The pre-construction phase is a critical part of any project, setting the foundation for smooth execution and long-term success.
But pre-construction processes can become bottlenecks if not managed properly. Fortunately, there are strategies that can be implemented to improve efficiency during the pre-construction phase, reducing delays and increasing productivity for construction teams, contractors, and clients alike.
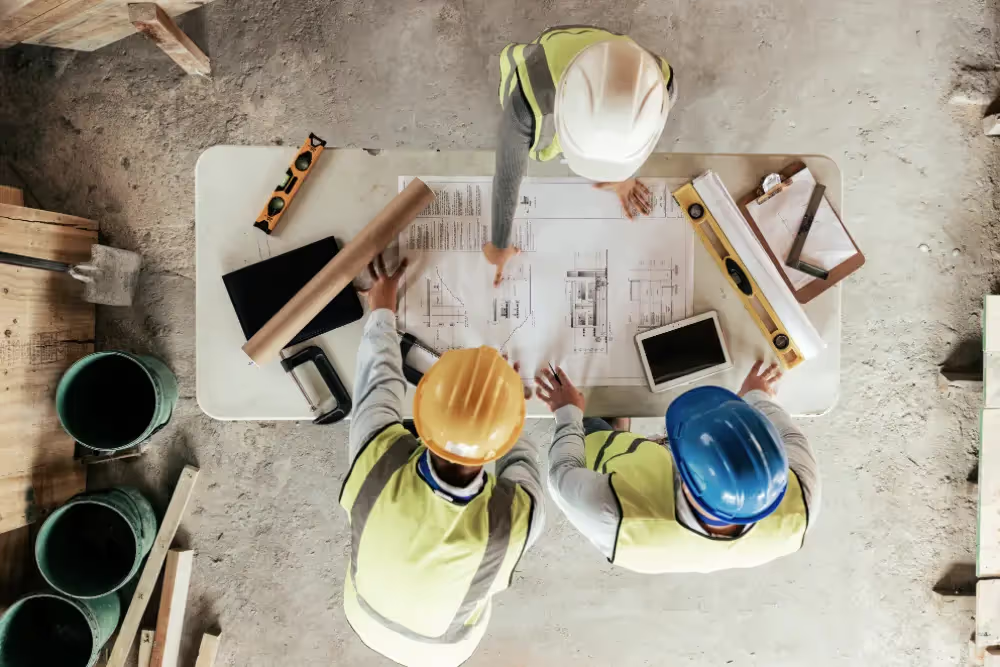
Collaborative Planning with Stakeholders
One of the most effective ways to enhance efficiency is to involve all stakeholders—clients, architects, contractors, engineers, and consultants—early in the process. Collaborative planning fosters alignment on goals and expectations, helps avoid miscommunication, and identifies potential challenges from the outset.
How to implement collaborative planning:
- Hold kick-off meetings to define roles, responsibilities, and project scope
- Use charrette workshops—intensive sessions where multidisciplinary teams develop solutions collectively
- Establish a clear communication plan that defines meeting schedules, reporting formats, and communication channels
By aligning all parties early, potential design flaws, budget gaps, and logistical issues can be uncovered before they escalate.
Adopt Building Information Modeling (BIM) Tools
Building Information Modeling (BIM) has become a game-changer in the construction industry. This technology enables a virtual representation of the project, providing a collaborative platform for planning, design, and coordination.
Key benefits of BIM in pre-construction:
- Enhanced visualization: Stakeholders can see the project’s design and identify conflicts before construction begins
- Improved coordination: Clash detection tools in BIM reveal issues between systems—such as plumbing and electrical—at an early stage
- Accurate cost estimation: BIM can integrate with estimation software, streamlining the budgeting process
Investing in BIM tools reduces the risk of rework, minimizes errors, and accelerates the pre-construction process by keeping all data centralized.
Streamline Documentation and Permitting Processes
The pre-construction phase involves managing an array of documentation—contracts, drawings, permits, and compliance reports. A poorly managed document flow can create delays, especially if approvals are required from local authorities.
Best practices for documentation management:
- Use construction management software that organizes and tracks all project documents
- Implement checklists to ensure all required permits and approvals are identified early
- Assign a dedicated permit coordinator to follow up with regulatory bodies, reducing waiting times
Early identification of permitting requirements ensures smoother approval processes, preventing unexpected delays once the project is underway.
Thorough Site Assessments and Due Diligence
Conducting site assessments early helps identify challenges such as soil issues, environmental hazards, or zoning restrictions. Without proper due diligence, unforeseen site conditions can derail project timelines and budgets.
Effective ways to improve site assessments:
- Use drone technology to conduct aerial surveys and gather real-time data
- Commission soil testing to detect ground conditions that might affect construction
- Perform feasibility studies to ensure the site complies with all regulatory and zoning requirements
By addressing these issues during pre-construction, teams can mitigate risks and prepare contingency plans.
Develop a Detailed Project Schedule and Workflow
A well-structured project schedule is essential for pre-construction efficiency. It provides a roadmap for project activities, sets expectations, and ensures each phase is allocated enough time without causing bottlenecks.
Key elements of effective scheduling:
- Create a critical path schedule (CPS) to identify the sequence of tasks that directly affect the project’s completion date
- Use Gantt charts to visualize task dependencies and milestones
- Establish buffer times for high-risk activities to absorb unforeseen delays
Regularly updating the schedule throughout pre-construction ensures the team stays on track, making it easier to address potential delays before they become critical.
Accurate Budgeting and Value Engineering
Cost overruns are among the most common issues in construction projects. Efficient pre-construction planning includes developing accurate budgets that align with the client’s expectations and exploring value engineering opportunities to maintain quality while controlling costs.
Tips for effective budgeting and value engineering:
- Involve estimators and contractors early to get realistic cost projections
- Use historical data from past projects to benchmark costs
- Conduct value engineering workshops where teams brainstorm ways to optimize materials and construction methods without compromising quality
An accurate budget serves as a financial guide throughout the project, and proactive value engineering helps avoid expensive changes during later phases.
Risk Identification and Management
Every construction project comes with inherent risks—ranging from supply chain disruptions to weather delays and safety issues. Identifying these risks early allows the team to develop mitigation strategies.
Best practices for risk management:
- Conduct risk workshops where teams brainstorm potential risks and rank them based on probability and impact
- Develop contingency plans for high-impact risks, such as alternative suppliers or backup workflows
- Use risk management software to track risks in real-time and monitor mitigation strategies
Effective risk management ensures that the project can move forward even when unforeseen challenges arise.
Supplier and Subcontractor Coordination
Poor coordination with suppliers and subcontractors can cause delays and inefficiencies. Early engagement with these stakeholders ensures that the right resources are available when needed.
Strategies for better coordination:
- Prequalify and onboard subcontractors and suppliers during the pre-construction phase
- Develop procurement schedules to align material deliveries with construction timelines
- Use supply chain management software to monitor deliveries and address issues proactively
Having a clear understanding of supplier timelines and subcontractor availability minimizes disruptions once the project begins.
Embrace Lean Construction Principles
Lean construction focuses on maximizing value while minimizing waste, promoting efficiency from the pre-construction phase onward. This approach encourages continuous improvement and accountability among all stakeholders.
Lean practices to adopt:
- Use pull planning to work backward from project milestones and ensure alignment between tasks
- Identify and eliminate non-value-adding activities, such as redundant meetings or excessive documentation
- Encourage a culture of continuous feedback among teams to identify inefficiencies early
Incorporating lean principles reduces waste and increases productivity, ensuring the project starts on the right foot.
Foster a Culture of Communication and Transparency
Clear and open communication is the backbone of an efficient pre-construction process. When teams and stakeholders share information freely, misunderstandings are minimized, and decision-making is expedited.
How to promote communication and transparency:
- Establish centralized communication platforms, such as project management tools, to keep everyone updated
- Hold regular check-in meetings to review progress and address emerging issues
- Encourage open forums where team members can raise concerns or suggest improvements without fear of reprisal
Transparent communication creates an environment of trust, leading to faster resolutions and smoother collaboration throughout the project.
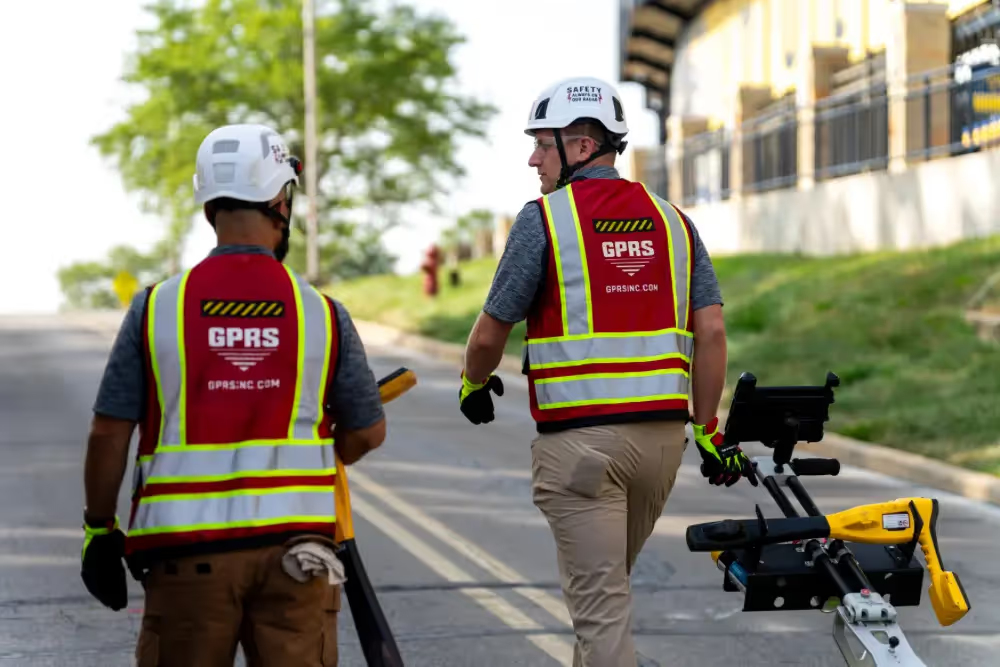
Let GPRS Help You Make Pre-Construction More Efficient!
Improving efficiency in the pre-construction phase of a project requires a strategic approach that integrates collaboration, technology, thorough planning, and proactive management.
GPRS offers a comprehensive suite of subsurface damage prevention, existing conditions documentation, and construction & facilities project management services designed to keep your projects on time, on budget, and safe.
We help you Intelligently Visualize The Built World® with 99.8% accurate utility locating and concrete scanning, NASSCO-certified video pipe inspections, pinpoint-accurate leak detection, and 2-4mm accurate 3D laser scanning and photogrammetry. And all this data is at your fingertips with SiteMap® (patent pending), our project & facility management application that provides existing conditions documentation to protect your assets and people.
What can we help you visualize?
Frequently Asked Questions
What is as-built documentation?
As-built documentation is an accurate set of drawings for a project. They reflect all changes made in during the construction process and show the exact dimensions, geometry, and location of all elements of the work.
Will I need to mark out the utilities that GPRS locates?
No, GPRS will locate and mark all utilities for you. We have a variety of tools and markers we can use to highlight the locations of utilities, underground storage tanks and whatever else may be hiding.
Can GPR determine the difference between rebar and electrical conduit?
Ground penetrating radar (GPR) can accurately differentiate between rebar and electrical conduit in most cases. We have an extremely high success rate in identifying electrical lines in supported slabs or slabs-on-grade before saw cutting or core drilling.
Additionally, GPRS can use EM locators to determine the location of conduits in the concrete. If we can transmit a signal onto the metal conduit, we can locate it with pinpoint accuracy. We can also find the conduit passively if a live electrical current runs through it.
The combined use of GPR and EM induction allows us to provide one of the most comprehensive and accurate conduits locating services available.