How Do You 3D Laser Scan a Building?
To get precise measurements of a building or site, the best method is to 3D laser scan it. 3D laser scanning captures every as-built detail of your site – the structural, architectural, and MEP features, plus underground utility and concrete markings – at incredible speeds with unparalleled accuracy. 3D laser scanning delivers exact building dimensions, locations, and layout, supported by 3-dimensional imagery, making it ideal for building or construction design and project management applications.
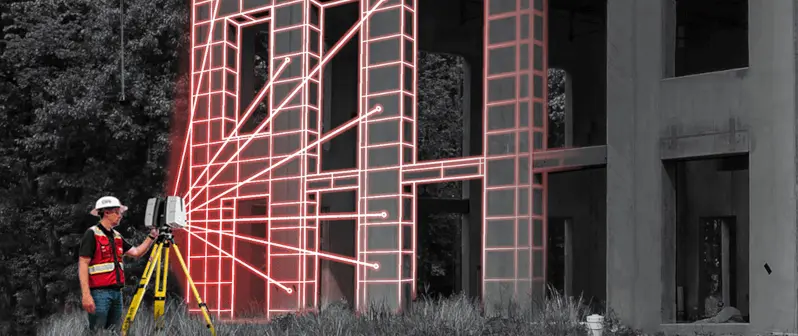
What is the Process of 3D Laser Scanning a Building?
A Project Manager will position the laser scanner at multiple locations around the site, capturing millions of measurements and documenting every project detail into a digital map or point cloud. 3D scanning is only as good as the person positioning the scanner. The Project Manager must be trained and have project awareness. It is not always as simple as pressing a button and moving onto the next position in a random fashion, although it may look like that at times.
Here are the Steps Involved in 3D Laser Scanning a Building:
- Select a Laser Scanner: A laser scanner is selected based on the size and complexity of the building, project timeline, and the level of detail required.
- Mount the Scanner to a Tripod: Set up a stable tripod to mount the laser scanner. This ensures accurate and consistent scanning.
- Calibrate the Scanner: Perform a calibration procedure to ensure accurate measurements. This often involves scanning a known target or reference object.
- Define the Scan Area: Divide the building into manageable sections, considering factors like size, complexity, and accessibility.
- Establish Control Points: Identify and mark control points in the building. These points act as reference markers to merge individual scans into a cohesive model.
- Capture Site Data: Start the scanning process. The laser scanner emits laser beams that bounce off surfaces and are recorded by the scanner's sensors. For each pulse, the distance between the scanner and object is measured by determining the elapsed time between the sent and received pulses. The laser scanner collects millions of data points, creating a point cloud representing the building's geometry. Be sure to ensure sufficient overlap between individual scans to facilitate accurate alignment during post-processing.
- Register the Scans: All scans are registered together during post-processing, removing the noise and setting the coordinate system to provide the most precise measurements.
- Register the Data: Use specialized software to merge and align the individual scans into a unified point cloud. This process involves identifying common features and control points.
- Clean and Filter the Data: Remove any unwanted noise or outliers from the point cloud to enhance data quality.
- Convert the Data to CAD, Maps, and Models: Once the point cloud is refined, it can be processed into 2D CAD drawings, 2D utility maps, 3D BIM models, 3D mesh models, TruViews, and virtual tours to any level of detail.
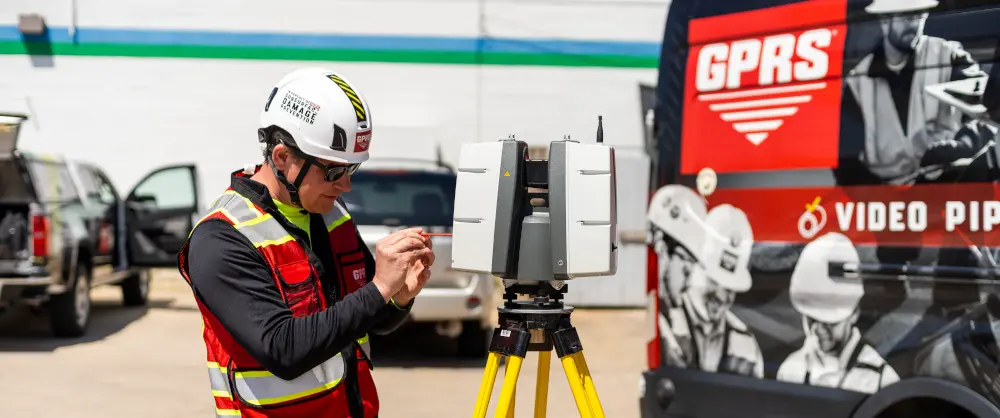
Frequently Asked Questions About 3D Laser Scanning
What is LiDAR Scanning?
LiDAR, or Light Detection and Ranging, is an active remote sensing system that can be used to measure objects. The process of LiDAR scanning occurs when the scanner transmits a laser beam and hits an object, at which point the light is reflected back and captured by the scanner. Because light travels at a constant speed, the variation can be calculated as a distance; therefore, producing an accurate point in space.
LiDAR scanners repeat this process up to a million times a second, creating a 3D image made up of millions of data points referred to as a point cloud. Point clouds are an accurate map of the shape and size of the building or site. Each point of the LiDAR scan will be converted to a pixel with a known x, y, and z coordinate.
Why is a Point Cloud Important?
Point clouds provide powerful and dynamic information for a project. By representing spatial data as a collection of coordinates, point clouds deliver large datasets that can be mined for information. The visualization and analysis from point cloud data is invaluable for decision making.

Does the Data Need to be Processed?
Once laser scanning is complete, the data needs to be processed or registered. All of the individual scans taken by the Project Manager need to be aligned and fit together. The registration process is similar to putting together a digital 3D puzzle, overlapping scan data and joining together the scan points. Once the scans are all registered, the combined deviations between the registered scans are totaled to provide overall survey accuracy. Leica ScanStations can tie to survey control and achieve 2-4mm accuracy.
What Can I Do With the 3D Scan Data?
Some clients are able to utilize the point cloud data directly. 2D drawings and 3D BIM models can be created from the registered point cloud data by the GPRS Mapping & Modeling Team. A client’s 3D model can also be imported, overlaying it against the point cloud, this can save time and is a cost-effective way of identifying clash detection without having to model the whole building or site.
Many software applications also allow you to create a 3D mesh model of the scanned data. This is a process that converts the point cloud into a digital solid object by triangulating points to form a surface. Meshes can then be processed as a 3D solid instead of a point cloud and have multiple uses in 3D CAD software.
TruViews can also be created. They are 3-dimensional photographs overlaid on top of the point cloud data. A TruView let’s you navigate a site, add markups and GeoTags, plus visualize designs in context to check design models against real work conditions.
Virtual tours allow your team to virtually walk-through a site or facility in minutes, take basic measurements, estimate clearances and distances, and add digital notes.
3D scan data can be used for visualization, analysis, design, construction, renovation, prefabrication, and facility modifications.
What are the Benefits of 3D Laser Scanning?
Buildings or sites are captured in high detail the first time, eliminating the need for return visits. The high speed data collection from 3D laser scanning a site expedites time-sensitive projects or those that require minimal disruption. Point cloud datasets are dimensionally accurate, measurable, and shareable, optimizing the efficiency of time spent during project planning and execution. Communication is improved, teams can discuss plans while each has access to the same information, creating a more dynamic work environment. Laser scanning allows you to minimize risk, design confidently, and avoid change orders.
How Long Does 3D Laser Scanning Take?
An individual scan usually takes between 1-2 minutes. The Project Manager will set up the scanner in multiple positions around the building or site. Most building scanning projects can be laser scanned in as little as a couple of hours or larger sites in a few days. Entire facilities or campuses can take several weeks to capture the entire site, but most projects are scanned in a few hours or one day.
How Much Does 3D Laser Scanning Cost?
The cost of 3D laser scanning a building depends on the size and complexity of what is being scanned. Modeling costs are based on the size of the area being modeled, level of detail, and features needing to be included. 3D laser scanning can bring tremendous cost savings to a project. Quality data can lead to a faster design process and fewer change orders, saving time and money. 3D laser scanning could lead to significant savings over the course of a project.
Request a quote for 3D laser scanning services.
Why Choose GPRS for 3D Laser Scanning?
You can trust the GPRS team to provide the best experience in laser scanning by walking you through the entire 3D laser scanning process from pre-planning through project completion.
We offer a consultative approach to project management, working with you to ensure our data, maps, and models are the perfect solution for your project. The data delivered is accurate within millimeters, and the maps and models provide complete as built and location data.
GPRS services a wide variety of industries, including architecture, engineering, design, construction, oil & gas, facility management, historical preservation, stadium & theater, education, healthcare, water & wastewater, energy & utility, and multimedia & entertainment industries.
Our elite team of Project Managers is required to complete an extensive training program before performing field services on your job site. Every Project Manager completes 80 hours of classroom training and 320 hours of field mentoring.
We ensure you have all the information you need to get the job done right, delivering accurate as built data to expedite project planning and reduce change orders, delays, and costs.