“When a bridge closes, it costs Americans time and money, disrupts supply chains across the region, and sometimes cuts off entire communities from vital resources.” – U.S. Transportation Secretary Pete Buttigieg.
How One Bridge’s Story Illustrates a Nationwide Problem
On December 12, 2023, Rhode Island’s highway authority, RIDOT, suddenly closed the Washington Bridge, effectively blocking access across the Seekonk River to some 96,000 vehicles daily.
The Boston Globe reported that commutes which normally took 20-30 minutes were now two to four-hour journeys for those who had to make their way into Providence, Warwick, or Boston from the East Bay area.
So, why would RIDOT close the bridge without notice? Because the concrete bridge structure is failing, and has been in extreme decay for more than five years, according to RIDOT’s own report from 2019. At that time, they rated the bridge “in poor structural condition” and stated that it has been “forced to operate well beyond the bounds of its anticipated capacity for decades.”
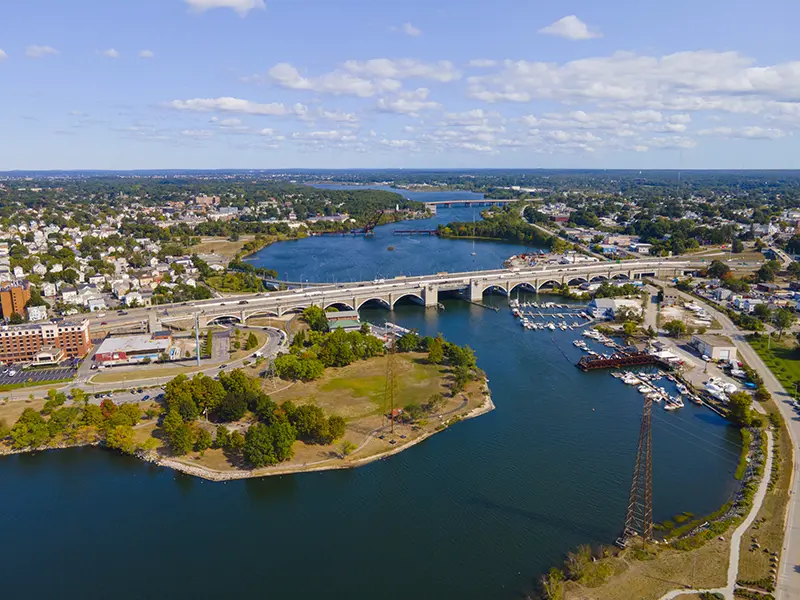
The Washington Bridge, originally constructed as a bascule bridge in 1930, and reconceived as an arch bridge in 1968, had been partially closed for three years while it underwent a $78-million reconstruction effort.
ENR reported the specifics on the December 2023 closure, stating that an engineer found failing anchor rods and deteriorating structural components on the 1,671-foot-long bridge. Which led RIDOT officials to find “other deficiencies that were happening in a kind of cascading way,” requiring immediate closure.
An engineering report prepared for RIDOT found that the cascade of problems showed “evidence of deterioration and failure through corrosion and shearing.” And a 2017 below-deck inspection showed exposed rebar, rust, cracking, hollowing, efflorescence, and isolated spalls (delamination) throughout the concrete structure.
What makes the Washington Bridge closure noteworthy isn’t its suddenness, but the fact that most steel-reinforced concrete bridges in the United States are in a similar state of disrepair.
In fact, many of the 400,000 concrete bridges in the U.S. are past their lifespan, which is estimated at 75 – 80 years.
That is why the Bipartisan Infrastructure Law established the Bridge Investment Program. The Program earmarks $40 billion over a five-year period to “help ensure some of the nation’s most important bridges remain safe and operational.”
If you are an engineer, municipal planner, or general contractor engaging in concrete bridge repair and construction, GPRS is here to support you. Our 99.8% accuracy rate in ground penetrating radar (GPR) concrete scanning provides important infrastructure data to help you plan demolition, repair, construction, and maintenance of all kinds of reinforced and post-tension concrete structures.
How are Most U.S. Concrete Bridges Made?
There are four types of bridges commonly used in road construction in the United States:
- Beam
- Arch
- Cable-Stayed
- Suspension
Suspension bridges, like the iconic Golden Gate Bridge in California, the Brooklyn Bridge in New York, or The Mackinac Bridge in Michigan may get all the attention for their heights and unusual structures, but most highway and road bridges in the United States are beam bridges, followed by arch bridges like the Washington Bridge in Rhode Island.
One thing all the bridge types have in common is their composition of steel and concrete, which means they are all at risk of decay due to corrosion.
More Than 60% of All U.S. Bridges are Beam Bridges
Beam bridges suffer the most failures, accounting for 45% of all bridge structural failures. Arch bridges are in second place in the failure sweepstakes at 20%, meaning that 65% of all bridge structural failures occur in the two most common concrete bridge structures.
A beam bridge refers to the horizontal beam of the bridge that is supported on either end by a vertical pillar. A single beam bridge is knowns as a supported beam bridge. One that contains more than one beam to traverse the area is called a continuous beam bridge.
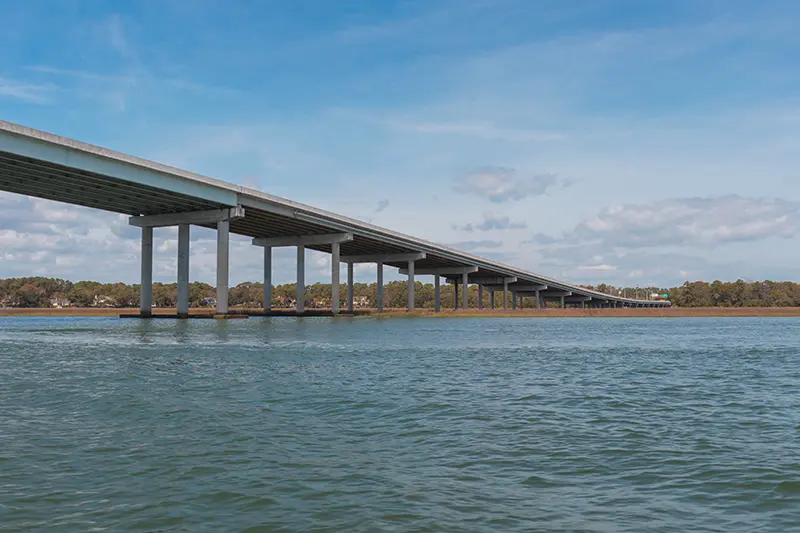
How Does a Beam Bridge Work?
In architectural design, a beam is installed to horizontally carry vertical loads by bending, which causes horizontal compression on its top, while the bottom experiences horizontal tension. The supports on either end of the beam act to transfer the load compression vertically to the foundation of the pillars.
Due to the bending required for a beam bridge, supports are generally placed every 250 ft. to ensure structural integrity.
How is a Beam Bridge Constructed?
Concrete footings are generally cast first, as piers and abutments to support the load. Then steel beams are placed on top. Once the steel beam structure has been placed, a concrete deck can be cast on top. Metal is usually welded to the top of the steel beam flanges, around which the concrete is poured. The metal welds form a connection between the beam and the slab to create a composite structure that is more flexible and more structurally strong than either material alone to manage the load.
There are four main types of steel beams used in these bridges:
- Rolled Beams
- Box Beams (Adjacent or Spread)
- Plate Girders
- I-Beams
Each type of steel reinforcement is similar in construction cost and maintenance cost per square foot, but the concrete I-beam combination has the shortest life-span – with only a 44.3% probability of surviving more than 75 years, according to Short Span Steel Bridge Association (SSSBA) as reported in Modern Steel Construction.
What Causes Concrete Bridge Decay?
According to a 2023 article on non-destructive inspection of reinforced concrete bridge defects in Buildings, “Reinforced concrete bridges are referenced as the most common type of structures in transportation networks. Their damage types include surface and subsurface defects such as corrosion, delamination, surface cracks, deformation, spalling, scaling, efflorescence, erosion, voids, moisture, etc.”
Many of the defects in that list were also listed in the 2017 report on the Washington Bridge. The majority of those defects can be seen in a structural review of the bridge (i.e., the white dust of efflorescence, cracking, and exposed rebar caused by corrosion and rust), and can be seen by the naked eye or drone photogrammetry in difficult to reach areas.
Some concrete deterioration occurs simply because a span of steel-reinforced concrete is bridging water. Water and even humid air can erode concrete and corrode the metal supporting it, inside and out. Other major stressors on bridge structural integrity are carbon dioxide, de-icing solution and salt penetration into the concrete, and traffic load.
How Does Concrete Corrosion Occur?
According to one publication, corrosion is responsible for as much as 90% of all reinforced concrete damage. It’s even got a catchy name, concrete cancer, because it often erodes the structure from within and by the time it is detectable to the human eye, the damage is done.
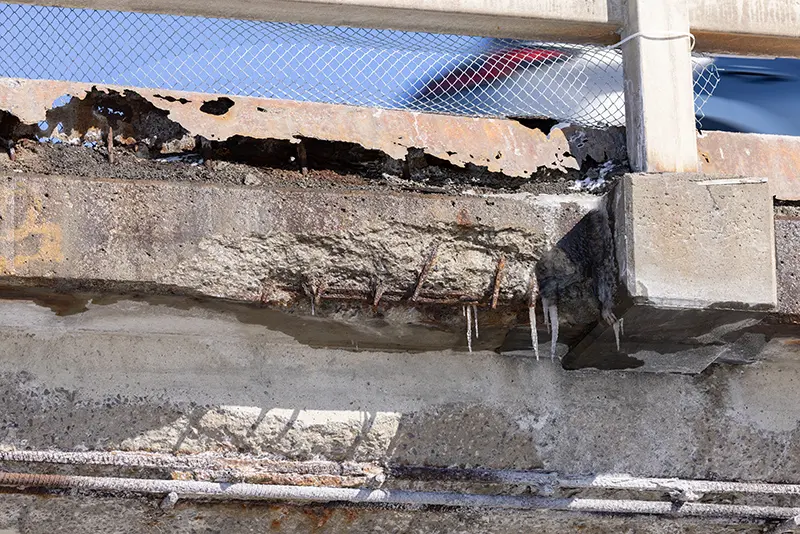
When chlorides or other harmful substances reach the rebar or other steel reinforcement in a concrete slab, they cause a chemical reaction that releases the iron and oxygen ions that create rust. Rust takes up more space than the steel, so rusted rebar expands pressure within the slab, which causes the concrete to crack. When the cracks reach the surface of the slab, they allow more air and substances to reach the reinforcements, speeding up the corrosive process even more.
Can You Stop Concrete Corrosion?
While there are protective coatings you can spray on concrete surfaces to attempt to prevent corrosion and protect concrete from corrosive elements, the reality is that concrete deterioration cannot be stopped or reversed. It must be repaired, and that means extensive construction.
That is why, as of August of 2023, some 222,000 U.S. bridges are in need of repair, and why the Bridge Investment Program, and matching state and private funds, are so important to preserving America’s transportation infrastructure.
When repairing steel-reinforced concrete structures of all kinds, there are a multitude of factors that you must take into account. It is important to be sure you don’t compound an already challenging situation by cutting, coring, or drilling into a concrete slab without complete confidence that you won’t hit reinforcements, create additional damages, or cause an accident or injury.
It’s GPRS’ mission to Intelligently Visualize The Built World® for our customers. What can we help you visualize?