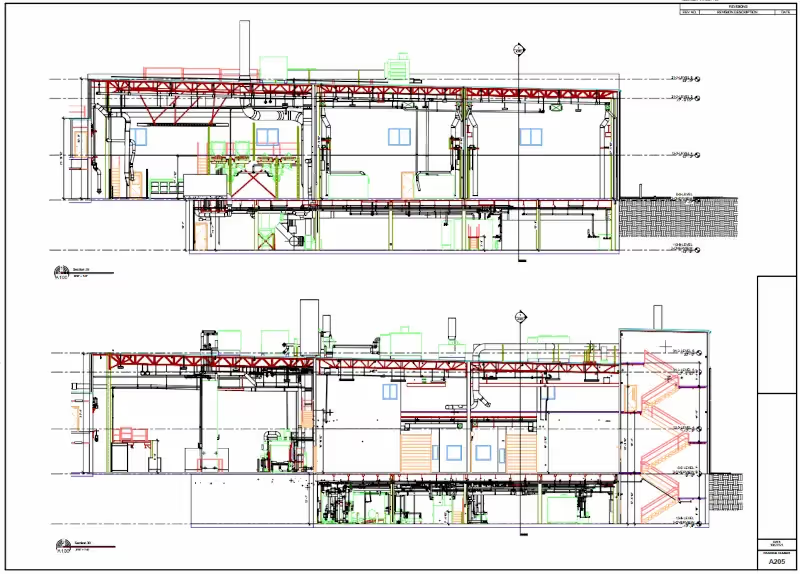
The GPRS Difference. Why Choose GPRS?
Accurate measurements help you avoid expensive mistakes, reworks, and change orders. GPRS 3D laser scanning services provide 2-4mm accurate existing conditions site documentation for efficient planning, design, and construction.
GPRS’ elite team of Project Managers efficiently 3D laser scans the exterior and interior of each site with professional-grade Leica laser scanners, capturing the exact layout, dimensions, and locations of your specific project requirements, such as architectural, structural, and MEP features, walls, windows, doors, stairs, roof, railings, exposed columns, beams, equipment, piping, ducts, and more.
Our Mapping & Modeling Team registers and processes the point cloud, removing noise and setting the coordinate system to provide the most precise measurements. Data is then compiled into custom 2D CAD drawings and 3D BIM models and delivered via SiteMap®. SiteMap® is a free cloud-based software that delivers point cloud data, 2D CAD drawings and 3D BIM models, all in one platform.
What can we help you visualize?
Frequently Asked Questions
What is BIM?
BIM stands for Building Information Modeling and is more than just a 3D model. 3D BIM scanning gives engineers the ability to manage the building data throughout its whole life-cycle. It provides accurate spatial relationships and manufacturer details, as well as geographic information and other pertinent aspects of a building or site.
What is a Digital Twin?
A digital twin is highly complex virtual model that is the exact counterpart (or twin) of a physical space. GPRS uses 3D laser scanners to collect real-time data for a building or facility and create a digital duplicate. Data can be easily visualized, measured, and analyzed. Digital twins can be used to improve efficiencies, optimize workflows, and detect problems before they occur.
What is Floor Flatness and Floor Levelness?
Floor flatness refers to the smoothness of the concrete surface. It measures the degree to which a floor is free of bumps and dips over a small area. The flatness is quantified using the Floor Flatness Number (FF), which is calculated based on the variation in elevation over a certain distance. A higher FF number indicates a smoother floor. Floor levelness, on the other hand, pertains to the extent to which a floor conforms to a horizontal plane over a larger area. It measures the overall slope and waviness of the floor. The levelness is quantified using the Floor Levelness Number (FL), which is calculated based on the floor's deviation from a horizontal plane over longer distances. A higher FL number indicates a more level floor.