The advanced age of most buried water, sewer, and gas pipelines in the U.S. has led to an ever-increasing need for maintenance and repairs to this critical infrastructure.
One innovative method that has become essential in addressing aging underground pipelines is static pipe bursting. This trenchless technology offers an efficient way to replace deteriorated pipes with minimal surface disruption.
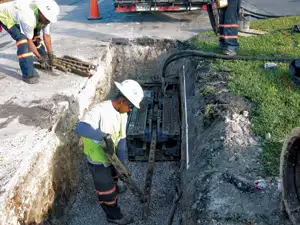
What Is Static Pipe Bursting?
Static pipe bursting is a method used to replace old or damaged underground pipelines with new pipes of the same or larger diameter. Unlike traditional excavation methods that require digging up long stretches of land, static pipe bursting uses a trenchless approach, minimizing the impact on surface structures, roadways, and landscapes.
In this process, the old pipe is split or burst from within using a hydraulic pulling force applied to a bursting head, while a new pipe is pulled into place simultaneously. This method is called “static” because it relies on constant pulling pressure instead of dynamic impact or pneumatic tools, providing greater control and reduced vibrations during the replacement.
How Static Pipe Bursting Works
The static pipe bursting process involves several key steps, each of which plays a vital role in ensuring the success of the operation.
1. Site Preparation and Launch Pit Installation
Before the bursting begins, small access points called launch and reception pits are excavated at either end of the section to be replaced. These pits are essential for setting up the bursting equipment and positioning the replacement pipe.
2. Insertion of Bursting Rods
A series of steel bursting rods are pushed through the existing pipeline from the reception pit to the launch pit. These rods serve as the pulling mechanism, creating a continuous line through the length of the old pipe.
3. Attaching the Bursting Head and New Pipe
At the launch pit, a specialized bursting head is attached to the front end of the rod string. This head features a cutting edge designed to split or break the old pipe as it moves through. The new pipe, typically made of high-density polyethylene (HDPE), PVC, or ductile iron, is connected to the rear of the bursting head.
4. Hydraulic Pulling Process
Hydraulic machinery applies steady pulling force to the rod string, drawing the bursting head and new pipe through the old pipeline. As the head progresses, it bursts or splits the existing pipe into fragments, pushing the debris into the surrounding soil.
5. Pipe Replacement Completion
Once the bursting head exits the old pipe and reaches the reception pit, the new pipe is fully installed in the space left by the old one. The rods are disconnected and removed, and the ends of the new pipe are secured and connected to the existing infrastructure.
Applications of Static Pipe Bursting
Static pipe bursting is highly versatile and is used in various infrastructure projects. The technology is especially effective for replacing:
- Sewer lines: Aging sewer systems made from clay, cast iron, or other brittle materials often need replacement. Static pipe bursting is ideal for these situations, especially in residential areas with minimal space for digging
- Water mains: Old water pipelines prone to leaks or contamination are prime candidates for pipe bursting
- Gas lines: Static pipe bursting is used to upgrade gas pipelines, especially where expansion to larger diameters is required to meet increased demand
- Storm drains: Larger-diameter pipes, such as storm drains, can also be replaced using this method, particularly where flooding or blockages are a concern
Advantages of Static Pipe Bursting
One of the key reasons for the growing popularity of static pipe bursting is its numerous advantages over traditional open-cut methods.
1. Minimal Surface Disruption
Unlike traditional methods that require large trenches, static pipe bursting only requires small launch and reception pits. This reduces disruption to roadways, sidewalks, and landscapes, making it ideal for urban areas or environments with sensitive ecosystems.
2. Cost-Effective
Although the initial setup costs can be higher than traditional methods, the overall cost of static pipe bursting is often lower due to reduced labor, quicker project completion, and minimal surface restoration.
3. Increased Pipe Capacity
Static pipe bursting can replace old pipelines with larger-diameter pipes, improving flow capacity and future-proofing infrastructure for population growth and increased demand.
4. Suitable for Various Pipe Materials
This method works well for replacing a wide range of materials, including clay, concrete, cast iron, and steel. Additionally, it allows the installation of modern materials like HDPE, which offers improved durability and resistance to corrosion.
5. Environmentally Friendly
With less excavation required, static pipe bursting minimizes the amount of soil displacement and waste material generated during the project. This makes it a more environmentally friendly solution compared to open-cut excavation.
Challenges and Limitations of Static Pipe Bursting
While static pipe bursting offers many benefits, it is not without its challenges. Understanding these limitations is essential for project planners and engineers.
1. Soil Conditions Matter
The success of static pipe bursting depends heavily on the type of soil surrounding the pipeline. Soft or loose soils may not provide enough resistance for the bursting process, while hard or rocky soils can complicate the operation.
2. Limited to Certain Pipe Sizes
While static pipe bursting can increase the diameter of the replacement pipe, it is usually limited to a diameter increase of up to 30%. For significant upsizing, other methods may need to be considered.
3. Risk of Pipe Collapse or Misalignment
In cases where the old pipe is severely degraded or crushed, the bursting process may encounter difficulties. There is also a small risk that the new pipe could misalign during installation, requiring additional adjustments.
4. Access Constraints
The need for launch and reception pits means that some areas with limited access may pose challenges for static pipe bursting. For example, pipelines running beneath densely developed properties may require alternative methods.
Key Equipment Used in Static Pipe Bursting
Several specialized tools and machines are essential for the static pipe bursting process:
- Hydraulic Power Unit: This machine provides the constant pulling force needed to move the rod string and bursting head through the old pipe
- Bursting Rods: Steel rods are connected end-to-end to create a continuous pulling line
- Bursting Head: The cone-shaped head splits the old pipe and pushes the fragments outward, making room for the new pipe
- New Pipe Material: HDPE is the most commonly used material for replacement pipes due to its flexibility and resistance to corrosion
- Guidance and Alignment Tools: Laser guidance systems or CCTV cameras may be used to ensure proper alignment during the pulling process
Best Practices for Successful Pipe Bursting Projects
To maximize the effectiveness of static pipe bursting, several best practices should be followed:
- Preliminary Inspection: Conduct a thorough inspection of the existing pipeline using CCTV cameras or other diagnostic tools to identify potential obstacles, such as collapsed sections or blockages.
- Soil Testing: Analyze the soil conditions along the pipe route to assess suitability for bursting.
- Proper Equipment Sizing: Use equipment that matches the diameter and length of the pipeline being replaced to ensure efficient operation.
- Experienced Operators: Hire contractors with expertise in pipe bursting to reduce the risk of complications during the project.
- Post-Installation Inspection: After installation, conduct pressure testing and camera inspections to confirm the integrity and alignment of the new pipe.
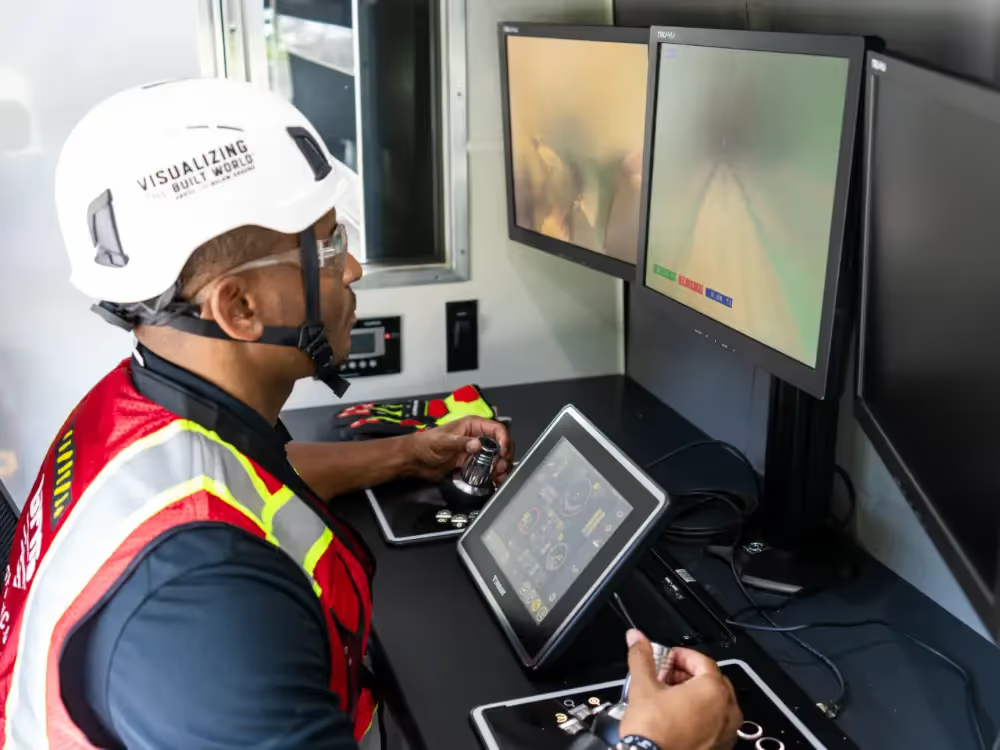
GPRS Ensures Safety & Success of Maintenance & Repair Projects
Static pipe bursting is a powerful trenchless technology that has revolutionized the way aging underground infrastructure is replaced. With its ability to minimize surface disruption, reduce project costs, and install larger, more durable pipes, it has become a go-to solution for many municipalities and contractors.
Whenever you’re working with or around buried utilities, having a complete and accurate map of that infrastructure is critical to the safety and success of that project.
GPRS provides 99.8% accurate utility locating and mapping services, utilizing ground penetrating radar (GPR) scanners and electromagnetic (EM) locators to visualize what’s below your job site. And our Video Pipe Inspection services use remote-controlled, CCTV camera-equipped sewer inspection rovers and push-fed sewer scopes to not only map buried pipelines but also provide NASSCO-certified reporting on the integrity of these utilities.
From sewer lines to skyscrapers, GPRS Intelligently Visualizes The Built World® to keep your projects on time, on budget, and safe.
What can we help you visualize?
Frequently Asked Questions
What do I get when I hire GPRS to conduct a utility locate?
Our Project Managers flag and paint our findings directly on the surface. This method of communication is the most accurate form of marking when excavation is expected to commence within a few days of service.
GPRS also uses a global positioning system (GPS) to collect data points of findings. We use this data to generate a plan, KMZ file, satellite overlay, or CAD file to permanently preserve results for future use. GPRS does not provide land surveying services. If you need land surveying services, please contact a professional land surveyor. Please contact us to discuss the pricing and marking options your project may require.
Can GPRS locate PVC piping and other non-conductive utilities?
Ground penetrating radar (GPR) scanning is exceptionally effective at locating all types of subsurface materials. There are times when PVC pipes do not provide an adequate signal to ground penetrating radar equipment and can’t be properly located by traditional methods. However, GPRS Project Managers are expertly trained at multiple methods of utility locating.
What deliverables does GPRS offer when conducting a video pipe inspection (VPI)?
GPRS is proud to offer WinCan reporting to our Video Pipe Inspection clients. Maintaining sewers starts with understanding sewer condition, and WinCan allows GPRS Project Managers to collect detailed, NASSCO-compliant inspection data. GPRS Project Managers not only inspect the interior condition of sewer pipes, laterals, and manholes – they can also provide a map of their location. The GPRS Mapping & Modeling Department can provide detailed GPS overlays and CAD files. Our detailed WinCan/NASSCO reports contain screenshots of the interior condition of the pipe segments that we inspect, as well as a video file for further evaluation, documentation, and/or reference.
Does GPRS offer lateral launch services?
Yes, we offer lateral launch capabilities as part of our standard Video Pipe Inspection services.