Sustainability is a significant concern in the construction industry, driving innovation in materials and methods.
One such groundbreaking development is waterless concrete, a new formulation designed to address environmental concerns while maintaining the strength and durability essential for modern construction.
That idea is being taken to new heights – literally – as part of a project designed to test new lunar construction materials in preparation for NASA’s planned 2025 return to the moon.
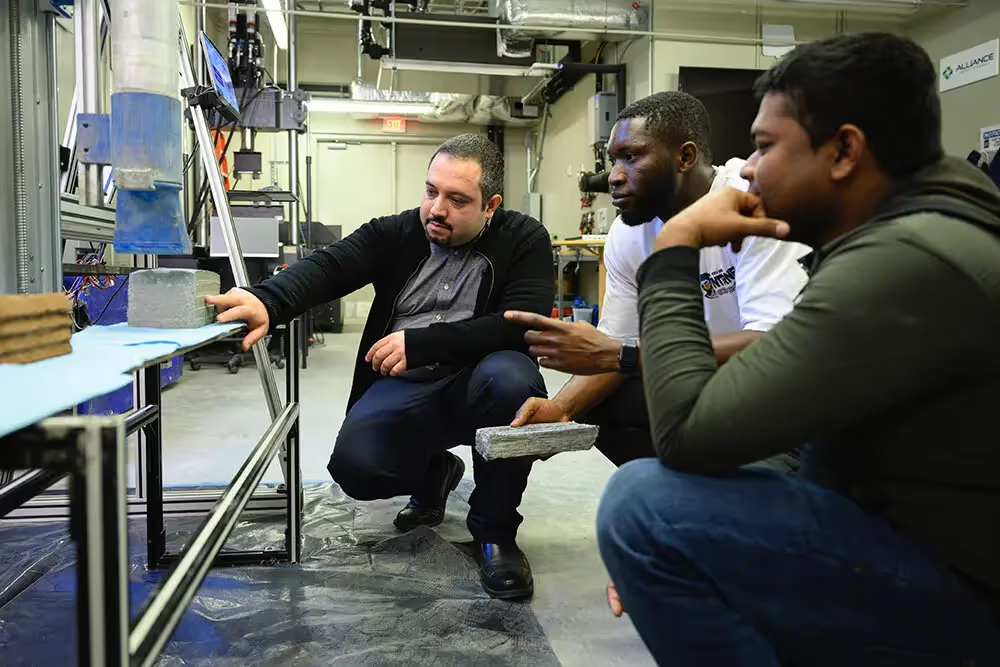
According to a press release on Louisiana State University’s website, LSU and scientists from NASA Marshall Space Flight Center in Alabama have partnered to research the use of native raw materials readily available on the surface of the Moon and Mars – namely sulfur and regolith – to develop 3D-printed, waterless concrete.
The project is in support of the overall goal of NASA’s return to the Moon: to explore its south pole and begin the process of establishing a long-term presence there.
“Molten sulfur is the binder and regolith, i.e. Lunar soil, acts as the filler material,” said LSU Bert S. Turner Construction Management Assistant Professor Ali Kazemian. “Robotic construction on the Moon using Lunar resources and large-scale 3D-printing technology is the goal. Even shipping raw materials from Earth is cost prohibitive, so the only practical approach is to use the resources which are already available on the Moon and Mars for construction. That is why 3D printing using sulfur-regolith concrete (SRC) is attractive. On the other hand, production of Portland cement concrete, the most commonly used construction material on Earth, will be complicated on the Moon and will require large amounts of water that could otherwise be used for life support or other exploration activities.”
Funded through a $200,198 grant from the National Science Foundation, the work will be carried out at LSU and the NASA Marshall Space Flight Center. The team will study the extrusion parameters and interplay between material-process-environment factors during high-temperature SRC extrusion and test the space resilience of 3D-printed SRC specimens under vacuum conditions and temperature swings, extreme thermal load resistance, and simulated micrometeorite impact resistance.
“The planned research tasks will provide a fundamental understanding of the impacts of high-temperature, extrusion process parameters and environmental factors, such as near-vacuum conditions, on the performance of 3D-printed SRC structures,” Kazemian said. “After reaching these objectives, together with our NASA Colleagues, we will work on design and development of a large-scale SRC 3D-printing system at NASA Marshall to validate our research findings on a large scale. For example, by 3D printing a Lunar habitat analog…”
Whether created with extraterrestrial material, or Earth-bound products, waterless concrete represents a significant step forward in the pursuit of sustainable construction. By eliminating the need for water in the concrete mixing process, this innovative material not only conserves a precious natural resource but also offers a more environmentally friendly alternative to traditional concrete.
What is Waterless Concrete?
Waterless concrete, also known as dry concrete, is a type of concrete that does not require water for mixing or curing. Traditional concrete production involves mixing cement, water, and aggregates like sand and gravel. The chemical reaction between water and cement allows concrete to set and harden. However, waterless concrete uses a different chemical process that eliminates the need for water, relying on chemical additives and reactions to achieve the necessary binding and hardening properties.
Composition and Production
The key to waterless concrete lies in its innovative composition. Manufacturers replace water with chemical activators that trigger the hydration process of cement. These activators are often composed of various compounds that can efficiently initiate and sustain the hydration process without external water. Additionally, waterless concrete incorporates superabsorbent polymers that help in retaining any intrinsic moisture within the mix, which is crucial for the curing process.
The production of waterless concrete involves mixing cement, aggregates, and specific chemical activators under controlled conditions. This process not only reduces the dependence on water but also results in a faster setting time, making it highly beneficial for rapid construction scenarios.
Environmental Benefits
One of the most significant advantages of waterless concrete is its environmental impact. The traditional concrete production process is water-intensive, consuming large quantities of water. By eliminating the need for water in concrete, we significantly reduce water use in construction, conserving this vital resource for other needs, especially in arid regions or places with water scarcity.
Furthermore, waterless concrete contributes to reducing the carbon footprint of construction activities. The production of cement, a primary component of traditional concrete, is energy-intensive and generates considerable amounts of CO2. Since waterless concrete can be formulated to use alternative and less carbon-intensive binders, it offers a greener alternative to conventional concrete.
Applications and Limitations
Waterless concrete is particularly useful in environments where water is scarce or where rapid construction is necessary. It has potential applications in desert regions, in military construction, in space exploration habitats, and in emergency constructions such as flood barriers or temporary shelters in disaster-struck areas.
However, the adoption of waterless concrete also faces certain limitations. The cost of chemical activators can be higher than the traditional water-based mix, making it more expensive in current market conditions. Moreover, because it's a relatively new technology, there may be challenges related to long-term durability and behavior under different environmental conditions, which are still under research and testing.
The Future of Waterless Concrete
As the technology develops and more research is conducted, the applications and efficiency of waterless concrete are expected to expand. Innovations in chemical additives and further understanding of the material's properties could lead to wider acceptance and usage in the construction industry. Additionally, as environmental regulations become stricter and water scarcity issues increase, the demand for sustainable construction materials like waterless concrete is likely to grow.
Efforts to make waterless concrete more cost-effective are also crucial for its adoption. This could involve finding cheaper sources of chemical activators or improving the manufacturing process to reduce costs. Furthermore, education and training for engineers and construction workers in the use of waterless concrete will play a vital role in its integration into mainstream construction practices.
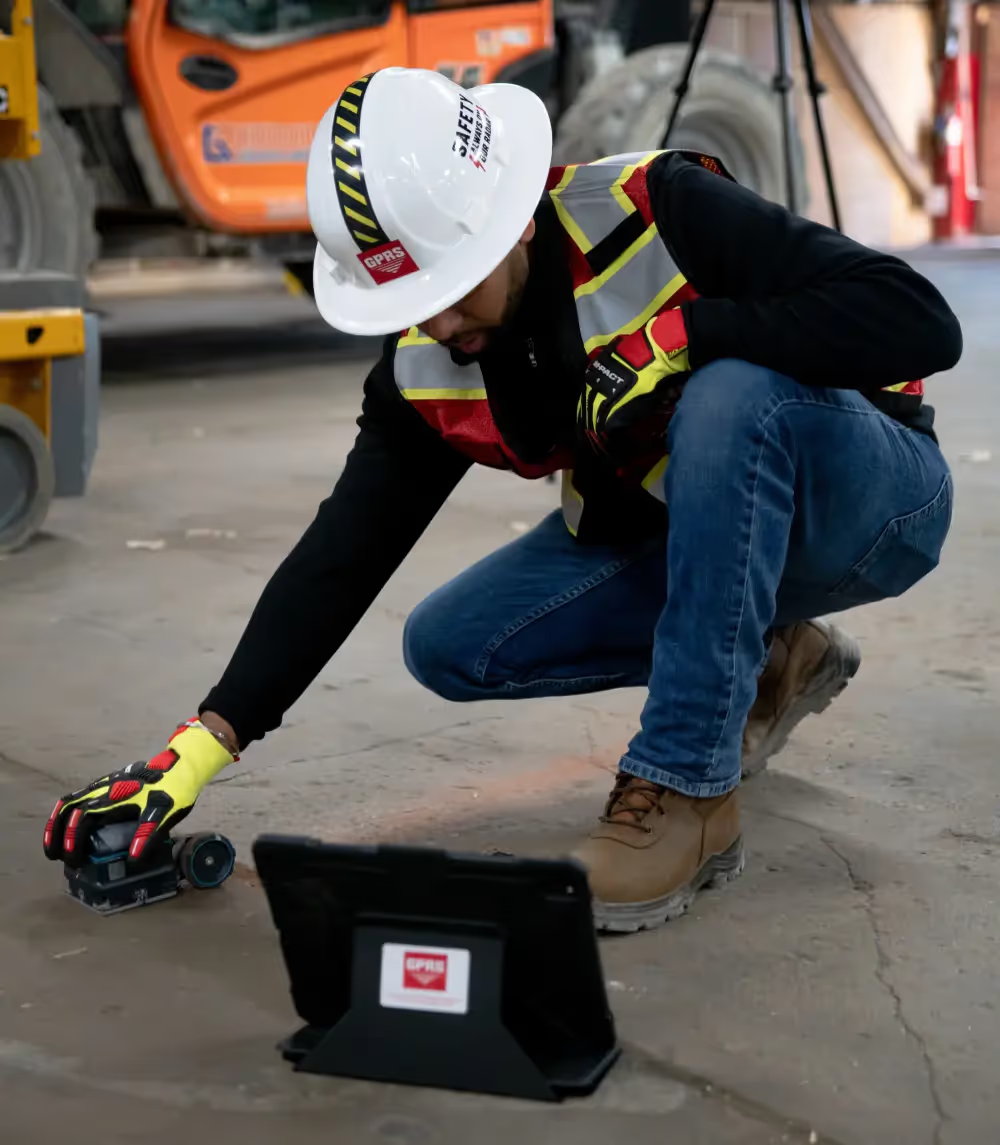
GPRS Concrete Scanning Solutions Ensure Safe Cutting & Coring
As the construction industry continues to evolve towards greener practices, waterless concrete is poised to play a crucial role in shaping the future of construction, making it an exciting area for ongoing research and application.
Of course, no matter the composition of the concrete, it’s important to know what’s embedded within a slab before you cut or core.
GPRS offers comprehensive, precision concrete scanning and imaging services designed to keep you and your team safe, your budget intact, and your projects on time.
Concrete coring comes at a risk to you and your team – as well as your budget and schedule. GPRS’ SIM-certified Project Managers (PMs) are equipped with multiple technologies to clear areas prior to you core drilling and/or anchoring. Upon completion of the scanning process, you will have a clear layout of the vertical and horizontal position of impediments such as post tension cables, rebar, beams, and conduits. Our scanning and imaging services can be completed on any surface you might be working on, including concrete slabs, walls, columns, and beams.
As with concrete coring, it’s crucial to locate unseen or buried objects prior to saw cutting into slab-on-grade concrete. You don’t want to risk severing post tension cables, rebar, conduits, pipes, grade beams, or any of the other obstructions that could be inches from your saw blade. GPRS concrete scanning and imaging services mitigate these risks by utilizing both ground penetrating radar (GPR) scanning and electromagnetic (EM) locating to visualize what is inside and underneath your concrete slab.
We are so confident in our PMs that we introduced the Green Box Guarantee, which states that when we place a Green Box within a layout prior to anchoring or coring concrete, we guarantee that the area will be free of obstructions.
If the area isn’t free of obstructions when you core or cut, GPRS will pay the material cost of the damage.
What can we help you visualize? Click below to schedule a service or request a quote today!
Frequently Asked Questions
Can GPR determine the difference between rebar and electrical conduit?
Ground penetrating radar can accurately differentiate between rebar and electrical conduit in most cases. We have an extremely high success rate in identifying electrical lines in supported slabs or slabs-on-grade before saw cutting or core drilling.
Additionally, GPRS can use EM locators to determine the location of conduits in the concrete. If we can transmit a signal onto the metal conduit, we can locate it with pinpoint accuracy. We can also find the conduit passively if a live electrical current runs through it.
The combined use of GPR and EM locating allows us to provide one of the most comprehensive and accurate conduit locating services available.
Do all concrete scanning companies offer a green box guarantee?
No, the Green Box Guarantee is an industry-leading, proprietary program GPRS created to help prevent injuries and damages. We want to provide you with the peace of mind that comes with knowing you and your team can safely core and drill into concrete without worrying about subsurface damage. GPRS offers this program as part of our pursuit of 100% subsurface damage prevention. We are the only company that can provide the Green Box Guarantee, because we’re the only company that can lean on our industry-leading 99.8%+ accuracy rate for concrete scanning projects.