Pipeline systems are critical infrastructure, transporting essential resources such as water, oil, gas, and chemicals.
Given their vital role, even minor damage or deterioration in pipelines can have significant financial, environmental, and operational consequences.
Conducting effective repairs is essential, not only to restore the functionality of pipelines but also to ensure that the repairs match the original service life of the system. Here is a comprehensive guide to best practices for ensuring high-quality pipeline repair efforts, focusing on techniques, materials, monitoring, and long-term durability.
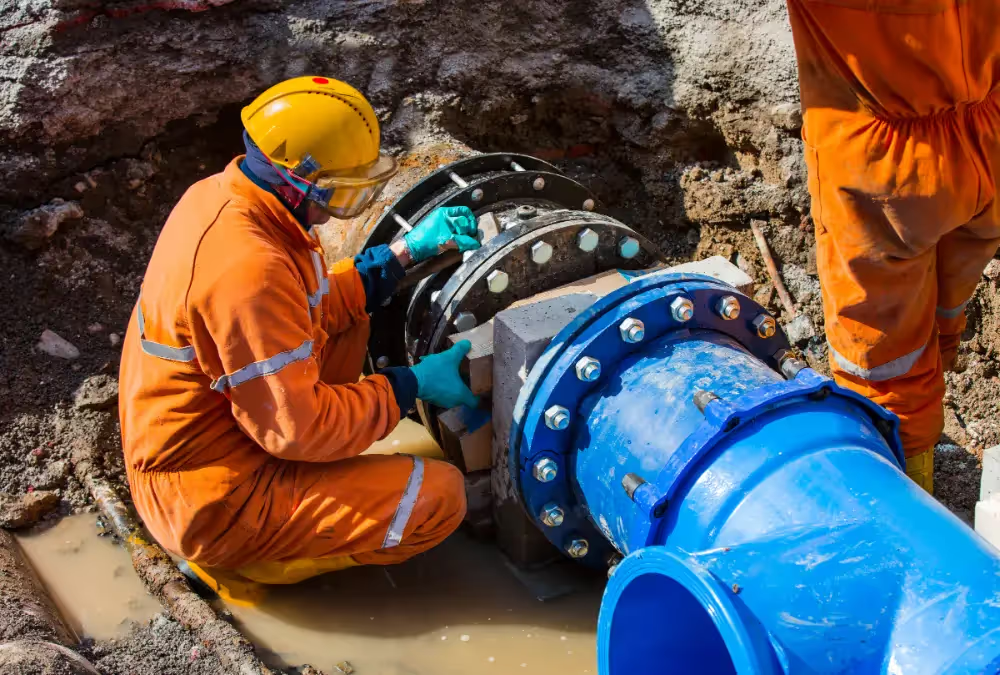
Accurate Assessment of Pipeline Condition
The foundation of a successful pipeline repair begins with a detailed and accurate assessment of the pipeline's current condition. Repair methods and materials vary depending on factors such as the pipe’s material, type of defect, and environmental conditions.
Best Practices for Condition Assessment
- Non-Destructive Testing (NDT): Techniques such as ultrasonic testing, magnetic flux leakage (MFL), and infrared thermography allow inspectors to identify corrosion, cracks, or thinning without damaging the pipe
- Smart Pigging: In-line inspection (ILI) tools, commonly referred to as “pigs,” can travel through pipelines to detect anomalies, such as corrosion or deformation, with precision
- Data Analysis and Historical Records: Assessing past inspection records and repair histories helps determine patterns of wear, allowing for more accurate diagnosis of the root cause
- Hydrostatic Pressure Testing: Pressure tests identify leaks by exposing the pipeline to high-pressure water, ensuring no weak spots are left unaddressed
Early detection of defects minimizes the extent of repair work and reduces the risk of catastrophic failure, keeping downtime and repair costs manageable.
Selecting the Appropriate Repair Method
Choosing the correct repair technique is vital to achieving a lasting solution. Not all pipelines and repair needs are the same; repairs may range from localized spot treatments to major rehabilitation efforts. Some common repair methods include:
Best Practices for Repair Selection
- Clamps and Sleeves: Temporary repairs can be done using clamps or sleeves to halt leaks, but they are generally not suited for long-term solutions
- Composite Wrap Systems: These are increasingly popular for corrosion or crack repairs. They involve wrapping a high-strength, corrosion-resistant composite material around the damaged area. Composite systems are lightweight, non-intrusive, and can extend the life of pipelines without costly shutdowns
- Welding and Sectional Replacements: For pipelines with severe metal loss or rupture, welded repairs or section replacements may be required. Welding ensures structural integrity but demands skilled labor and compliance with safety standards
- Trenchless Repair Methods: For underground pipelines, trenchless technologies such as cured-in-place pipe (CIPP) relining minimize excavation. This technique extends the life of old pipelines with minimal disruption to operations and infrastructure
Selecting the right technique involves balancing cost, downtime, and the long-term needs of the pipeline. Engaging experienced engineers and consultants during the decision-making process is crucial.
High-Quality Materials for Repair Durability
The longevity of any repair effort is only as good as the materials used. Using inferior or incompatible materials could result in frequent maintenance cycles, undermining the repair's objective to extend service life.
Best Practices for Material Selection
- Compatibility with Existing Infrastructure: Ensure that repair materials (like composite wraps, epoxy, or metal) are chemically and mechanically compatible with the original pipeline. Incompatible materials can lead to stress points or premature failure
- Corrosion-Resistant Materials: Given that corrosion is a leading cause of pipeline degradation, using corrosion-resistant alloys, coatings, or composite materials can significantly enhance durability
- Temperature and Pressure Considerations: Select materials rated for the specific pressure and temperature conditions under which the pipeline operates. Using materials that cannot withstand the operational environment may compromise the repair effort
- Standards and Certification: Ensure all materials meet industry standards (such as ASME, ISO, or NACE) for safety and reliability. Certified materials offer a higher degree of assurance for performance over time
Skilled Labor and Adherence to Repair Protocols
Even the best materials and repair techniques can fail if they are not implemented correctly. Skilled labor and strict adherence to repair protocols are crucial for ensuring long-lasting results.
Best Practices for Skilled Execution
- Training and Certification: Personnel involved in pipeline repairs must undergo rigorous training and certification. For example, welding repairs require certified welders familiar with pipeline-specific techniques, while composite repairs demand technicians trained in applying wrap systems
- On-Site Quality Control: Supervisors should verify that all repairs follow design specifications and comply with industry standards. Quality control measures, such as visual inspections and pressure tests, help validate the repair's effectiveness
- Documentation and Traceability: Keeping detailed records of repairs, including materials used, inspection results, and techniques employed, ensures traceability. This documentation can guide future maintenance efforts and allow quick identification of potential issues
Contracting reputable service providers and ensuring a high level of workmanship can dramatically enhance the lifespan of repair efforts.
Implementing Corrosion Control Measures
Corrosion is one of the leading causes of pipeline failure. In addition to addressing corrosion during repairs, proactive measures must be taken to protect the pipeline from future degradation.
Best Practices for Corrosion Control
- Cathodic Protection Systems: Installing cathodic protection (CP) systems helps mitigate corrosion by applying an electric current to the pipeline, preventing the metal from oxidizing
- External Coatings: Applying protective coatings, such as fusion-bonded epoxy (FBE) or polyurethane, provides an additional barrier against moisture and chemicals
- Internal Linings: In pipelines carrying corrosive materials, internal linings or inhibitors can slow down corrosion and extend the life of both the repair and the pipeline itself
- Regular Monitoring and Inspections: Ongoing monitoring, such as corrosion probes and periodic inspections, ensures early detection of corrosion-related issues
Combining these techniques helps maintain the repair's integrity and ensures long-term durability.
Post-Repair Testing and Monitoring
Testing after the repair is crucial to ensure the pipeline can safely resume operation. In addition to verifying the repair's immediate effectiveness, establishing a monitoring framework helps detect any issues before they escalate.
Best Practices for Testing and Monitoring
- Pressure Testing: After repairs, pipelines should undergo hydrostatic or pneumatic pressure tests to confirm there are no leaks
- Ultrasonic Thickness Testing: This technique checks for wall thickness and identifies any areas still prone to corrosion
- Remote Monitoring Systems: Advanced sensors and Internet of Things (IoT) technology allow real-time monitoring of pressure, temperature, and corrosion rates. Remote monitoring helps operators address issues proactively and avoid unexpected failures
- Scheduled Inspections: Regular follow-up inspections, especially during the first few months after repairs, help ensure the repair remains intact and is performing as expected
Planning for Long-Term Maintenance and Lifecycle Management
Achieving repair durability goes beyond the immediate fix. A proactive maintenance strategy and lifecycle management plan are essential for matching the repair’s lifespan to the anticipated service life of the pipeline.
Best Practices for Long-Term Maintenance
- Predictive Maintenance Programs: Implement predictive maintenance programs that use data from sensors and inspections to forecast potential failures
- Risk-Based Inspections (RBI): Prioritize inspections based on risk levels, focusing on high-risk sections that are more prone to failure
- Asset Management Systems: Use digital asset management systems to track the performance of repairs and plan future maintenance more effectively
- Contingency Planning: Have contingency plans in place for emergency repairs to minimize downtime in case of unexpected issues
Integrating repair efforts into a broader lifecycle management approach ensures the pipeline remains functional and safe throughout its intended lifespan.
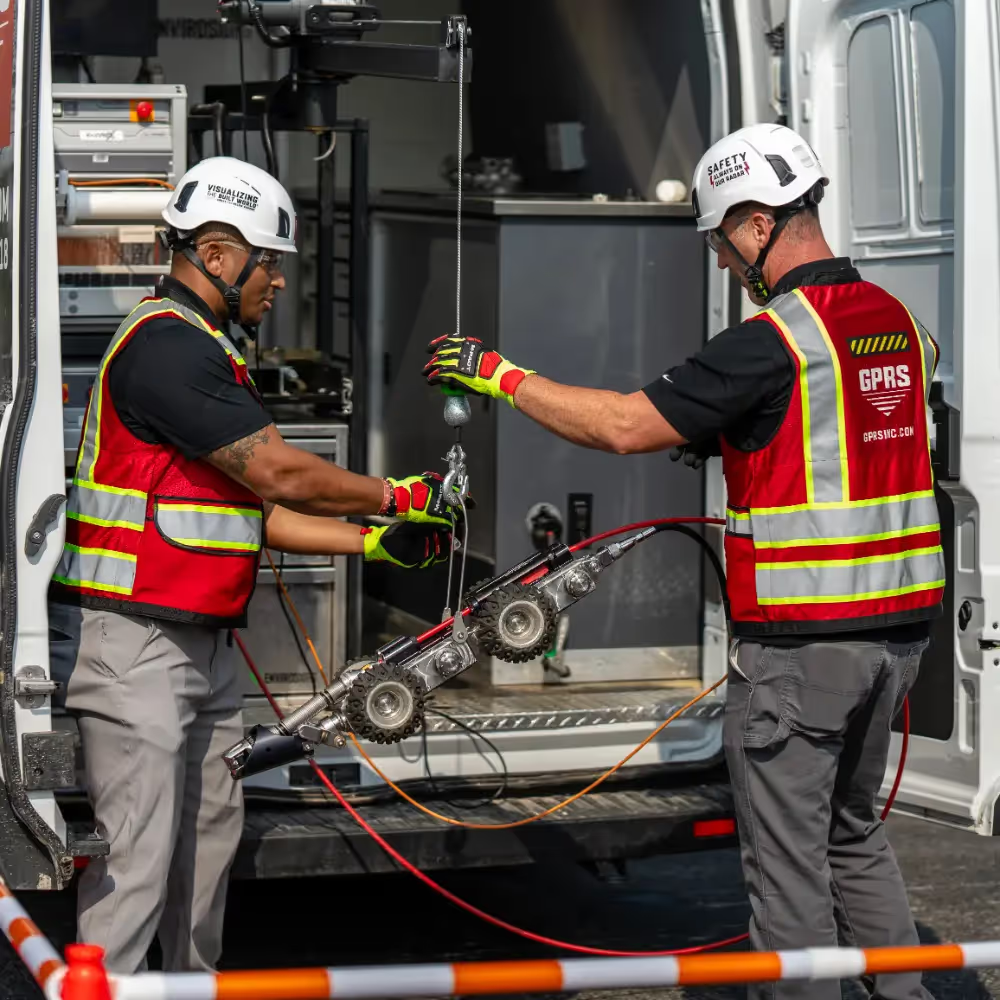
GPRS Puts Pipeline Repair Projects on Track
Pipeline repairs are critical undertakings that demand a balance between cost-efficiency, operational continuity, and long-term durability. By adhering to best practices — such as conducting accurate condition assessments — operators can enhance the reliability of repair efforts.
GPRS helps get pipeline repair projects off on the right foot with our utility locating, leak detection, and sewer pipe inspection (also known as video pipe inspection) services.
Utilizing ground penetrating radar (GPR) scanning and electromagnetic (EM) locating, our SIM-certified Project Managers can map not only your water and/or sewer lines, but also any other buried utilities in your project area – so you know where you can and can’t safely dig when excavating to complete repairs. And with remote-controlled sewer inspection rovers and push-fed cameras equipped with sondes – instrument probes that are detectable with our EM locators and allow for mapping buried sewer lines from the surface – we can inspect your wastewater infrastructure for defects at the same time we’re mapping it.
Our PMs use acoustic leak detection and leak detection correlators to pinpoint the location of leaks in buried water lines, so you can avoid exploratory excavation to try and determine where non-revenue water (NRW) loss is occurring.
All this accurate, field-verified data is at your fingertips 24/7 thanks to SiteMap® (patent pending), GPRS project & facility management application that provides accurate existing conditions documentation to protect your assets and people. Easily, yet securely accessible from any computer, tablet, or smartphone, SiteMap® ensures that your project team always has the data they need to plan, design, manage, dig, and ultimately build better.
From sewer lines to skyscrapers, GPRS Intelligently Visualizes The Built World® to keep your projects on time, on budget, and safe.
What can we help you visualize?
Frequently Asked Questions
What size pipes can GPRS inspect?
Our NASSCO-certified VPI Project Managers have the capabilities to inspect pipes from 2” in diameter and up.
What deliverables does GPRS offer when conducting a sewer pipe inspection?
GPRS is proud to offer WinCan reporting to our Video Pipe Inspection clients. Maintaining sewers starts with understanding sewer condition, and WinCan allows GPRS Project Managers to collect detailed, NASSCO-compliant inspection data. GPRS Project Managers not only inspect the interior condition of sewer pipes, laterals, and manholes – they can also provide a map of their location. The GPRS Mapping & Modeling Department can provide detailed GPS overlays and CAD files. Our detailed WinCan/NASSCO reports contain screenshots of the interior condition of the pipe segments that we inspect, as well as a video file for further evaluation, documentation, and/or reference.
Does GPRS offer lateral launch services?
Yes, we offer lateral launch capabilities as part of our standard Video Pipe Inspection services.