Environmental, Health, and Safety (EHS) processes are critical frameworks within organizations designed to ensure compliance with environmental laws, promote the health and safety of employees, and minimize the impact of business operations on the environment.
These processes not only safeguard the workforce and the surrounding community, they also enhance organizational reputation, operational efficiency, and regulatory compliance.
GPRS has been protecting job sites from damages, clashes, and reworks for 23 years. Learn more here.
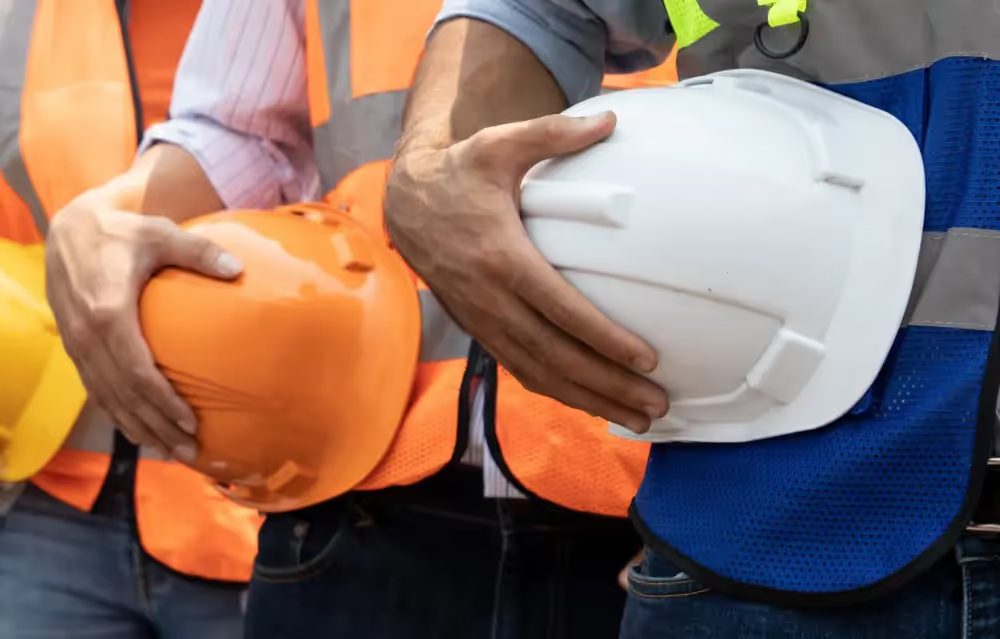
The Importance of EHS Processes
Protecting Employee Health and Safety
The primary objective of EHS processes is to protect employees from workplace hazards. This includes preventing accidents, injuries, and illnesses that can occur due to unsafe working conditions or exposure to harmful substances. Effective EHS programs foster a safe working environment, which can significantly reduce the incidence of workplace injuries and illnesses. This, in turn, leads to lower absenteeism, higher employee morale, and increased productivity.
Ensuring Environmental Compliance
Organizations are subject to a myriad of environmental regulations that mandate the proper handling, disposal, and management of hazardous materials and waste. EHS processes help organizations comply with these regulations, thereby avoiding legal penalties, fines, and potential shutdowns. Moreover, adherence to environmental standards demonstrates a commitment to sustainability, which can enhance the organization's public image and relations with stakeholders.
Promoting Sustainable Practices
Beyond compliance, EHS processes encourage organizations to adopt sustainable practices. This includes reducing waste, conserving energy, and minimizing the overall environmental footprint of business operations. Sustainable practices not only benefit the environment but can also result in cost savings through more efficient use of resources and reduced waste disposal costs.
Enhancing Operational Efficiency
EHS processes often lead to more efficient operations. By identifying and mitigating risks, organizations can avoid disruptions caused by accidents or regulatory non-compliance. Furthermore, continuous improvement initiatives within EHS programs can streamline processes, reduce waste, and improve overall operational performance.
Evaluating the Effectiveness of EHS Processes
To ensure that EHS processes are effective, organizations must regularly evaluate and assess their EHS programs. This involves a combination of qualitative and quantitative measures, as well as ongoing monitoring and continuous improvement efforts. Here are key steps to evaluate the effectiveness of EHS processes:
- Establish Clear Objectives and Metrics: The first step in evaluating EHS effectiveness is to establish clear objectives and corresponding metrics. Objectives should align with the organization's overall goals and regulatory requirements. Metrics might include incident rates, near-miss reports, environmental impact indicators, and compliance audit results. These metrics provide a baseline for measuring progress and identifying areas for improvement.
- Conduct Regular Audits and Inspections: Regular audits and inspections are crucial for assessing compliance with EHS regulations and internal policies. These evaluations can be conducted by internal teams or external auditors to ensure objectivity. Audits should review documentation, inspect facilities, and interview employees to gauge the implementation and effectiveness of EHS processes. Findings from audits should be documented, and corrective actions should be implemented promptly.
- Monitor Incident and Near-Miss Data: Tracking incidents, injuries, and near-misses is vital for understanding the effectiveness of EHS processes. This data can reveal trends and patterns that indicate underlying issues or areas of concern. Organizations should analyze this data to identify root causes and implement preventive measures. Additionally, encouraging employees to report near-misses can provide valuable insights into potential hazards before they result in actual incidents.
- Assess Employee Training and Engagement: Employee training and engagement are critical components of EHS effectiveness. Regular training ensures that employees are aware of potential hazards, understand safety procedures, and know how to respond in emergencies. Evaluating the effectiveness of training programs can be done through assessments, feedback surveys, and observation of employee behavior. Engaged employees are more likely to adhere to safety protocols and contribute to a culture of safety within the organization.
- Review Compliance with Regulatory Requirements: Compliance with regulatory requirements is a fundamental aspect of EHS processes. Organizations should regularly review their adherence to relevant laws and regulations. This includes maintaining accurate records, staying up-to-date with regulatory changes, and ensuring that all necessary permits and licenses are obtained. Non-compliance can result in legal penalties and damage to the organization's reputation.
- Implement Continuous Improvement Initiatives: Continuous improvement is essential for maintaining and enhancing EHS effectiveness. Organizations should establish mechanisms for regularly reviewing and updating EHS processes. This might involve setting up cross-functional teams to identify improvement opportunities, conducting risk assessments, and benchmarking against industry best practices. Continuous improvement efforts should focus on eliminating hazards, reducing environmental impact, and enhancing overall safety and sustainability.
- Foster a Culture of Safety and Responsibility: A culture of safety and responsibility is the foundation of effective EHS processes. Organizations should promote a culture where safety is prioritized, and all employees are encouraged to take responsibility for their own safety and the safety of others. This can be achieved through leadership commitment, clear communication, and recognition of safe behaviors. A strong safety culture ensures that EHS processes are not just policies on paper but are actively practiced and valued by everyone in the organization.
GPRS Supports Your EHS Processes
Environmental, Health, and Safety (EHS) processes are indispensable for organizations committed to protecting their employees, the environment, and their operational integrity. By implementing robust EHS programs, organizations can achieve regulatory compliance, promote sustainability, and enhance their overall efficiency.
GPRS supports your EHS processes through our comprehensive suite of subsurface damage prevention, existing conditions documentation, and construction & facilities project management services. Our 99.8%+ accurate utility locating and concrete scanning services, pinpoint accurate leak detection, and NASSCO-certified video pipe inspections protect your workers from the dangers of subsurface damage.
From skyscrapers to sewer lines, GPRS Intelligently Visualizes The Built World® to keep you and your team on time, on budget, and safe.
What can we help you visualize?
Frequently Asked Questions
Does GPRS perform S.U.E. work?
Subsurface Utility Engineering (SUE) reduces the risk and improves the accuracy of subsurface utility readings. It is broken down into four levels of quality, governed by ASCE Standard 38-02. GPRS provides private utility locating services but does not currently provide a fully comprehensive in-house SUE service. GPRS does not provide engineering services. If you need professional engineering services, please contact a professional engineer.
How does GPRS ensure quality of service?
GPRS Project Mangers undergo a rigorous training program to ensure you have the most reliable and accurate infrastructure visualization services at your disposal. This includes the Subsurface Investigation Methodology (SIM), which consists of 320 hours of field training and 80 hours of classroom training during which Project Managers tackle real-world scenarios in a safe and structured environment.