“This job caught me off guard. I got it on very short notice and there was no time for research,” said GPRS Project Manager Nicholas Slack.
All he knew going in was that the Brentwood, California high rise was in the heart of the entertainment corridor in the L.A. area, just five miles from Universal Studios, and was being constructed for something “very high profile” in the entertainment industry. Specifically, the new 12-story building needed nearly 100 scans to provide clearance for 2-3” cores in pan deck concrete.
What is Pan Deck?
Like Kleenex is to tissues and Band-Aids are to bandages, the phrase pan deck has become synonymous with all varieties of metal concrete decking.
Metal pan decking was a specific variety of decking used from the 1940s - 1960s to mold and support poured concrete slabs in construction. Although the specific product known as pan deck hasn’t been manufactured in the United States for over 50 years, many in the construction trades still refer to all types of metal concrete decking as pan decking.
These days, the decking is either a form deck that provides a mold for the curing concrete, or a composite deck that is made to adhere to the cured concrete and aid in its support. Composite decking is designed to support and mold the poured concrete with less additional weight than form decking, but both are constructed with the familiar corrugated steel pattern of “highs and lows” to create a suspended slab. One of the only differences to the untrained eye is that composite decks are embossed on their sides to “grip” the cured concrete once it is dry.
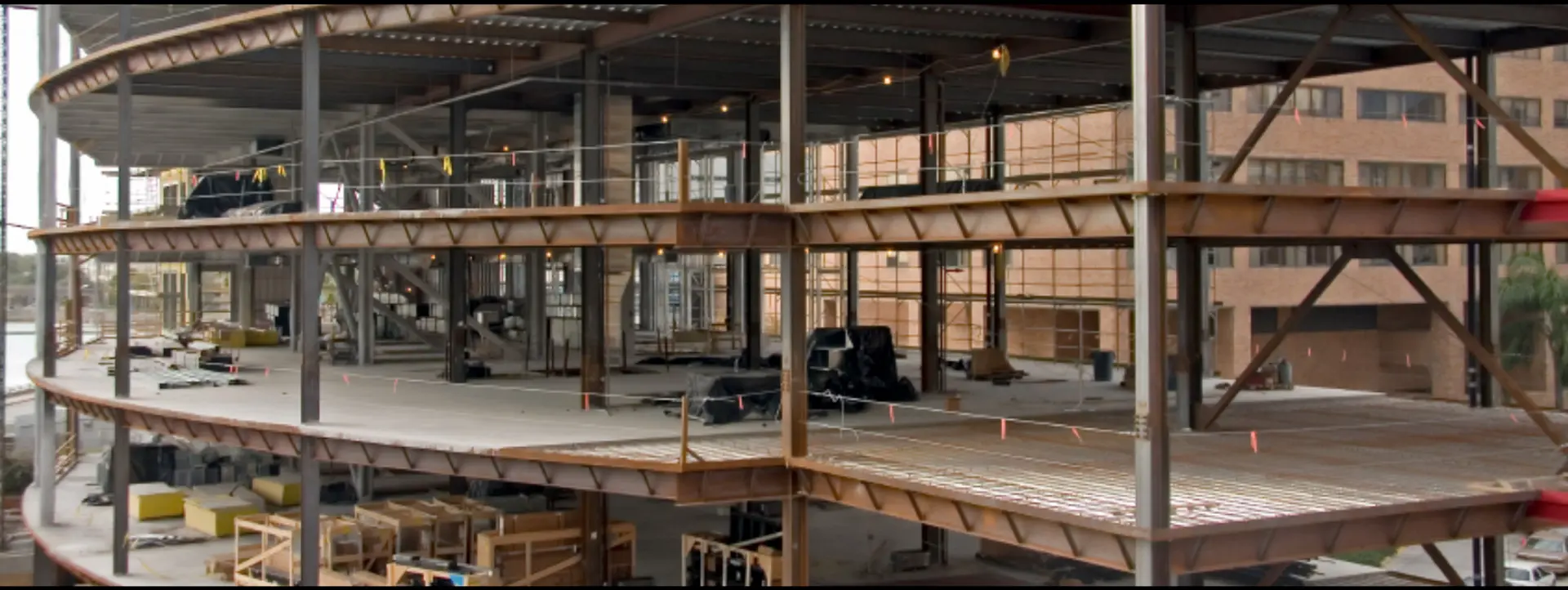
Slack aptly describes pan deck as, “looking like one of those metal roofs you see on houses, but in this case, it’s used to support concrete.” Wire mesh and beams, usually attached with Nelson studs, add to the structural support.
Why Does Concrete Deck Require Scanning Expertise?
The unique corrugated patterns in pan decking create a stronger slab, but present a challenge to concrete scanning & imaging companies because there is no flat bottom edge to the slab. The highs and lows of the corrugated shape present almost like the hyperbolas that GPRS Project Managers zero in on to locate rebar, conduit, pipes, and other subsurface infrastructure. Add the wire mesh and beams into the picture, and getting an accurate image of a pan deck concrete slab can get tricky.

“Unlike post tension concrete, you don’t have to worry about cables popping out when cut, so it’s easier to cut than post tension. Your biggest structural risk is hitting a beam,” Slack continued, because you often have to use line of sight to locate them. However, when Nelson studs are attached to the beams, they show up clearly on scans, allowing Project Managers to locate them more easily.
“We always treat anything like it is full of conduit,” Slack said. “When we started scanning, we noticed a lot of conduits, so we made sure we found as much of it as possible in each scan area.”
With pan deck concrete it is imperative to assume a lot of encased infrastructure: Wire mesh, conduit, and beams are the main sources of concern, with conduit leading in terms of concern because hitting a single live line can shut down the job, mean costly repairs, and could cause serious injury to those on site.
The hope is that the conduit is laid shallowly, away from the corrugated deck, so it is easier to see with the ground penetrating radar unit, but that is not always the case.
Because there was no lead time for the job, Slack joined a team of three other Project Managers and one field trainee to scan the site for the 2-3” core clearances needed, and decided to do some reconnaissance.
“By the time we’re on site, the pan deck flooring isn’t usually exposed. I stopped on a couple of lower floors to gauge the scope of the job and found some of the deck was still exposed, so I was able to see the pan deck and beam patterns,” he said.
But as Slack stated earlier, GPRS Project Managers don’t make assumptions, so each of the approximately 100 core sites were thoroughly scanned. If a PM marks a green “CLEAR” box on your concrete slab, you can cut, core, or drill with confidence. Because we back it up with our 99.8% accuracy rate and Green Box Guarantee.
It took the team of four PMs less than four hours to mark out 100 core sites, and they went beyond the scope of each site to provide more safety to anyone who would be cutting the concrete.
The Brentwood high rise project had some deeply laid conduit. The GPRS Project Managers found several instances of well-hidden conduit in the low areas of the corrugated slab.
“We always recommend drilling in the ‘highs’ due to the least drilling resistance and depending on how clear conduits appear over the highs,” Slack said when he shared his findings on LinkedIn.
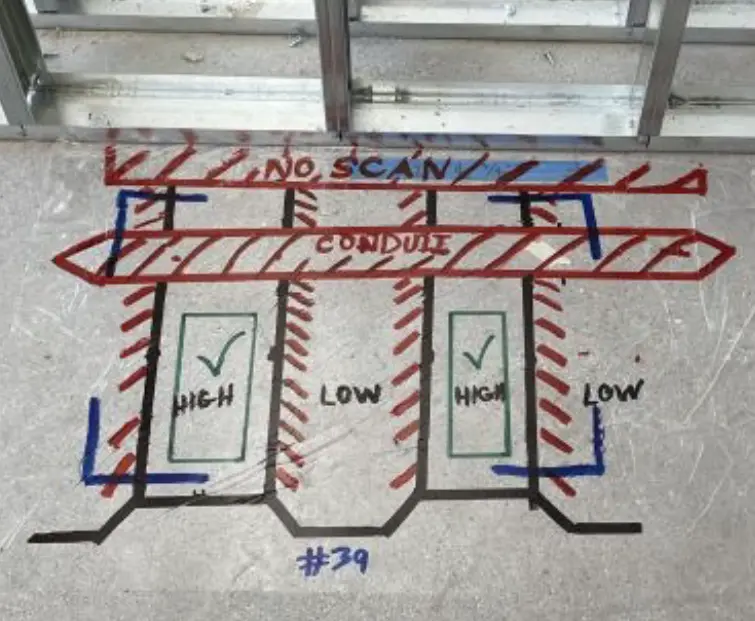
The GPRS Difference
Going the extra mile is something of a specialty for Nicholas Slack, which may be why he is such a good fit at GPRS. Led by Area Manager, Alfredo Espinal, the team of Southern California Project Managers is always looking for ways to make faster, clearer, cleaner markings on site. So, Slack began utilizing carpet mask over his locates. Because the floor in Brentwood was finished, he needed something that would be resistant to standard job site clean-up yet was not permanent.
“This is finished floor with a very tacky and easy to clean carpet mask.
Protecting a smooth finish from seepage of the markers and still providing
top quality markings,” Nicholas Slack shared on LinkedIn.
You can clearly see the green boxes, marked as high points in the locate area in the image above, where the customer could core with confidence. One of the comments on LinkedIn called Slack a “concrete scanning Picasso,” for the innovation and precision of his concrete markings.
Decisions like utilizing carpet mask for marking to preserve the surface, conducting full site recon to understand the scope of the job, and extending the scan area for a greater boundary of safety are some of the hallmarks of the elite level of consultative service GPRS provides.
“The SoCal GPRS crew has done a lot to improve performance and innovate new methodologies, like the use of carpet mask to make marks which are more intuitive for anyone who has to cut and core,” shared GPRS Field Support Director, Jamie Althauser. “Anything from the thickness of the lines to the line colors were scrutinized to help make everything as clear as possible.”
We have been Intelligently Visualizing The Built World™ for our customers since 2001. What can we help you visualize?