As the U.S. Environmental Protection Agency (EPA) tightens its regulations around lead and copper in drinking water, water systems across the country are under increasing pressure to comply with the Lead and Copper Rule Improvements (LCRI) and the Lead and Copper Rule Revisions (LCRR).
With deadlines looming and complexity mounting—particularly around inventory development, customer communication, and service line replacement—utilities are turning to digital tools to help bridge the compliance gap.
Digital transformation isn’t just a buzzword; it’s becoming a lifeline for water systems trying to meet federal requirements in a cost-effective, scalable, and timely manner. From asset management software to cloud-based GIS platforms and AI-powered data analytics, technology is playing an essential role in preparing for both LCRI and LCRR compliance.
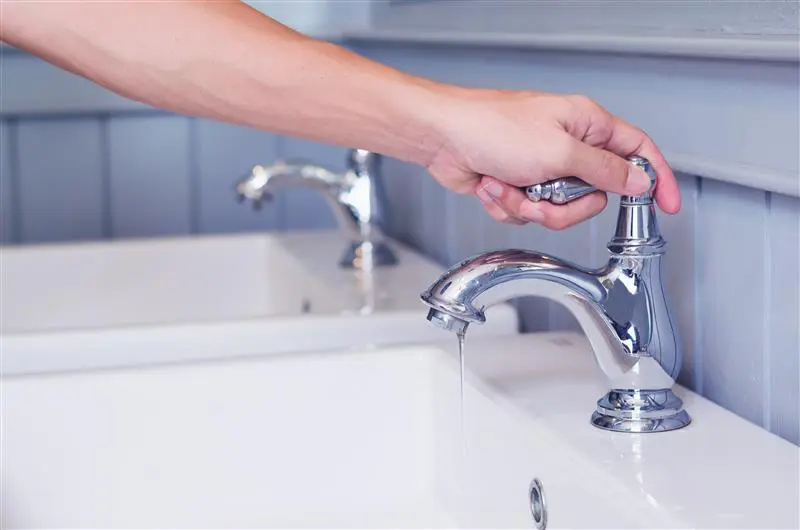
Understanding LCRR and LCRI
The LCRR, published in January 2021, mandates that all community water systems develop a comprehensive inventory of both utility- and customer-owned lead service lines (LSLs) by October 16, 2024. This requirement includes identifying the materials used in service lines and creating a plan to replace those containing lead.
The LCRI builds on the LCRR by clarifying which LCRR provisions will be maintained and detailing new LCRI requirements and compliance deadlines. Together, these rules represent a significant shift in how lead is managed in drinking water systems, necessitating stronger visibility, communication, and accountability across utility operations.
The Compliance Challenge
Meeting these requirements poses numerous challenges:
- Identifying unknown service lines: Many utilities lack complete records of materials used in service lines, particularly on the customer-owned portion. Many more lack accurate data of these lines’ locations.
- Data management: Accurate and accessible data is essential for regulatory reporting and public transparency.
- Customer coordination: Because the rules apply to both sides of the service line, utilities must engage with customers to inspect and, if necessary, replace customer-owned pipes.
- Resource constraints: Smaller utilities may struggle with the staffing, technical expertise, and funding needed to implement compliance plans.
These challenges underscore the need for digital innovation that can streamline data collection, enhance public engagement, and drive informed decision-making.
Digital Solutions: The Path Forward
1. Asset Management & GIS Platforms
Geographic Information Systems (GIS) play a central role in LCRR compliance, enabling utilities to create interactive, map-based service line inventories. These platforms allow for the integration of historic records, field inspection data, and predictive modeling to categorize service line materials with greater confidence.
2. Predictive Analytics and Machine Learning
Where historical data is missing or inconclusive, machine learning algorithms can help fill in the gaps. By analyzing patterns in existing data—such as construction era, property records, or neighborhood characteristics—AI models can predict the likelihood that a service line contains lead.
This predictive approach allows utilities to target investigations and reduce the need for costly, labor-intensive field verification. The EPA has acknowledged predictive modeling as an acceptable methodology for categorizing unknown lines, provided that the approach is transparent and documented.
3. Cloud-Based Platforms for Data Collection and Reporting
Cloud-based tools enable seamless data entry from the field, centralize customer service interactions, and automatically generate compliance documentation. They also provide templates for customer notifications, educational materials, and sample result letters, ensuring that communication aligns with regulatory expectations.
4. Customer Engagement Tools
Given the importance of customer-owned service lines in both LCRR and LCRI, public engagement is a critical success factor. Digital tools help streamline this process through customer portals, online self-reporting forms, and automated outreach campaigns.
For example, utilities can deploy digital surveys that ask homeowners to identify the material of their service lines using photos or inspection guides. The data collected through these platforms feeds directly into the utility’s inventory and reduces the need for on-site visits.
Some platforms also allow customers to schedule inspections or replacements directly online, improving responsiveness and satisfaction while reducing administrative burden.
5. Mobile Field Data Collection
Mobile applications used by field crews can dramatically improve the speed and accuracy of service line verification. With GPS-tagged photos, drop-down menus for materials identification, and cloud syncing, field data can be uploaded in real time and integrated with GIS systems.
This eliminates paper-based recordkeeping, minimizes data entry errors, and enables immediate analysis. Teams can also access customer records and work orders from the field, improving operational efficiency.
Funding and Scalability
Federal funding from the Bipartisan Infrastructure Law (BIL) is helping make digital transformation more attainable. Many states are channeling funds from the Drinking Water State Revolving Fund (DWSRF) into technical assistance and infrastructure upgrades. These funds can be used to purchase software, train personnel, and digitize historical records—an essential first step for compliance.
However, scalability remains a concern. Smaller and rural systems may need more targeted support, especially when it comes to deploying predictive analytics or cloud-based inventory platforms. Regional partnerships and shared service models can help spread costs and expertise across neighboring utilities.
Preparing for the Future
With the LCRR compliance deadline less than a year away and LCRI rulemaking on the horizon, utilities must act now. Digital tools offer a pathway not just to compliance, but to long-term resilience and operational excellence.
GPRS offers 99.8%+ accurate utility line location and mapping, and NASSCO-certified video pipe inspection (VPI) services to accurately map all your storm and sanitary sewer lines, laterals, and to find cross bores caused by trenchless technology (directional drilling). We ensure you have a comprehensive map of your entire drinking and wastewater systems to make finding and replacing LSLs much faster and easier.
Further, every GPRS customer receives access to SiteMap® (patent pending), our interactive infrastructure visualization software that provides you with layered, interactive utility maps and NASSCO WinCan reports in a secure, cloud-based platform, so you can control the quality of your water infrastructure information and who has access to it. SiteMap® allows you to put the right information into the right hands, at exactly the right time.
What can we help you visualize?
Frequently Asked Questions
How can I tell if my building has lead pipes that need to be replaced?
If you have access to the original record drawings that include MEP (mechanical electrical & plumbing) specifications, you may be able to determine the material of the original pipes. However, most record drawings are inaccurate and do not include renovations and updates. The conscientious process to assess and remove LSLs is to hire an expert utility locating company near you to locate your pipes so you can limit potholing to determine their material.
Learn more about GPRS 99.8%+ accurate utility locating and mapping, here.