3D laser scanning is one of the most innovative additions to the construction industry’s toolbox, as it has changed the way that buildings are captured, designed, and managed.
Used to document every detail – big or small – of an existing building, an industrial laser scanner improves project coordination and collaboration. This type of scanner makes use of laser light to create 3D renders, commonly known as point clouds.
The millions of data points in a point cloud are used for mapping out the dimensions of buildings. High-accuracy results make laser scanning a preferred technology in construction. From helping with design and planning, an industrial laser scanner is a huge asset that makes the entire construction process more efficient.
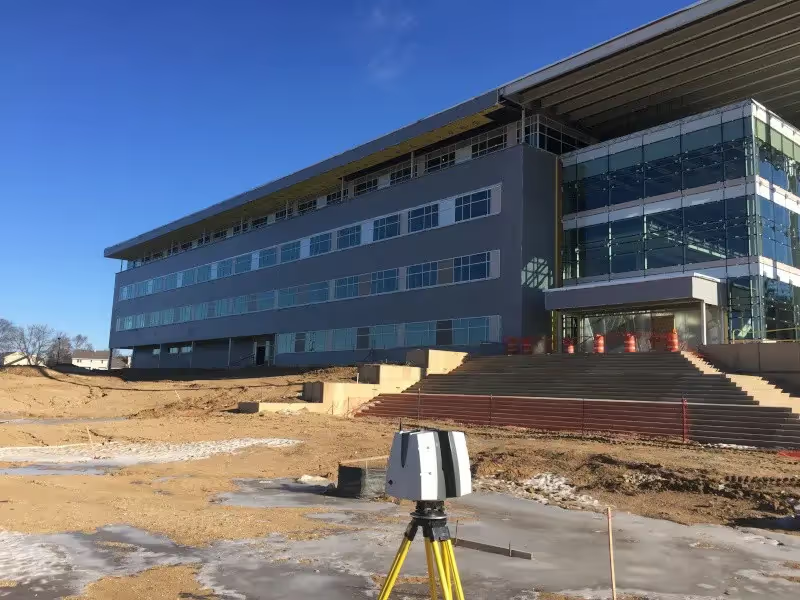
How Can 3D Laser Scanning Be Used by Construction Companies?
Design Planning and Quality Assurance
Every construction project starts with design, and integrating 3D laser scanning at this early stage can be incredibly advantageous. Scan-to-BIM technology provides construction professionals with detailed insights crucial for accurate design planning. Conducting a scanner survey can significantly enhance quality assurance throughout the design process.
When a building is either completed or still under construction, laser scanning can be used to validate the design against the physical structure. This process captures precise details of the building, allowing contractors to compare these with the original plans. As a result, they can verify that the construction aligns with the design and promptly address any discrepancies. This proactive approach ensures that any necessary corrections are identified and implemented efficiently, maintaining the integrity and accuracy of the project.
Planning for Renovation
One of the more obvious uses of laser scanning is in renovation projects. Architects who make designs for such projects need to base them off the pre-existing components of the building. By using 3D laser scan data, architects can get an accurate representation of the as-built dimensions. At the same time, the 3D point cloud data provided by a laser scanner will likely show flaws and capture details that even a site survey may not uncover. With the exceptional accuracy provided by 3D laser scanners, architects can create better designs and minimize the risk of change orders.
Creating 3D BIM Models
Laser scanning is instrumental in creating detailed 3D BIM models. Through scan-to-BIM technology, construction professionals can generate precise digital representations of physical spaces, useful for a variety of applications beyond just building. These 3D models are especially valuable for architects, as they facilitate more efficient communication with stakeholders and investors.
Traditional construction drawings can be challenging for those without technical expertise to interpret. By presenting digital twins, virtual models, or three-dimensional representations, architects can more effectively convey complex information. Laser scanners excel in capturing accurate data quickly, making them an ideal tool for producing the visualizations needed to engage and inform key stakeholders throughout the project.
GPRS Provides Industry-Leading 3D Laser Scanning Services
GPRS 3D Laser Scanning Services provide 2-4mm accuracy by capturing 2 million data points per second, for efficient planning, design, and construction. And our in-house Mapping & Modeling Team can export your GPR utility locates & concrete scans, 3D laser & photogrammetry data, and video pipe inspection reports to create accurate existing condition as-builts – above and below ground – to give you the accurate information you need in a format you can easily work with and share to keep your project on time, on budget, and safe.
From skyscrapers to sewer lines, GPRS Intelligently Visualizes The Built World® to keep your projects on time, on budget, and safe.
What can we help you visualize?
Frequently Asked Questions
What is the difference between a design intent and as-built model?
Design Intent: Deliverables will be shown as a “best fit” to the point cloud working within customary standards, such as walls being modeled 90 degrees perpendicular to the floor, pipes and conduit modeled straight, floors and ceilings modeled horizontal, and steel members modeled straight. This will produce cleaner 2D drawings and allow for easier dimensioning of the scan area. The deliverables will not exactly follow the scan data to maintain design intent standards. Most clients will want this option for their deliverables.
As-Builts: Deliverables will be shown as close as possible to actual field capture. If walls are out of plumb, pipes and conduit show sag, floors and ceilings are unlevel, steel members show camber, etc., this will be reflected in the model. This will produce reality-capture deliverables, but 2D drawings may show “crooked” or out of plumb lines, floors will be sloped or contoured, steel members may show camber, twisting or impact damage. Dimensioning will not be as easy due to elements of the building being out of plumbness/levelness, etc. This option should be used when the exact conditions of the scan area is imperative, such as when the data is being used for fabrication, forensic analysis, bolt hole patterns, camber/sag/deformation analysis, and similar needs.
What is As-Built Documentation?
As-built 3D documentation is an accurate set of drawings for a project. They reflect all changes made during the construction process and show the exact dimensions, geometry, and location of all elements of the work.