It’s hard to imagine that anyone managing a facility – be it a college campus, a healthcare center, a commercial manufacturing plant, or a government building – still resorting to paper to track environmental, health, and safety (EHS) reporting. However, at least 20% of facility managers do not utilize digital EHS solutions for their regulatory compliance, tracking, and employee safety concerns.
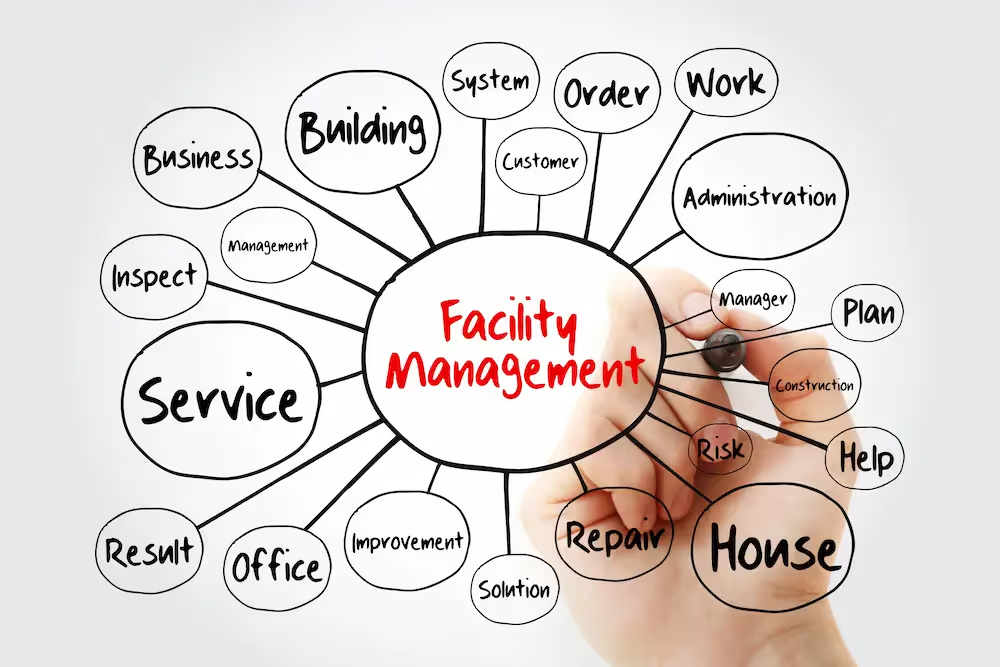
Instead, they use a self-constructed, hybrid set of reporting techniques that may include everything from paper files to massive digital spreadsheets and store each portion of those records separately, in an average of four different locations, according to research conducted by Finch for GPRS. Not only does this D-I-Y approach to EHS create more work for employees and the facility managers themselves, it leaves stakeholders and the facility at risk.
Here are just a few of the sobering statistics about the risk involved:
• The Occupational Health and Safety Administration (OSHA), issued a huge $132.3 million in fines in 2023 alone – a 30% increase over 2022, as the federal agency added staff and increased inspections
• In 2017, the first year after Great Britain enacted new health and safety guidelines, fines issues by authorities more than doubled, from £35 million to over £73 million, due to lack of ESH compliance
• 62% of facility managers report experiencing a utility strike between 2015-2020 and 50% of managers cited inaccurate data and miscommunication as the primary cause of the damages
• The average cost of a utility strike is $56,000 and as much as six weeks of downtime as reported by Finch for GPRS in 2020
And for those managers who are trying to keep it all straight in Excel…
• 88-90% of all spreadsheets contain “significant errors,” according to research conducted by Professor Ray Panko at the University of Hawaii. The “vast majority” of those errors are human mistakes.
So, how do you choose the right digital solutions for your facility ESH reporting?
The first step is to assess the needs of your facility’s infrastructure, workforce, and production.
Do you need to streamline your EHS program elements with segmented trainings, contractor onboarding, and documentation version control?
How much automation do you need? Do you want to be notified the moment a non-compliant event is logged, reminders to complete remediation measures and compliance deadlines?
What level of accessibility, sharing, and security do you require? Do you need a mobile application with a SaaS platform? How many integrations of other software, like GIS and inventory applications need to be supported?
And then there are the questions you have to answer to justify the return on investment for your company’s stakeholders:
• How will this software help solve our problems?
• How much will it cost?
• What are the features we need?
• What happens if it doesn’t reduce incidents?
The National Safety Council released a paper on how to unravel the tech-speak and assess EHS software on a direct comparison basis. It also looked at the increasing trend of machine learning (AI). Predictive analytic algorithms were rightly expected to explode by 67% of EHS professionals they polled.
The paper, part of the NSC’s “Work to Zero” initiative, designed to reduce workplace fatalities, looks at the “use of EHS software and mobile applications for reducing injury and fatality risk, and managing incidents in the workplace” with a focus on industrial operations.
Their methodology was simple:
• Identify case studies and suitable applications for EHS software
• Develop a market landscape “shortlist” of vendors to help facility safety managers
The NSC looked at large-scale enterprise software (on premise) and SaaS (software as a service) cloud-based platforms to provide the widest variety of alternatives to users. It also took into account the differences between customized and off-the-shelf software, their benefits, and their limitations.
How Will You Use the Software?
Knowing your use case will help determine what features you require. The NSC broke their findings into four specific use case scenarios:
1. Hazard Identification & Risk Management (HIRA)
2. Permit Management (Permit to Work/PtW)
3. Incident Management
4. Safey Audit Management
Other sources invite you to consider functionality, workforce buy-in/engagement, ease of implementation & training, privacy & security, compliance, support quality, scalability, and the ability to integrate with other necessary software as qualifying factors.
What About Data Quality?
One of the toughest realizations for any FM is coming to terms with the fact that the data held in any system is only as good as the quality of its collection. Nowhere is that more evident than with facility and site infrastructure. Even the most advanced integrated GIS platform still requires you – the manager, or your team – to input the data, meaning that just like those spreadsheets, there will be errors.
That is why so many FMs are excited about the automating qualities of an algorithmic approach to forecasting and notifications, to help monitor data quality. However, even the most sophisticated software cannot accurately capture your above and below-ground physical infrastructure.
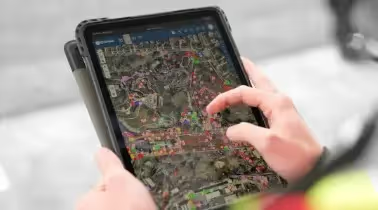
Accuracy above and below-ground requires expertise in multiple technologies, an understanding of the purpose of the data, and the ability to instantly upload findings in a digital format that offers data portability to other GIS and EHS platforms.
Which is why GPRS created SiteMap®. SiteMap® helps to ensure your facility infrastructure data – from your buried utilities to your rooftop – are up-to-date, version-sorted, accurate, and construction-grade. Because GPRS collects and uploads the data for you. And, in the case of utility locating and concrete scanning and imaging – 99.8% accurate.
In most cases, your facility’s layered, geolocated, and 99.8% accurate utility maps are available in SiteMap® within five minutes of completion, ensuring you have the data you need to dig safely at your fingertips, from anywhere, 24/7. Our in-house CAD team can turn your utility, concrete imaging, video pipe inspection reporting, and 3D laser scans into a wide variety of deliverables that can all also be accessed easily inside SiteMap®. They include FLRPLN, which you can use to quickly delineate escape routes in case of emergency, and Walkthru 3D, that provides an individualized guided 3D tour of an escape route based on its point of origin. Both are powerful tools in a facility manager’s risk mitigation arsenal.
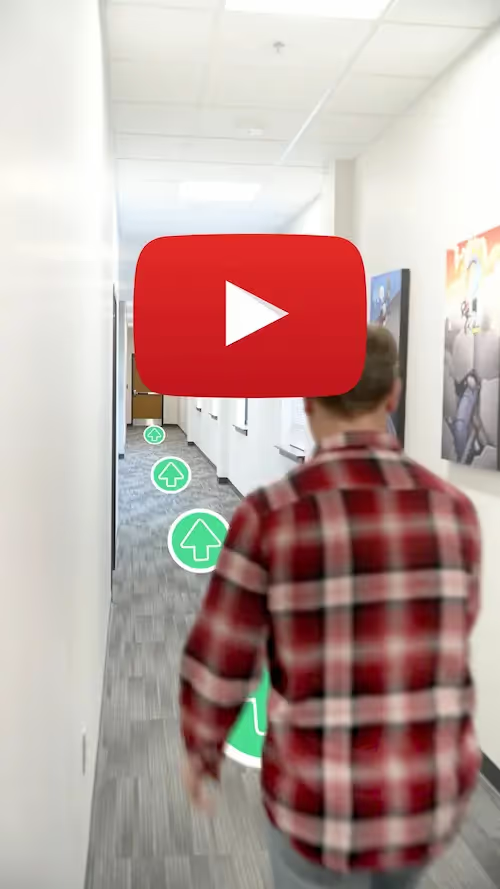
Leveraging EHS and GIS software – when it’s the right software to meet your specific facility needs – protects the safety of your team, gives you deeper insights into emerging trends, ensures your regulatory compliance, untethers you from the office or site, and safeguards your reputation, all while reducing mistakes and keeping insurance premiums lower.
GPRS helps facility managers nationwide to Intelligently Visualize The Built World®.
What can we help you visualize?