Pre-construction risk assessments are a critical part of any construction project.
These evaluations help identify potential hazards, streamline project planning, and ensure the safety of workers, stakeholders, and the surrounding community.
Failing to conduct a thorough risk assessment can lead to costly delays, safety incidents, and legal challenges.
Why Pre-Construction Risk Assessments Are Essential
Before breaking ground on a construction project, it’s crucial to understand the potential risks associated with the site, the design, and the construction process itself. Pre-construction risk assessments serve several key purposes:
- Ensuring Worker Safety: Identifying hazards in advance helps implement measures to protect workers and reduce accidents.
- Compliance with Regulations: Risk assessments ensure that projects meet local, state, and federal safety standards.
- Cost and Time Management: By identifying risks early, teams can plan for contingencies, avoiding unexpected delays and budget overruns.
- Preserving Community and Environmental Health: Understanding environmental impacts and community concerns minimizes negative effects and builds trust with stakeholders.
- Improving Project Outcomes: Proactively managing risks contributes to smoother project execution and higher-quality results.
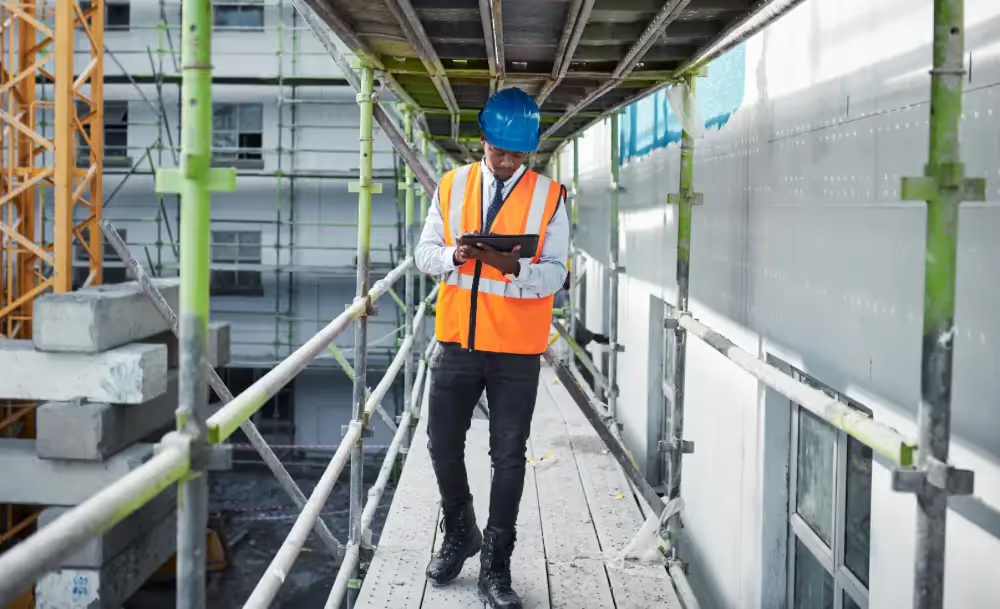
Key Steps in Conducting Pre-Construction Risk Assessments
Define the Scope of the Assessment
Begin by clearly defining the scope of the assessment. This involves identifying:
- The type and size of the project
- Key stakeholders, including contractors, subcontractors, and clients
- The location and its specific challenges, such as urban, rural, or environmentally sensitive areas
By understanding the scope, you can tailor the risk assessment to address the unique aspects of the project.
Assemble a Qualified Team
Risk assessments require input from a multidisciplinary team, including:
- Project managers
- Safety officers
- Engineers and architects
- Environmental consultants
- Legal advisors
Each member brings valuable expertise to identify and address risks from different perspectives.
Conduct Site Inspections
Visiting the project site is essential to identify physical hazards. During the inspection, look for:
- Uneven terrain, sinkholes, or unstable soil conditions
- Proximity to utilities, such as power lines or gas pipelines
- Environmental concerns, including wetlands, wildlife, or hazardous materials
- Accessibility challenges for equipment and personnel
Document all observations and collect relevant data to inform your risk analysis.
GPRS Project Managers take a collaborative approach to your projects, which includes conducting pre- and post-job walks to ensure clear communication of both your needs and our deliverables. Click here to learn more.
Analyze Design and Engineering Plans
Review architectural and engineering plans to identify potential risks. Consider:
- Structural integrity: Are the materials and designs suitable for the intended purpose?
- Fire safety: Does the design include appropriate fire suppression systems?
- Accessibility: Are provisions made for safe entry, exit, and movement on-site?
- Load capacity: Will the site and structures support the intended loads?
Collaborate with design professionals to address any issues early.
Identify Regulatory and Legal Requirements
Understanding and adhering to relevant laws and regulations is critical. Research:
- Occupational Safety and Health Administration (OSHA) standards
- Environmental Protection Agency (EPA) guidelines
- Local zoning and permitting requirements
Non-compliance can result in fines, delays, or project shutdowns.
Engage Stakeholders
Involving stakeholders early ensures that their concerns are addressed and that they’re invested in the project’s success. Key steps include:
- Conducting meetings with local authorities and community members
- Sharing risk assessment findings transparently
- Addressing concerns proactively, such as noise, traffic, or environmental impacts
This collaboration fosters goodwill and reduces opposition.
Evaluate Potential Risks
Identify and categorize risks into the following categories:
- Health and Safety Risks: Falls, equipment accidents, chemical exposures, etc.
- Environmental Risks: Soil erosion, pollution, impact on local ecosystems
- Financial Risks: Budget overruns, contractor insolvency
- Operational Risks: Delays due to weather, labor shortages, or supply chain disruptions
Use tools like risk matrices or software solutions to rank risks by likelihood and severity.
Develop Risk Mitigation Strategies
Once risks are identified, create strategies to mitigate them. Examples include:
- Implementing engineering controls, such as barriers or ventilation systems
- Developing safety protocols, including worker training and personal protective equipment (PPE) requirements
- Establishing contingency plans, such as backup suppliers or alternative schedules
- Allocating resources, including budgets and personnel, to address high-priority risks
Document the Assessment
A comprehensive risk assessment report is an essential deliverable. It should include:
- An executive summary of key findings and recommendations
- Detailed descriptions of identified risks
- Mitigation strategies and implementation plans
- Documentation of stakeholder consultations and regulatory compliance
This report serves as a reference throughout the project lifecycle.
Implement and Monitor Mitigation Measures
Risk mitigation doesn’t end with planning; it requires ongoing implementation and monitoring. Key actions include:
- Regular safety audits to ensure compliance
- Monitoring environmental impacts during construction
- Adjusting plans based on new information or changing conditions
Effective communication and accountability are crucial to maintaining risk management efforts.
Best Practices for Effective Risk Assessments
- Start Early: Conduct risk assessments as soon as possible during the planning phase
- Utilize Technology: Leverage software tools for data collection, risk analysis, and reporting
- Train Personnel: Ensure that everyone involved in the project understands the importance of risk management and their role in it
- Foster a Safety Culture: Encourage open communication about risks and solutions among all team members
- Review and Update Regularly: Reassess risks at key project milestones and whenever significant changes occur
Challenges in Conducting Pre-Construction Risk Assessments
While critical, pre-construction risk assessments come with challenges, including:
- Incomplete Data: Limited site information or historical records can hinder analysis
- Stakeholder Disputes: Conflicting priorities among stakeholders can delay decision-making
- Dynamic Conditions: Weather, market fluctuations, and unforeseen events can impact risk evaluations
Addressing these challenges requires flexibility, proactive communication, and a commitment to thoroughness.
GPRS offers a comprehensive suite of subsurface damage prevention, existing conditions documentation, and construction & facilities project management services designed to keep your projects on time, on budget, and safe.
We help general contractors like you Intelligently Visualize The Built World® with 99.8% accurate utility locating and concrete scanning, NASSCO-certified video pipe inspections, pinpoint-accurate leak detection, and 2-4mm accurate 3D laser scanning and photogrammetry. And all this data is at your fingertips with SiteMap® (patent pending), our project & facility management application that provides existing conditions documentation to protect your assets and people.
We provide additional site safety support through our series of safety events, including Safety Tour of America, Construction Safety Week, Concrete Sawing & Drilling Safety Week, and Water & Sewer Damage Awareness Week. At GPRS, safety is always on our radar because we want you and your team to leave the job site in the same condition in which you arrived.
What can we help you visualize?
Frequently Asked Questions
What is as-built documentation?
As-built documentation is an accurate set of drawings for a project. They reflect all changes made in during the construction process and show the exact dimensions, geometry, and location of all elements of the work.
Will I need to mark out the utilities that GPRS locates?
No, GPRS will locate and mark all utilities for you. We have a variety of tools and markers we can use to highlight the locations of utilities, underground storage tanks and whatever else may be hiding.
Can GPR determine the difference between rebar and electrical conduit?
Ground penetrating radar (GPR) can accurately differentiate between rebar and electrical conduit in most cases. We have an extremely high success rate in identifying electrical lines in supported slabs or slabs-on-grade before saw cutting or core drilling.
Additionally, GPRS can use EM locators to determine the location of conduits in the concrete. If we can transmit a signal onto the metal conduit, we can locate it with pinpoint accuracy. We can also find the conduit passively if a live electrical current runs through it.
The combined use of GPR and EM induction allows us to provide one of the most comprehensive and accurate conduits locating services available.