Concrete scanning and imaging is the process of using specialized, non-destructive equipment to locate and identify objects such as rebar, post tension cables, conduits, and piping embedded within concrete structures. Using ground penetrating radar (GPR) scanning technology, it is possible to scan up to 18”-24” deep into a concrete slab or structure.
This technique allows the construction, engineering, and maintenance industries to assess the structural integrity of concrete and avoid damaging important elements during drilling, cutting, or coring. Concrete scanning ensures the safety of workers and prevents accidents by identifying potential hazards before any work occurs.
Tools of the Construction Trade
Ground penetrating radar (GPR) is the primary tool used by GPRS Project Managers for precision concrete scanning.
Concrete scanning using GPR is different than concrete X-Ray, even though the terms are often used interchangeably within the construction industry. GPR provides a safer, faster, and cheaper alternative to X-Ray for evaluating a concrete structure. While both GPR and X-Ray are non-destructive ways to see inside a concrete slab, GPR requires no prior set-up time on site, emits no radiation, and only requires access to one side of a slab or structure.
For specific structural analysis testing, GPRS uses GPR and Electromagnetic (EM) locating in tandem with Ultrasonic Pulse Velocity (UPV) testing and imaging, tomography, drone photogrammetry, and even 3D laser scanning services to completely assess concrete structures.
Thanks to new technologies and applications, it is possible to “see” inside a post tension slab and assess everything from honeycombing to cold joints in seconds, without drilling, cutting, or sounding. Non-invasive and non-destructive structural analysis tools like UPV and tomography have a much higher accuracy rate in finding and identifying the exact type of concrete deterioration occurring in a building, cause no additional damage, and provide a clear, concise pathway to recommend repairs because they allow you to actually see what is going on inside the concrete.
How Concrete Scanning Works
Precision concrete scanning primarily relies on ground penetrating radar (GPR) to see what’s hidden within a slab or structure.
GPR involves sending a radio wave into a concrete slab and reading the interactions between the wave and any subsurface objects. These interactions are displayed in a reading as hyperbolas - smooth curves lying in a plane.
The color of the hyperbolas varies depending on what type of subsurface object is located. Metallic objects will appear primarily white in a GPR reading, while non-metallic objects will appear primarily black.
The shape of the hyperbolas also varies depending on what was located. Post tension cables, for example, are run in bundles of two-to-five cables, so they typically have a brighter and wider reaction than rebar.
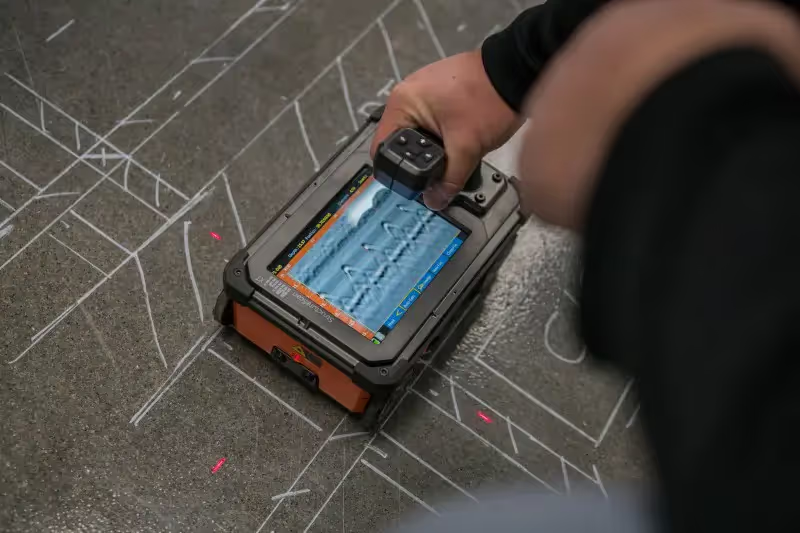
The Right Hands
Above all, the effectiveness of GPR equipment relies on the knowledge and experience of its operator.
The best concrete scanning professionals complete an intensive, months long training regimen known as Subsurface Investigation Methodology, or SIM. Through this program, they receive 320 hours (about 2 weeks) of field training, and log 80 hours (about 3 and a half days) of classroom training where they tackle real-world scenarios in a safe and structured environment. All this training ensures that these professionals can accurately interpret the readings provided by a GPR unit.
In cases where GPR is unable to penetrate a concrete slab for whatever reason, GPRS Project Managers will use complimentary technologies such as EM locating to visualize what’s hidden.
GPRS compiles the collected data to create an accurate map of a property’s underground infrastructure. Our SiteMap® digital facility management platform is a first-of-its-kind tool for storing, annotating, and collaborating with the hyper-accurate infrastructure information collected by our elite Project Managers.
This ensures that the right information is put in the right hands at exactly the right time.
What Can Be Found During a Concrete Scan – and Why it Matters
Scanning concrete with GPR reveals rebar, post tension cables, electrical conduits, voids, and more. This is also an effective method of structural review including concrete slab measurement and rebar spacing.
Concrete scans should occur before any excavation or renovation work begins, because hitting even a single utility line or post tension cable could result in costly and dangerous subsurface damage.
The average total cost of a single utility strike is $56,000. This includes project downtime, repairs, medical costs, and in the worst cases, evacuating surrounding neighborhoods. But the biggest risk of not scanning concrete before coring, drilling, or cutting is not to the pocketbook; it’s to the workers performing the task.
Damage to post tension cables could cause immediate structural failure. Severing a hidden power line could cause electrocution. The lives of your workers are on the line here.
Then there’s your company’s reputation to consider. You don’t want to be known as a contractor who hits utilities.
Timeframe
The time required for a concrete imaging project depends on various factors including the amount of space being scanned, your specific needs, the type of slab and amount of reinforcement present, and more.
GPR scans are typically fast. Data is sent instantaneously from the receiver to an iPad or tablet, and a technician interprets that data to provide same-day deliverables to the client.
Scanning All Types of Slabs
Concrete scanning with GPR reveals the subsurface infrastructure of even the most unique types of concrete slabs, including ribbed and waffle slabs and concrete slab-on-grade.
Both ribbed and waffle slabs are types of reinforced concrete slabs with patterns of ridges or depressions on their bottom surface. These patterns help to increase the strength and stiffness of the slab while also reducing the slab’s weight and saving materials.
Most of the structural support in a ribbed slab is in the joists. This allows the slab to be thin and contain minimal reinforcing.
A waffle slab is a two-way joist system with a grid of depressions or square pockets on the bottom surface of the slab. These pockets are created by construction of a system of beams in both directions underneath the slab, forming a grid pattern. The beams intersect at regular intervals, creating pockets or depressions. The edges of the slab rest on the beams, increasing its load-carrying capacity.
GPR’s ability to visualize what’s inside and under concrete slab-on-grade is one of its biggest advantages over X-Ray scanning technology. As the name suggests, slab-on-grade is a type of concrete slab poured directly onto the ground. A stone base is often placed between the slab and the native soil. With only one side of a slab-on-grade accessible, it is impossible to evaluate this type of slab with X-Ray.
A concrete slab-on-grade typically contains little-to-no rebar, as it does not require much structural support due to it being poured directly onto the ground. In contrast, a raised slab should be expected to contain a lot of rebar.
A highly trained concrete scanning technician will be able to determine what types of subsurface obstructions they should be looking for depending on the type of slab they are evaluating.
The GPRS Difference
Sometimes it’s what’s inside a slab that presents a unique challenge.
That was certainly the case when GPRS’ Jaime Gamache was called in to define the structural reinforcement and rebar pattern in the concrete of a pre-World War I munitions factory for The Richmond Group, so the building could be renovated into an expansive health care facility right on the Charles River in Watertown. Using his industry-leading training, and state-of-the-art GPR scanner, Gamache was able to determine that the rebar inside the factory’s slab was what’s known as circumferential or S.M.I. System reinforcement.
This extremely rare design was developed by Edward Smulski, a New York City engineer who patented it in 1916. The system is also sometimes referred to as the spiderweb pattern and combines concentric circles and straight rebar running through them in a starburst pattern.
The idea behind Smulski’s system was that it could support more weight than a standard two-way or four-way slab system, where only straight rebar is used. There is some speculation that his circular bent rebar construction model was “nonsensical,” but the federal government determined it was worthwhile to use in new construction before WWI.
Bent rebar is more expensive and complicated to produce, and according to Kloeckner Metals, almost impossible to remove from the slab when demoing, which may also have led to the downfall of this complex pattern. Another potential reason for its retirement is that it used more rebar than a two-way or four-way pattern, and as the nation veered from WWI into WWII, metals were needed more for munitions than for homeland construction projects.
If Gamache had not been dedicated to solving the puzzle, this very rare and incredibly strong support structure would have caused chaos when construction crews attempted to drill or cut into the slab.
It’s the professionalism and dedication of GPRS’ SIM-certified Project Managers that make it possible for GPRS to offer its Green Box Guarantee, which states that when we scan your concrete slab and provide you with a green box marked “CLEAR,” you know that you can safely cut, core, or drill in that space with 99.8% certainty that you will not hit conduit, rebar, or any other dangerous or costly obstructions.
Through our use of GPR, EM locating and other technologies, and our dedication to industry-leading training and standards, GPRS is able to provide services such as precision concrete scanning to Intelligently Visualize The Built World™ for our clients and customers. And with a nationwide footprint, you can rest assured you always have these services near you.