industry insights
Featured Articles
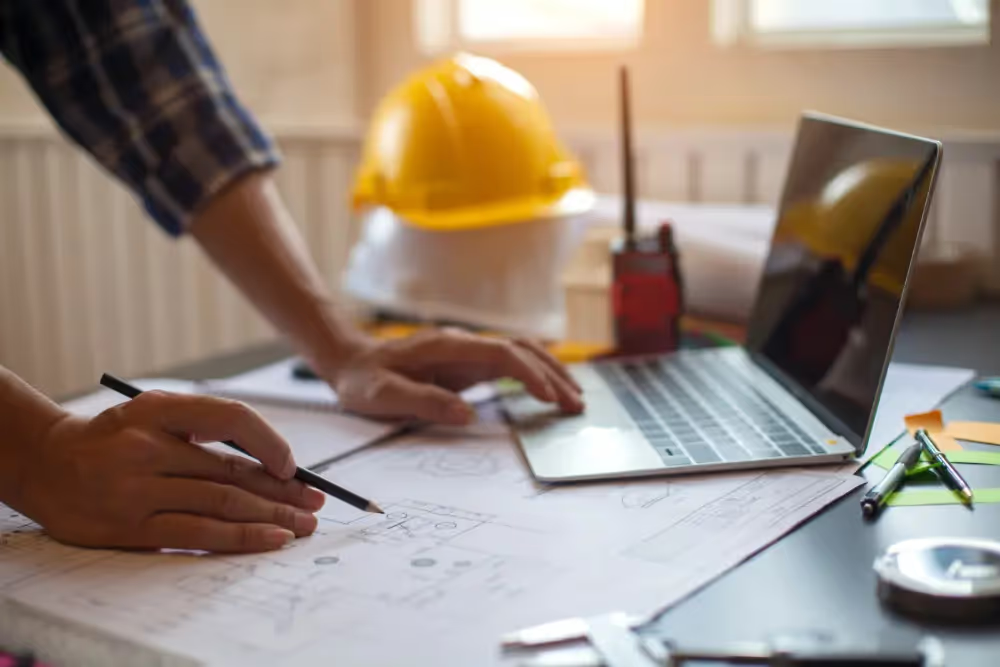
Why Do You Need Updated As-Builts on Your Next Project?
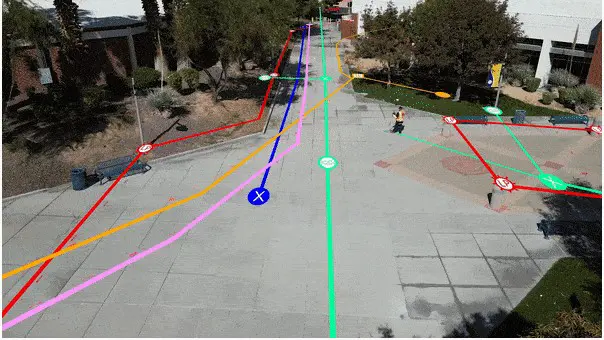
Is Utility Mapping Worth the Cost?
industry insights
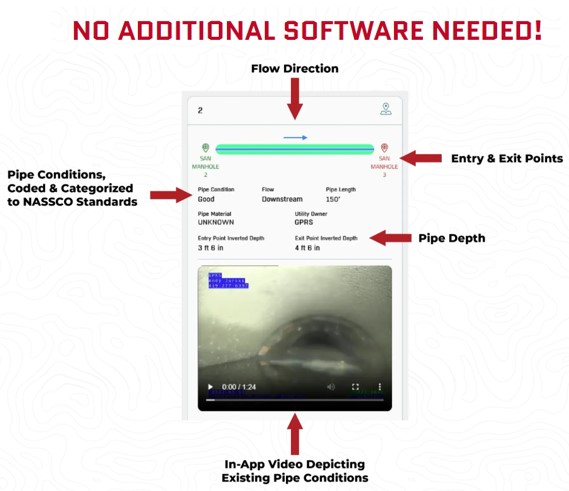
Unlocking Subsurface Clarity: How GPRS’ SiteMap Sewer Layer Shows Facilities Managers Exactly “Where in the World” Their Pipes Are
Facilities managers are all too familiar with the challenges of wastewater systems management. Fortunately, there is a new tool that could take a lot of the stress out of maintaining sanitary and storm sewer lines by allowing you to visualize your subsurface infrastructure from anywhere 24/7. That may sound like science fiction, but it’s now reality thanks to GPRS’ new SiteMap® Sewer Layer.
Accurately locating and managing underground sewer infrastructure traditionally requires a lot of guesswork around incomplete, outdated sanitary or storm sewer as-builts, and expensive, time-consuming, and wasteful potholing as you play a frustrating game of whack-a-mole trying to find the source of a break, blockage, or overflow.
And the worst part is that after all that, you still don’t know the exact location of all your sewer lines, cleanouts, and laterals, let alone any damaging cross bores caused by trenchless technology line installations drilling straight through your sewer system.
That’s why GPRS is pleased to introduce you to the SiteMap Sewer Layer, a transformative solution for facilities and municipal managers. delivering precise, accessible, and actionable sewer mapping data. This innovation enhances everything from daily operational efficiency to risk mitigation, and long-term asset maintenance planning by providing a centralized, single source of truth for sewer systems.
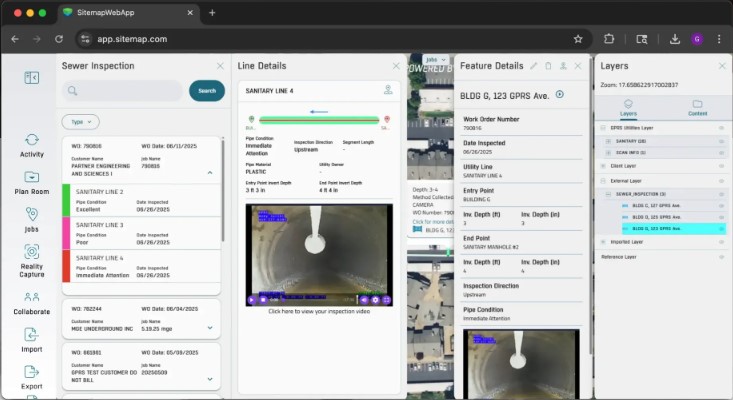
What is the SiteMap Sewer Layer?
The SiteMap Sewer Layer integrates data collected through GPRS’ advanced video pipe inspection technologies, including CCTV robotic crawler cameras and lateral launch “push camera” systems. These tools, used in concert with utility locating technologies like ground penetrating radar (GPR), electromagnetic (EM) locators, tracer wires, and sondes, capture high-resolution imagery and video, enabling detailed condition assessments and precise mapping of sewer lines, lateral connections, and manholes. The resulting data is uploaded to the SiteMap® platform (patent pending), where you can view, analyze, and share it with key team members, subcontractors, and stakeholders in real time.
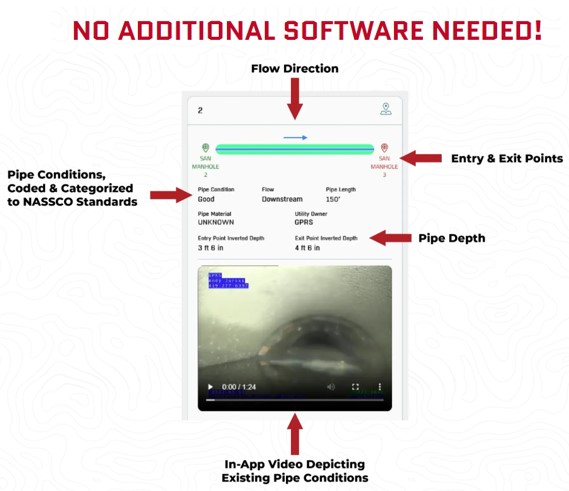
There is no additional software required to see each geolocated pipe segment, the entry & exit points for that segment, pipe material, depth, flow direction, and the condition of the segment, coded and categorized to NASSCO standards. Plus, in-app video depicting your existing pipe conditions, allowing you to proactively plan, maintain, repair and upgrade your sanitary and storm systems to:
• Reduce potholing & destructive excavation
• Reduce utility strikes & service interruptions
• Find damaging cross bores before they compromise your system
Regardless of industry, this new tool is a game-changer. As GPRS Chief Strategy Officer, Jason Schaff said in a recent press release on the subject, “Two of the biggest problems we’ve been trying to tackle for our customers, especially those managing large campuses or municipalities, are how we can give them concrete evidence showing them exactly where in the world their sewer lines are, and what condition they are in, so that they have access to that data in the palm of their hand 24/7.”
“We believe SiteMap’s Sewer Layer update solves both issues; not only can you see direct video of every pipe segment and its condition, each line is geolocated with real-time kinematic positioning (RTK), so you can be certain of the location of every pipe in your wastewater infrastructure. And since it’s all delivered via SiteMap, you have complete access and control of your wastewater system data from anywhere, anytime you need it, to plan upgrades, expansions, and repairs.”
How Does The SiteMap Sewer Layer Help Facilities Managers?
Facilities managers in higher education, health care, manufacturing, municipal wastewater, and virtually every industry could shift to proactive vs. reactive maintenance and repair schedules, provide concrete sewer budget items for capital planning, avoid service interruptions, locate previously unknown sanitary and storm sewer lines, and eliminate construction delays.
University campuses often span hundreds of acres with sewer infrastructure that spans centuries. With SiteMap, operations and facilities managers can identify root intrusions, pipe deformation, or blockages before they escalate into costly emergencies. For example, The University of Toledo now has its entire sanitary and storm sewers, water lines, steam lines, and more, mapped and catalogued in SiteMap for their use.
In manufacturing environments, unplanned downtime due to sewer failures can halt production and compromise safety. SiteMap allows plant engineers to monitor critical sewer lines beneath production floors, loading docks, and chemical storage areas. A Midwest automotive manufacturer leveraged SiteMap to provide a full site scan of its facilities, covering 3,700,000 s.f. and 419 acres while it retooled and renovated.
“One of the biggest issues we were solving [for the auto plant] was scanning and collecting the data proactively ahead of the project rather than waiting until the construction phase. This gave them the subsurface information they needed to design and plan with accurate information that we updated from the out of date and inaccurate as builts.” – Nate Stair, GPRS SiteMap Market Segment Leader & Account Executive
Municipal wastewater departments benefit from SiteMap’s ability to centralize data across multiple sites and teams. With aging infrastructure and limited budgets, municipalities must prioritize repairs based on accurate condition assessments. The City of Fremont, California utilized GPRS’ video pipe inspection & SiteMap to accurately locate and track the remediation of 10 dangerous cross bores caused by directional drilling fiber line installations. The platform’s cloud-based access enabled collaboration between public works, engineering consultants, and contractors, streamlining their repairs.
Municipalities across the U.S. are requiring pre and post-cross bore inspections surrounding fiber line installations to avoid dangerous and costly sewer problems caused by utility line intrusions.
Health care facilities, where sanitation and operational continuity are paramount, gain critical visibility of data with SiteMap.
Hospitals and medical campuses often have complex, undocumented sewer networks. General contractor Rudolph Libbe used SiteMap® to trace sewer lines that were more than 150 years old, and verify the locations of all their subsurface infrastructure prior to building a new central utility plant at Mercy Health’s St. Vincent Medical Center. With precise mapping and video documentation, the facilities team coordinated to locate the CUP much closer to the main hospital than usual. This was only possible with exceptional subsurface as-builts.
What Are The Benefits of SiteMap's Sewer Layer?
Key benefits of the SiteMap Sewer Layer include the ability to:
• Navigate to any individual line, lateral, or feature in your storm or sanitary sewer system
• Access the geolocated, tagged, and annotated video feed of your pipe conditions anytime, anywhere at the touch of a button
• Filter your data based on pipe condition and level of defect
• Securely share any segment of your sewer data with your team, contractors, vendors, and subcontractors to eliminate confusion & miscommunication
• Maintain a permanent record of your sewer data for future planning and proactive maintenance
The bottom line: GPRS’ new SiteMap Sewer Layer gives facilities managers a powerful tool for reducing risk, optimizing maintenance, and extending the life of critical wastewater infrastructure.
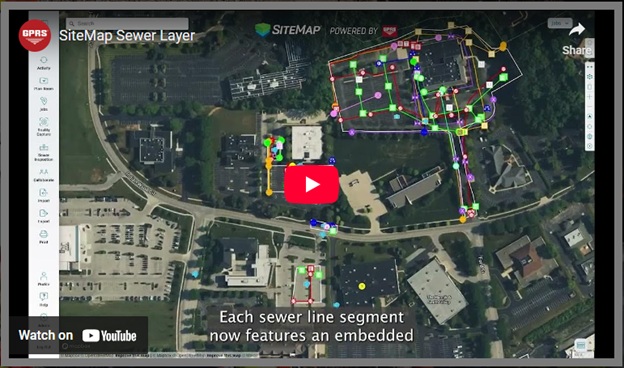
What can we help you visualize? Schedule your personal SiteMap demonstration and view information about the new Sewer Layer, here.
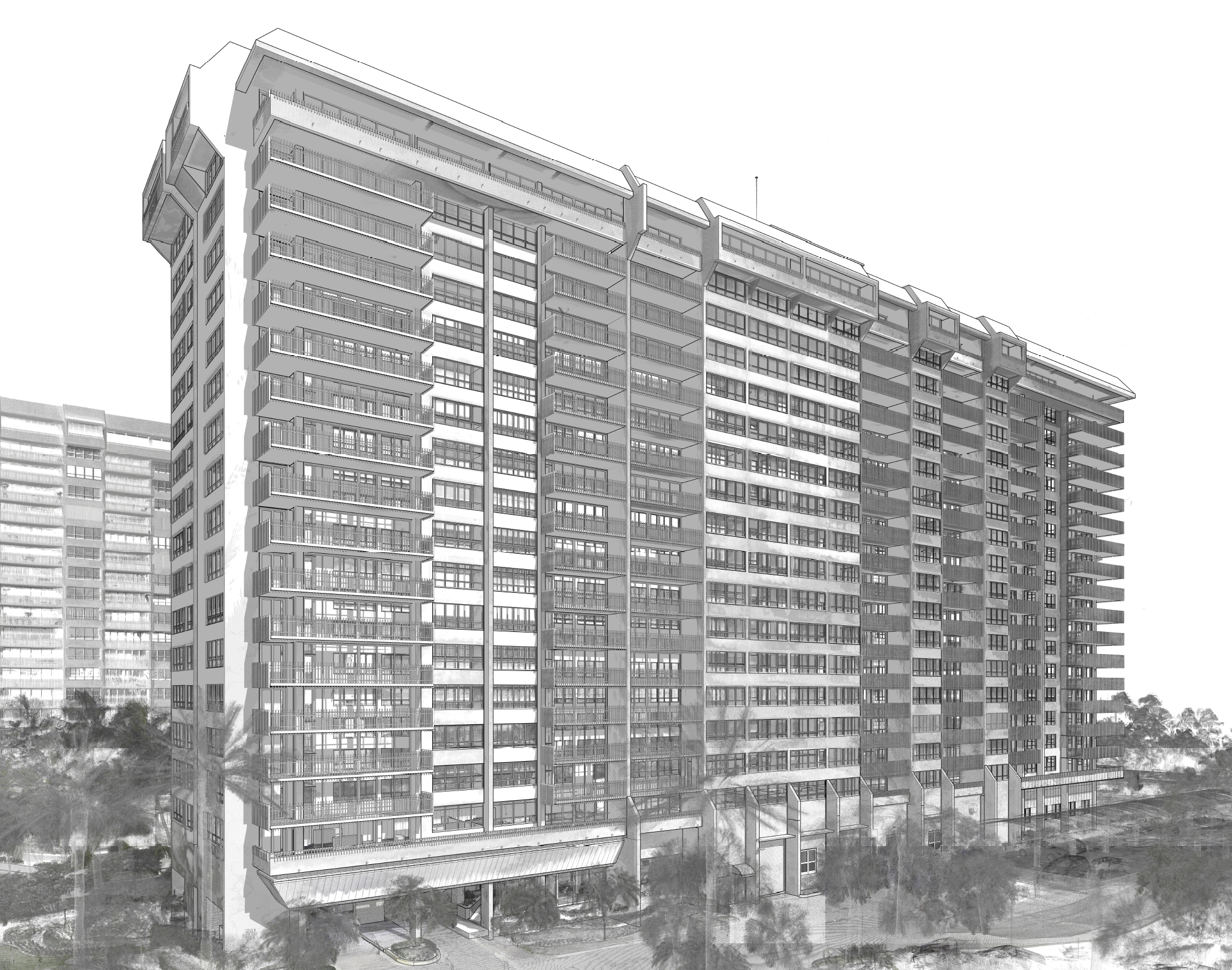
GPRS Reality Capture Services Aid ADA Renovations to Luxury Condos
A decades-old, luxury condominium complex on a man-made island off the southern coast of the United States was set to undergo renovations to bring the buildings into ADA compliance.
The contractor overseeing the project called GPRS to provide reality capture services that ensured their work started accurate and stayed accurate.
Project Manager John Lehaney traveled to the island to conduct 3D laser scans in and around the three existing towers. Our client required accurate floor plans of the first floors, and scans of the exteriors of each of the three buildings to expedite project planning. But data capture needed to be completed without disrupting tenants and while working around the active construction of an additional condo tower on the island.
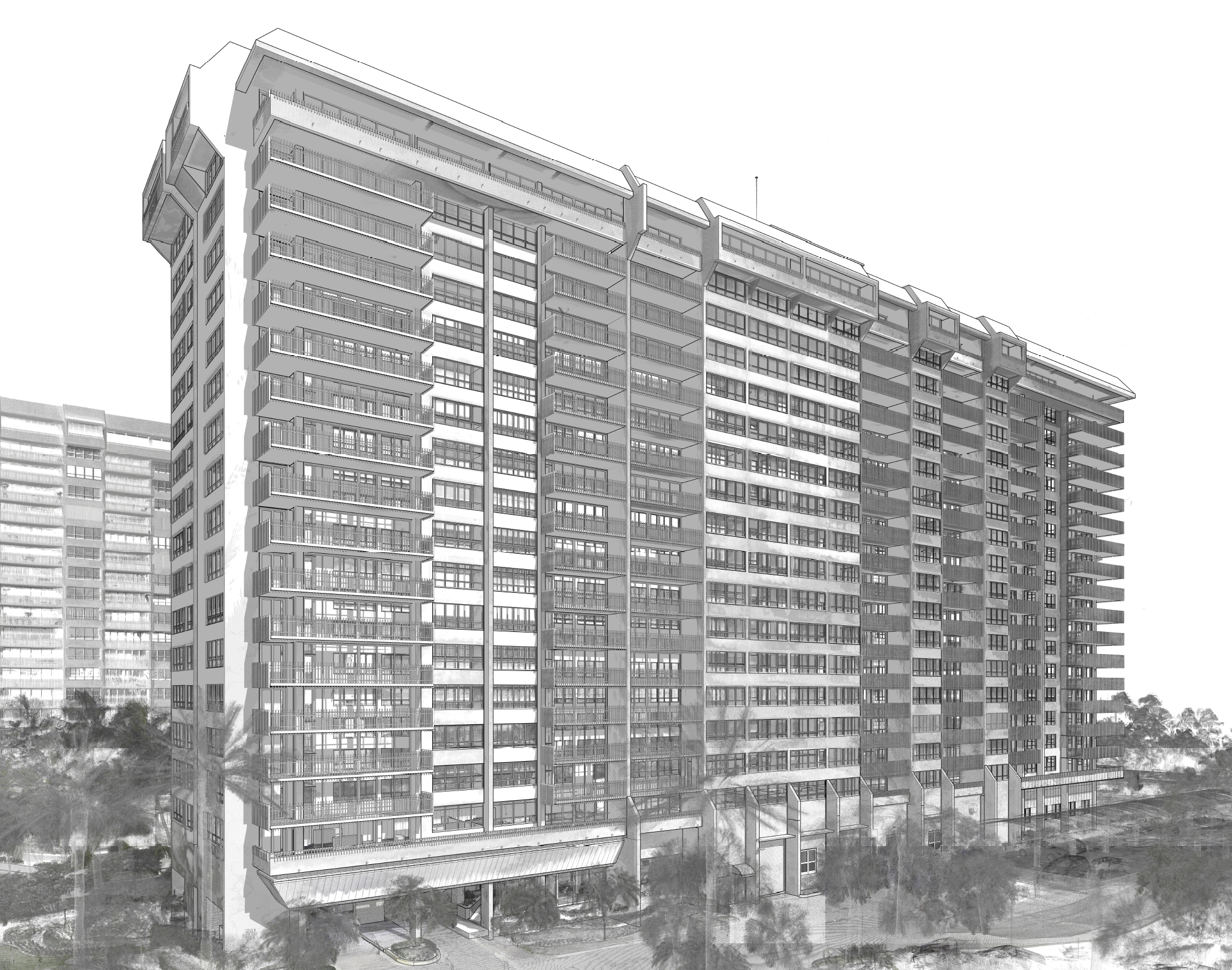
The scope of work also tripled in size as the client came to fully understand what data they required to complete their project.
“It went from being about, I want to say, 9-10,000 s.f. of building [scanning]… to around 30,000 s.f. of building,” Lehaney said. “So, it consisted of the lobby, the carports, community spaces, storage lockers, staff housing, and then one of the buildings, instead of staff housing, [we needed to scan] what was actually a tenant’s condo unit. So, we had to get special access to get in there from security.”
What Does it Mean to be ADA Compliant?
The Americans with Disabilities Act (ADA) is a federal law that prohibits discrimination based on disability and ensures equal access and opportunities for individuals with disabilities in various area, including employment, transportation, public accommodations, and communications
For buildings, ADA compliance means physical accessibility through the inclusion of features like ramps, accessible restrooms, and clear pathways.
How GPRS Helps You Comply with ADA Requirements
GPRS offers reality capture services that can be used to inspect ramps and cross slopes – the angle of a road’s surface perpendicular to the direction of travel, designed to allow water to drain away effectively – to ensure they comply with ADA requirements.
When you need to renovate to achieve compliance, our laser scanners collect the accurate, actionable data that our in-house Mapping & Modeling Team needs to create floor plans, virtual walkthroughs, BIM models, and whatever other deliverables you need to get the job done right.
At the condos, Lehaney deployed the Leica RTC360 and P50 ScanStation to obtain the desired point cloud data.
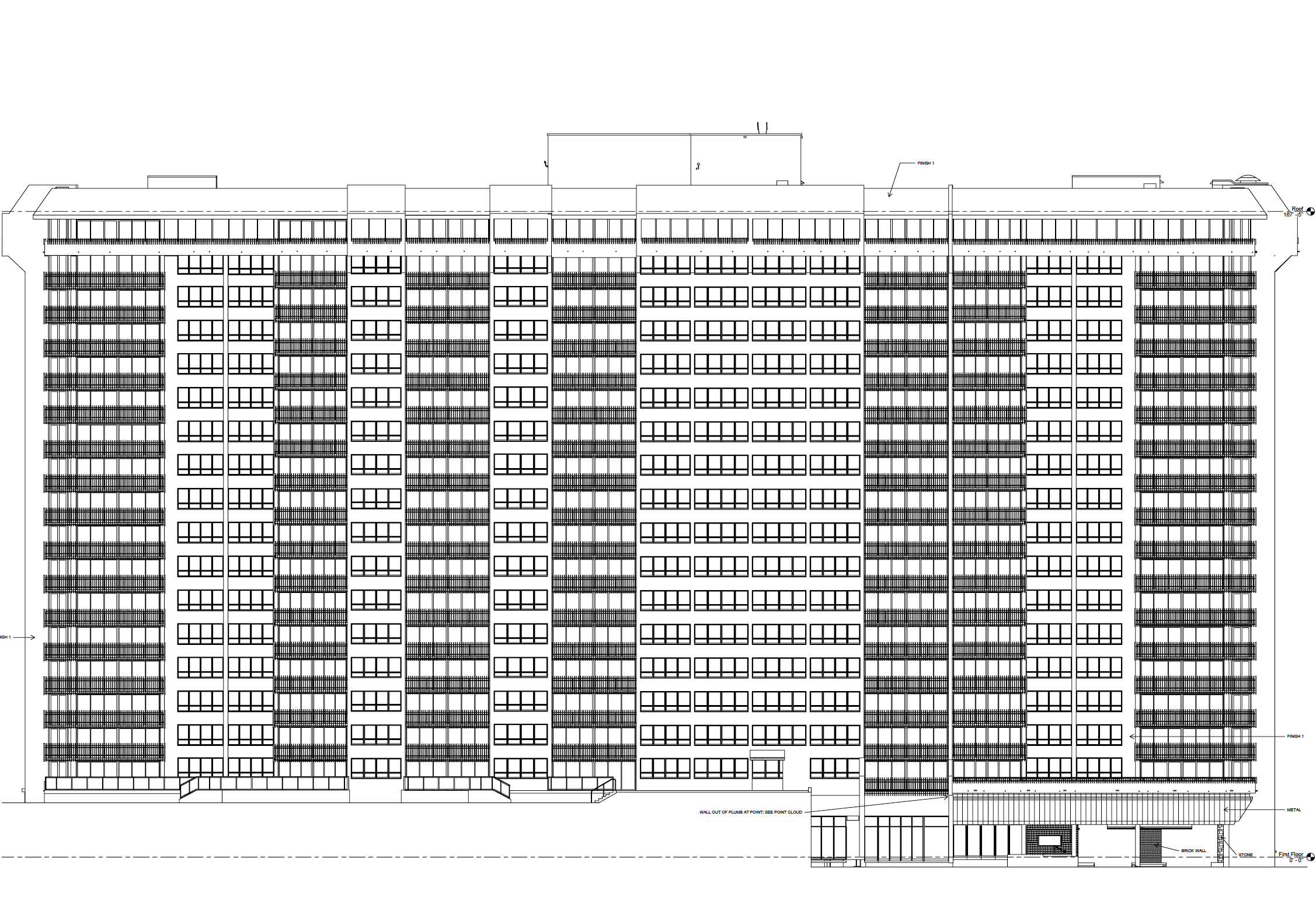
The Leica RTC360 3D laser scanner combines a high-performance laser scanner with Cyclone FIELD 360, a mobile-device app on a tablet computer, to capture and automatically pre-register scans in real time. With a measuring rate of up to 2 million data points per second and advanced HDR imaging system, you can have 3D colorized point clouds with 2-4 mm accuracy in under 2 minutes. Automatic targetless field registration (based on VIS technology) and the seamless transfer of data from site to office reduces time spent in the field, maximizing project productivity.
Leica P-Series ScanStations deliver the highest quality point cloud data and HDR imagery at an extremely fast scan rate of up to 1 million points per second and ranges of more than 1 kilometer. The P-series Leica laser scanners can tie to survey control, achieve 2-4mm accuracy and have real-time liquid filled dual axis compensators to help mitigate movement and ensure level scans. These scanners deliver highly detailed point clouds mapped in realistic clarity.
With this equipment, Lehaney was able to collect the data needed for GPRS’ Mapping & Modeling Team to create the floor plans and other deliverables the client needed to complete their work efficiently, and without the delays and mistakes they would have incurred without accurate as-built information.
“Overall, it was a pretty smooth project,” he said. “[The data] came out nice and clean… It’s just good data for them to have, including the hardscape information outside the building too.”
From condo towers to municipal sewer systems and everything in between, GPRS Intelligently Visualizes The Built World® to keep your projects on time, on budget, and safe.
What can we help you visualize?
Frequently Asked Questions
How do I know if 3D laser scanning or other reality capture services are right for my project?
Almost any project that requires as-built information can benefit from a laser scanning survey. Talk with our experts and start your 3D laser scanning survey project today.
What deliverables can GPRS provide when conducting reality capture services?
We can provide 3D modeling in many formats such as:
- Point Cloud Data (Raw Data)
- 2D CAD Drawings
- 3D Non-Intelligent Models
- 3D BIM Models
- JetStream Viewer
Customizable Deliverables Upon Request
- Aerial Photogrammetry
- Comparative Analysis
- Deformation Analysis
- Digital Drawings of GPR Markings
- Floor Flatness Analysis/Contour Mapping
- New Construction Accuracy Analysis/Comparative Analysis
- Point Cloud Modeling Training Webinars
- Reconciliation of Clients 2D Design Drawings
- Reconciliation of Clients 3D Design Model
- Structural Steel Shape Probability Analysis
- Template Modeling
- Volume Calculations
- Wall Plumb Analysis
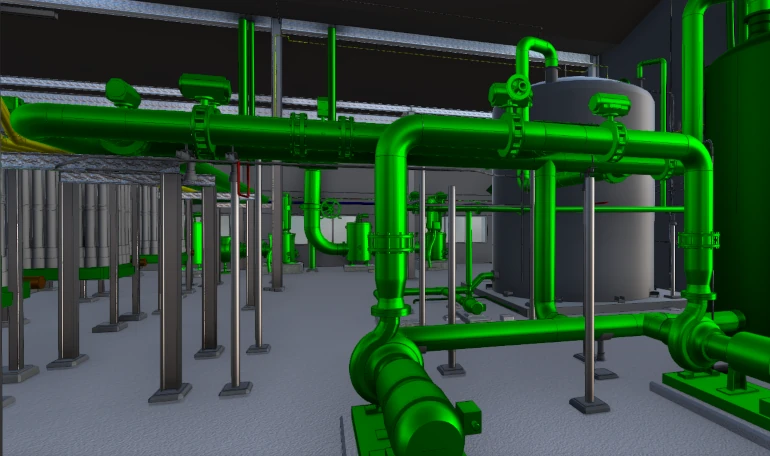
How Does 3D Laser Scanning Aid MEP Design and Layout?
For an engineer managing MEP design and execution, precision and coordination are imperative. Successful design, fabrication, and installation depend on the knowledge of existing site conditions, and reality capture via 3D laser scanning delivers just that.
With a single 3D laser scan, millions of site dimensions are captured in a point cloud, providing the data needed to create accurate 3D BIM models. BIM models allow MEP engineers to design HVAC layouts, plan electrical runs, and route plumbing systems with confidence. Plus, they help to avoid clashes, improve spatial planning, and streamline installation.
Scan-to-BIM workflows reduce human error, enhance coordination across trades, and save time during prefabrication and field installation. With advanced features like clash detection and construction sequencing, BIM technology helps MEP engineers visualize complex systems and streamline execution.
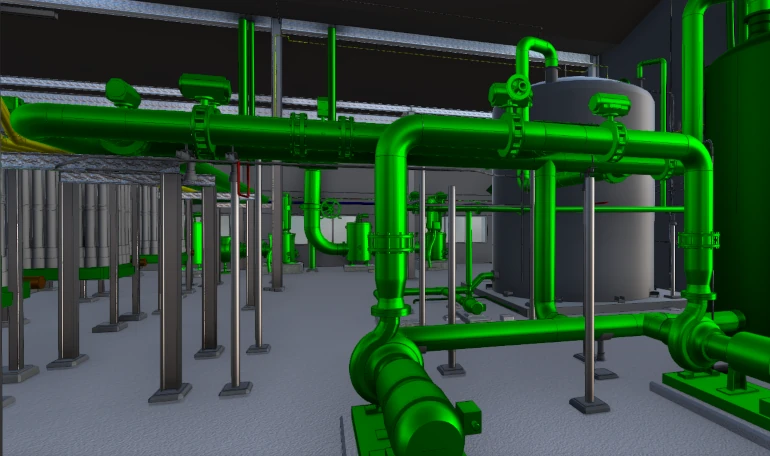
How Does 3D Laser Scanning Benefit Mechanical Contractors?
3D laser scanning delivers precise data that helps mechanical contractors improve planning, fabrication, and installation. Here’s how 3D laser scanning helps:
- Digitally capture exact MEP dimensions, layouts, and locations to minimize rework
- Reduce time spent in hazardous, hard-to-reach areas, or clean rooms
- Use BIM models to route efficient paths for HVAC, piping, and mechanical systems
- Overlay data with design models to identify clashes between mechanical systems before installation
- Prefabricate ductwork and piping assemblies with precision
What are the Benefits of 3D Laser Scanning for Electrical Contractors?
3D laser scanning offers electrical contractors a smarter, faster way to plan and execute installations with precision. 3D laser scan technology can:
- Capture exact locations of panels, conduits, junction boxes, and cable trays
- Minimize time spent in hazardous areas by capturing site data quickly
- Overlay laser scan data to build precise electrical design models
- Detect clashes between electrical systems and other trades before installation
- Plan conduit and wiring paths for maximum efficiency
- Speed up large installs with better coordination and data-driven decisions
How Does 3D Laser Scanning Help Plumbing Contractors?
3D laser scanning and BIM provide the precise data plumbing contractors need to plan efficiently, install faster, and avoid costly errors. 3D laser scanning & BIM services can:
- Capture pipe dimensions, slopes, and connections to eliminate guesswork and reduce field errors
- Visualize plumbing systems in relation to structural and MEP elements to prevent clashes and plan optimal routing
- Prefabricate assemblies with confidence in fit and alignment, minimizing rework and material waste
- Coordinate installation steps across teams to avoid delays and ensure systems are installed to spec
Case Study Example: 3D BIM Model Aids Wastewater Treatment Plant Heat Exchanger Upgrades
Faced with dense mechanical and piping systems, ABC Piping Co. turned to GPRS to 3D laser scan the Southerly Wastewater Treatment Plant and create an LOD 300 BIM model of its complex heat exchanger system. The model delivered accurate pipe sizes, routing, and spatial layout, enabling precise MEP design updates without guesswork or costly rework.
“We are delivering an architectural/structural 3D BIM model and MEP 3D BIM model for design and engineering, providing a 3D space for all disciplines to work together to identify and resolve clashes before system integration begins, ensuring a smooth retrofit with minimal rework,” Belinda Thompson, GPRS CAD Technician stated.
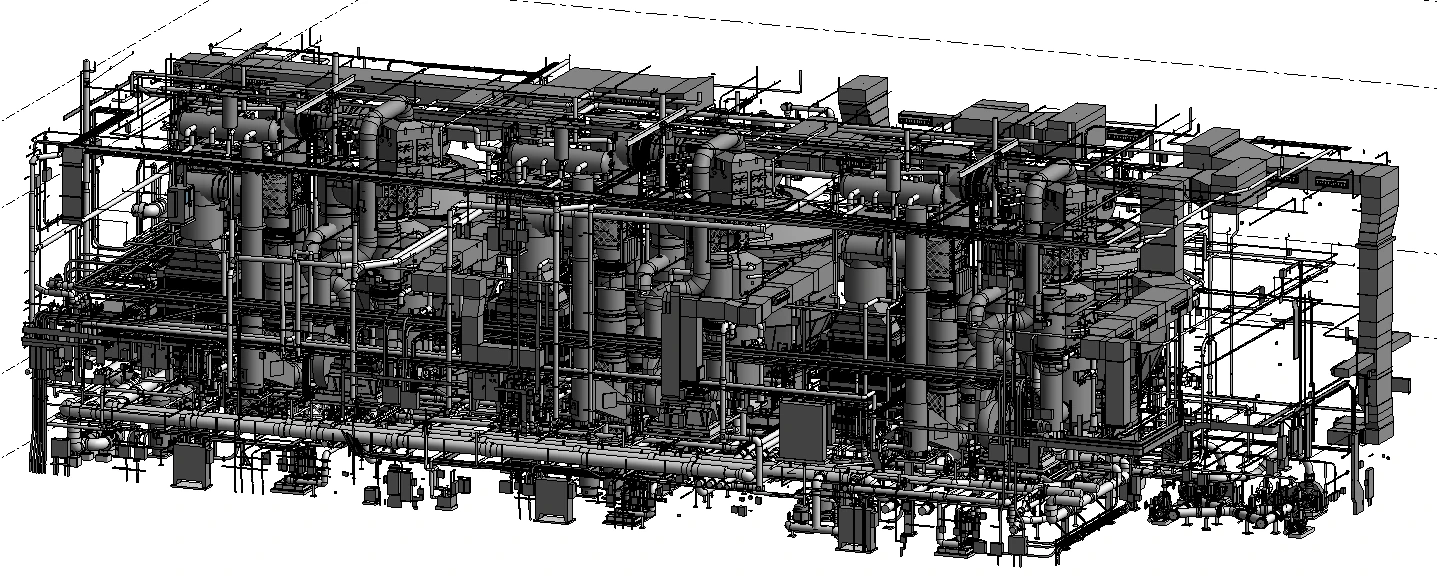
How Does a 3D Laser Scanner Work?
The primary way a laser scanner works is to send light pulses at high speed which reflect off objects and return to the scanner’s sensor, known as LiDAR technology. For each pulse, the distance between the scanner and object is measured by determining the elapsed time between the sent and received pulses. Each data point is converted to a pixel with a known x, y, and z coordinate for accurate reality capture.
Laser scans are taken in multiple positions around a site from varying viewpoints. Millions of data points are captured and processed into a point cloud, creating an accurate 3D as built data set of the site. This all happens very quickly, with some scanners, like the Leica RTC360, capturing and calculating 2 million points per second with 2-4 mm accuracy.
What is Scan-to-BIM?
Scan to BIM is the process of digitally capturing a site with a 3D laser scanner and using the data to create a BIM model. BIM models provide a comprehensive view of a building that can be used throughout its lifecycle – during the design phase, construction phase, and operation phase of the building.
Scan to BIM gives MEP contractors highly accurate, field-verified models that streamline design, eliminate clashes, and ensure systems fit perfectly before installation begins.
Why Choose GPRS for 3D Laser Scanning?
GPRS is the trusted leader in 3D laser scanning and BIM modeling, helping you to design and install MEP systems with precision. Our laser scanning delivers millimeter-accurate site data, capturing the exact layout, dimensions, and locations of existing system elements. This data is expertly converted into custom 2D CAD drawings and 3D BIM models that enable precise engineering, prefabrication, and fit-out. This ensures that MEP system updates are designed to fit precisely within the existing space, reduces errors and rework, and delivers superior results for your project.
Through SiteMap® (patent pending), our cloud-based GIS software platform, clients gain secure, 24/7 access to their drawings, models, and deliverables, all in one place. With GPRS, you get MEP clarity from day one and confidence throughout your build. Every GPRS customer receives complimentary Personal Level SiteMap access as part of our services.
What can we help you visualize?
Frequently Asked Questions
How does 3D laser scanning improve accuracy in MEP design?
It captures millions of precise measurements of existing site conditions, creating a reliable foundation for BIM models that help engineers design systems with confidence and avoid costly errors.
What role does scan-to-BIM play in coordinating MEP systems?
Scan-to-BIM workflows allow teams to visualize spatial relationships, detect clashes early, and plan installations that integrate seamlessly with other building components.
Can 3D laser scanning help with prefabrication and installation?
Yes, by providing exact dimensions and layouts, it enables off-site fabrication of MEP components that fit perfectly on-site, reducing rework and speeding up installation.
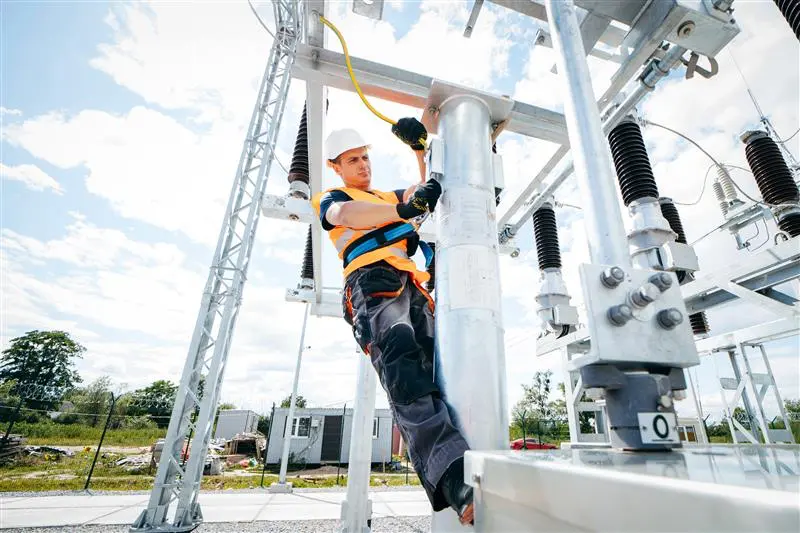
What is a Grounding Grid?
Often hidden beneath power substations, industrial facilities, and large electrical installations, grounding grids play a vital role in protecting equipment, infrastructure, and – most importantly – human life.
A grounding grid is a network of interconnected conductors, typically made of copper or galvanized steel, buried in the earth to provide a low-resistance path for electrical currents to safely dissipate into the ground. These grids are designed to handle fault currents, lightning strikes, and other transient over voltages by directing them away from equipment and personnel.
Grounding grids form the foundation of an effective grounding – also known as earthing – system, which is essential for maintaining voltage stability and ensuring the safe operation of electrical equipment. They are most commonly found in:
- Electrical substations
- Power generation plants
- Industrial facilities
- Data centers
- Telecommunications hubs
- Wind and solar farms
- Hospitals
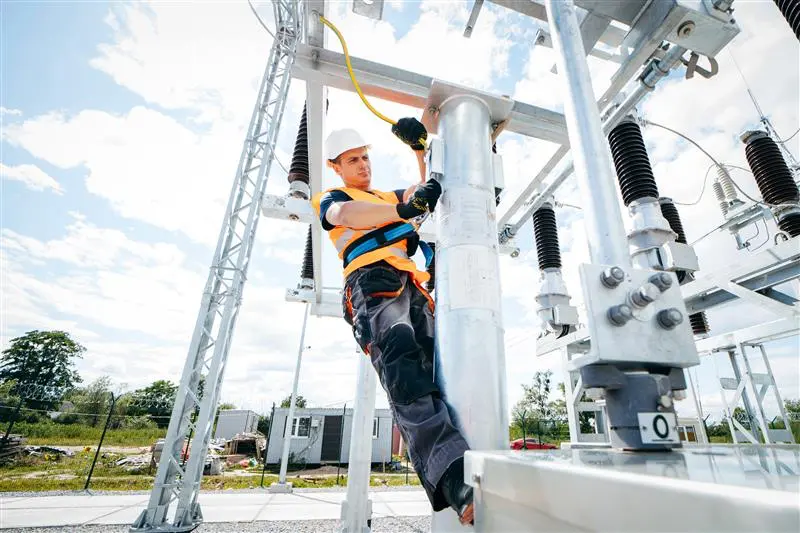
Why Grounding Is Necessary
Grounding serves several critical purposes:
Personnel Safety
In the event of a fault – a failure in the electrical system caused by incidents such as outages or lightning strikes – grounding ensures that dangerous voltages do not persist on exposed conductive parts. This minimizes the risk of electric shock.
Equipment Protection
Sensitive electrical and electronic equipment can be damaged by transient voltages. A grounding grid helps divert these surges safely into the earth.
System Stability
Grounding provides a reference point for system voltages, which is essential for the proper operation of protective relays and circuit breakers.
Lightning Protection
Grounding grids help dissipate the high-energy currents from lightning strikes, reducing the risk of fire or equipment failure.
Components of a Grounding Grid
A typical grounding grid consists of the following elements:
- Horizontal Conductors: These are laid out in a grid pattern (e.g., square or rectangular) and buried at a shallow depth, usually one to two feet below the surface
- Vertical Ground Rods: Driven deeper into the earth to improve the overall grounding resistance, especially in areas with high soil resistivity
- Grounding Electrodes: These may include rods, plates, or rings that enhance the contact area with the soil
- Connections to Equipment: All metallic parts of electrical equipment, enclosures, and structures are bonded to the grid
The design of the grid is influenced by factors such as soil resistivity, fault current magnitude, and the physical layout of the facility.
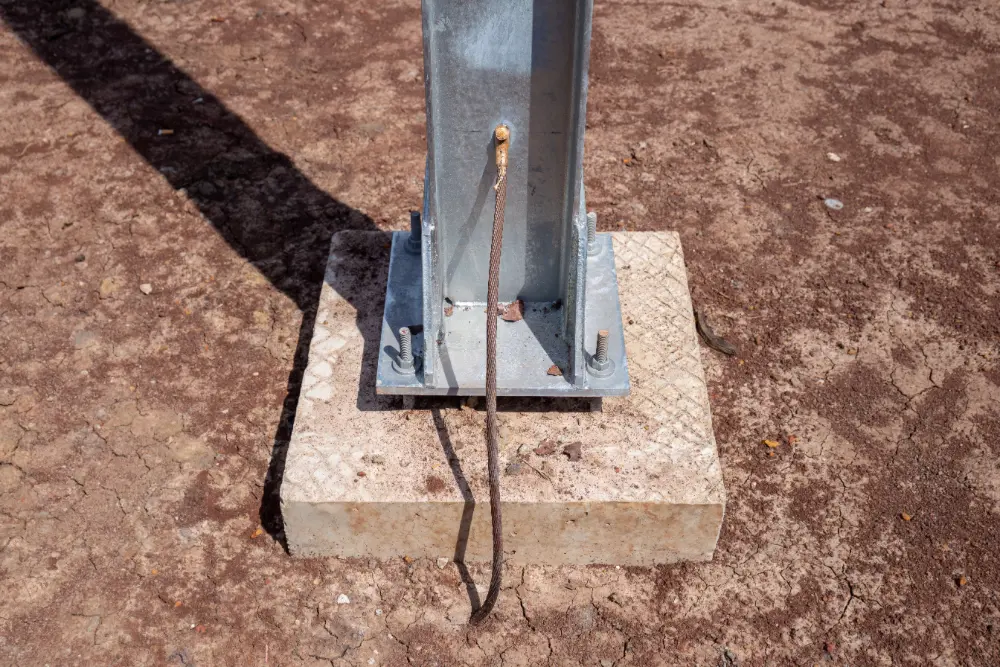
How Grounding Grids Work
When a fault occurs – say, a lightning strike hits a transmission line, or a transformer develops an internal short – the resulting surge of electrical energy must be safely dissipated. The grounding grid provides a low-impedance path for this current to flow into the earth.
Here’s how the process works:
- Current Injection: The fault current enters the grounding grid through the connected equipment or structure.
- Current Distribution: The grid distributes the current across its network of conductors, minimizing localized heating and voltage rise.
- Dissipation into Earth: The current flows from the grid into the surrounding soil, where it is absorbed and neutralized.
The effectiveness of this process depends on the resistance to ground, which is influenced by soil type, moisture content, temperature, and the geometry of the grid.
Key Design Considerations
Designing a grounding grid is a complex engineering task that must balance safety, performance, and cost. Key considerations include:
Soil Resistivity
Soil resistivity is a measure of how easily electrical current can pass through the ground. It varies with soil composition, moisture, and temperature. Engineers often conduct a soil resistivity survey using the Wenner or Schlumberger method to inform the grid design.
Grid Geometry
The layout of the grid – spacing between conductors, depth of burial, and number of ground rods – affects its resistance and current distribution. A denser grid with more conductors generally offers better performance.
Touch and Step Voltage
These are critical safety parameters:
- Touch Voltage: The potential difference between a grounded object and the feet of a person touching it
- Step Voltage: The voltage difference between two points on the ground a step apart
The grid must be designed to keep these voltages within safe limits during fault conditions.
Corrosion Resistance
Materials used in grounding grids must withstand corrosion over time. Copper is preferred for its conductivity and durability, but galvanized steel is often used for cost reasons.
Testing and Maintenance
Even the best-designed grounding grid can degrade over time due to corrosion, soil movement, or construction activities. Regular testing is essential to ensure continued performance. Common tests include:
- Fall-of-Potential Test: Measures the resistance between the grid and remote earth
- Clamp-on Ground Resistance Test: A non-intrusive method for measuring resistance in multi-grounded systems
- Soil Resistivity Testing: Periodically reassessing soil conditions to detect changes that may affect grounding performance
Maintenance may involve replacing corroded conductors, improving soil conductivity (e.g., with bentonite or conductive concrete), or expanding the grid.
How GPRS Helps Protect Grounding Grids During Excavation
Grounding grids are an indispensable element of power infrastructure, providing a vital layer of protection against electrical hazards. By accurately locating and mapping these systems before excavating or trenching near them, we can mitigate risks, protect personnel and equipment, and ensure the continued reliability and resilience of our electrical networks.
GPRS offers 99.8%+ accurate utility locating services designed to mitigate the risk of subsurface damage by providing you with the information you need to break ground safely. Using ground penetrating radar (GPR) scanners and electromagnetic (EM) locating, our SIM-certified Project Managers create comprehensive infrastructure maps to keep you on time, on budget, and safe.
What can we help you visualize? Click below to schedule a service or request a quote today!
Frequently Asked Questions
What does GPRS give me when I hire them to conduct a utility locate?
Our Project Managers flag and paint our findings directly on the surface. This method of communication is the most accurate form of marking when excavation is expected to commence within a few days of service.
GPRS also uses Real-Time Kinematic (RTK) Positioning to collect data points of findings. We use this data to generate a plan, KMZ file, satellite overlay, or CAD file to permanently preserve results for future use.
GPRS does not provide land surveying services. If you need land surveying services, please contact a professional land surveyor.
Please contact us to discuss the pricing and marking options your project may require.
Can GPR scanning locate PVC piping and other non-conductive utilities?
GPR scanning is exceptionally effective at locating all types of subsurface materials. There are times when PVC pipes do not provide an adequate signal to ground penetrating radar equipment and can’t be properly located by traditional methods. This is why GPRS Project Managers are expertly trained at multiple methods of utility locating, including utilizing electromagnetic (EM) locating, to complement GPR scanning.
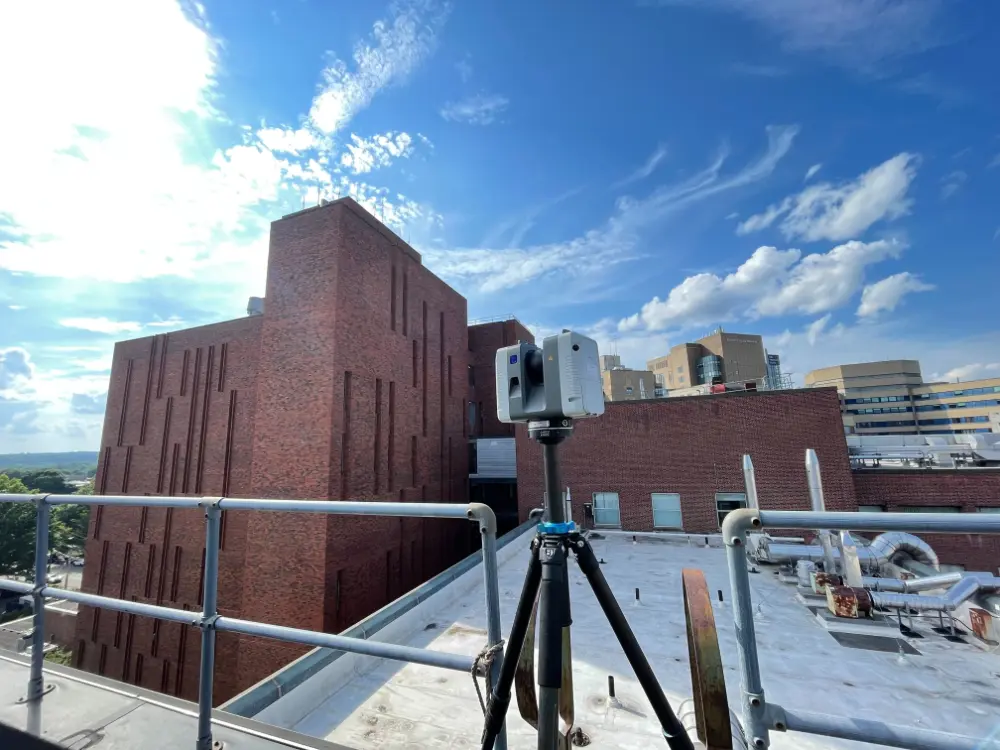
GPRS Reality Capture Services Help University Renovate Medical Research Facility
When one of America’s most prestigious universities was planning to renovate their advanced medical research facility, they relied on reality capture data and deliverables from GPRS to help them start accurate and stay accurate.
A team of GPRS Project Managers 3D laser scanned every inch of the six-story building, including the exterior façade, to capture the accurate existing conditions documentation the university required.
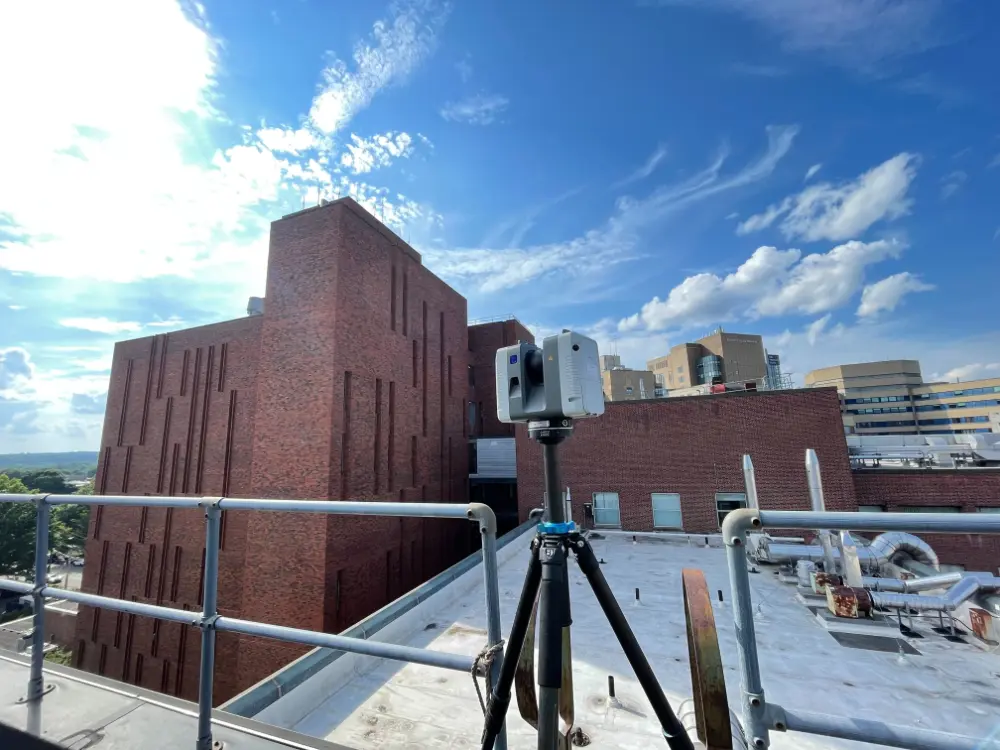
Accurate, real-time as-built data is essential for informed decision-making and seamless collaboration. With precise design plans from the start, architects, contractors, engineers, and facility managers can streamline fieldwork and minimize change orders, plus avoid delays and extra costs.
GPRS Reality Capture Services provide clients with precise as-built documentation of buildings and infrastructure using advanced Leica laser scanners, delivering point clouds, 2D CAD drawings, and 3D BIM models to streamline project planning and construction.
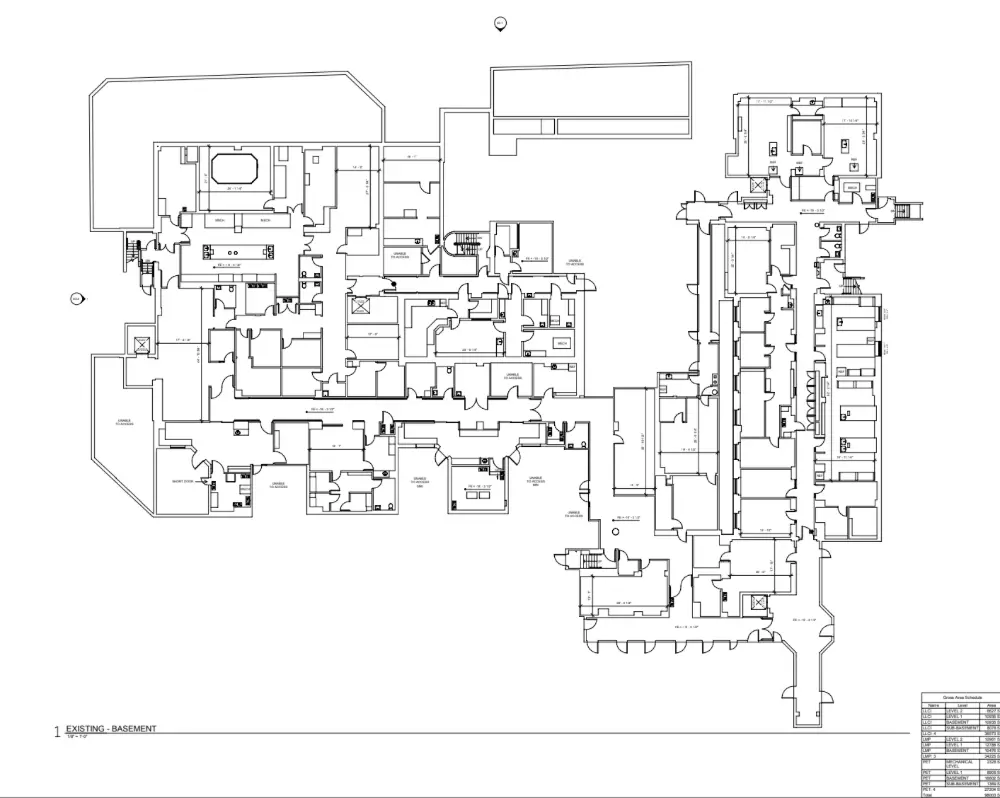
At the university, the GPRS team had to conduct its scans after hours, so as not to disrupt the research being conducted in the facility and so that medical equipment such as MRI machines could be turned off and not interfere with the 3D laser scanning equipment.
“They wanted us in there with as few people as possible, so we’re not disturbing anything,” said GPRS Sales Development Representative John Lehaney, who was a Project Manager on the assignment. “Essentially, we were in there to document everything in sight that they were looking to renovate. They had no existing floor plans.”
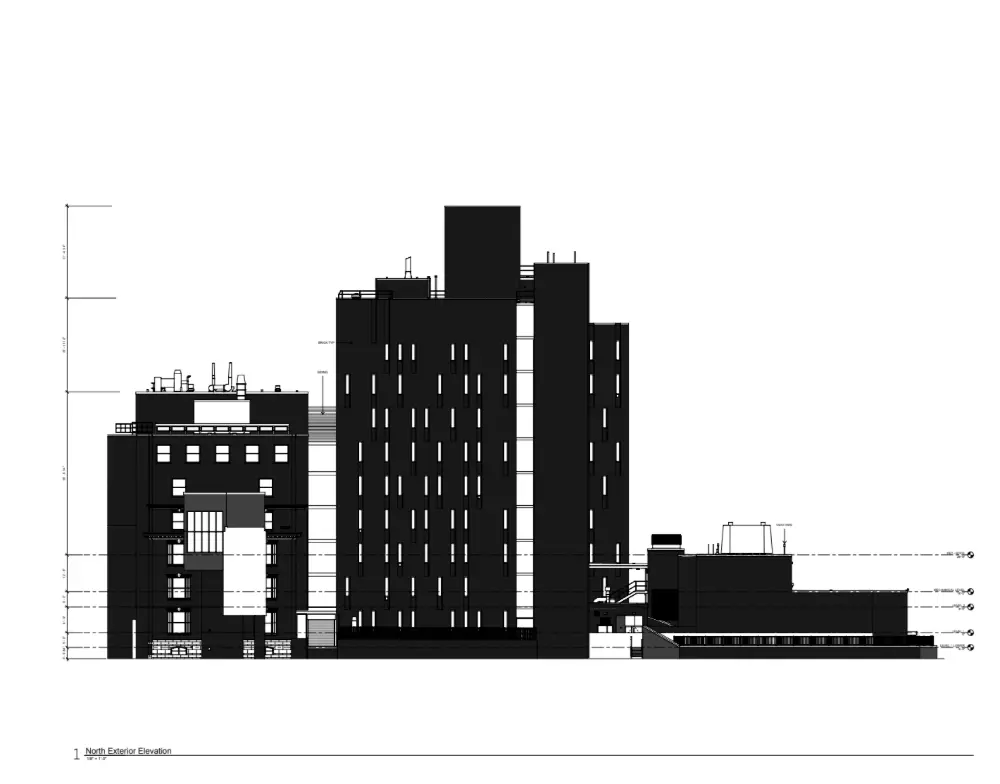
GPRS deployed the Leica RTC360, and NavVis VLX 3D laser scanners to capture 2-4 mm accurate data of the research facility.
The Leica RTC360 3D laser scanner combines a high-performance laser scanner with Cyclone FIELD 360, a mobile-device app on a tablet computer, to capture and automatically pre-register scans in real time. With a measuring rate of up to 2 million data points per second and advanced HDR imaging system, you can have 3D colorized point clouds with 2-6 mm accuracy in under 2 minutes. Automatic targetless field registration (based on VIS technology) and the seamless transfer of data from site to office reduces time spent in the field, maximizing project productivity.
The NavVis VLX captures survey-grade point clouds with two multi-layer LiDAR sensors equipped with SLAM (simultaneous localization and mapping) technology. Four cameras are positioned on top of the device, taking high resolution images in every direction for complete 360º capture – all without the operator appearing in the field of view.
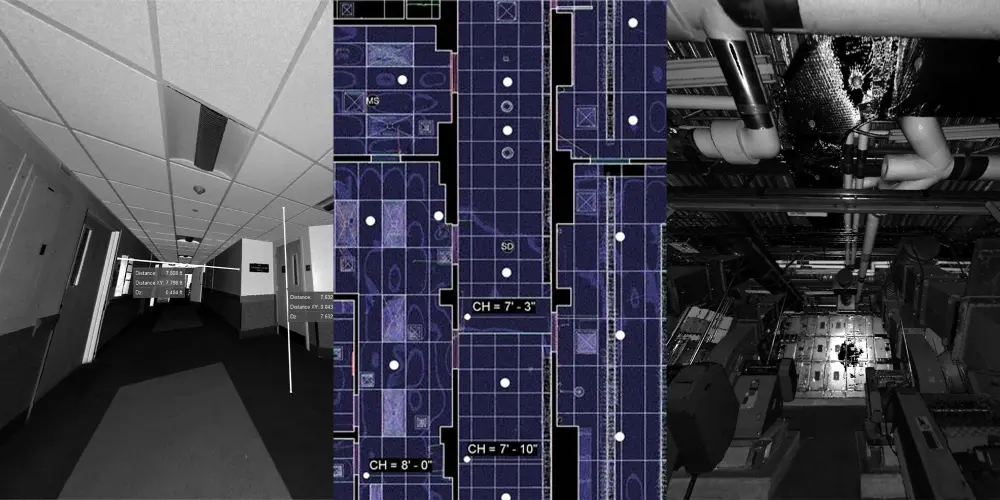
With the RTC360 and NavVis, Lehaney and his fellow Project Managers were able to collect the data needed for GPRS’ in-house Mapping & Modeling Team to create a 3D Revit model, floor plans, a roof plan, a TruView Virtual Site Visit, exterior elevations, and reflected ceiling plans (RCPs) to assist the university in accurate design and planning for their renovations.
The university had the accurate data they needed, and it was obtained without disrupting the vital research being conducted in the facility.
From visualizing school campuses to locating buried utilities and beyond, GPRS Intelligently Visualizes The Built World® to keep your projects on time, on budget, and safe.
What can we help you visualize?
Frequently Asked Questions
How do I know if 3D laser scanning is right for my project?
Almost any project that requires as-built information can benefit from a laser scanning survey. Talk with our experts and start your 3D laser scanning survey project today.
What deliverables can GPRS provide?
We can provide 3D modeling in many formats such as:
- Point Cloud Data (Raw Data)
- 2D CAD Drawings
- 3D Non-Intelligent Models
- 3D BIM Models
- JetStream Viewer
Customizable Deliverables Upon Request
- Aerial Photogrammetry
- Comparative Analysis
- Deformation Analysis
- Digital Drawings of GPR Markings
- Floor Flatness Analysis/Contour Mapping
- New Construction Accuracy Analysis/Comparative Analysis
- Point Cloud Modeling Training Webinars
- Reconciliation of Clients 2D Design Drawings
- Reconciliation of Clients 3D Design Model
- Structural Steel Shape Probability Analysis
- Template Modeling
- Volume Calculations
- Wall Plumb Analysis
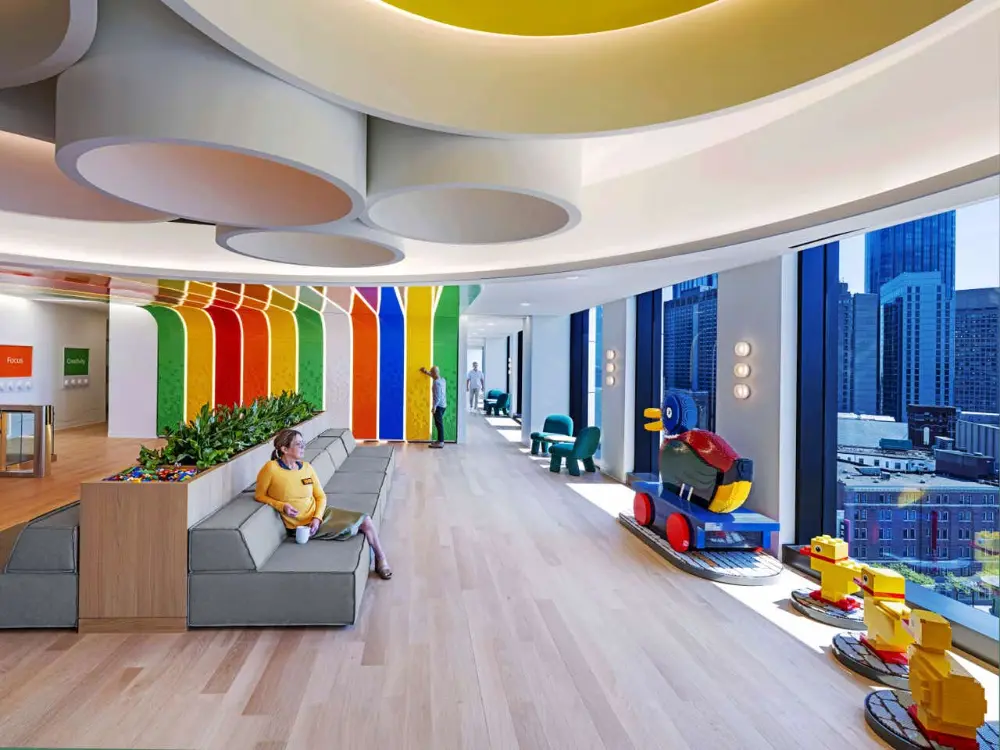
World’s Largest Toy Company Increasing Investment in U.S. Operations
The LEGO Group’s new, 157,000 s.f. U.S. Hub in Boston, Massachusetts is just the latest example of the world’s largest toy company’s increasing its investment in its North American operations.
According to a press release on the LEGO Group’s website, “the new state-of-the-art office will be the company’s new U.S. Hub and support its ongoing commitment to reaching more children across the U.S. with LEGO® play.”
The opening of the Danish toymaker’s new U.S. headquarters signals the beginning of the end for its former Connecticut headquarters, which the company has occupied for more than 50 years.
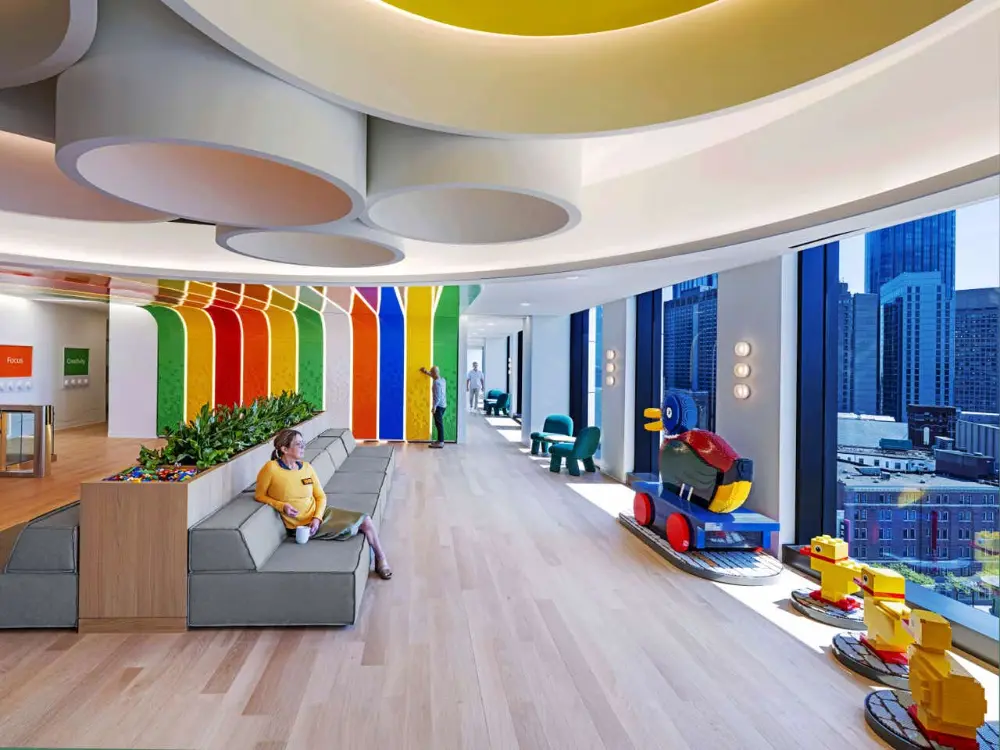
"This fantastic new LEGO® workspace is an important part of our US investment strategy, fast becoming a talent magnet in this important market,” said LEGO Group CEO Niels B. Christiansen. “The Boston Hub will open up new ways for LEGO colleagues to create, connect, and grow as we continue our mission to inspire and develop the builders of tomorrow across the US.”
The LEGO Group’s new HQ is LEED Gold and WELL Gold certified and features over 660 workstations, complimentary gym access, parents’ rooms and flexible wellness areas for employees to engage in activities like medication, prayer and relaxation, playful common spaces, sky terraces, and over 90 meeting spaces.
Over 800 employees will work out of the six-floor office, which was built by Structure Tone and designed by BDG, and is situated in the Lyrik, a 20-story office building completed last year.
Ryan Megenedy, senior account executive at Structure Tone, acknowledged in an interview with Engineering News-Record that building a space for a company like the LEGO Group “required a lot of creativity.”
“Many elements of the design echo the ‘studs’ on the iconic LEGO brick, which means we were working with a lot of curves and radiuses,” Megenedy explained in an email to ENR. “We also built four central staircases across five floors that enabled us to incorporate lots of fun and playful LEGO models throughout the space. We’re incredibly proud of how it turned out.”
In addition to its new U.S. headquarters, the LEGO Group is also opening a 2,000,000 s.f. regional distribution center (RDC) in Prince George, Virginia, which will support a future factory in Greater Richmond. Both facilities are currently under construction and expected to open in 2027.
In a press release announcing those projects, the LEGO Group said they are part of the company’s global supply strategy to locate factories and distribution centers close to major markets and ensure capacity to support future growth in the region.
The RDC will be the second in the company’s Americas network, joining an existing center in Fort Worth, Texas. It will be operated by a third-party logistics partner, creating 305 jobs. The factory will create more than 1,700 jobs with the LEGO Group once fully operational.
“The regional distribution center will bring greater flexibility to our network, ensuring we are well positioned to support long-term growth in the Americas,” said Carsten Rasmussen, Chief Operations Office of the LEGO Group. “Together with our future Virginia factory, the RDC will shorten our supply chain in the region – reducing lead times for our customers as well as our environmental impact. We are grateful for the continued support from the Commonwealth of Virginia.”
Whether you’re building a 2,000,000 s.f. distribution center, a multi-story office space, or a skyscraper, GPRS can support your construction project through our comprehensive suite of subsurface damage prevention, existing conditions documentation, and construction & facilities project management services. We offer precision concrete scanning and utility locating, pinpoint-accurate leak detection, NASSCO-certified sewer line inspections, 2-4mm accurate 3D laser scanning, and in-house mapping & modeling tailored to your project’s specific needs.
All this accurate, actionable data is at your fingertips 24/7 thanks to SiteMap® (patent pending), GPRS’ project & facility management application that provides accurate existing conditions documentation to protect your assets and people.
From skyscrapers to sewer lines, GPRS Intelligently Visualizes The Built World® to help keep you on time, on budget, and safe.
What can we help you visualize?
Frequently Asked Questions
Will I need to mark out the utilities that GPRS locates?
GPRS will locate and mark all utilities for you. We have a variety of tools and markers we can use to highlight the locations of utilities, underground storage tanks and whatever else may be hiding.
What is the difference between a design intent and as-built model?
DESIGN INTENT – deliverables will be shown as a "best fit" to the point cloud working within customary standards, such as walls being modeled 90 degrees perpendicular to the floor, pipes and conduit modeled straight, floors and ceilings modeled horizontal, and steel members modeled straight. This will produce cleaner 2D drawings and will allow for easier dimensioning of the scan area. The deliverables will not exactly follow the scan data to maintain design intent standards. Most clients will want this option for their deliverables.
AS-BUILTS – deliverables will be shown as close as possible to actual field capture. If walls are out of plumb, pipes and conduit show sag, floors and ceilings are unlevel, steel members show camber, etc., this will be reflected in the model. This will produce reality-capture deliverables, but 2D drawings may show “crooked” or out of plumb lines, floors will be sloped or contoured, steel members may show camber, twisting or impact damage. Dimensioning will not be as easy due being out of plumbness/levelness, etc. This option should be used when the exact conditions of the scan area is imperative. Clients using the data for fabrication, forensic analysis, bolt hole patterns, camber/sag/deformation analysis, and similar needs would require this option.
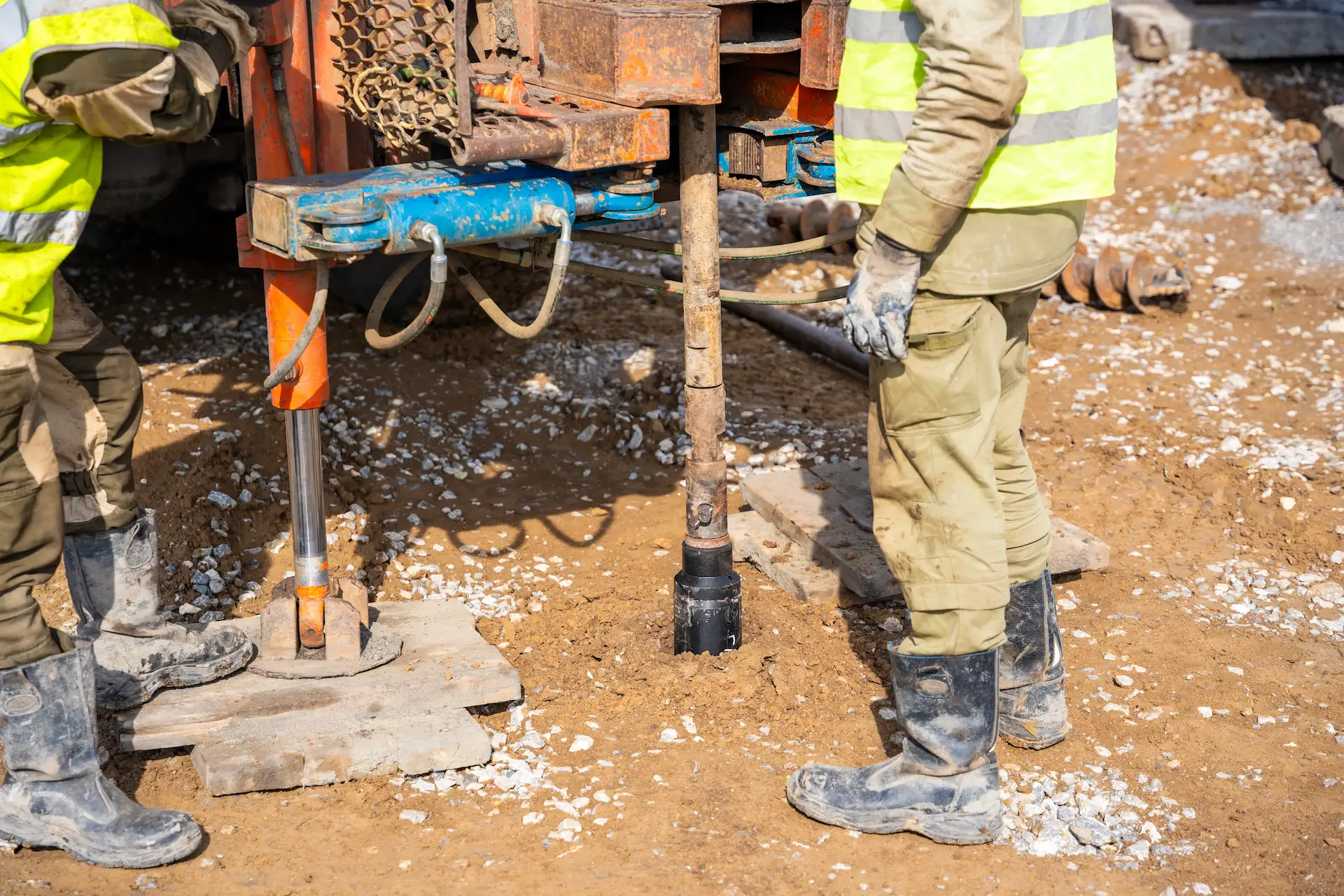
What Are Soil Borings & How Are They Conducted?
Understanding what lies beneath the surface of the earth is a critical piece of planning in the fields of construction, environmental due diligence, and geotechnical engineering.
Conducting soil borings is one of the most reliable methods for gaining this insight. Soil borings provide essential data about subsurface conditions, helping engineers, architects, and developers make informed decisions about site suitability, foundation design, and environmental impact.
What Are Soil Borings?
Soil borings are a geotechnical investigation technique used to collect soil samples from below the ground surface. These samples are analyzed to determine the physical and mechanical properties of the soil, such as composition, density, moisture content, strength, and bearing capacity. The information gathered is crucial for designing safe and effective foundations for buildings, roads, bridges, and other infrastructure.
Soil borings are also used in environmental assessments to detect contamination, monitor groundwater, and evaluate the suitability of land for agricultural or industrial use.
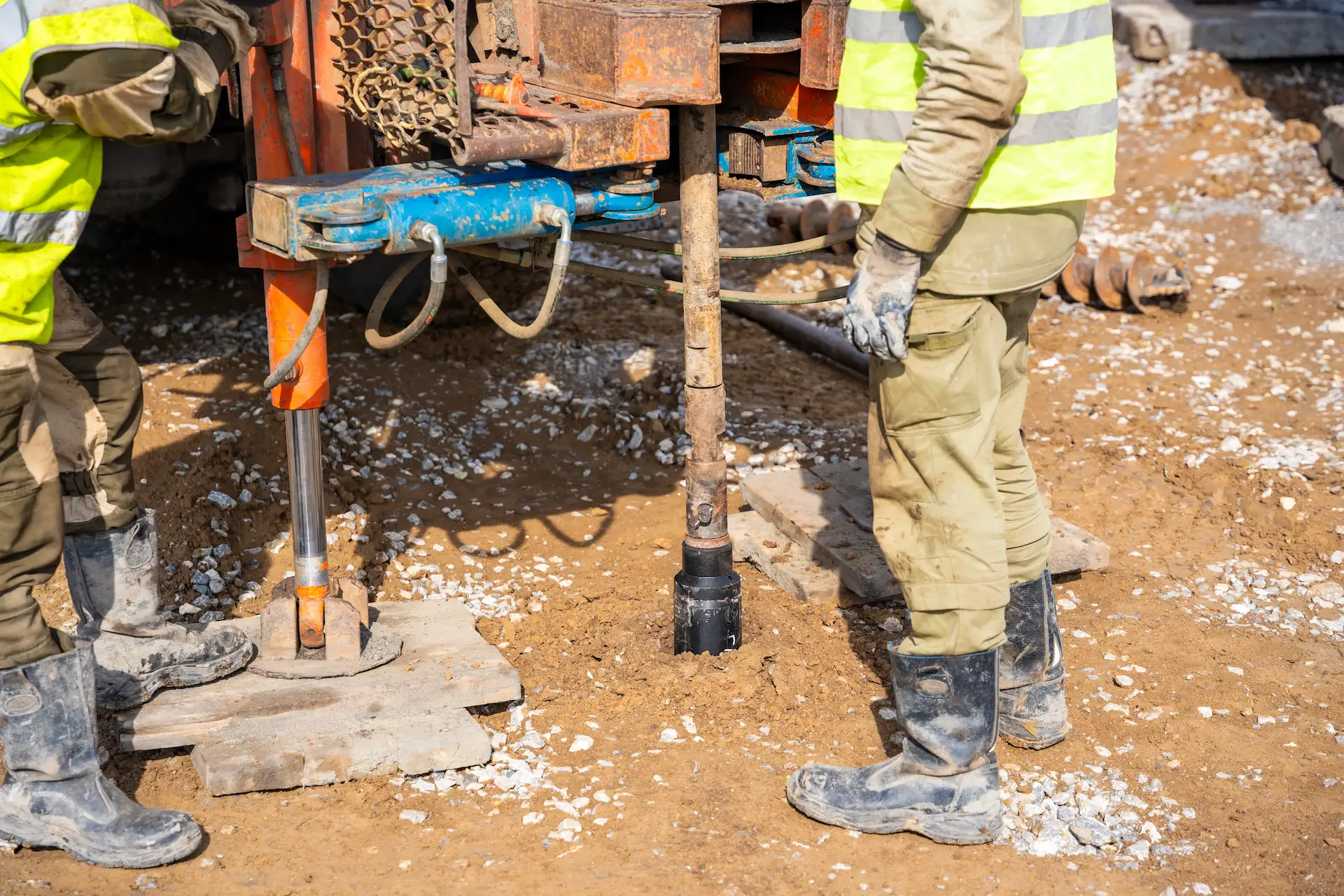
Why Are Soil Borings Important?
The subsurface conditions of a site can vary significantly, even within a small area. Without proper investigation, construction projects risk encountering unexpected soil behaviors such as settlement, liquefaction, or slope instability. These issues can lead to structural failure, costly delays, or environmental hazards.
Soil borings help to:
- Assess soil stability and load-bearing capacity
- Identify groundwater levels and flow
- Detect the presence of contaminants
- Inform the design of foundations and earthworks
- Ensure compliance with building codes and environmental regulations
Types of Soil Boring Methods
Several methods are used to conduct soil borings, each suited to different site conditions and project requirements. The most common include:
Auger Boring
This method uses a helical screw blade (auger) to drill into the ground. It is typically used for shallow borings in soft to medium soils. There are two main types:
- Hand augers are used for depths up to 10-15 feet
- Power augers are used for deeper or more resistant soils
Auger boring is relatively quick and cost-effective but may not be suitable for very hard or saturated soils.
Rotary Drilling
Rotary drilling uses a rotating drill bit to cut through soil and rock. It is often used for deeper borings and can penetrate a wide range of soil types. The drill bit is lubricated and cooled with drilling fluid (mud or water), which also helps to bring cuttings to the surface.
This method allows for continuous sampling and is ideal for complex geotechnical investigations.
Percussion Drilling
Also known as cable tool drilling, this method involves repeatedly dropping a heavy bit to break up soil and rock. The loosened material is then removed from the borehole. While slower than rotary drilling, percussion drilling is effective in hard or boulder-laden soils.
Wash Boring
Wash boring uses a jet of water to loosen soil, which is then removed by a suction pump. It is commonly used in soft soils and for preliminary investigations. However, it does not provide undisturbed samples, limiting its usefulness for detailed analysis.
The Soil Boring Process: Step-by-Step
Conducting a soil boring involves several key steps, typically carried out by a geotechnical engineering firm:
1. Site Preparation
Before drilling begins, the site is surveyed and cleared. The boring locations are selected based on the proposed construction layout and known geological conditions. Permits may be required, especially in urban or environmentally sensitive areas.
2. Drilling and Sampling
The drilling rig is set up at the designated location. As the borehole is advanced, soil samples are collected at regular intervals – usually every 2 to 5 feet or at changes in soil strata.
There are two main types of samples:
- Disturbed samples, which are suitable for classification and basic testing
- Undisturbed samples, which preserve the soil structure and are used for strength and compressibility tests
Sampling tools include split-spoon samplers, Shelby tubes, and piston samplers, depending on the soil type and required data.
3. Standard Penetration Test (SPT)
One of the most common in-situ tests performed during soil borings is the Standard Penetration Test (SPT). It involves driving a split-spoon sampler into the soil using a standardized hammer and recording the number of blows required to penetrate a set depth. The resulting "N-value" provides an indication of soil density and strength.
4. Groundwater Monitoring
As the borehole is drilled, groundwater levels are observed and recorded. In some cases, temporary or permanent monitoring wells are installed to track fluctuations over time.
5. Logging and Documentation
Throughout the boring process, a detailed borehole log is maintained. This log includes:
- Depth and type of each soil layer
- Sample locations and types
- SPT results
- Groundwater observations
- Any anomalies or obstructions encountered
This documentation forms the basis for the geotechnical report.
6. Laboratory Testing
Collected samples are sent to a geotechnical laboratory for further analysis. Common tests include:
- Grain size distribution
- Atterberg limits (plasticity)
- Moisture content
- Shear strength
- Consolidation and compaction characteristics
These tests provide the data needed to model soil behavior under load and design appropriate foundations.
Interpreting the Results
The final deliverable of a soil boring investigation is a geotechnical report. This report synthesizes field and lab data to provide:
- Soil profiles and stratigraphy
- Engineering properties of each soil layer
- Recommendations for foundation design
- Assessment of potential risks (e.g., settlement, liquefaction)
- Construction considerations (e.g., dewatering, excavation support)
This report is a critical tool for engineers and architects, guiding decisions that affect safety, cost, and long-term performance.
GPRS offers nationwide, precision utility locating services to help ensure the success of your soil boring projects.
Utilizing state-of-the-art subsurface investigation technology such as GPR scanning and EM locating, our SIM-certified Project Managers provide you with complete and accurate data bout the built world beneath your project site, so you can excavate without the risk of costly and potentially dangerous subsurface damage.
All this data is at your fingertips 24/7 thanks to SiteMap® (Patent Pending), GPRS’ project & facility management application that provides accurate existing conditions documentation to protect your assets and people.
From soil boring clearances to skyscrapers, GPRS Intelligently Visualizes The Built World® to keep your projects on time, on budget, and safe.
What can we help you visualize?
Frequently Asked Questions
What do I get when I hire GPRS to conduct a utility locate?
Our Project Managers flag and paint our findings directly on the surface. This method of communication is the most accurate form of marking when excavation is expected to commence within a few days of service.
GPRS also uses a global positioning system (GPS) to collect data points of findings. We use this data to generate a plan, KMZ file, satellite overlay, or CAD file to permanently preserve results for future use. GPRS does not provide land surveying services. If you need land surveying services, please contact a professional land surveyor.
Please contact us to discuss the pricing and marking options your project may require.
Can GPRS Project Managers distinguish between different underground utilities that they locate?
In most situations, we can identify the utility in question without any problems, although it is not always possible to determine what type of utility is present. When this happens, we attempt to trace the utility to a valve, meter, control box, or other signifying markers to determine the type of utility buried.
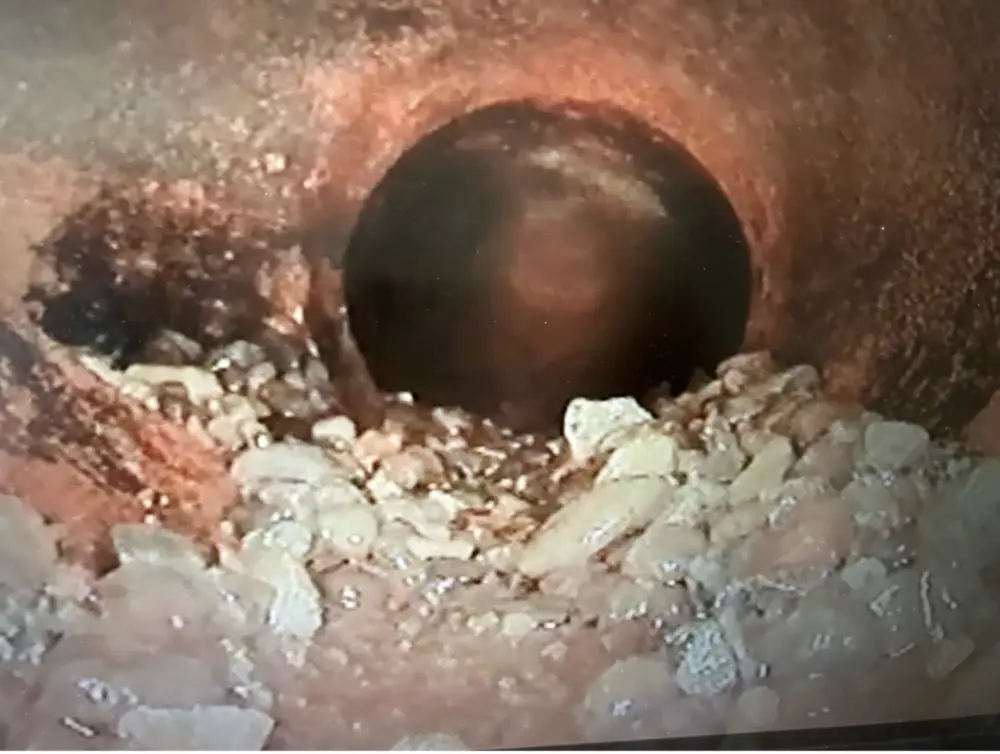
GPRS VPI Services Help New High School Address Cracking Sewer System
When students at Rainier Beach High School in Seattle, Washington, returned from spring break this past school year and entered their brand new, four-story school building, the sanitary sewer lines running underneath the campus would have been the last thing on their minds.
But about a year before the new, 297,000 s.f. school building opened, those pipes were all that contractor Lydig Construction could think about. That’s because they’d discovered that the building’s concrete slab was slowly sinking into the ground, cracking open the new cast iron pipes as it went.
Lydig and the school district needed to pinpoint the location of each break in the pipelines, and they needed an accurate map of the entire buried sewer system, so they could effectively plan a permanent repair. While a plumber working on the project had sewer inspection equipment of their own, however, they had been unable to obtain the data the contractor needed.
So Lydig called GPRS.
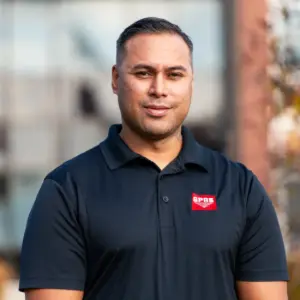
Project Manager Robert Rasmussen deployed a combination of a remote-controlled sewer inspection crawler and push-fed sewer scope to provide the contractor with a NASSCO-certified report of their sewer system, complete with photo and video evidence of every defect.
Rasmussen worked together with the contractor, returning to the site several times over the course of a week to inspect and map more segments of the system.
He’d access the system from inside the school by feeding his push-fed scope into the cleanouts. Then, when he couldn’t continue any further due to sediment buildup in the lines, he’d deploy his remote-controlled crawler from a manhole outside and try to meet up with where the scope had run into the blockage. As Rasmussen provided the contractor and plumber with the precise location of each area where water, sediment, and other debris was entering the cracked pipes, a jetting company would use the data to clear the lines so that he could proceed further.
“I was able to pinpoint where all the breaks were in the pipelines, and where all the pea gravel and dirt was coming in from the breakage,” Rasmussen said. “And then I was able to locate all the pipelines.”
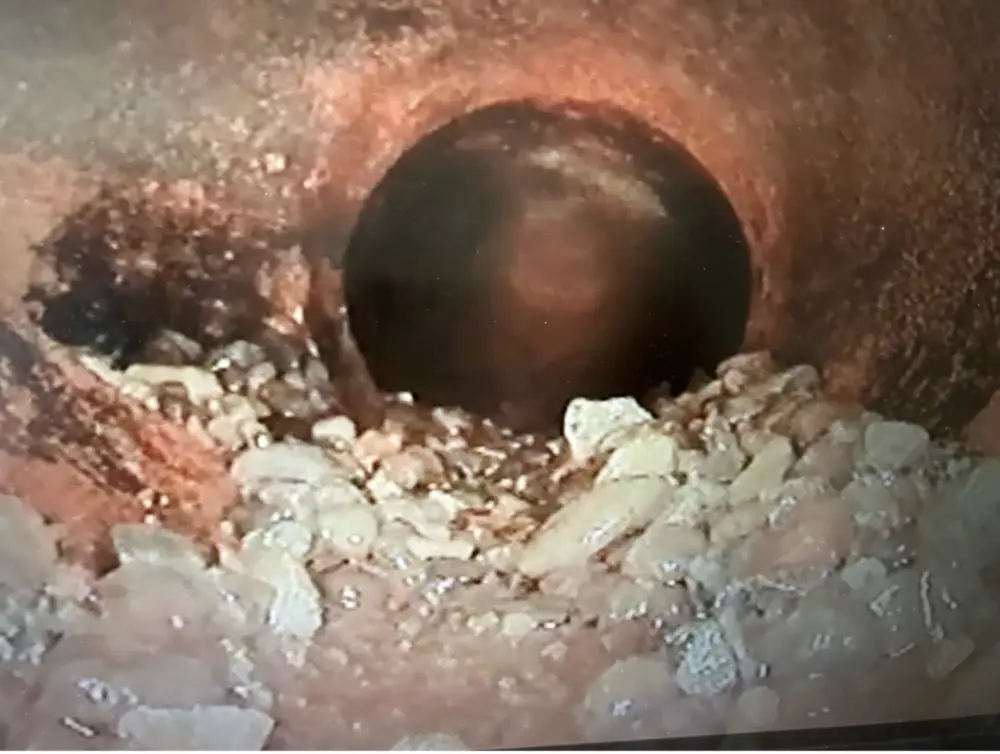
In total, Rasmussen inspected 105 linear feet of sewer line. Both his push-fed sewer scope and remote-controlled crawler were equipped with sondes: instrument probes that emit a signal detectable from the surface with an electromagnetic (EM) locator. This allowed Rasmussen to map the sewer system while he was locating defects.
The data Rasmussen collected at Rainier Beach High School helped Lydig and the school district effectively repair the damaged sanitary sewer lines and reroute them to protect from future damage. When students and faculty did finally get to enjoy their new building, they could focus on academics and athletics – and not on what was going on beneath their feet.
“[The client was] very impressed,” he said. “They initially called me out for just one day, to scope some of the lines that their plumbers found and couldn’t really investigate. Then two days after that, they called me back out on site and it ended up being like three or four days of me being out there scoping, to see where the real problem was. Every single one of those new cleanouts and pipelines, they were filled with rock and sediment.”
Whether you need help assessing a brand-new sanitary sewer system, or a decades-old storm line, GPRS’ comprehensive suite of sewer inspection services can help ensure your infrastructure keeps working for you.
We offer video pipe inspection (VPI) using the remote-controlled crawlers and push-fed scopes to create comprehensive NASSCO reports that detail every defect located, ranked by severity and identified with photo and video evidence. You’ll know what needs fixed immediately and exactly where you need to dig to enact those repairs.
NASSCO stands for the National Association of Sewer Service Companies, and they are the industry-leading provider of training and certification programs focused on assessing, maintaining, and rehabilitating underground sanitary sewer and stormwater lines. Every GPRS Project Manager that conducts sewer inspection services has achieved NASSCO certification in pipeline (PACP), manhole (MACP), and lateral (LACP) assessments. So when you hire GPRS, you always know you’re getting the best trained sewer inspection company near you.
Additionally, GPRS can inspect your sewer system using dye tracing or smoke testing, to assess things like flow direction and determine if there are any illegal or incorrect hookups to your lines.
From sewer lines to skyscrapers, GPRS Intelligently Visualizes The Built World® to keep your projects on time, on budget, and safe.
What can we help you visualize?
Frequently Asked Questions
What size sewer pipes can GPRS inspect?
Thanks to our use of both remote-controlled sewer inspection crawlers and push-fed sewer scopes, we’re able to inspect pipes 2” in diameter and up.
Can you locate sewer pipes in addition to evaluating their integrity?
Yes! Our SIM and NASSCO-certified Project Managers use VPI technology equipped with sondes, which are instrument probes that allow them to ascertain the location of underground utilities from an inaccessible location. This allows them to use electromagnetic (EM) locating to map sewer systems at the same time they’re evaluating them for defects.
What deliverables does GPRS offer when conducting a VPI?
GPRS is proud to offer WinCan reporting to our Video Pipe Inspection clients. Maintaining sewers starts with understanding sewer condition, and WinCan allows GPRS Project Managers to collect detailed, NASSCO-compliant inspection data. GPRS Project Managers not only inspect the interior condition of sewer pipes, laterals, and manholes – they can also provide a map of their location. The GPRS Mapping & Modeling Department can provide detailed GPS overlays and CAD files. Our detailed WinCan/NASSCO reports contain screenshots of the interior condition of the pipe segments that we inspect, as well as a video file for further evaluation, documentation, and/or reference.
Does GPRS offer Lateral Launch Services?
Yes, we offer lateral launch capabilities as part of our standard Video Pipe Inspection services.
.webp)
$500M Hydrogen Retrofit to Transform Coal-Fired Power Plant
In a landmark move for the energy sector, Utah’s Intermountain Power Project (IPP) is undergoing a transformative upgrade that positions it at the forefront of clean energy innovation. As reported by Engineering News-Record (ENR), the IPP Renewed initiative is a testament to the power of regional cooperation and a bold step toward decarbonizing large-scale power generation through the integration of green hydrogen. As the global energy landscape shifts toward sustainability, this project exemplifies how legacy infrastructure can be reimagined to meet the demands of a low-emissions future.
Environmental Impact and Emissions Reduction
The transition from coal to hydrogen-blended fuel represents a significant environmental milestone. By leveraging green hydrogen – produced through electrolysis powered by renewable energy – the IPP Renewed project aligns with California’s stringent emissions regulations and broader climate objectives.
Hydrogen combustion emits only water vapor, eliminating carbon dioxide and other harmful pollutants associated with fossil fuels. As the technology matures and the hydrogen blend increases, the plant’s emissions profile will continue to improve, setting a new standard for utility-scale power generation.
.webp)
A Strategic Shift Toward Hydrogen Power
Commissioned in the 1980s, the IPP has long served as an energy hub for communities across six states. With its 1,800-MW coal-fired units nearing the end of their operational life and power purchase agreements set to expire in 2027, stakeholders faced a pivotal decision. Rather than decommission the site, the Intermountain Power Agency (IPA) and its partners chose to invest in a cleaner, more flexible future.
The centerpiece of this transformation is the installation of two advanced M501JAC gas turbines from Mitsubishi Power, capable of operating on a blend of natural gas and hydrogen. To start, the turbines will run on a 30% hydrogen mix, with a roadmap to transition to 100% green hydrogen by 2045. This shift is expected to reduce carbon dioxide emissions by over 75% compared to traditional coal-fired generation.
Leveraging Unique Geology for Energy Storage
One of the most innovative aspects of the IPP Renewed project is its integration with the Advanced Clean Energy Storage (ACES) Delta hub. Located atop a geologic salt dome, the site offers a natural advantage for underground hydrogen storage. Two massive caverns, each capable of holding 4.5 million barrels of hydrogen, will serve as long-term, seasonal energy reservoirs.
This storage capability is crucial for balancing the intermittency of renewable energy sources. Surplus solar and wind power can be converted into green hydrogen via electrolysis and stored until demand peaks. This method enhances grid reliability and enables a more resilient and sustainable energy system.
Engineering Excellence and Workforce Development
The scale and complexity of the IPP Renewed project are immense. With over five million labor hours logged and more than 2,000 workers on-site, the project has become a model for workforce development in the energy sector. The Industrial Company (TIC), serving as the EPC contractor, implemented an on-site training program to certify workers in real-time, accelerating their progression to journeyman status.
In a notable first, TIC also self-performed heavy equipment hauling using self-propelled modular transport units, eliminating reliance on specialty subcontractors and streamlining logistics. This approach underscores the importance of adaptability and innovation in modern infrastructure projects.
Modernizing Transmission for a Clean Energy Future
Beyond generation, the IPP Renewed initiative includes a $2.7-billion overhaul of the Southern Transmission System, which delivers power from Utah to Southern California. This upgrade involves constructing new DC converter stations and enhancing the 2,400-MW transmission capacity to accommodate the evolving energy mix.
The modernization of transmission infrastructure is a critical enabler of the hydrogen economy. It ensures that clean, dispatchable power generated in Utah can be efficiently delivered to demand centers hundreds of miles away, supporting regional decarbonization goals.
The Role of Utility Locating and Leak Detection
As hydrogen infrastructure expands, utility locating and leak detection becomes paramount. Because hydrogen is the smallest and lightest molecule, it can escape through minute leaks that would be inconsequential for other gases. Accurate utility locating ensures that underground pipelines and storage facilities are mapped with accuracy, reducing the risk of accidental damage during construction or maintenance.
Advanced leak detection technologies, including acoustic sensors and leak detection correlators, are essential for maintaining safety and operational integrity.
How GPRS can Support the Future of Clean Energy Infrastructure
GPRS expertise in subsurface infrastructure plays a vital role in supporting projects of this magnitude. As the energy industry embraces hydrogen and other clean technologies, the need for accurate, real-time data on underground utilities and structural conditions becomes increasingly critical.
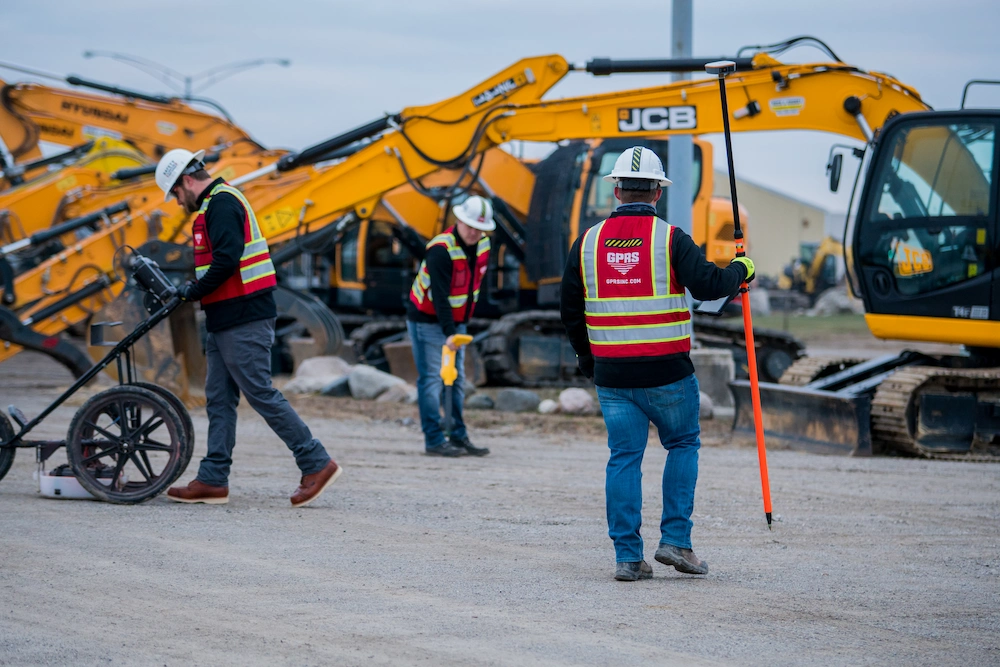
For complex infrastructure projects like the IPP, GPRS offers support services that enhance safety, accuracy, and efficiency. These include utility locating using ground penetrating radar (GPR) and electromagnetic (EM) locating, advanced leak detection, concrete scanning, 3D laser scanning and mapping to create accurate digital models for design and construction planning, and video pipe inspection to assess the condition of sewer and stormwater systems. Projects involving hydrogen power plants and large-scale energy storage require the highest levels of precision and risk mitigation. GPRS services are indispensable for ensuring safe construction, reliable operations, and long-term infrastructure integrity.
As hydrogen power plants and storage hubs become more prevalent, GPRS stands ready to support these projects with the tools and expertise necessary to ensure safety, efficiency, and regulatory compliance. Our commitment to precision and innovation makes us a trusted partner in the transition to a cleaner, more sustainable energy future.
From hydrogen hubs to high-voltage transmission lines, GPRS Intelligently Visualizes The Built World® to keep your infrastructure projects safe, efficient, and on schedule.
What can we help you visualize?
FREQUENTLY ASKED QUESTIONS
Why is utility locating critical for hydrogen infrastructure projects?
Hydrogen facilities require accurate excavation to avoid damaging underground utilities. GPRS uses ground-penetrating radar (GPR) and electromagnetic (EM) locating to identify and map subsurface utilities before construction begins. This helps reduce the risk of utility strikes, supports safe excavation, and ensures compliance with safety regulations.
How does GPRS support leak detection in hydrogen systems?
Hydrogen is colorless, odorless, and highly flammable, which makes early leak detection essential for safety. GPRS’ SIM-certified Project Mangers use acoustic sensors and leak detection correlators to identify leaks in pressurized systems. These technologies help prevent safety incidents, reduce operational downtime, and support compliance with safety standards.
What role does concrete scanning play in hydrogen facility construction?
GPRS can help prevent costly delays and safety risks during hydrogen facility construction by identifying embedded objects before any coring or cutting begins. These objects may include rebar, conduits, and post-tension cables. When locating them in advance, project teams can avoid structural damage and ensure the safe installation of critical systems.
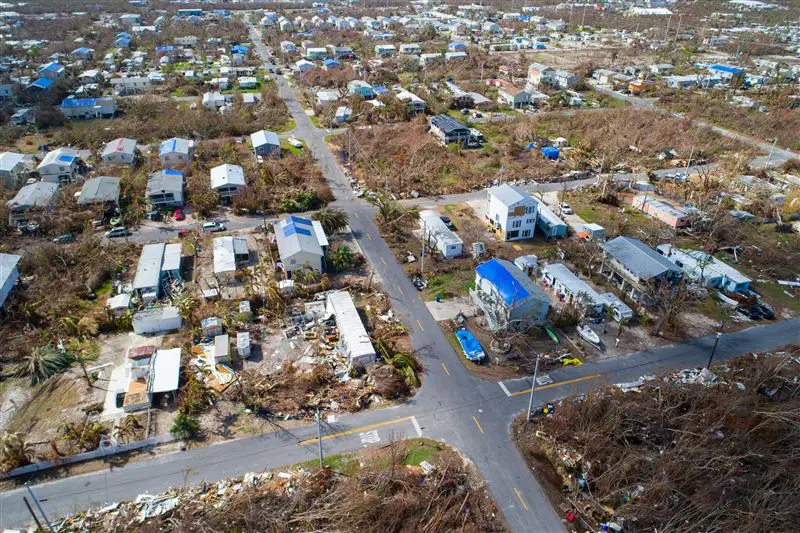
Jacobs Wins $137M Award to Help Rebuild U.S. Virgin Islands After Hurricane Damage
Global professional services firm Jacobs has been awarded a program management contract to rebuild the U.S. Virgin Islands following hurricanes Irma and Maria.
According to a press release on Jacobs’ website, the company was contracted by the Virgin Islands Public Finance Authority to deliver program management services for the “Rebuild USVI” initiative. The contract is valued at $137 million and will see Jacobs work with the U.S. Virgin Islands’ Super Project Management Office on simultaneous, critical infrastructure projects, including hospitals, schools, transit corridors, power, water and wastewater utilities.
"Rebuilding is critical for St. Croix, St. Thomas, and St. John,” said Jacobs Executive Vice President Ron Williams. “The islands are home to nearly 90,000 people who depend on safe schools, reliable transportation, consistent utility services and access to healthcare. Further, with tourism as the economic engine, it's essential we prioritize efforts quickly and make the islands' infrastructure more resilient for the future."
During this three-year-contract, Jacobs – which has a long history of rebuilding critical infrastructure following severe weather events – will also provide advisory and consulting services focused on future project planning, environmental management, logistics, supply chain, and workforce challenges.
The Office of Disaster Recovery (ODR), operating under the Virgin Islands Public Finance Authority, manages the territory’s $23 billion in federal aid allocated following the devastating hurricanes of 2017. While progress has been made in the years since the hurricanes ravaged the islands, there is still much work to be done. Director Adrienne Williams-Octalien reaffirmed ODR’s dedication to the Super Project Management initiative, noting that Jacobs was chosen for the “Rebuild USVI” program due to its strong proposal response, proven expertise, competitive pricing, available resources, innovative approach, and strategic alliances.
Jacobs has supported efforts like the Port of San Francisco Waterfront Resilience Program, which is adapting 7.5 miles of the city's waterfront to be resilient to earthquakes, coastal storms and sea level rise; reinstating vital power infrastructure in the Philippines following devastating earthquakes; returning and maintaining essential services to the Puerto Rican community following Hurricane Maria; and continued on-the-ground assistance with FEMA disaster-related operations throughout the U.S. and its territories.
"We are excited to have Jacobs' support as we continue working to rebuild a stronger, more resilient community while ensuring full compliance with our funding requirements," Williams-Octalien said.
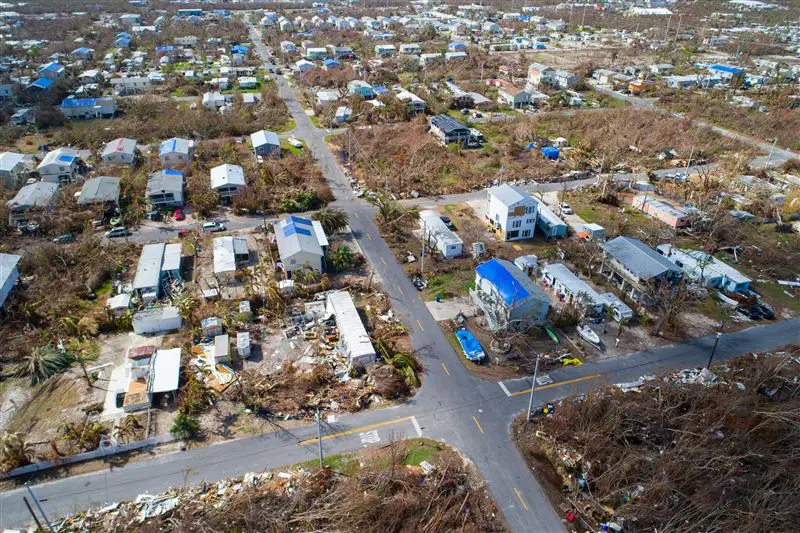
The Importance of Fortifying Our Infrastructure for Extreme Weather – and How GPRS Can Help
The changing climate has altered the landscape of risk for infrastructure globally. Rising temperatures, increased precipitation in some areas, and prolonged droughts in others present complex challenges that existing infrastructure was not originally designed to withstand. These changes have resulted in more frequent and severe weather events, from the flooding of major urban centers to the destructive paths of hurricanes across coastlines.
Elevating building foundations, using water-resistant materials, installing sump pumps and other flood mitigation systems can help protect buildings and their infrastructure from water damage during floods. Non-combustible building materials help reduce wildfire risks in fire-prone regions, and wind-resistant roofing and impact-resistant windows ensure structures can withstand high winds and flying debris in hurricane-prone areas.
Utility or grid hardening, the process of upgrading and strengthening utility infrastructure to make it more resilient to severe weather and other disruptions, can protect these critical utilities from a variety of weather-related issues. Communities across the country are undergrounding their power lines to reduce the risk of outages from wind, lightning strikes, and more.
But anytime you’re putting something new in the ground, it’s vital you’re aware of any buried utilities or other underground infrastructure assets that are already there.
GPRS is the nation’s largest company offering above and below-ground existing conditions documentation. We Intelligently Visualize The Built World® to keep your projects on time, on budget, and safe.
GPRS employs advanced technologies like ground penetrating radar (GPR) and electromagnetic (EM) locating to locate utilities underground, as well as post tension cable, rebar, and conduits and more within concrete slabs.
We geolocate and digitize these findings and deliver them to you through SiteMap® (patent pending), our project & facility management application that provides accurate existing conditions documentation to protect your assets and people.
Available 24/7 from any computer, tablet, or smartphone, SiteMap is a single source of truth for the critical data that allows you to protect your infrastructure from damage, whether you’re hardening a power grid or just conducting regular maintenance.
What can we help you visualize?
Frequently Asked Questions
Does GPRS locate PVC piping and other non-conductive utilities?
Yes, our SIM-certified Project Managers utilize a suite of infrastructure visualization tools, including ground penetrating radar (GPR) and electromagnetic (EM) locating, to find all types of subsurface materials. These tools compensate for each other’s weak points, allowing us to create an accurate, complete picture of your job site.
Will I need to mark out the utilities that GPRS locates?
No, our Project Managers locate and mark all utilities for you when conducting a utility locate. We have a variety of tools and markers we use to highlight the locations of utilities, underground storage tanks (USTs), and other buried items.
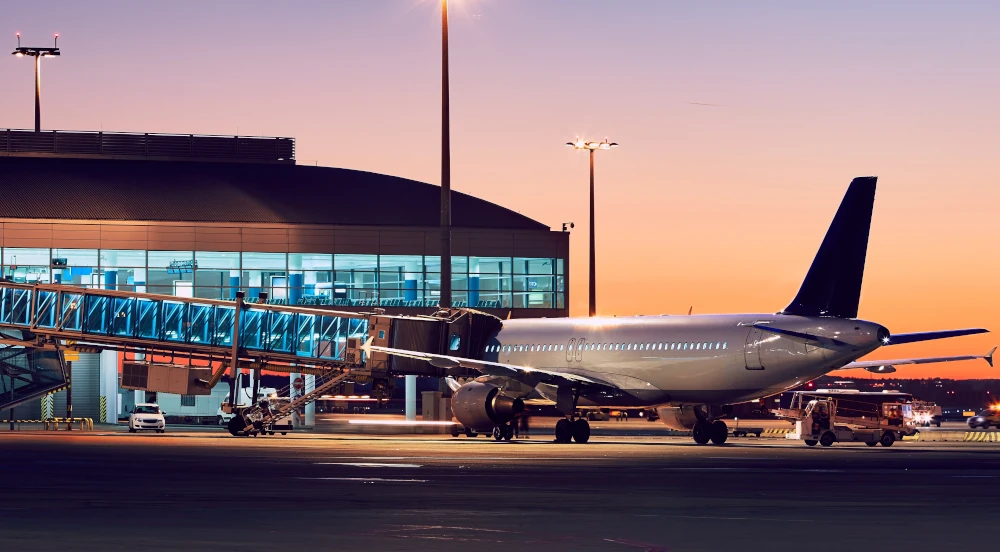
Severed Fiber Line at Jacksonville Airport Causes Radar Outage
Damage to critical buried infrastructure recently caused a scary situation at Jacksonville International Airport (JAX) in Jacksonville, Florida.
On June 20, air traffic controllers briefly lost radar capabilities after contractors cut a buried fiber optic cable during construction work.
According to The Associated Press, controllers were able to continue directing planes across five states in the Southeast because a backup system kicked in as designed. The Federal Aviation Administration (FAA) said no flights were disrupted.
“The FAA said the radar center in Jacksonville, Florida, continued operating but on alert status because its primary communication line went down,” the AP wrote. “A contractor was working on repairing the severed fiber line Friday afternoon. Authorities didn’t specify what caused the severed line or where it happened.”
While this event was, thankfully, resolved without incident, it serves as a reminder of how easily a single mistake when digging or trenching can put lives in danger.
Whether you’re digging just a few inches into the ground or several feet, or conducting your excavation utilizing directional drilling or other trenchless technologies, obtaining accurate utility locating and mapping data prior to breaking ground is the best way to avoid costly and potentially dangerous damage to buried infrastructure.
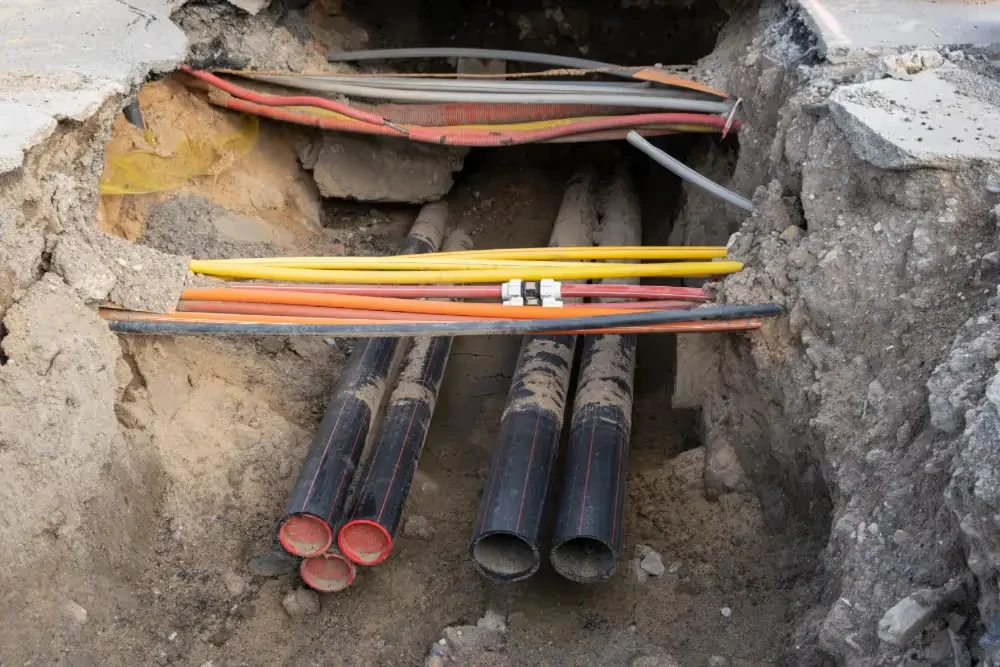
Why Are Fiber Optic Lines Especially Vulnerable?
Unlike metal pipes or electrical lines, fiber optic cables are made of glass or plastic and do not emit electromagnetic signals. This makes them harder to detect using traditional methods. They are often installed with tracer wires within the conduit, allowing for the use of electromagnetic signal tracing. Utility locating companies use electromagnetic (EM) locators to detect these tracer wires.
The Cost of Damaging a Fiber Optic Line
At JAX, the severed fiber optic line likely served as a vital data link for radar systems. The consequences of such damage extend far beyond repair costs. In air traffic control, even a brief radar outage can delay hundreds of flights and jeopardize passenger safety. The FAA and other agencies must then reroute traffic and investigate the incident, pulling resources from other essential operations.
Hiring a professional utility locating company to find and map underground fiber optic cables and all other buried utilities prior to breaking ground is an essential step in mitigating the risk of costly and potentially dangerous subsurface damage.
How Do Utility Locating Services Help Prevent Subsurface Damage?
Utility locating services identify and map underground utilities before any digging or construction begins, helping to avoid accidental strikes that could cause costly damage, service outages, or safety hazards.
Calling your local 811 center should be your first step whenever you’re planning an excavation. Federal law requires you contact 811 to receive the approximate location of all registered utilities within your project area prior to breaking ground. Registered utilities can consist of both private and public lines, but it’s important to remember that not all utilities are registered with 811.
GPRS’ professional utility locating services complement the 811 locate by providing you with accurate and complete data about the buried infrastructure on your job site. GPRS uses a combination of tools, including ground penetrating radar (GPR), electromagnetic (EM) locators, and GPS mapping to detect both public and private utility lines.
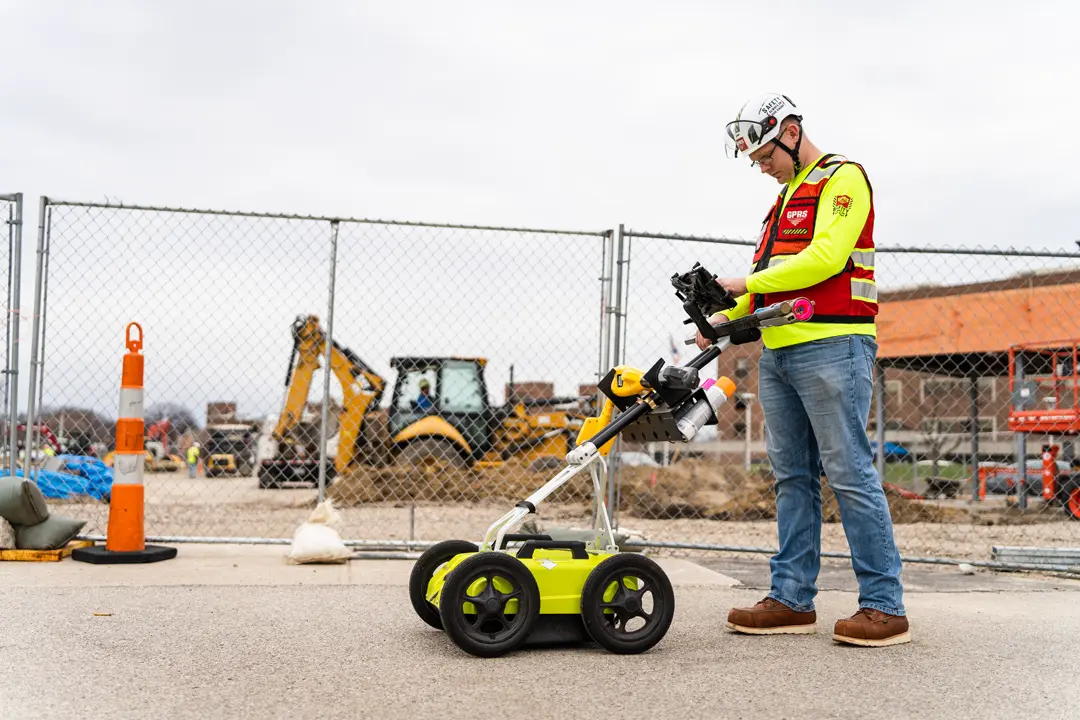
Once utilities have been detected, they’re physically marked at the job site with highly visible, color-coded flags or paint to indicate their type and precise location. These markings serve as a visual guide for construction crews, helping them navigate around underground infrastructure safely and accurately during excavation and construction.
The GPRS Mapping & Modeling team provides digital maps and .KMZ files that can be integrated into construction planning software, ensuring that crews have real-time access to utility layouts.
SiteMap®, (patent pending), powered by GPRS, is our proprietary infrastructure mapping software solution that provides you and your team with 24/7, secure access to the accurate, field-verified data collected by GPRS Project Managers. Accessible from any computer, tablet or smartphone, it is a single source of truth for the critical infrastructure you and your team needs to plan, manage, and build better.
GPRS Intelligently Visualizes The Built World® to keep your projects on time, on budget, and safe.
What can we help you visualize?
Read Also: How is Utility Locating Done?
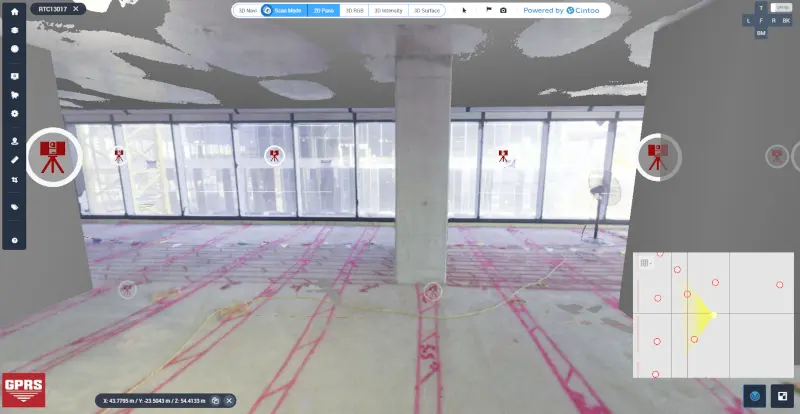
How Does a 3D Laser Scanner Capture Concrete Markings?
A 3D laser scanner captures concrete markings by emitting laser beams that reflect off surfaces and return to the scanner, collecting millions of precise data points that map the concrete markings on site. These data points are compiled into a high-resolution 3D point cloud that maps the shape, texture, and position of everything in view, including paint, chalk lines, or other surface markings. This digital record allows teams to document site conditions, verify layouts, and permanently record markings for future reference.
Not only does the 3D laser scanner provide detailed and accurate records of concrete markings, but it also captures all architectural, structural and MEP features, delivering a comprehensive digital asset for renovation, construction, and analysis.
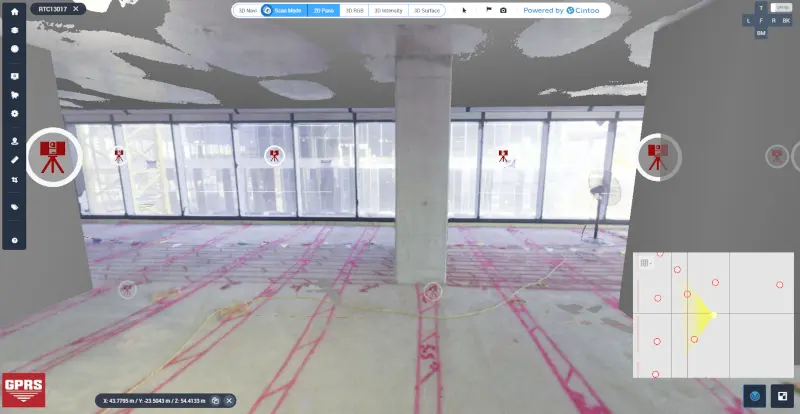
What is the Method of Concrete Scanning?
Concrete scanning uses ground penetrating radar (GPR), which sends radio signals into the concrete to detect subsurface features. The system’s transmitter, receiver, and signal processor work together to identify embedded objects like rebar, conduits, or post tension cables. Trained professionals interpret the reflected signals to map their location, pattern, and depth.
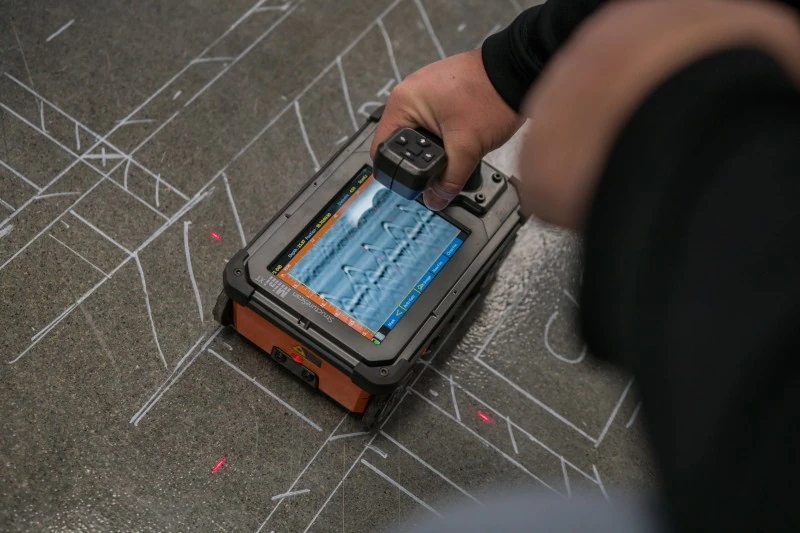
What is the Process of Capturing Concrete Markings with a 3D Laser Scanner?
- Process: After using GPR to identify and mark objects within concrete, such as rebar or utilities, a 3D laser scanner captures these markings in a point cloud.
- Purpose: This process allows for accurate documentation of concrete markings and can be used to generate 2D CAD drawings or 3D models of findings to aid in safe cutting, drilling, or anchoring into concrete.
- Technology: Leica laser scanners, such as the RTC360, utilize LiDAR technology to capture precise site data at high speeds.
- Software: Leica Cyclone or Autodesk Recap can be used to process the captured point cloud, allowing for the extraction of markings and the generation of CAD/BIM deliverables.
- Benefits: Capturing concrete markings with laser scanners like the Leica RTC360 ensures 2-4mm accuracy and helps minimize human error, leading to improved safety and efficiency on construction sites.
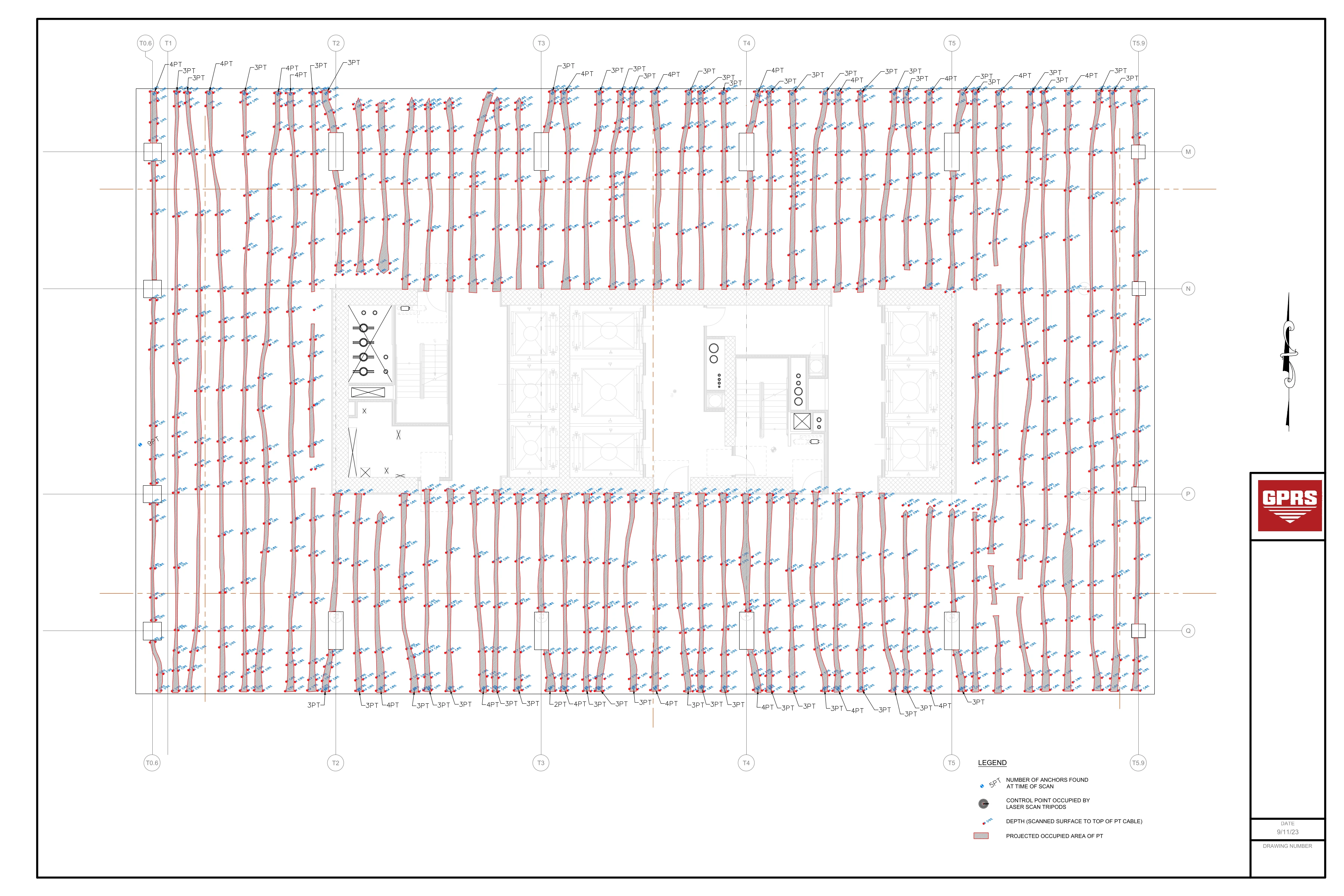
Why Use Leica Laser Scanners to Capture Concrete Markings?
Leica laser scanners are considered among the best in the industry because they combine exceptional speed, accuracy, and ease of use with powerful software integration. For example, the Leica RTC360 laser scanner can capture up to 2 million data points per second and uses advanced features like automatic point cloud registration and HDR imaging to deliver high-quality, colorized scans in under two minutes. Leica’s software makes it easy to turn raw scan data into deliverables like BIM models, CAD drawings, and immersive 3D environments. High-resolution imagery, or TruViews, can be added to the laser scanning process, making it easier to identify and document markings digitally for layout verification or future reference.
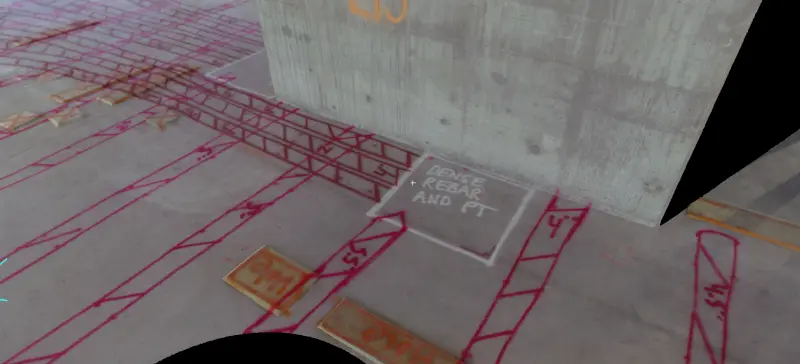
Can GPRS Use a 3D Laser Scanner to Capture Concrete Markings?
Yes, the Project Managers at GPRS are formerly trained to perform concrete imaging services using GPR technology and reality capture services using 3D laser scanners.
GPRS Project Managers complete the most extensive subsurface training program in the industry, called SIM certification. SIM teaches Project Managers how to utilize GPR and EM locating to identify the layout of rebar, post tension cables, buried utilities, and more with 99.8%+ accuracy. Achieving SIM 101 certification, which is required of all GPRS Project Managers, involves completing 80 hours of hands-on classroom instruction and 320 hours of mentorship in the field.
While the technology for underground utility locating and concrete imaging is standardized, the methods of deploying the tools are not. SIM certification ensures the precision and attention to detail necessary for the accurate subsurface investigations that will keep projects on time, on budget, and safe.
The training program for GPRS 3D laser scanning services includes an additional 40 hours of LiDAR training on Leica scanning equipment, plus additional field experience.
GPRS Project Managers have elite training in concrete scanning and reality capture technologies, plus a field-tested methodology to deliver high-quality results tailored to each project’s needs.
GPRS Intelligently Visualizes the Built World® above and below ground as the leading national provider of accurate utility locating, concrete scanning & imaging, reality capture, video pipe inspection, leak detection, and mapping & modeling solutions for the construction, architecture, and engineering industries.
What can we help you visualize?
Frequently Asked Questions
What Types of Concrete Scanning are There?
GPRS provides two specific but different concrete scanning services: elevated concrete slab scanning and concrete slab-on-grade locating. Elevated concrete slab scanning involves detecting embedded electrical conduits, rebar, post-tension cables, and more before core drilling a hole through the slab. Performing a concrete slab-on-grade locating service typically involves scanning a trench line for conduits before conducting saw cutting and trenching to install a sanitary pipe, water line, or something similar.
Who Needs Concrete Scanning?
Clients turn to us for concrete scanning for a range of needs, from verifying the placement of rebar to safely drilling or cutting into post-tension slabs without damaging the tensioned cables.
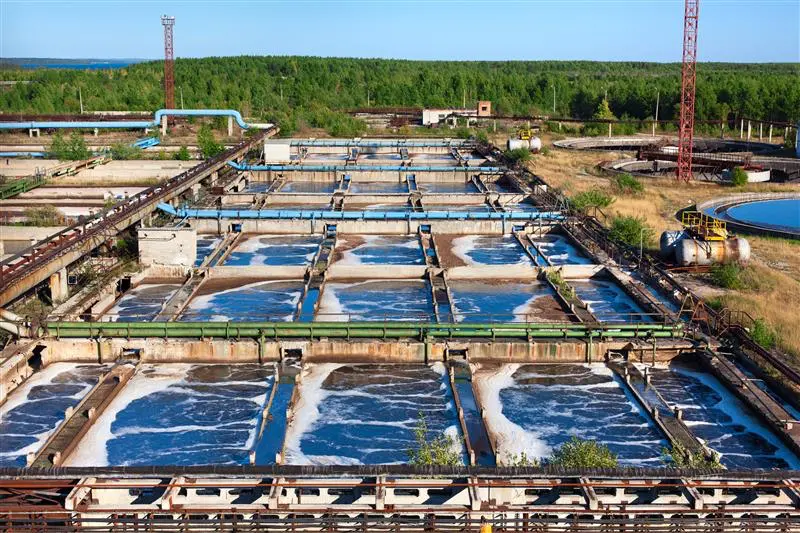
Largest Water Treatment Plant in Arkansas to Receive $230 Million Overhaul
The largest water treatment plant in the State of Arkansas is set to receive a $230 million overhaul.
The Jack H. Wilson Water Treatment Plant in west Little Rock is being renovated to deal with new regulations, changes to its water source and any emerging contaminants while increasing its treatment capacity from 133 million gallons per day to 150 million, according to an article in the Northwest Arkansas Democrat-Gazette.
One of Central Arkansas Water’s two water treatment facilities, the nearly-70-year-old Wilson plant receives water from the Lake Maumelle reservoir. This renovation project is Central Arkansas Water’s biggest ever, according to reporting by Construction Dive, which spoke with Central Arkansas Water spokesperson, Douglas Shackelford.
Construction will be conducted in phases, with the facility remaining operational throughout. Work is expected to take about five years to complete.
“This plant is vital to our system, and so we can’t shut it down. It’s got to be operational while construction is going on,” Shackelford said. “There are four large water basins in the facility, and we will essentially shut down one and renovate that basin and then keep the other three open and working while one is under construction.”
“[New technology is] going to allow us to move the water through it at a faster pace that would allow for the capacity increase,” he continued. That will “help us out in the long run, because obviously, as cities grow and demand goes higher for water, we need to be able to produce it.”
The Max Foote Construction Co. is the project’s construction manager at-risk. Unlike with Design-Build projects, during construction manager at-risk projects, design and construction are separate contracts and criteria other than lowest total construction cost factor into the selection of the construction manager.
“CM-at-Risk allows for the early project involvement of a CM who can partner with the A/E and Agency to provide constructability assistance, estimating, design review and early procurement opportunities,” writes Associated General Contractors (AGC) of America. “Additionally, the start of construction can begin prior to 100% complete design documents. The CM-at-Risk typically also provides detailed cost estimates early in the design phase, so that value engineering and cost reduction ideas can be considered when they are the most easily addressed.”
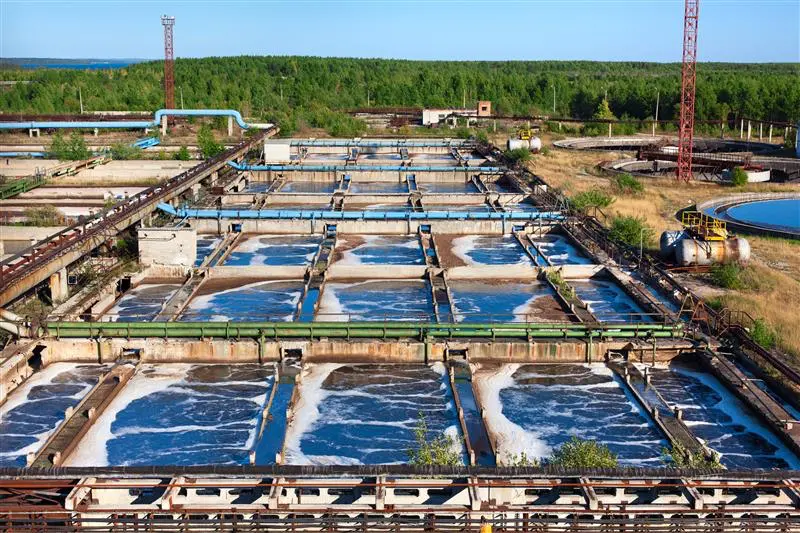
The State of America’s Drinking Water Infrastructure
Arkansas’ investment in its largest water treatment facility comes just as the nation is seeing the first positive signs from recent, widespread investments in critical infrastructure.
America’s infrastructure received its highest-ever grade in the American Society of Civil Engineers’ 2025 Report Card for America’s Infrastructure. The country received an overall grade of “C”, with eight of the 18 categories assessed by ASCE seeing grade increases, and – for the first time since 1998 – no categories receiving a rating of D- or lower.
“For more than two decades, the message behind the unflattering grades was consistent: federal, state, and local governments, in addition to the private sector, have not been prioritizing our interdependent infrastructure systems,” the ASCE wrote in the 2025 report card’s executive summary. “In sum, the bill on our infrastructure systems was past due. We needed to reverse the nation’s growing infrastructure investment gap to remain competitive in the global marketplace, allow local businesses to thrive, and keep our families safely connected. That message grew louder with each evaluation, through our most recent Report Card release in early 2021”.
Drinking water received a grade of C-. This was the same grade it earned in the previous report card released in 2021, with the ASCE noting in the 2025 report the need for additional funding to assess this infrastructure’s shortcomings.
“The nation’s water infrastructure is aging and underfunded,” the ASCE wrote. “More than 9 million existing lead service lines pose health concerns, and in 2023, the Environmental Protection Agency (EPA) determined that the nation’s water infrastructure needs stand at $625 billion over 20 years. That exceeds EPA’s 2018 assessment by more than $150 billion. The 2021 Infrastructure Investment and Jobs Act (IIJA) invested more than $30 billion for drinking water capital improvements, removal of lead service lines, and addressing emerging contaminants such as per- and polyfluoroalkyl substances (PFAS). However, funding shortfalls continue in state revolving funds that support drinking water.”
In addition to the advanced age of much of the U.S.’s water infrastructure, the ASCE outlined other challenges in this sector such as emerging contaminants and the increasingly severe effects of extreme weather.
The ASCE said that the implementation of asset management plans is a critical step needed to address the challenges facing America’s drinking water infrastructure.
“Many drinking water utilities are actively improving infrastructure through innovations such as asset failure prediction technologies, which improve the ability to identify issues before they become failures. Unfortunately, only about 30% of utilities have fully implemented an asset management plan, and just under half are in the process of implementing one.”
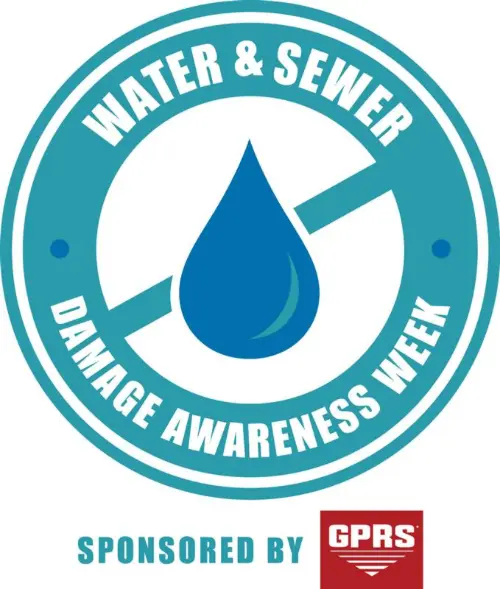
Let GPRS Help You Maintain Your Water Infrastructure
GPRS is committed to helping you maintain the drinking water infrastructure under your care.
We offer pinpoint-accurate leak detection services that utilize acoustic leak detection and leak detection correlators to ensure your water stays where it belongs. And our comprehensive suite of subsurface damage prevention, existing conditions documentation, and construction & facilities project management services help you plan, manage, and build better.
Our commitment to helping you maintain your infrastructure extends beyond the services we offer. GPRS also sponsors Water & Sewer Damage Awareness Week, an annual safety initiative designed to help water and wastewater system operators take a more proactive approach to maintaining their infrastructure.
During this event, our safety experts travel to your job site, office, council meeting – wherever you need us – to deliver free safety presentations to municipalities, engineers, facility managers, property management groups, and anyone else who is ready to regain control of their fresh and wastewater infrastructure.
Click here to schedule your free WSDAW presentation today!
Frequently Asked Questions
How many miles of underground water pipe can GPRS test for leaks in a single day?
While it can depend on a variety of factors, our leak detection Project Managers typically can inspect up to 10 miles of pipe a day on a metallic system (cast iron/ductile) and one contact point (hydrant/valve) per minute.
Can GPRS determine the size of a located leak?
After analyzing thousands of previous leaks detected, we asked clients to send us pictures of the remediation. This information has helped us compare our final leak signal detected with the results of the actual leak. We determine the size of the leak by how far the leak signal travels between contact points and the pitch of the tone received. We do not, however, produce formal leak estimations.
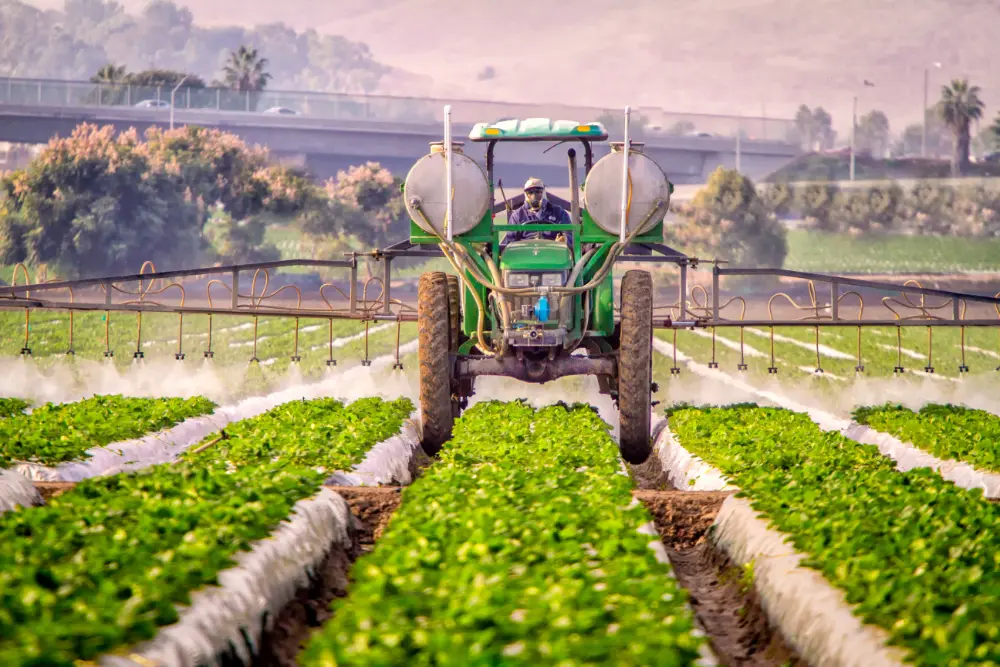
Semi-Volatile Organic Compounds (SVOCs) Explained
Semi-volatile organic compounds, or SVOCs, are – as their name suggests – less volatile than volatile organic compounds (VOCs). But SVOCs still pose significant implications for indoor air quality, environmental contamination, and human health.
What Are Semi-Volatile Organic Compounds?
SVOCs are a class of organic chemicals characterized by their intermediate vapor pressures, typically ranging from 10⁻¹¹ to 10² Pascals at room temperature.
This property places them between VOCs, which readily evaporate into the air, and non-volatile compounds, which tend to remain in solid or liquid form.
SVOCs include a wide variety of chemical families such as:
- Phthalates: Used as plasticizers
- Polybrominated diphenyl ethers (PBDEs): Used as flame retardants
- Polychlorinated biphenyls (PCBs): Formerly used in electrical equipment
- Pesticides (e.g., DDT, chlorpyrifos)
- Polycyclic aromatic hydrocarbons (PAHs): Byproducts of combustion
These compounds are typically found in both indoor and outdoor environments, often persisting in dust, on surfaces, and in the air.
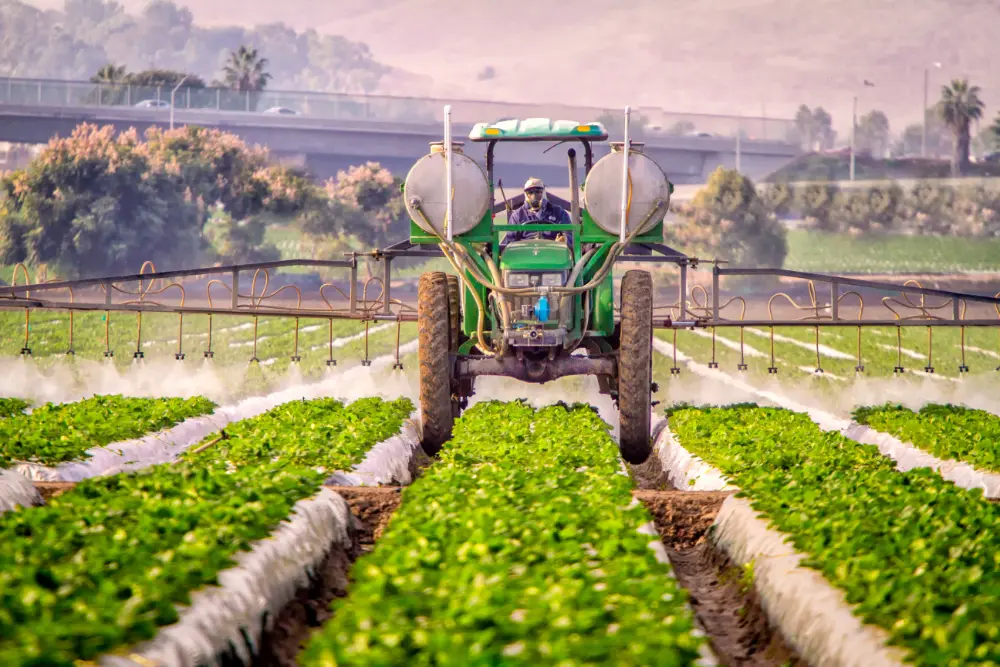
Sources of SVOCs
SVOCs originate from a wide array of sources, both anthropogenic and natural. Common indoor sources include:
- Consumer products: Personal care items, cleaning agents, and air fresheners.
- Building materials: Paints, sealants, adhesives, and vinyl flooring.
- Furnishings: Upholstered furniture, carpets, and electronics.
- Combustion processes: Tobacco smoke, cooking, and heating appliances.
Outdoors, SVOCs are released through industrial emissions, vehicle exhaust, pesticide application, and the degradation of other organic compounds.
Behavior and Fate in the Environment
Unlike VOCs, which tend to dissipate quickly into the atmosphere, SVOCs exhibit a more complex behavior due to their dual-phase nature. They can exist in both the gas phase and adsorbed onto particles or surfaces. This characteristic leads to several important environmental behaviors:
- Partitioning: SVOCs partition between air, dust, water, and surfaces. Indoors, they often accumulate in settled dust and on surfaces like walls and furniture.
- Persistence: Many SVOCs are chemically stable and degrade slowly, leading to long-term environmental presence.
- Bioaccumulation: Some SVOCs, particularly those with high lipid solubility, can accumulate in the fatty tissues of living organisms, magnifying their effects through the food chain.
Health Impacts of SVOCs
Exposure to SVOCs can occur through inhalation, ingestion (especially of dust), and dermal contact. The health effects vary depending on the specific compound, concentration, duration of exposure, and individual susceptibility. Some of the documented and suspected health impacts include:
- Endocrine disruption: Certain phthalates and flame retardants can interfere with hormone systems, potentially affecting reproductive and developmental health.
- Respiratory issues: Inhalation of SVOCs may exacerbate asthma and other respiratory conditions.
- Neurotoxicity: Compounds like PBDEs have been linked to cognitive and behavioral effects, particularly in children.
- Carcinogenicity: Some SVOCs, such as PAHs and PCBs, are classified as probable or known human carcinogens.
Children are particularly vulnerable due to their developing systems and behaviors such as hand-to-mouth activity, which increases ingestion of contaminated dust.
SVOCs in Indoor Environments
Indoor environments are of particular concern because people spend most of their time indoors – at home, work, or school. SVOCs can be released slowly over time from materials and products, leading to chronic low-level exposure. Factors influencing indoor SVOC levels include:
- Ventilation: Poor ventilation can lead to accumulation of SVOCs.
- Temperature and humidity: Higher temperatures can increase SVOC emissions from materials.
- Cleaning practices: Dust removal can reduce SVOC reservoirs, but some cleaning products may also introduce new SVOCs.
Studies have shown that indoor dust can contain significant concentrations of SVOCs, making it a major exposure pathway, especially for young children.
Regulation and Standards
Regulatory oversight of SVOCs varies by region and compound. In the United States, several agencies play roles in monitoring and regulating SVOCs:
- Environmental Protection Agency (EPA): Regulates pesticides and industrial chemicals under laws such as the Toxic Substances Control Act (TSCA).
- Consumer Product Safety Commission (CPSC): Oversees safety of consumer products, including restrictions on phthalates in children's toys.
- Occupational Safety and Health Administration (OSHA): Sets exposure limits for certain SVOCs in workplace settings.
Internationally, the European Union’s REACH regulation and the Stockholm Convention on Persistent Organic Pollutants (POPs) also address SVOC risks.
Mitigation and Exposure Reduction
Reducing exposure to SVOCs involves a combination of source control, environmental management, and personal behavior. Key strategies include:
Source Identification and Substitution
- Choose products labeled as low-emission or free of specific SVOCs
- Avoid materials known to contain phthalates or flame retardants
Improved Ventilation
- Use mechanical ventilation systems or open windows to dilute indoor pollutants
Dust Control
- Regular vacuuming with HEPA filters and wet dusting can reduce SVOC-laden dust
Temperature and Humidity Control
- Maintain moderate indoor temperatures and humidity to limit SVOC emissions
Policy and Advocacy
- Support regulations that limit the use of harmful SVOCs in consumer products and building materials
Future Directions and Research
Ongoing research continues to uncover the complexities of SVOC behavior, exposure pathways, and health effects. Emerging areas of interest include:
- Cumulative risk assessment: Understanding the combined effects of multiple SVOCs and other pollutants.
- Green chemistry: Developing safer alternatives to SVOCs in industrial and consumer applications.
- Advanced monitoring technologies: Improving detection and quantification of SVOCs in various environments.
Semi-volatile organic compounds represent a significant yet often overlooked class of environmental contaminants. Their persistence, ubiquity, and potential for harm underscore the importance of awareness, regulation, and mitigation.
GPRS is the trusted leader for damage prevention in the environmental sector. Our project managers deliver results from the beginning of the initial investigation, throughout delineation and remediation, until project completion. With our nationwide network of Project Managers, we are equipped to mobilize to projects across the United States.
From sewer lines to skyscrapers, GPRS Intelligently Visualizes The Built World® to keep your projects on time, on budget, and safe.
What can we help you visualize?
Frequently Asked Questions
What do I get when I hire GPRS to conduct a utility locate?
Our Project Managers flag and paint our findings directly on the surface. This method of communication is the most accurate form of marking when excavation is expected to commence within a few days of service.
GPRS also uses a global positioning system (GPS) to collect data points of findings. We use this data to generate a plan, KMZ file, satellite overlay, or CAD file to permanently preserve results for future use. GPRS does not provide land surveying services. If you need land surveying services, please contact a professional land surveyor.
Please contact us to discuss the pricing and marking options your project may require.
Can GPRS Project Managers distinguish between different underground utilities that they locate?
In most situations, we can identify the utility in question without any problems, although it is not always possible to determine what type of utility is present. When this happens, we attempt to trace the utility to a valve, meter, control box, or other signifying markers to determine the type of utility buried.
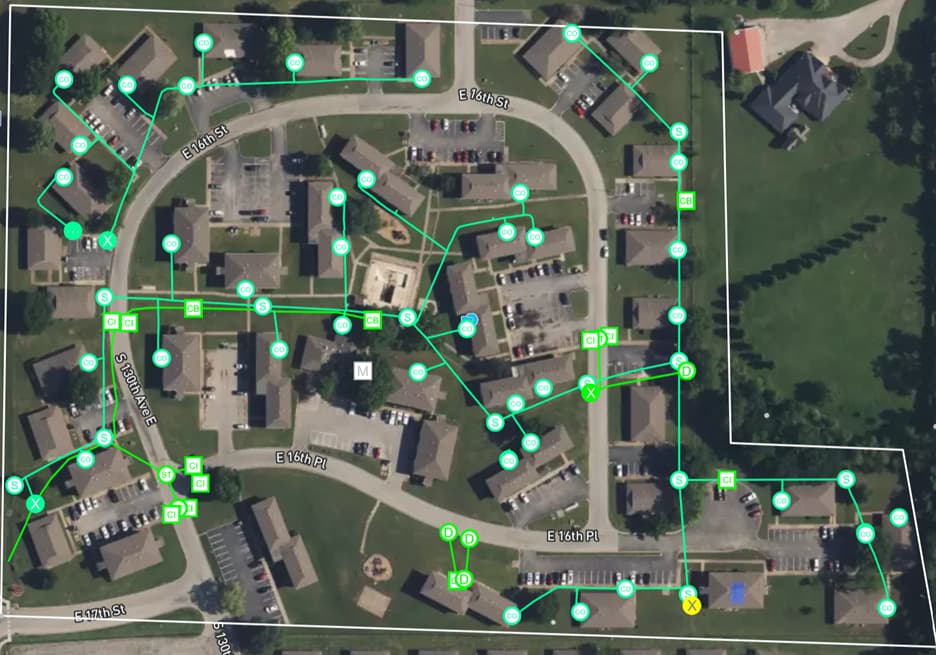
GPRS VPI Services Locate and Assess Conditions of All Sanitary and Storm Sewer Lines Across a 19-Acre Apartment Complex
GPRS helped locate all underground sewer and sanitary lines throughout a 19-acre apartment complex in Tulsa, Oklahoma.
The complex’s facility manager had no existing records of their 1950s-era subsurface infrastructure and was not aware of the current conditions of these lines. They needed an updated map of the built world beneath their feet.
GPRS Project Manager Joe Meyer was tasked with investigating the complex’s sewer and sanitary lines and provide a NASSCO-certified report on all blocked, defective, or obstructed pipes along with the map, so they could effectively plan repairs and maintenance.
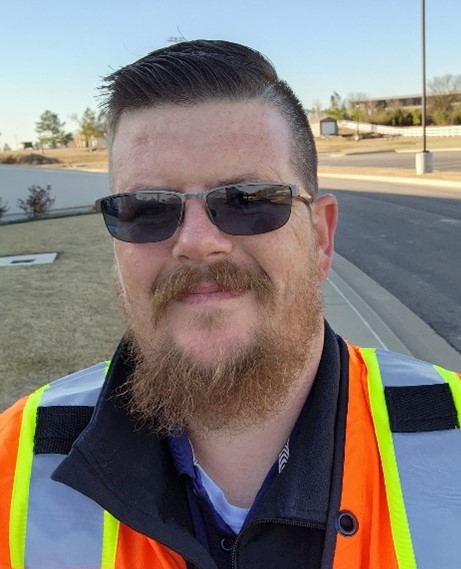
All GPRS Project Managers are NASSCO (National Association of Sewer Service Companies) certified in pipeline (PACP), lateral (LACP), and manhole (MACP) assessments.
GPRS Project Managers use the Envirosight ROVVER X Mainline Crawler to capture photo and video evidence of defects and other issues along sewer and stormwater lines. This remote-controlled rover can crawl as far as 1,640 feet into a sewer line and can adapt to inspect lines from 6” to 96” in diameter.
The ROVVER X SAT Lateral Launch camera can inspect sewer laterals from the mainline to identify any damages or defects, including cross bores, so clients can properly address them.
Push cameras, also known as flexible rodders, are used by GPRS Project Managers to access smaller spaces that crawlers can’t fit in, like vents, cleanouts, and toilet plumbing. The push camera also contains a sonde that can be detected by an electromagnetic (EM) locator to map non-metallic pipes.
“For this job, I inspected and located 3,411 linear feet of underground pipes, including 1,823 feet of sanitary and storm sewer mainline and 1,588 feet of sanitary sewer lateral lines,” Meyer said.
The 75-year-old infrastructure presented challenges Meyer had to overcome, including the design of the pipes.
“There was no sweep to the clean outs, they were straight 90 [degrees], so there was some trouble trying to get the camera to swoop into them,” he explained. “That was a challenge, but I was able to overcome that by using that SAT launcher from the mainline and when I got one halfway, I could meet up with the other [from the other side of the mainline].”
Meyer also found himself getting creative to access manholes that were in difficult to access locations.
“There was a gated swimming pool area that had a manhole right in the corner of the gate,” he said. “I had to set up in a weird way, so that was kind of fun, but I overcame that challenge.”
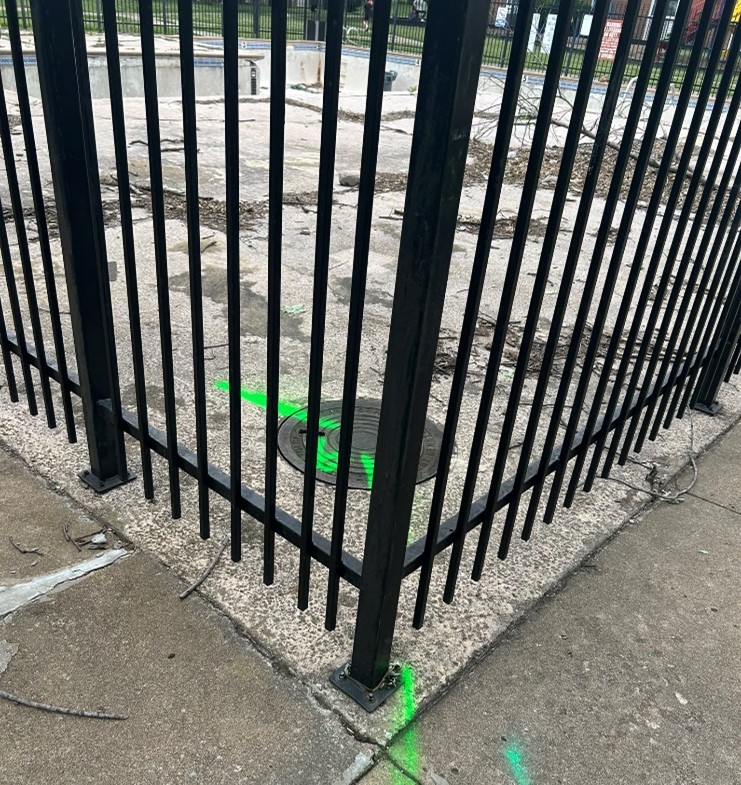
This job was conducted during the first week of June, so Meyer was faced with a fun challenge since summer vacation had begun for the kids in the neighborhood.
“It was right when school got let out, so all my flags disappeared overnight,” Meyer said. “That was pretty funny, so I didn't put any more flags down after that once I knew that they were all fair game. There were tons of kids around and there were some of them having fun watching what I was doing and seeing me test my crawler.”
Once he finished his investigation, Meyer provided the client with a map depicting the location of their sewer and sanitary lines via SiteMap® (patent pending), GPRS’ cloud-based infrastructure mapping platform. With SiteMap, the client can securely access their records 24/7 as they plan any upcoming renovation or restoration projects.
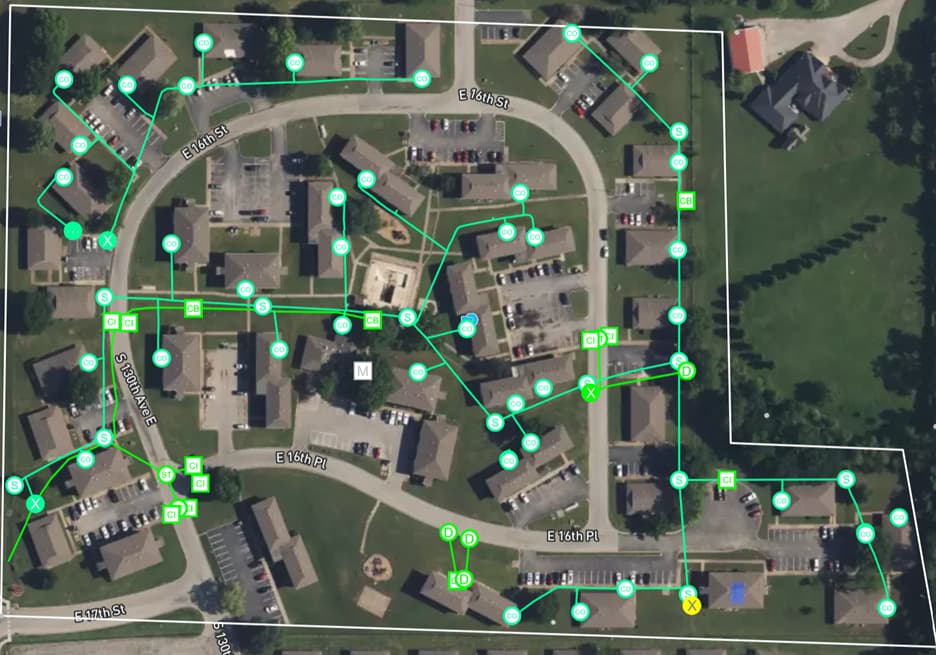
A NASSCO-certified Video Pipe Inspection report was created detailing the condition of the pipes and ranking defects by severity. Meyer did find some obstructions within the pipes that he was able to relay to the client so they can make necessary repairs.
“I found I had three units that did not have an external clean out and I could not access it from the main[line],” Meyer explained. “I also found a few clean outs that were completely full of dirt that maintenance had to come take care of while I was there. And I gave them a list, with priority, of what they can work on, so, all in all, it was helpful for them, even beyond just the mapping.”
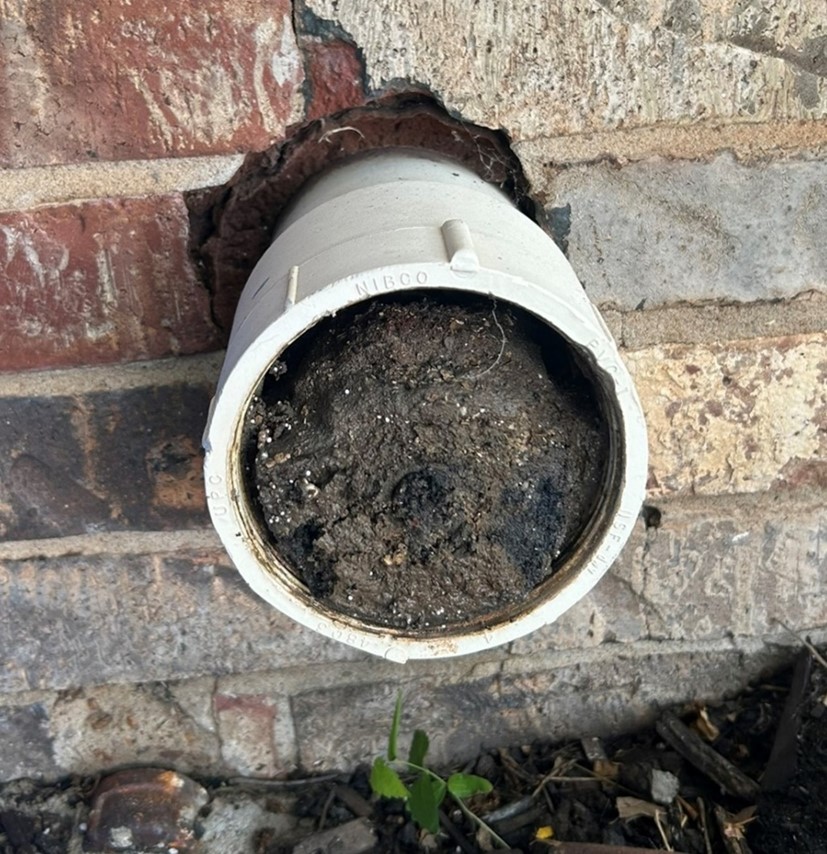
Even, with the hurdles to overcome, Meyer completed his work within the client’s timeline.
“Everything really went well and it went on time as expected,” Meyer explained. “I kept in contact with the site contact and he was appreciative of that.”
From sewer line inspections to skyscraper scans, GPRS Intelligently Visualizes the Built World® to keep your projects on time, on budget, and safe.
What can we help you visualize?
FREQUENTLY ASKED QUESTIONS
What size sanitary sewer and stormwater pipes can GPRS inspect with its Video Pipe Inspection service?
Our elite, NASSCO-certified VPI Project Managers have the capabilities to inspect pipes from 2” in diameter and up.
What deliverables does GPRS offer when conducting a VPI?
GPRS is proud to offer WinCan reporting to our Video Pipe Inspection clients. Maintaining sewers starts with understanding sewer condition, and WinCan allows GPRS Project Managers to collect detailed, NASSCO-compliant inspection data. GPRS Project Managers not only inspect the interior condition of sewer pipes, laterals, and manholes – they can also provide a map of their location. The GPRS Mapping & Modeling Department can provide detailed GPS overlays and CAD files. Our detailed WinCan/NASSCO reports contain screenshots of the interior condition of the pipe segments that we inspect, as well as a video file for further evaluation, documentation, and/or reference.
.webp)
$250M Expansion of South Bay Wastewater Treatment Plant Fast-Tracked in San Diego
In a bold move to address one of the most persistent environmental and public health challenges on the U.S.-Mexico border, PCL Construction and Stantec have announced a $250 million expansion of the South Bay International Wastewater Treatment Plant in San Diego. According to a recent article in Engineering News-Record, the project has been fast-tracked in response to ongoing cross-border sewage flows from Tijuana, Mexico, and represents a landmark in binational infrastructure collaboration and environmental engineering.
The expansion, awarded under a $42.4 million progressive design-build contract, will double the plant’s treatment capacity from 25 million to 50 million gallons per day (MGD). This represents a significant increase from the previously targeted 35 MGD. This upgrade is critical to mitigating the decades-long issue of untreated sewage entering the Tijuana River and flowing into the Pacific Ocean near the South Bay community of Imperial Beach.
.webp)
A Technical Blueprint for Resilient Water Treatment
At a public forum hosted by the U.S. Section of the International Boundary and Water Commission (IBWC) on June 12, Michael Watson, Senior Vice President of Major Projects (Water) at Stantec, and Jeff Newman, Operations Manager at PCL, outlined the technical roadmap for the expansion.
The project scope includes:
• A new integrated headworks system for improved preliminary treatment
• Two new primary sedimentation tanks and 10 secondary sedimentation tanks
• Seven activated sludge tanks to enhance biological treatment
• A new chemical treatment system
• Sludge thickening and storage facilities
• A 12-kV electrical building with upgraded switchgear and transformers provided by San Diego Gas & Electric
“In partnership with PCL, we will work hard to provide the most seamless plant expansion possible,” said Watson. “We believe the repairs and changes we are undertaking will make a measurable difference both now and in the future.”
This expansion is a major milestone for wastewater treatment plant capacity and a model for how modern water treatment infrastructure can be scaled to meet urgent environmental demands.
A Binational Challenge with Global Implications
Mexico’s military has completed the expansion of the Punta Bandera Wastewater Treatment Plant, but concerns remain about long-term capacity and maintenance. With Tijuana’s population doubling over the past two decades, infrastructure resilience is more critical than ever.
The South Bay expansion goes beyond a local project, it’s a model for international cooperation, resilient infrastructure, and environmental justice. It demonstrates how engineering, policy, and technology must converge to solve complex, cross-border challenges.
How GPRS Supports Infrastructure Companies with Precision and Safety
With excavation, retrofitting, and utility integration at the core of the project, GPRS brings essential visibility and verification to ensure construction proceeds safely and without costly delays.
A trusted partner to infrastructure companies across North America, GPRS has demonstrated its value in complex environments, such as a recent California trenching project, helping teams avoid utility strikes and maintain excavation safety.
In projects where excavation, retrofitting, and utility integration are central to success, GPRS supports contractors and engineers by delivering detailed utility mapping and structural scanning before any ground is broken. This helps prevent utility strikes, ensures safe trenching, and allows for confident decision-making during construction. GPRS’ concrete scanning services help identify embedded elements like rebar and post-tension cables, reducing the risk of structural damage during coring or cutting.
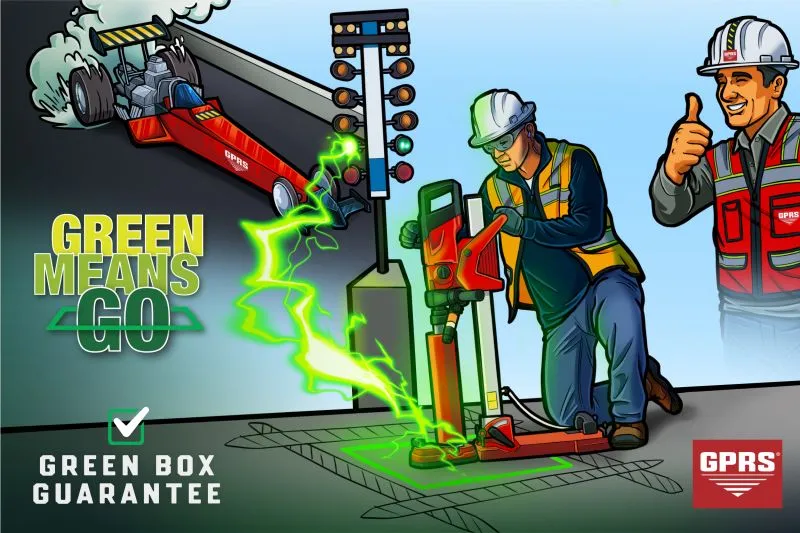
Leak detection is another key consideration in wastewater infrastructure. GPRS uses advanced acoustic technologies to identify leaks in pressurized systems, helping project teams maintain system integrity and avoid environmental or operational setbacks. In addition to acoustic methods, GPRS water loss specialists leverage a full suite of tools – including leak noise correlators, video pipe inspection, ground penetrating radar (GPR), and electromagnetic (EM) locating to accurately detect and pinpoint leaks. This service help clients reduce water loss, avoid costly emergency repairs, and maintain compliance with environmental regulations.
Video pipe inspection (VPI) provides a clear assessment of existing underground pipelines, ensuring that legacy systems are properly evaluated before integration with new components.
All this data is captured and delivered through SiteMap® (patent pending), GPRS’ cloud-based infrastructure mapping and facility management platform. It centralizes utility maps, inspection reports, and 3D models in one secure location. Project teams can access this information anytime, from anywhere, from any computer, tablet or smartphone. Improving coordination between field crews, engineers, and facilities managers, SiteMap also streamlines workflows and reduces the risk of miscommunication.
.webp)
From skyscrapers to sewer lines, GPRS Intelligently Visualizes The Built World® to keep your projects on time, on budget, and safe.
What can we help you visualize?
FREQUENTLY ASKED QUESTIONS
How does utility locating help prevent delays in wastewater treatment plant construction?
Utility locating is essential in large-scale infrastructure projects like wastewater treatment plant expansions. GPRS uses advanced ground penetrating radar (GPR) and electromagnetic (EM) locating technology to accurately map underground utilities before excavation begins. This prevents accidental utility strikes, reduces costly rework, and keeps construction on schedule.
Why is leak detection important in water treatment infrastructure?
Leak detection ensures the integrity of pressurized systems and prevents water loss, contamination, and environmental hazards. In wastewater and water treatment facilities, undetected leaks can lead to regulatory violations and operational inefficiencies. GPRS uses acoustic leak detectors and leak detection correlators to identify leaks early, helping infrastructure companies maintain system performance and avoid costly repairs.
What role does SiteMap® play in managing complex infrastructure projects?
SiteMap is designed to centralize and simplify access to critical subsurface data. It allows project teams to view and manage utility maps, inspection reports, and site documentation in one secure, cloud-based environment. By organizing high-resolution data collected from services like utility locating, video pipe inspection, and concrete scanning, SiteMap enhances coordination, reduces risk, and supports informed decision-making throughout the lifecycle of an infrastructure project.
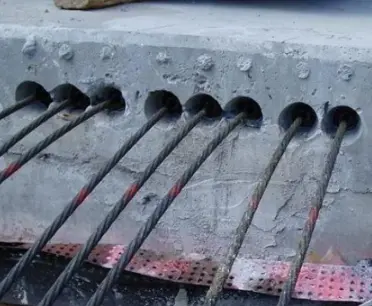
How Post-Tensioned Cables Are Anchored In Concrete Slabs
Post-tensioned (PT) slabs are essential in modern construction, especially high-rise construction, because they offer efficiency, durability, and the ability to span longer distances while reducing material usage.
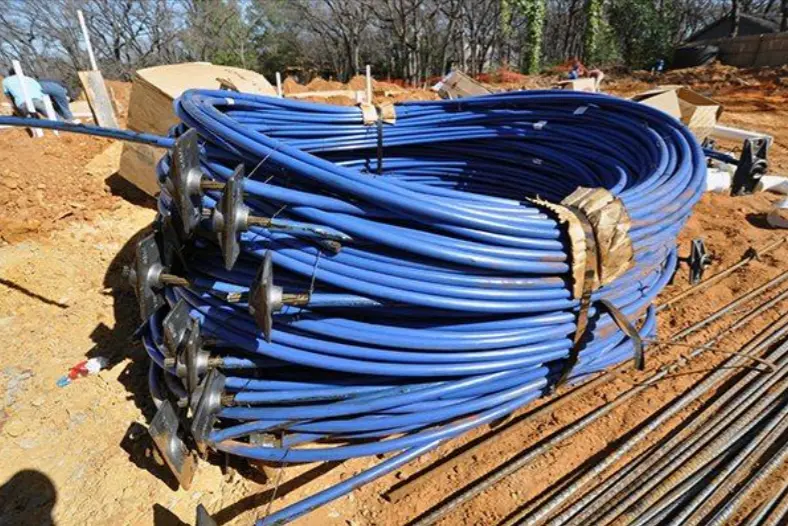
Unlike precast slabs, PT slabs are cast-in-place, meaning the concrete is poured on-site, allowing flexibility in design and construction. Embedded within the slab are post-tensioning cables, made of high-strength steel tendons, which are positioned before the concrete pour and later tensioned. Once the concrete reaches adequate strength (2,500 – 3,000 psi), the cables are anchored and stressed, compressing the slab to enhance its structural integrity. Proper installation and anchoring of PT cables ensure minimal deflection, reduced cracking, and increased load-bearing capacity.
Installation and Sequence of Post-Tensioned Slab Creation
The installation of post-tensioned cables follows a precise sequence to ensure reliable performance. Before any concrete is poured, the post tension tendons are laid out in specific locations and/or patterns. The individual tendons are housed within ducts or sleeves to prevent direct contact with the concrete, to reduce friction during stressing.
The cables are then anchored at their dead end, where they remain fixed, while the live end is left accessible for later tensioning. These are the “spaghetti ends” you can see emerging from the center of a newly poured PT slab to dangle over the side. In truth, the cable can be tensioned from either side, but the dead end generally arrives already seated in its anchor plate from the manufacturer, which will be grouted and capped after tensioning occurs.
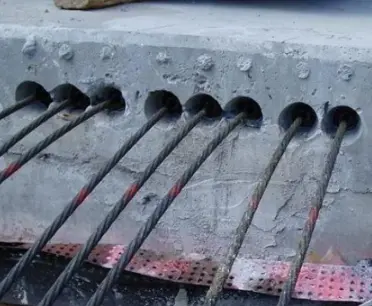
Once the cables are in position – in either a uniform or banded layout – concrete is poured and allowed to cure. The generally required compressive strength for these tendons is 3,500 to 5,000 psi before stressing. Once the concrete has cured, the molds used to frame it are removed and hydraulic jacks are employed at each live end to stretch the tendon to its designed tension level, after which anchors secure the tendons permanently within the slab.
What is the Difference Between Dead End and Live End Anchoring?
Each PT cable features two anchor points:
• The dead end is embedded in the concrete before it is stressed. The dead ends of the tendons are secured by fixed anchor plates, locking them into position to prevent movement.
• The live end is where the “magic” happens because that’s where tensioning occurs. Each live end is exposed post-cure, so that the hydraulic jack can pull them to the necessary force before locking them in place. Once the tendons are secured, the stressing pocket is typically grouted or encased in concrete to protect the anchorage system.
Composition and Specifications of PT Cables & Anchors
Post tension cables are engineered to withstand significant tension forces while maintaining flexibility during installation. They are composed of high-strength steel tendons, ranging in diameter from 3/8" to 1/2", and are encased to reduce friction and shield them from corrosion.
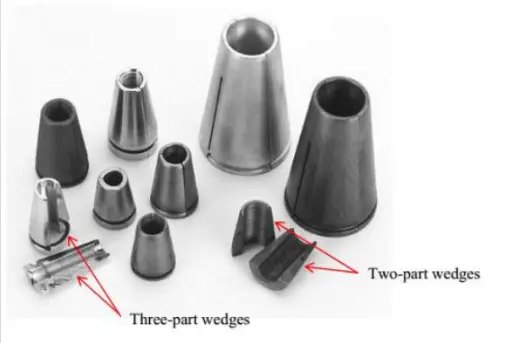
Anchor wedges, plates, and encapsulations are integral components of the system, ensuring a secure attachment to the concrete structure. Grout is applied in bonded post-tensioning systems, to provide added durability and prevent destructive moisture intrusion, particularly in applications requiring long-term exposure to environmental elements.
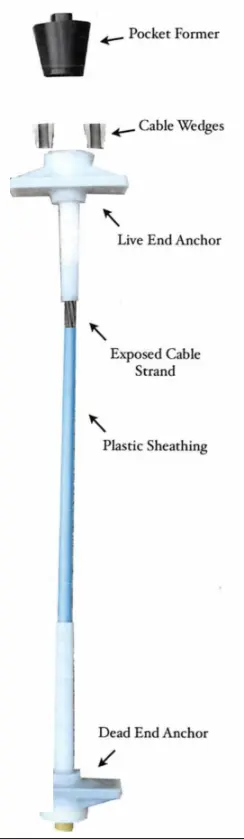
Anchoring Mechanisms and Types of PT Anchors Explained
Anchoring post-tensioned cables requires specialized components to ensure stability and load distribution. At the dead end, fixed anchors secure tendons before tensioning begins, preventing unwanted movement within the slab. The live end allows controlled tensioning, where cables are individually stretched before locking them permanently.
There are several types of PT anchors and components used based on structural requirements.
Pocket formers are devices that form temporary recesses in the concrete to allow for stressing.
Flat plate anchors are frequently used in thin slabs because they offer reliable load distribution while minimizing bulk.
Multi-strand anchors accommodate multiple cables and are common in bridge decks and large-scale concrete structures, due to their need for high-capacity tensioning.
Barrel anchors, which are compact in design, provide effective solutions for space-constrained applications while maintaining performance.
Anchor/Cable Wedges are pieces of tapered, heat-treated, high-strength steel, whose serrations (teeth) penetrate the prestressing steel during the transfer of prestressing force. Anchorage systems sometimes contain two-part or three-part wedges.
Each anchoring method is selected based on load demands, slab thickness, and expected structural movement.
How Do You Reinforce PT Anchors?
Post-tensioned cable anchors experience high localized stresses, so they often require additional reinforcement to maintain stability.
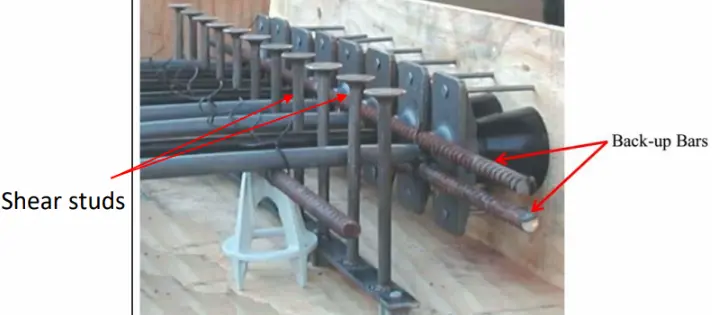
Bursting steel is incorporated around the live-end anchors to mitigate stress concentrations and prevent cracking or failure.
Shear studs enhance anchorage integrity by increasing resistance against movement, especially in applications subjected to dynamic loads.
Back-up bars assist in distributing the force across a broader surface area, reducing stress buildup and improving durability.
Together, these reinforcement strategies ensure the longevity and reliability of post-tensioned slab systems and reduce the risk of long-term degradation.
What Happens After the PT Slab is Tensioned?
When a PT cable is tensioned, it’s generally carrying about 80% of its tensile force. The average PT cable has a tensile strength of 270,000 pounds per square inch (psi). The stressing force for the average ½-inch 270 strand is used, which puts the stressing force at around 33,000 pounds. For comparison, rebar typically yields 60,000 psi.
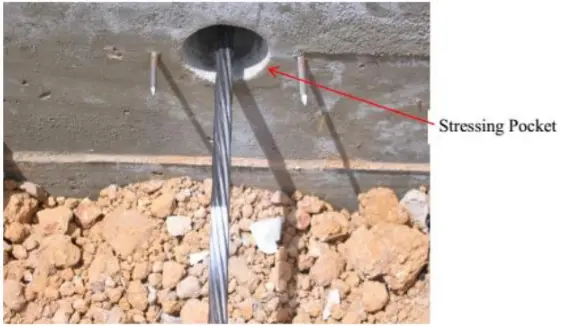
Once tension has been applied to the PT cable, its elongation is measured. A paint mark placed on the cable at end of the slab before it is tensioned allows you to measure the elongation post-tensioning. The area in which this takes place is called the cable’s stressing pocket: the recess created by the pocket that is formed between the stressing or intermediate anchorage and the edge of the concrete that allows nosepiece access for stressing. If you’re checking elongation on the dead end, it is then cut and the pocket grouted over.
Detecting Post-Tensioned Cables Using Ground Penetrating Radar
Ground penetrating radar (GPR) is an effective tool for identifying embedded PT cables within concrete slabs. Unlike the uniform grid-like patterns of rebar reinforcements, post-tensioned tendons display curved profiles, due to their specific placement and stressing process. Anchorage zones, particularly on live ends, generally produce stronger signal reflections. This allows construction engineers and GPRS Project Managers to differentiate between fixed-end anchors, stressing pockets, and the paths of the tendons.
GPR technology is frequently utilized as part of structural assessments, retrofits, and post-construction modifications, to provide contractors accurate locations of all PT slab reinforcements, and to provide safe cutting, coring, and drilling clearances. The cables can also be placed in banded columns for additional reinforcement near pillars and elevator shafts, so it’s vital to know which kind of PT layout you’re dealing with prior to making any cuts into the slab.
The correct anchoring of post-tensioned cables is essential to achieving structural integrity and optimizing the performance of PT slabs. From installation and dead/live end anchoring to reinforcement measures and detection methods, each step in the process plays a critical role in ensuring reliability. Understanding the nuances of post-tensioning is crucial to maximizing efficiency while maintaining compliance with industry standards and keeping work teams safe.
GPRS is the only company in the U.S. that offers the Green Box Guarantee. Since 2017, our Project Managers have maintained a 99.8% accuracy rate in concrete scanning & imaging, so if we mark out a green box that says clear, we guarantee that you will not strike a PT cable or reinforcement. If you do, we’ll pay the material cost to repair it.
Frequently Asked Questions
How does GPR find post tension cables in concrete?
Ground penetrating radar (GPR) is used to locate post tension cables by emitting high-frequency radio waves into concrete and analyzing the reflected signals – that show up on a readout screen as hyperbolas – to identify embedded objects based on their dielectric properties and depth.
Learn more about how GPRS uses GPR, here.
What happens when a post tension cable is accidentally severed?
Severing a post tension cable can cause it to snap back violently due to the high tension, which poses serious safety risks and can compromise the structural integrity of the slab. The average cost to replace a severed post tension cable is between $20,000 and $30,000.
Learn more about GPRS concrete services, here.
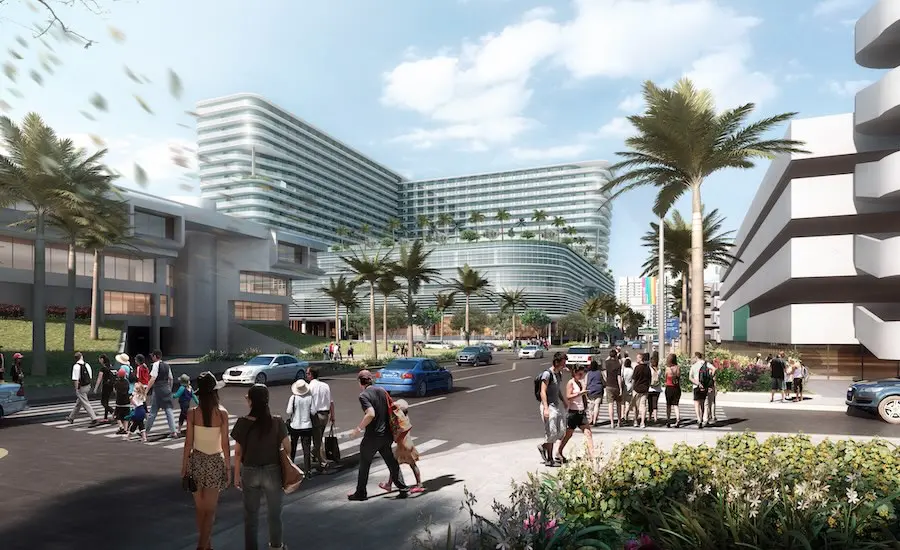
Balfour Beatty Breaks Ground on Miami Beach Hotel
GPRS safety partner Balfour Beatty has begun construction on the Grand Hyatt Miami Beach in Florida.
The $385 million construction services contract calls for the delivery of a 17-story, 996,130 s.f. hotel located at the intersection of 17th Street and Convention Center Drive, which will include 800 guestrooms – including 52 suites – as well as convention and meeting space, and ground floor retail areas.
According to a press release issued by Balfour Beatty, the construction company is undertaking the development on behalf of MB Mixed Use Investment, LLC, a partnership between developers Terra Group and Turnberry.
Once complete, the hotel will serve as the central anchor of the Miami Beach Convention Center District, “transforming the city’s convention center campus into a desirable meeting and convention destination worldwide,” the press release states.
“We are excited to partner with Terra Group and Turnberry, two highly regarded developers in South Florida, to deliver this transformative project for the Miami Beach community,” said Scott Skidelsky, Balfour Beatty’s President of Southeast Buildings Operations. “This project further strengthens our diverse business portfolio in South Florida, where hospitality continues to be an anchor market sector throughout Florida. We look forward to leveraging the experience of our South Florida team, who bring extensive expertise in the successful delivery of high-rise projects, hospitality and convention spaces.”
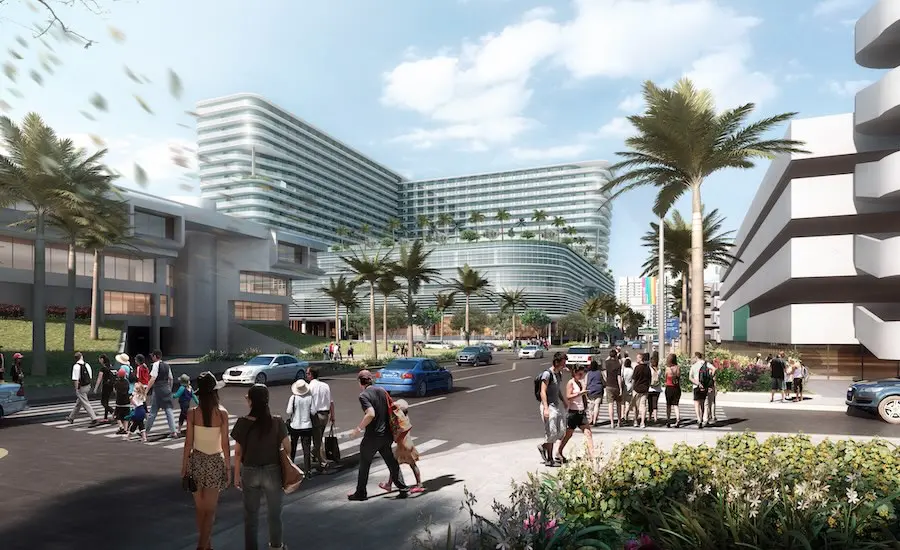
Construction on Grand Hyatt Miami Beach is scheduled for completion in late 2027. Balfour Beatty says the project will employ more than 500 workers at peak construction.
The hotel will feature a resort-style pool deck with panoramic views, five food and beverage outlets including a signature restaurant, a lobby lounge and bar, and fitness and spa facilities. The hotel’s design is being overseen by Arquitectonica and includes a podium with retail and restaurant spaces at street level and a covered drop-off area accessible from two streets.
According to the Miami Beach Convention Center website, the hotel is positioned “to integrate harmoniously with surrounding landmarks such as the New World Symphony and the Miami Beach Botanical Garden.”
“Grand Hyatt Miami Beach is a major investment in our city’s future – bringing jobs, quality year-round tourism, and long-term economic growth,” Miami Beach Mayor Steven Meiner told the MBCC. “Miami Beach remains a sought-after destination for its beauty and growing reputation as a safe, strong, and sophisticated city. This groundbreaking is further evidence that investor confidence in Miami Beach has never been higher.”
“This is a defining moment for our convention and trade show eco system,” added David Whitaker, President & CEO of the Greater Miami Convention & Visitors Bureau (GMCVB). “Grand Hyatt Miami Beach will further strengthen our ability to compete for premier meetings, trade shows and conventions by offering a level of integration and convenience that meeting planners increasingly value. With direct access to our state-of-the-art Miami Beach Convention Center and the vibrant energy of Miami Beach just steps away, this hotel adds an exciting new dimension to the experience we offer.”
According to reporting by Engineering News-Record, funding for the project is being supported, in part, by a $75 million grant awarded through the Miami Beach Redevelopment Agency in late 2024.
Balfour Beatty was selected to construct the hotel in 2023. The firm recently celebrated the completion of the $1.2 billion Broward Convention Center & Hotel and expansion project.
“The company's reputation as a premier hospitality builder in Florida as well as its continued commitment to delivering transformative projects that enhance communities throughout the state were key factors in being selected for this development [in Miami Beach],” Balfour Beatty said in its press release. “Balfour Beatty brings significant hospitality and convention center expertise to the project…”
Whether you’re building a luxury resort in the Sunshine State or a 60,000-seat football stadium in New York State, GPRS supports your construction projects through our comprehensive suite of subsurface damage prevention, existing conditions documentation, and construction & facilities project management services. We offer precision concrete scanning and utility locating, pinpoint-accurate leak detection, NASSCO-certified sewer line inspections, 2-4mm accurate 3D laser scanning, and in-house mapping & modeling tailored to your project’s specific needs.
All this accurate, actionable data is at your fingertips 24/7 thanks to SiteMap® (patent pending), GPRS’ project & facility management application that provides accurate existing conditions documentation to protect your assets and people.
From skyscrapers to sewer lines, GPRS Intelligently Visualizes The Built World® to help keep you on time, on budget, and safe.
What can we help you visualize?
Frequently Asked Questions
Will I need to mark out the utilities that GPRS locates?
GPRS will locate and mark all utilities for you. We have a variety of tools and markers we can use to highlight the locations of utilities, underground storage tanks and whatever else may be hiding.
What is the difference between a design intent and as-built model?
DESIGN INTENT – deliverables will be shown as a "best fit" to the point cloud working within customary standards, such as walls being modeled 90 degrees perpendicular to the floor, pipes and conduit modeled straight, floors and ceilings modeled horizontal, and steel members modeled straight. This will produce cleaner 2D drawings and will allow for easier dimensioning of the scan area. The deliverables will not exactly follow the scan data to maintain design intent standards. Most clients will want this option for their deliverables.
AS-BUILTS – deliverables will be shown as close as possible to actual field capture. If walls are out of plumb, pipes and conduit show sag, floors and ceilings are unlevel, steel members show camber, etc., this will be reflected in the model. This will produce reality-capture deliverables, but 2D drawings may show “crooked” or out of plumb lines, floors will be sloped or contoured, steel members may show camber, twisting or impact damage. Dimensioning will not be as easy due being out of plumbness/levelness, etc. This option should be used when the exact conditions of the scan area is imperative. Clients using the data for fabrication, forensic analysis, bolt hole patterns, camber/sag/deformation analysis, and similar needs would require this option.