The construction industry has faced significant challenges in recent years, particularly with supply chain disruptions that have led to delays, increased costs, and inefficiencies.
These disruptions, exacerbated by global events such as the COVID-19 pandemic and geopolitical tensions, have prompted industry leaders to seek innovative solutions to keep projects on track. One approach that has gained attention is the design-build delivery method.
Understanding the Design-Build Delivery Method
The design-build method is a project delivery system where a single entity, known as the design-builder, is responsible for both the design and construction phases of a project. This contrasts with the traditional design-bid-build method, where the design and construction are handled by separate entities. In the design-build model, the design-builder coordinates all aspects of the project, from initial concept through to final construction, creating a more streamlined and integrated process.
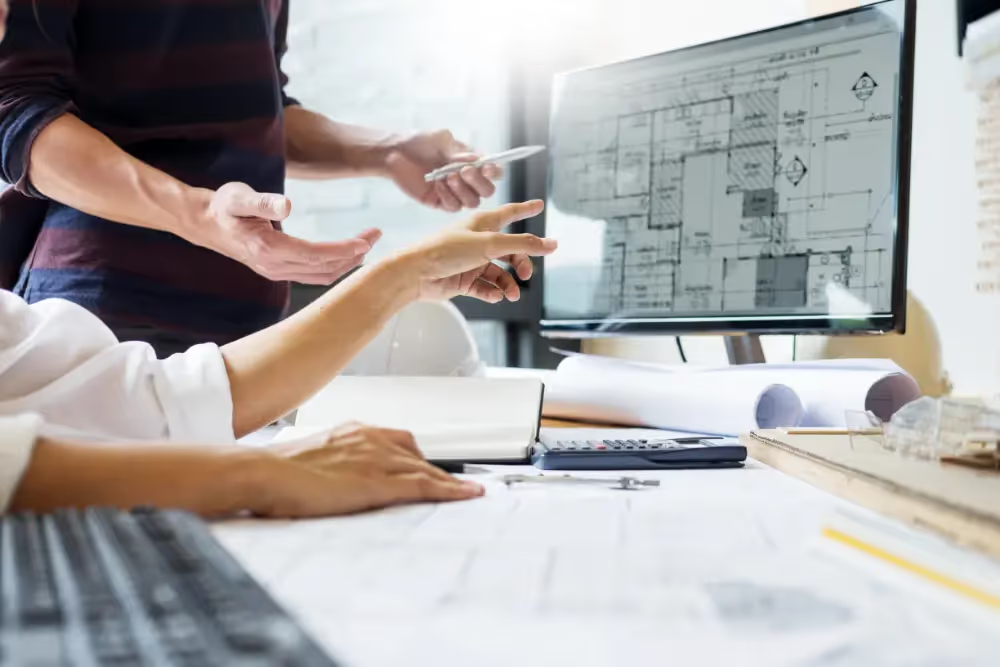
The Impact of Supply Chain Bottlenecks on Construction
Supply chain bottlenecks have become a significant concern for the construction industry, leading to delays in project timelines, cost overruns, and challenges in meeting client expectations. These bottlenecks are often caused by factors such as shortages of key materials, delays in transportation, labor shortages, and fluctuations in material costs.
According to a report by Dodge Data & Analytics, supply chain disruptions have led to a 7.6% increase in construction costs in 2022 alone, with materials like steel, lumber, and concrete being particularly affected. The traditional design-bid-build method, with its segmented approach, often exacerbates these issues as the separation of design and construction can lead to miscommunication, delays in decision-making, and a lack of flexibility in responding to supply chain challenges.
How Design-Build Can Address Supply Chain Issues
Design-build offers several potential advantages in mitigating supply chain bottlenecks, primarily through its integrated approach. Here’s how:
1. Enhanced Collaboration and Communication
One of the key strengths of the design-build method is its emphasis on collaboration. With the design and construction teams working under a single contract, there is more direct communication and coordination between all parties involved. This enhanced collaboration allows for faster decision-making, which is crucial when responding to supply chain disruptions. For instance, if a particular material becomes unavailable, the design-builder can quickly pivot to alternative materials or adjust the design to accommodate the change, minimizing delays.
2. Streamlined Procurement Processes
In the traditional design-bid-build method, the procurement process can be cumbersome, with the construction team only coming into the picture after the design phase is complete. This separation can lead to delays in sourcing materials, especially in a tight supply chain environment. Design-build, however, allows for the procurement process to begin earlier, often during the design phase itself. This early involvement enables the design-builder to secure materials ahead of time, lock in prices, and mitigate the risks associated with fluctuating material costs and availability.
3. Flexibility in Design and Material Selection
Design-build's integrated nature provides greater flexibility in both design and material selection. If supply chain disruptions affect the availability of certain materials, the design-builder can make real-time adjustments to the project without the need for extensive redesigns or contract modifications. This flexibility not only helps keep projects on schedule but can also reduce costs by allowing the design-builder to explore alternative, cost-effective materials that meet the project's requirements.
4. Improved Risk Management
Risk management is another area where design-build can offer significant benefits. By consolidating the design and construction responsibilities under one entity, the design-build model reduces the potential for disputes and finger-pointing that can occur in traditional project delivery methods. This unified approach allows for more effective risk assessment and management, particularly in dealing with supply chain uncertainties. The design-builder can take proactive measures, such as pre-purchasing critical materials or establishing contingency plans for potential delays, to ensure that the project remains on track.
Potential Drawbacks of Design-Build
While design-build offers many advantages, it is not without its challenges. One potential drawback is that the success of a design-build project heavily depends on the capability and experience of the design-builder. A lack of experience in managing both design and construction can lead to quality issues or project delays. Additionally, some clients may be hesitant to adopt the design-build model due to perceived risks, such as reduced oversight or concerns about cost transparency.
Another consideration is that the design-build method may not be suitable for every project, particularly those that require highly specialized design work or involve complex regulatory requirements. In such cases, the traditional design-bid-build method may still be the preferred approach.
GPRS Supports Your Design-Build Projects
GPRS provides accurate as-built site data to help design-build projects move seamlessly through the design and construction process.
Our utility locating, precision concrete scanning, pinpoint leak detection, and NASSCO-certified video pipe inspection services help you prevent subsurface damage and provide you with an accurate, complete picture of the subsurface infrastructure on your job site. And our 3D laser scanning, photogrammetry, and SiteMap® (patent pending) infrastructure mapping software provide existing condition documentation, and construction & facilities project management services to help you plan, design, manage, dig, and ultimately build better.
What can we help you visualize?
Frequently Asked Questions
What are the Benefits of Underground Utility Mapping?
Having an updated and accurate map of your subsurface infrastructure reduces accidents, budget overruns, change orders, and project downtime caused by dangerous and costly subsurface damage.
How does SiteMap® assist with Utility Mapping?
SiteMap®, powered by GPRS, is the industry-leading infrastructure management program. It is a single source of truth, housing the 99.8%+ accurate utility locating, concrete scanning, video pipe inspection, leak detection, and 3D laser scanning data our Project Managers collect on your job site. And the best part is you get a complimentary SiteMap® Personal Subscription when GPRS performs a utility locate for you.
Click here to learn more.
Does SiteMap® Work with my Existing GIS Platform?
SiteMap® allows for exporting of data to SHP, GeoJSON, GeoPackage, and DXF directly from any user’s account that either owns or has a job shared to their account. All these file formats can be imported and utilized by other GIS packages if manually imported by the user. More information can be found at SiteMap.com.