“That was the darkest dark I’ve ever experienced. There was no sound, I had no idea where I was. Thank God the headlamp didn’t go out.” – William Johnson, Senior Project Manager, GPRS
It’s 2015, and GPRS Senior Project Manager William Johnson stands more than a mile below the Pennsylvania soil in a mine shaft. He’s completely alone, the light on his helmet barely holding his inky black surroundings at bay.
Should Johnson’s headlamp die, he’s been instructed to remain where he is until someone comes to retrieve him. He briefly shuts the light off just to get a sense of how dark it truly is in the bowels of the mine.
“That was the darkest dark I’ve ever experienced,” he recalls. “There was no sound, I had no idea where I was. Thank God the headlamp didn’t go out.”
Johnson was a fresh face at GPRS, having only joined the team a few months prior to being called out to what he thought was a routine concrete scanning inspection. He joined GPRS after hearing about the utility locating company from a couple of friends who already worked here. He figured he knew what to expect.
“I had no real information about the job other than the fact that it was on a mining facility property, and they were interested in the slab thickness of a concrete pad that they had poured,” he said.
Johnson arrived where he was told to meet his site contact, only to be told to load his scanning equipment into a waiting golf cart, and don a jumpsuit and hardhat.
The next thing he knew, they were driving into a mineshaft. It took them about 30 minutes to reach the point deep beneath the earth where the concrete pad was waiting.
“It was anywhere from a mile to two-and-a-half miles below the surface,” Johnson said.
There were other workers in the mine with Johnson, but they had their own jobs to do and quickly left him alone to conduct his scan. Johnson needed to determine the thickness of the slab so that the mining company could determine if it was strong enough to support a heavy piece of equipment they needed to move into the mine.
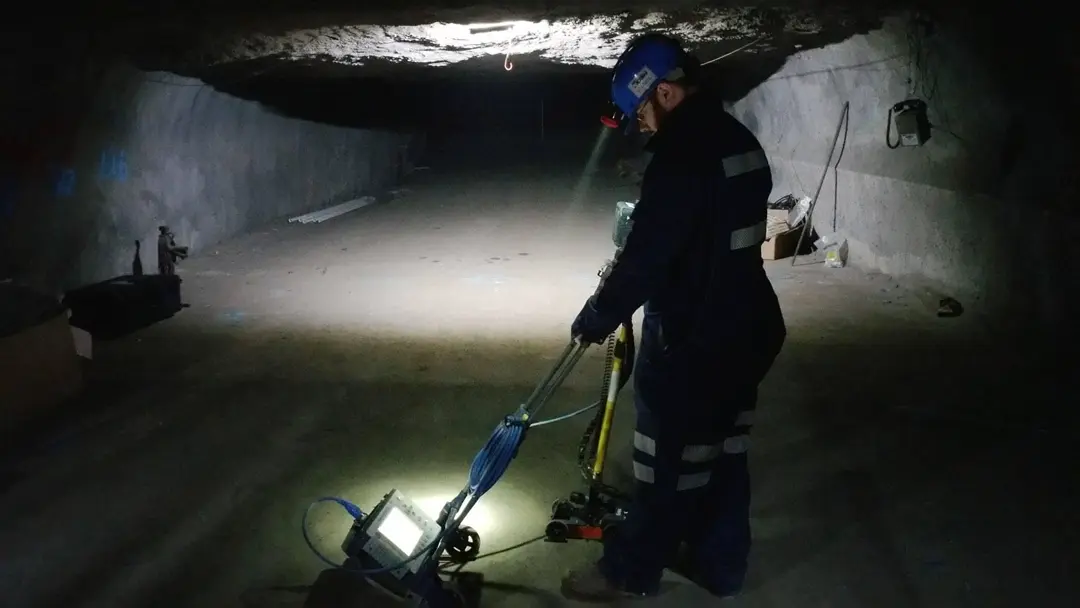
At the time, the most sophisticated and accurate ground penetrating radar (GPR) controller for precision concrete scanning was the SIR 3000. Johnson brought this 9-pound device and its 1600 MHz antenna into the mine shaft.
While this setup was top-of-the-line in its day, it has been left in the dust by GPRS’ current concrete scanning equipment. To do the same job now, Johnson would use either a StructureScan Mini XT or Proceq scanner – both handheld devices weighing a fraction of what the SIR 3000 weighs, yet capable of accurately detailing slab thickness and locating any subsurface obstructions.
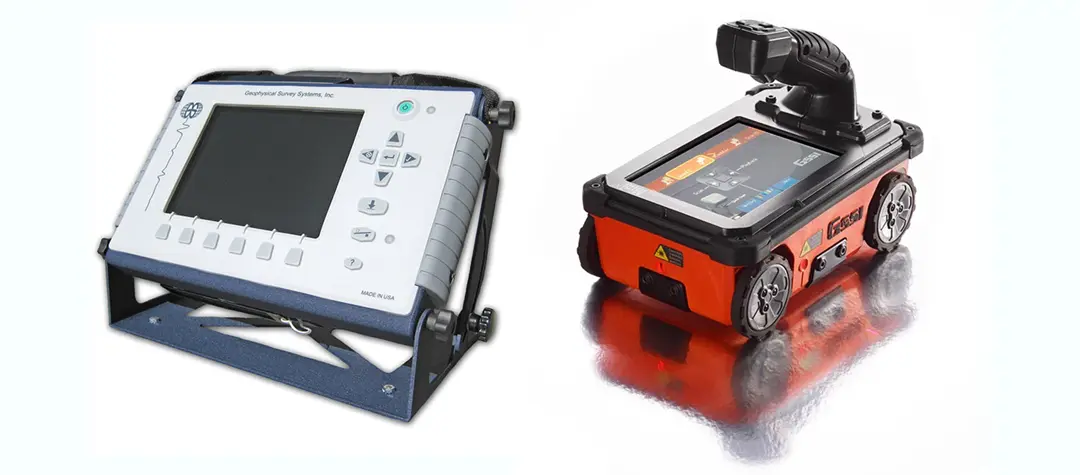
“With the new technology, depending on what unit you have, it’s either all wireless or an all-in-one unit,” Johnson explained. “The unit I currently use is the Mini XT, and with that you can attach a walking stick to it and that houses the GPR unit as well as the computer system. It’s all-in-one; no wires, no dolly, it’s significantly lighter, it’s way more accurate, and the quality of the data is a lot better as well.”
Mining is one of the world’s oldest industries, and it remains big business. The value added by the United States mining industry (excluding oil and gas) amounted to $61.24 billion in 2021. By comparison, the value added in 1998 came to approximately $29 billion.
Today, there are nearly 13,000 active mines in the U.S.
A notoriously dangerous profession, mining is safer today than it has ever been. In 2020 the U.S. Department of Labor’s Mine Safety and Health Administration (MSHA) reported there were 29 mining fatalities, the sixth consecutive year that mining fatalities were below 30. Five of those 29 fatalities occurred in coal mines – a historic low.
Safety, however, is about constantly improving practices and policies. You can never be too careful when it comes to planning and preparing for every phase of a project that will occur deep underground.
Despite the heavy, unwieldy equipment at his disposal, Johnson successfully determined the thickness of what must be one of the most unusually placed concrete pads in the world. Johnson can’t recall if it took two hours or four hours to completely scan the concrete pad – being a couple of miles away from sunlight tends to make it hard to keep track of time – but the important part is that, despite the unique conditions and challenges at play, his work was accurate. That accuracy ensured that the client knew where they could and couldn’t place their equipment so that miners weren’t endangered during the project.
“It went very well,” Johnson said. “The concrete thickness was thankfully very easy to ascertain, and they also wanted me to mark any significant changes within the concrete thickness every several feet. So, I just took spray paint and made those markings.”
Johnson never could have imagined that his work with GPRS would take him miles below the earth. He’s had many other memorable days on the job, but he says those few hours he spent in a Pennsylvania mine shaft eight years ago still stick out in his mind.
“I’ve had different work phones throughout the years, but the photos I took from this job are ones that I make sure to transfer to my new phone every time,” Johnson said. “I actually have them saved on my personal phone too, because family members are always asking what I do for a living.
“This is a very good conversation starter.”
Johnson’s story is an example of the limitless potential of GPRS’ services and abilities. It also speaks to some of the incredible experiences GPRS team members have as they work tirelessly to help clients Intelligently Visualize The Built WorldTM.
What can we help you visualize?