How Does a 3D Laser Scanner Work?
A 3D laser scanner works by emitting laser beams onto a surface, measuring the time or phase shift of the reflected light, and recording data points to create a precise 3D digital representation of the object or environment.
To 3D laser scan a building, multiple scans are taken from different positions to capture all angles. The scanner collects millions of data points, creating a point cloud where each point has X, Y, Z coordinates to map the building's layout accurately. The outcome of the 3D laser scanning process is a realistic true-to-life digital model of the object or building that was being scanned.
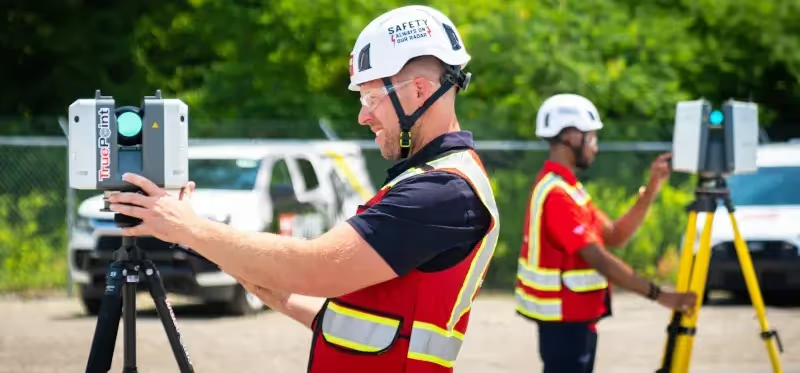
What Are the Methods of 3D Laser Scanning?
A laser scanner calculates the distance between itself and the object's surface using one of these four methods:
1. Time of Flight 3D Laser Scanning
Overview: Measures the time it takes for the laser pulse to travel to the object and reflect back, using the speed of light to calculate distance.
Time of Flight 3D laser scanners measure distance by calculating the time it takes for a laser pulse to travel to an object and reflect back to the sensor. By emitting a pulsed light signal and recording the return time, the scanner accurately records precise distance calculations. By rotating the laser and sensor, usually around a mirror, Time of Flight scanners can capture full 360-degree scans, enabling comprehensive spatial mapping.
Below are examples of Time of Flight Laser Scanners available in the market:
- Leica C10 Laser Scanner
- Leica RTC360 Laser Scanner
- Trimble TX8, TX6, and X7 3D Laser Scanner
- Riegl VZ-400
2. Phase Based 3D Laser Scanning
Overview: Compares the phase difference between the emitted and reflected laser beam to determine distance with high precision.
A phase based laser scanner is a type of 3D laser scanner that determines the distance to an object by measuring the "phase shift" of a constant laser beam that is emitted in multiple phases, rather than measuring the time it takes for the light to travel back, like in a time of flight scanner. The laser emits a patterned light wave, and when it reflects off an object, its phase shifts. The scanner measures this shift to calculate the distance to the object. This method allows for high accuracy and fast data capture, but typically has a shorter range compared to other laser scanners.
Below are examples of Phase Based Laser Scanners available in the market:
- FARO Focus M 70
- Faro Focus 3D
- Leica RTC360
- Leica BLK360
- Leica HDS7000
3. Laser Triangulation
Overview: Projects a laser onto the surface, and a sensor captures the reflection at a known angle to calculate distance using trigonometry.
In laser triangulation, a laser beam is projected onto a surface, and the reflected light is captured by a sensor to determine distance. This 3D laser scan technology applies the principles of trigonometry by measuring the displacement of the laser dot or line in the camera's field of view to calculate precise distances. Triangulation works by using geometric calculations based on the angle of the laser beam from a known position, forming a "triangle" to determine distance. This technique provides high accuracy at close ranges, though it has a shorter range compared to time of flight and phase based scanning technologies. This method provides high accuracy at close ranges, making it ideal for applications like industrial inspection and reverse engineering.
Below are examples of 3D Laser Triangulation scanners:
- Faro’s Focus3D
- MakerBot Digitizer
- BQ Ciclop
- Matter Form
4. Photogrammetry
Overview: This method captures multiple images of an object from different angles, then uses software to reconstruct the 3D shape.
Photogrammetry is the process of capturing images and stitching them together to create a digital model of the physical world. A 3D Matterport camera, which can also be equipped with LiDAR, can digitally document buildings, facilities, and sites with high-resolution images. Photogrammetry can be mounted on tripods, worn as mobile devices, flown by drones, or attached to cranes for aerial views. The process captures 4K HDR photographs from multiple angles to create a 360° site view, and LiDAR technology can record precise three-dimensional coordinates (X, Y, Z) in the form of a point cloud.
Below are examples of Photogrammetry cameras:
- Matterport Pro3
How is 3D Laser Scan Data Registered?
A 3D laser scan point cloud is registered by aligning multiple scans with overlapping areas into one coordinate system. Unwanted noise, like reflections or background clutter, is cleaned or deleted using software like Autodesk Recap. Once cleaned and aligned, the scans are merged into a single, accurate 3D point cloud. Proper registration ensures that measurements taken from the 3D laser scans are accurate and the data can be exported for use in CAD or BIM applications like Revit or AutoCAD.
What Can I Do with the Point Cloud?
The 3D laser scan technology mentioned above captures comprehensive as-built data of a building or site’s exterior and interior, including structural elements, architectural details, utilities, dimensions, surface features, and surrounding terrain.
Point cloud data can be transformed into custom 2D CAD drawings, 3D BIM models, 3D mesh models, TruViews, digital twins, 3D virtual tours, and floorplans, offering precise measurements and detailed visual data. GPRS uploads custom deliverables to SiteMap®, a free cloud-based digital storage platform.
3D laser scan point clouds provide architects, engineers, and contractors with highly accurate, real-world data for design, construction, and renovation projects. By capturing millions of precise measurements, point clouds create a detailed 3D representation of existing conditions, reducing the need for manual measurements and minimizing errors. Architects use this data to integrate designs seamlessly into existing structures, engineers rely on it for structural analysis and clash detection, and contractors benefit from improved planning, cost estimation, and quality control. This technology enhances efficiency, reduces rework, and ensures better decision-making throughout the project lifecycle.
Learn more about 3D laser scan point clouds.
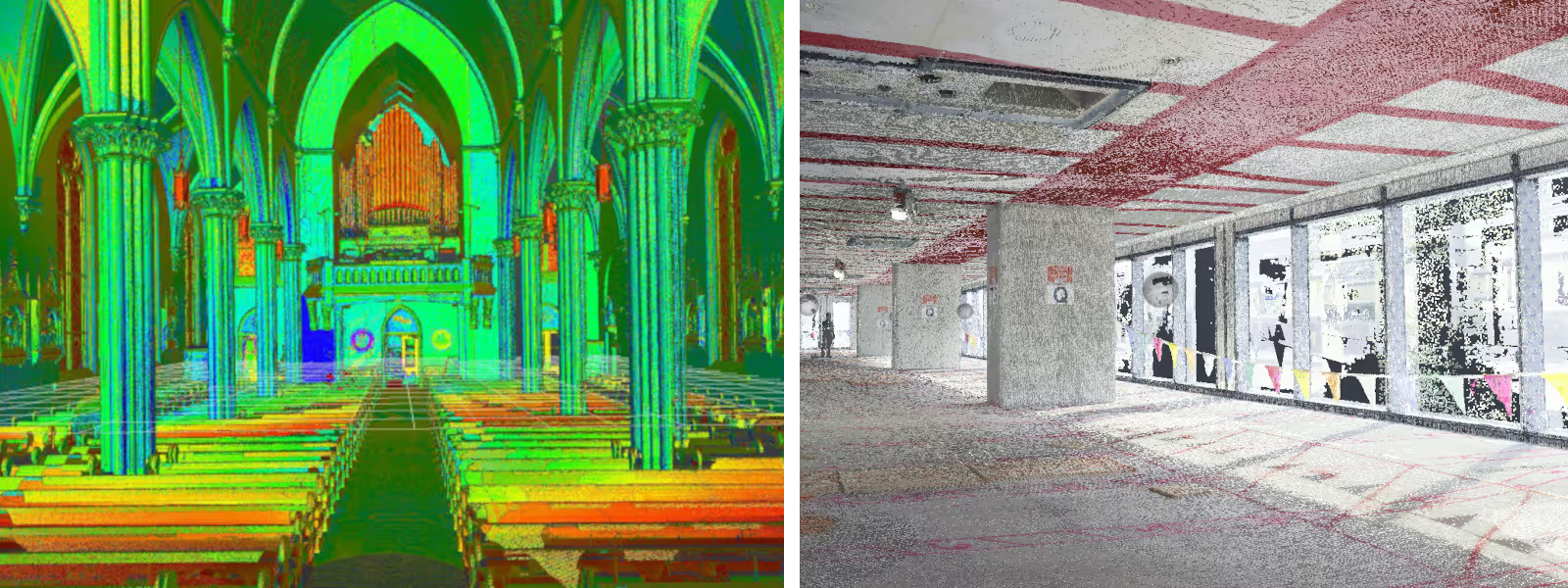
What Are the Benefits of 3D Laser Scanning?
3D laser scanning has become an indispensable tool across the architecture, engineering and construction industries due to its ability to capture highly detailed and accurate 3D site data. Here are some of the key benefits of 3D laser scanning:
- Fast Data Collection: Laser scanning quickly captures detailed and comprehensive digital records of buildings or sites, making it effective for applications where precision is critical, such as construction, engineering, architecture, manufacturing, healthcare, automotive, oil and gas, and historical preservation, among others.
- Dimensional Accuracy: A single laser scan captures millions of 3D data points per second, providing incredibly rich detail of a building or project site. Datasets are dimensionally accurate, measurable and shareable, expediting project planning and execution.
- Eliminates Revisits and Disruption: Sites are captured in high detail the first time, eliminating the need for return visits. High speed data collection expedites projects that require minimal disruption.
- Reduces Costs and Change Orders: Accurate design plans are produced from the start expediting field work and reducing change orders, delays and costs.
- Safe and Non-Contact: 3D laser scanners collect data on tripods from a distance in hard-to-reach or hazardous locations, keeping workers out of harm’s way. The non-intrusive nature keeps historic sites and fragile artifacts untouched.
- Visualization: Data from 3D laser scans can be used to create highly realistic visualizations and can be transformed into 2D drawings and 3D models, aiding in the design, analysis, and communication of complex structures and spaces.
- Improves Communication: Teams can discuss plans while each has access to the same information, creating a more dynamic working environment.
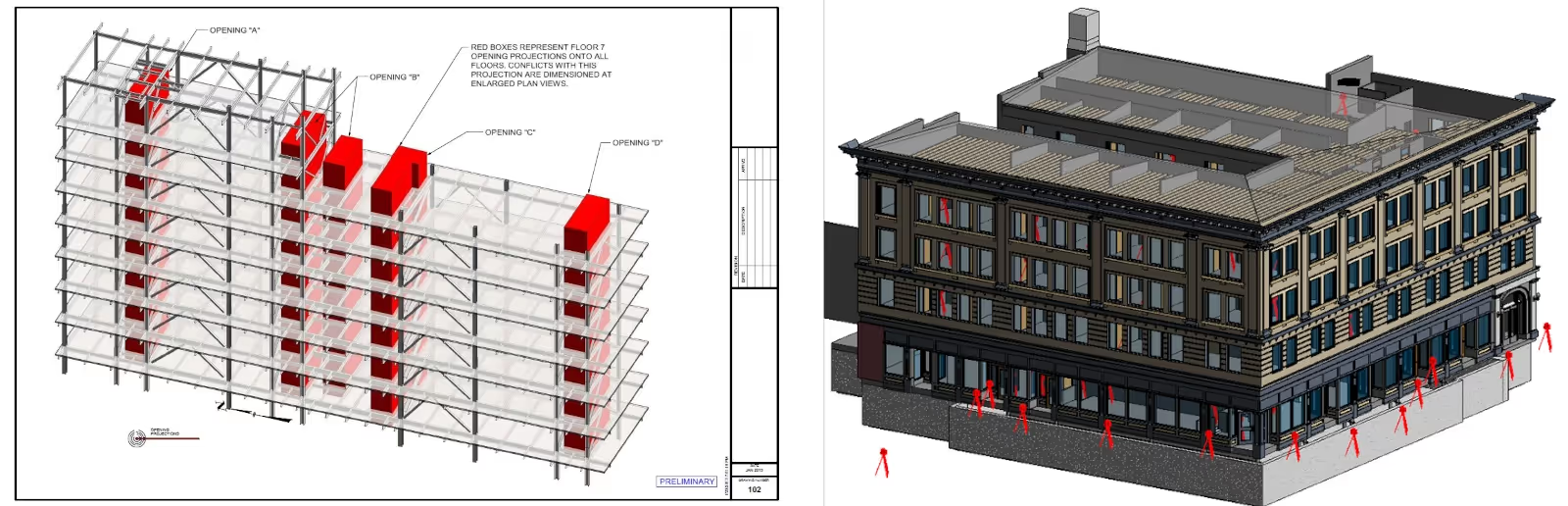
Why Use GPRS 3D Laser Scanning Services?
3D laser scanning is fast, accurate and reliable. Three-dimensional data provides exact measurements of sites with a level of confidence and speed not possible with traditional tools. There’s no better way to drive decision making than to have accurate and intelligent, real-time data.
GPRS 3D Laser Scanning Services provide 2-4mm accuracy by capturing 2 million data points per second, for efficient planning, design, and construction. Our in-house Mapping & Modeling Team can export your data to create accurate existing condition as-builts – above and below ground – to give you the accurate information you need in a format you can easily work with and share to keep your projects on time, on budget, and safe.
Learn more about the 3D Laser Scanning Process.
Learn more about 3D Laser Scanning Equipment.
Learn more about 3D Laser Scanning Deliverables.
GPRS 3D Laser Scanning Services reduce the risk for you, your team, and your assets with accurate as-built data to:
- Expedite project planning
- Reduce change orders
- Eliminate budget overruns
- Maintain project schedules
- Protect your reputation