Horizontal Directional Drilling (HDD) is a cutting-edge technique used in the installation of underground utilities, such as water, sewer, gas, and telecommunications lines.
This trenchless technology offers a less invasive alternative to traditional open-cut excavation methods. By drilling a precisely controlled, horizontal bore path underground, HDD minimizes surface disruption and reduces the environmental impact of utility installation projects.
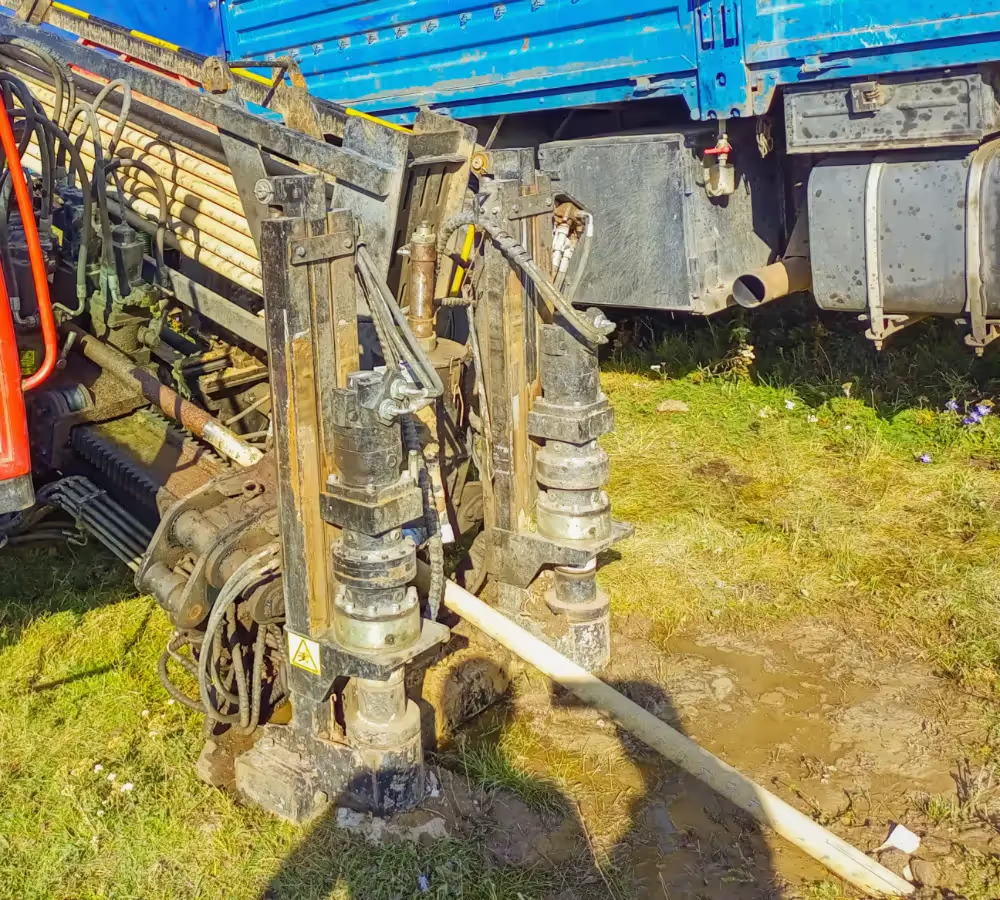
What is Horizontal Directional Drilling?
HDD involves several key steps. First, a pilot hole is drilled along a predetermined path from a launching pit to a receiving pit. The drill head is steered remotely, guided by sophisticated tracking technology to ensure accuracy. Once the pilot hole is completed, the hole is enlarged using reaming tools to accommodate the utility pipe. Finally, the pipe is pulled through the enlarged hole and connected to the existing utility network.
Advantages of Horizontal Directional Drilling
- Minimal Surface Disruption: One of the most significant benefits of HDD is its ability to install utilities without extensive surface excavation. This is particularly advantageous in urban areas, where digging up roads, sidewalks, and landscaping can cause major disruptions to daily life and business operations.
- Environmental Benefits: HDD reduces the need for open trenches, which can disturb ecosystems, waterways, and wetlands. By limiting surface impact, HDD helps preserve natural habitats and reduces soil erosion.
- Cost-Effective: Although the initial setup cost for HDD can be higher than traditional methods, the overall project cost is often lower due to reduced labor, restoration, and traffic management expenses. The speed of HDD installations also contributes to cost savings.
- Versatility: HDD is highly adaptable and can be used in a variety of soil conditions, including sand, clay, and rock. It is also suitable for crossing obstacles such as rivers, highways, and railways, making it an ideal solution for complex projects.
- Enhanced Safety: HDD minimizes the risk of accidents associated with open trenches, such as cave-ins and falling hazards. This makes the work environment safer for construction crews and the public.
Disadvantages of Horizontal Directional Drilling
- High Initial Cost: The equipment and technology required for HDD are more expensive than traditional trenching methods. This can be a barrier for smaller projects or companies with limited budgets.
- Technical Complexity: HDD requires specialized knowledge and training to operate the drilling equipment and navigate underground obstacles accurately. Inexperienced operators can lead to project delays and increased costs.
- Risk of Cross Bore: One of the significant risks associated with HDD is the potential for cross bores, where the new utility line intersects with existing underground utilities, such as gas or sewer lines. Cross bores can cause dangerous gas leaks or damage to existing infrastructure.
- Limited to Certain Lengths and Depths: While HDD is versatile, it has limitations in terms of the distance and depth it can achieve. Extremely long or deep installations may still require traditional methods.
Pros of Using HDD for Sewer Installations
- Preservation of Existing Infrastructure: HDD allows new sewer lines to be installed without disturbing existing roads, sidewalks, and buildings. This is particularly important in densely populated urban areas where surface disruptions can cause significant inconvenience.
- Reduced Environmental Impact: By minimizing the need for open trenches, HDD helps protect natural habitats and reduces the overall environmental footprint of sewer installation projects.
- Improved Efficiency: HDD can significantly reduce the time required to complete sewer installations compared to traditional methods. This is particularly beneficial for projects with tight deadlines or in areas with high traffic volumes.
Cons of Using HDD for Sewer Installations
- Potential for Cross Bores: Despite the advanced tracking technology used in HDD, there is still a risk of cross bores. Thorough pre-construction assessments like GPRS’ Pre and Post-Cross Bore Inspections and careful planning are essential to mitigate this risk.
- Technical Challenges: HDD requires specialized knowledge and experience to navigate underground obstacles and achieve accurate installations. Inexperienced operators can lead to project delays and increased costs.
- High Initial Investment: The cost of HDD equipment and technology can be a barrier for some projects. However, the long-term cost savings and benefits often outweigh the initial investment.
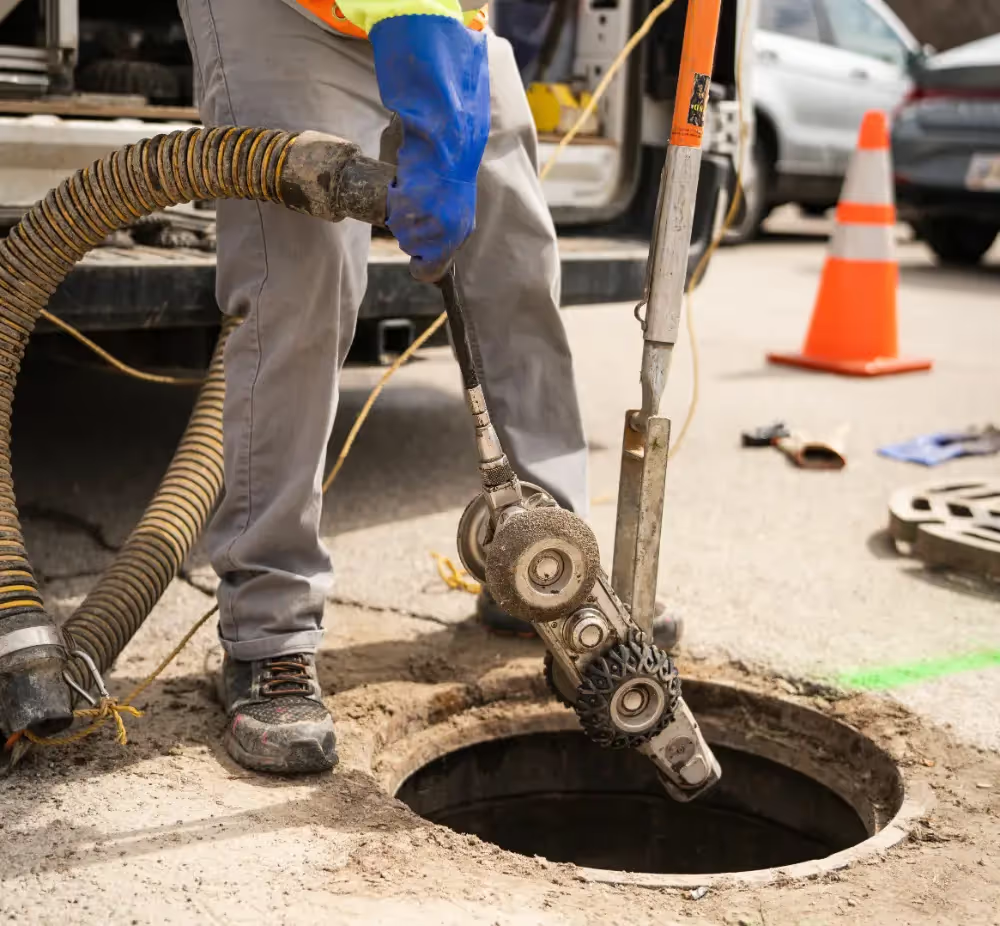
GPRS Services Ensure Successful Horizontal Directional Drilling Projects
When installing utilities underground using HDD, it’s important to know what’s below before breaking ground.
GPRS’ utility locating and video pipe inspection services mitigate the risk of subsurface damage during utility installation projects by ensuring you have a comprehensive understanding of the buried infrastructure on your job site.
Using ground penetrating radar (GPR) scanners and electromagnetic (EM) locating, our SIM-certified Project Managers visualize all buried utilities, underground storage tanks (USTs) and other unseen impediments that would otherwise lead to costly and potentially dangerous damage.
Our state-of-the-art, remote-controlled sewer pipe inspection rovers can be deployed both before and after utility installs occur to mitigate the risk of cross bores, which would otherwise compromise the safety of buried infrastructure, leading to groundwater contamination, service interruptions, or even explosions when gas and sewer lines are involved. It’s vital that we prevent the creation of these dangerous defects and identify and repair any that already existing within our infrastructure.
From skyscrapers to sewer lines, GPRS Intelligently Visualizes The Built World® to keep your projects on time, on budget, and safe.
What can we help you visualize? Click below to schedule a service or request a quote today!
Frequently Asked Questions
What type of informational output is provided when GPRS conducts a utility locate?
Our Project Managers (PMs) flag and paint our findings (aka mark-outs or field markings) directly on the surface we’re investigating. This is the most accurate form of marking and communication when excavation is expected to commence within a few days of service.
We also use a global positioning system (GPS) to collect data points of findings. We use this data to generate a plan, KMZ file, satellite overlay, or CAD file to permanently preserve results for future use. When a higher level of geolocation is required, we can also utilize RTK positioning.
Finally, all our findings are instantly uploaded into SiteMap® (patent pending), GPRS’ cloud-based infrastructure mapping software solution where you can securely access your data 24/7, from any computer, tablet, or smartphone.
Every GPRS customer receives a complimentary SiteMap® Personal subscription with every utility locate.
Will I need to mark out the utilities GPRS locates?
No, GPRS will locate and mark all utilities for you. We have a variety of tools and markers we can use to highlight the locations of utilities, underground storage tanks (USTs), and whatever else may be hiding.
What size pipes can GPRS inspect?
Our elite, NASSCO-certified Project Managers (PMs) can inspect pipes from 2” in diameter and up.
What deliverables does GPRS offer when conducting a VPI?
GPRS is proud to offer WinCan reporting to our video pipe inspection clients. Maintaining sewers starts with understanding sewer condition, and WinCan allows GPRS Project Managers to collect detailed, NASSCO-compliant inspection data. And we not only inspect the interior condition of pipes, laterals, and manholes – we also provide a map of their location. The GPRS Mapping & Modeling Department can provide detailed GPS overlays and CAD files. Our detailed WinCan/NASSCO reports contain screenshots of the interior condition of the pipe segments that we inspect, as well as a video file for further evaluation, documentation, and/or reference.