GPRS safety partners Gilbane and Turner Construction recently topped out the Buffalo Bills’ $2.1 billion New Highmark Stadium in Orchard Park, New York.
The milestone marks the halfway point of the joint venture project that broke ground twenty months ago and is expected to be completed prior to the 2026 NFL season, according to a press release issued by New York Governor Kathy Hochul’s office.
“Today marks a major milestone for the future home of the Buffalo Bills and one of the largest construction projects ever in Western New York,” Hochul said. “This world-class stadium would not be possible without our skilled union workers and partners, and I look forward to cheering along with them at the first Bills game being played here in the 2026 season.”
Hochul and other politicians were joined by NFL Commissioner Roger Goodell, project stakeholders, hundreds of union workers, and more than 1,400 guests at the topping out ceremony, during which the final structural steel beam was placed in the Bills’ future, 60,000-seat home. Kansas City, Missouri-based architecture firm Populous designed the stadium which is right next to the team’s existing facility.
According to the press release, in addition to structural steel work, project teams have removed 742,000 cubic yards of dirt and installed over 46,000 cubic yards of foundation concrete in addition to placing miles of piping. As many as 1,500 workers will be on site at peak construction.
Construction will now turn to the interior of the building as well as on the roof. The Gilbane/Turner joint venture is currently constructing a 360-degree canopy structure at the stadium’s uppermost level, which will extend to a height of 116 feet above grade. At the same time, the team is setting precast components that will shape the building’s exoskeleton, ahead of installing the exterior envelope this spring — which will include precast architectural panels, perforated metal, and glass elements.
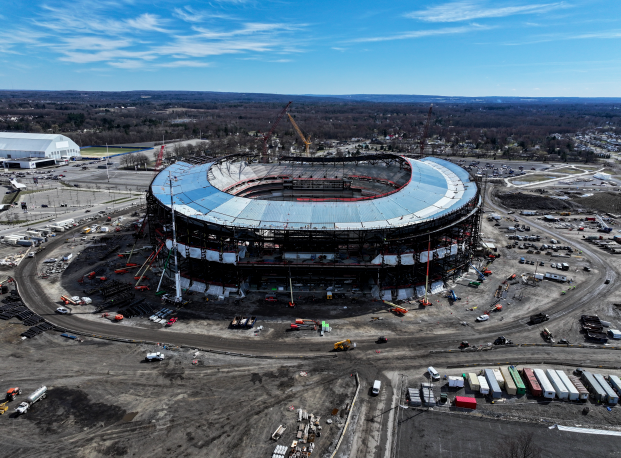
Once complete, New Highmark Stadium will also include:
- Heated concourses and seating in several areas
- The world’s largest snow melt system, which will utilize roof sensors to monitor and liquefy snow piles
- Two video boards and an acoustic system
- A mix of concessions, kitchens and retail stores
“We’re incredibly proud to reach this major milestone in the construction of the new Highmark Stadium,” said Gilbane Principal-in-Charge John LaRow. “This achievement is testament to the hard work of our skilled trade partners who have worked over 1.8 million hours to date building this state-of-the-art facility. Thanks to the incredible collaboration with the Buffalo Bills, the Gilbane | Turner team, Populous, Legends and the support of the State of New York and Erie County, this stadium will serve as a proud beacon for the region and showcase the very best in professional sports venues.”
Gilbane/Turner Program Director Joe Byrne said the topping out milestone “marks more than the structural progress of a stadium.”
“It reflects the spirit and strength of the Buffalo community,” Byrne said. “We are deeply grateful to the Buffalo Bills, our dedicated staff and trade partners and the thousands of union tradespeople – so many of whom call this region home – whose skill and commitment are bringing this landmark project to life. It is profoundly meaningful that members of the community are helping to build a venue that will serve as a source of pride and celebration for generations to come.”
“This topping out milestone at New Highmark Stadium stands as a testament to the positive impacts development done under project labor agreements and with prevailing wage measures can have on our local communities and collective state economy,” added New York State Building and Construction Trades Council President, Gary LaBarbera. “The construction of this new home for The Buffalo Bills is generating thousands of family-sustaining careers, adding economic stimulus to our neighborhood, and providing hard-working people in the Western New York region accessible pathways to the middle class. We thank Governor Hochul for her efforts in pushing this project forward and look forward to continuing our role in creating a world-class venue for Buffalo football fans and players alike.”
Whether you’re building a 60,000-seat football stadium or renovating an office building, GPRS supports your construction projects through our comprehensive suite of subsurface damage prevention, existing conditions documentation, and construction & facilities project management services. We offer precision concrete scanning and utility locating, pinpoint-accurate leak detection, NASSCO-certified sewer line inspections, 2-4mm accurate 3D laser scanning, and in-house mapping & modeling tailored to your project’s specific needs.
All this accurate, actionable data is at your fingertips 24/7 thanks to SiteMap® (patent pending), GPRS’ project & facility management application that provides accurate existing conditions documentation to protect your assets and people.
From skyscrapers to sewer lines, GPRS Intelligently Visualizes The Built World® to help keep you on time, on budget, and safe.
What can we help you visualize?
Frequently Asked Questions
Will I need to mark out the utilities that GPRS locates?
GPRS will locate and mark all utilities for you. We have a variety of tools and markers we can use to highlight the locations of utilities, underground storage tanks and whatever else may be hiding.
What is the difference between a design intent and as-built model?
DESIGN INTENT – deliverables will be shown as a "best fit" to the point cloud working within customary standards, such as walls being modeled 90 degrees perpendicular to the floor, pipes and conduit modeled straight, floors and ceilings modeled horizontal, and steel members modeled straight. This will produce cleaner 2D drawings and will allow for easier dimensioning of the scan area. The deliverables will not exactly follow the scan data to maintain design intent standards. Most clients will want this option for their deliverables.
AS-BUILTS – deliverables will be shown as close as possible to actual field capture. If walls are out of plumb, pipes and conduit show sag, floors and ceilings are unlevel, steel members show camber, etc., this will be reflected in the model. This will produce reality-capture deliverables, but 2D drawings may show “crooked” or out of plumb lines, floors will be sloped or contoured, steel members may show camber, twisting or impact damage. Dimensioning will not be as easy due being out of plumbness/levelness, etc. This option should be used when the exact conditions of the scan area is imperative. Clients using the data for fabrication, forensic analysis, bolt hole patterns, camber/sag/deformation analysis, and similar needs would require this option.