Submersible pumps play a crucial role in managing sewage systems, ensuring that wastewater is effectively transported to treatment facilities.
In prison environments, these pumps face a range of unique challenges that significantly complicate maintenance and clog elimination. Prisons generate a distinct blend of waste, and the confined, high-security setting adds further complexities to addressing pump clogs.
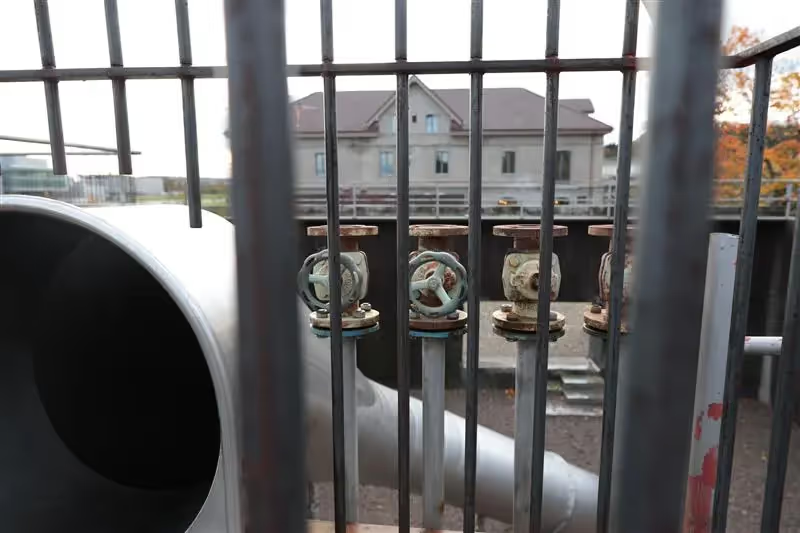
Waste Composition in Prisons
One of the most significant challenges in prison sewage systems is the atypical composition of waste. Unlike residential or commercial settings, prison sewage systems often contain non-flushable items intentionally or unintentionally introduced by inmates. Common culprits include:
- Clothing and fabric items: Socks, shirts, and other fabric materials are frequently flushed, either as acts of vandalism or to hide contraband
- Personal hygiene products: Items such as sanitary pads, tampons, and wipes, many of which are labeled as flushable but do not disintegrate effectively
- Contraband: Inmates may dispose of prohibited items like plastic wrappers, small electronics, or metal objects in toilets to avoid detection
- Improvised tools and weapons: Sharp objects can severely damage pump components if not removed promptly
The mix of organic waste with these non-biodegradable and often bulky items creates a high potential for clogs, leading to pump malfunctions.
Design and Accessibility Constraints
The design of sewage systems in prisons often complicates maintenance tasks. Submersible pumps are usually installed in confined spaces, such as underground lift stations, where accessibility is limited. Adding to this, prison environments necessitate stringent security measures, requiring specialized access protocols for maintenance crews. These constraints can lead to delayed responses and prolonged system downtime when clogs occur.
The layout of prison facilities also often does not prioritize easy access to infrastructure components. The retrofitting of older prisons with modern sewage systems is particularly challenging, as these structures were not originally designed with contemporary waste management needs in mind. Tight quarters, outdated piping, and lack of redundancy in pumping systems exacerbate the issue.
Security Considerations in Maintenance
Conducting maintenance in a prison setting requires careful planning and adherence to strict security protocols. Maintenance personnel must be supervised by corrections officers, and tools must be meticulously accounted for to prevent their misuse. These precautions can significantly extend the time needed to address clogs in submersible pumps.
Additionally, the presence of inmates during maintenance work poses risks to both personnel and equipment. To mitigate these risks, sewage system repairs are often scheduled during lockdown periods, which may not align with the urgency of the repair, prolonging downtime and increasing the likelihood of system backups.
High Frequency of Clogs and Operational Downtime
Given the unique waste profile in prisons, clogs occur more frequently than in typical sewage systems. The high incidence of blockages leads to repeated operational interruptions, causing strain on maintenance resources and increasing costs. Frequent clogs also pose environmental and health risks, as sewage backups can result in unsanitary conditions and potential contamination.
Strategies for Addressing Submersible Pump Clogs
To effectively manage and reduce submersible pump clogs in prisons, a multi-faceted approach is essential. Below are several strategies that can be implemented to address these challenges:
- Upgraded Pump Technology: Investing in robust pumps designed for handling challenging waste streams is critical. Grinder pumps, for instance, can shred non-biodegradable materials into smaller, more manageable pieces, reducing the likelihood of clogs. Similarly, pumps with higher torque and advanced impeller designs can better handle the diverse waste materials encountered in prison settings.
- Preventative Maintenance Programs: Proactive maintenance schedules can help identify and address potential issues before they escalate into full-scale clogs. Regular inspections of pump stations, combined with routine cleaning and component checks, can minimize downtime and extend the lifespan of the equipment.
- Education and Awareness Campaigns: Educating inmates about the impact of flushing non-biodegradable items can reduce intentional misuse of the sewage system. Posters, informational videos, and incentives for compliance can promote better waste disposal habits.
- Enhanced Waste Screening Systems: Installing screening systems at key points in the sewage network can intercept larger items before they reach the pumps. Bar screens and basket strainers are effective tools for capturing debris, although they require regular cleaning to maintain efficiency.
- Integration of Smart Monitoring Technology: The use of IoT-enabled sensors and monitoring systems can provide real-time data on pump performance, enabling quicker responses to potential clogs. Alerts for abnormal pressure levels or flow rates can help maintenance teams address issues proactively.
- Collaboration with Engineering Experts: Partnering with specialized engineers and contractors experienced in high-risk environments can lead to the development of customized solutions. For example, retrofitting older systems with bypass capabilities can facilitate quicker repairs without disrupting overall sewage flow.
Balancing Cost and Efficiency
Implementing these solutions often requires a significant upfront investment, which can be challenging given budget constraints in the corrections system. However, the long-term benefits — including reduced maintenance costs, fewer operational disruptions, and improved sanitation — justify the expense. Cost-benefit analyses can help prison administrators prioritize investments in the most impactful technologies and practices.
The Path Forward
Addressing submersible pump clogs in prison sewage systems is a complex but solvable challenge. By recognizing the unique factors at play and adopting a proactive, multi-pronged approach, corrections facilities can significantly reduce the frequency and severity of clogs. Collaboration among prison administrators, maintenance teams, engineers, and inmates is key to developing sustainable solutions that balance operational efficiency with security and safety considerations.
As technology continues to evolve, the adoption of smart systems and advanced pump designs will further enhance the resilience of prison sewage infrastructure. In the meantime, targeted investments in education, maintenance, and robust equipment will serve as the foundation for more effective waste management in these challenging environments.
GPRS offers an extensive suite of sewer inspection services to help you maintain your sewer system, whether you’re in charge of a high-security prison or a manufacturing facility.
Our Video Pipe Inspection service is a sewer inspection service that uses industry-leading remote video cameras to assess conditions and prevent problems in water, sanitary and storm sewer, and lateral pipelines. Our NASSCO-certified Project Managers scope your sewers to locate clogs, identify cross bores, find structural defects & damages, and conduct lateral sewer line inspections.
GPRS is the sewer inspection company you can trust to provide you with comprehensive, interactive reporting that details every inch of your pipes to help you plan repairs, maintain your system integrity, and mitigate risk.
All this crucial infrastructure data is at your fingertips 24/7 thanks to SiteMap® (patent pending), powered by GPRS.
SiteMap® is a project & facility management application that provides accurate existing conditions documentation to protect your assets & people. Accessible from any computer, tablet or smartphone, it allows you and your team to plan, design, and manage infrastructure projects from anywhere – reducing the number of trips you must make to your facility.
From sewer lines to skyscrapers, GPRS Intelligently Visualizes The Built World® to keep your projects on time, on budget, and safe.
What can we help you visualize?
Frequently Asked Questions
Does GPRS offer lateral launch services?
Yes, we offer lateral launch capabilities as part of our standard Video Pipe Inspection services.
What deliverables does GPRS offer when conducting a VPI?
GPRS is proud to offer WinCan reporting to our Video Pipe Inspection clients. Maintaining sewers starts with understanding sewer condition, and WinCan allows GPRS Project Managers to collect detailed, NASSCO-compliant inspection data. GPRS Project Managers not only inspect the interior condition of sewer pipes, laterals, and manholes – they can also provide a map of their location. The GPRS Mapping & Modeling Department can provide detailed GPS overlays and CAD files. Our detailed WinCan/NASSCO reports contain screenshots of the interior condition of the pipe segments that we inspect, as well as a video file for further evaluation, documentation, and/or reference.
What size pipes can GPRS inspect?
Our elite VPI Project Managers have the capabilities to inspect pipes from 2” in diameter and up.
Can you locate pipes in addition to evaluating their integrity?
Yes! Our SIM- and NASSCO-certified Project Managers use VPI technology equipped with sondes, which are instrument probes that allow them to ascertain the location of underground utilities from an inaccessible location. This allows them to use electromagnetic (EM) locating to map sewer systems at the same time they’re evaluating them for defects.