A long-delayed expansion to the San Francisco International Airport (SFO) is finally underway.
Longtime GPRS safety partner Turner Construction broke ground this summer on the $2.6-billion Terminal 3 West Modernization project, which will renovate the existing 650,000-square-foot western half of SFO’s Terminal 3, including a seismic retrofit, an expanded security checkpoint and new passenger amenities.
According to an SFO press release, the project will also create 200,000 square feet of additional space, allowing for expanded food, beverage, and retail concessions. The expansion is expected to open in fall 2027.
“For millions of people around the world, SFO creates their very first impression of the San Francisco Bay Area,” said San Francisco Mayor London Breed. “We want our residents to be proud of their hometown Airport and for visitors to experience what makes our region great the moment they step off an airplane. This Terminal 3 West Modernization project is another major step that will ensure SFO continues to reflect the innovation, sustainability, and diversity that make San Francisco such an amazing place.”
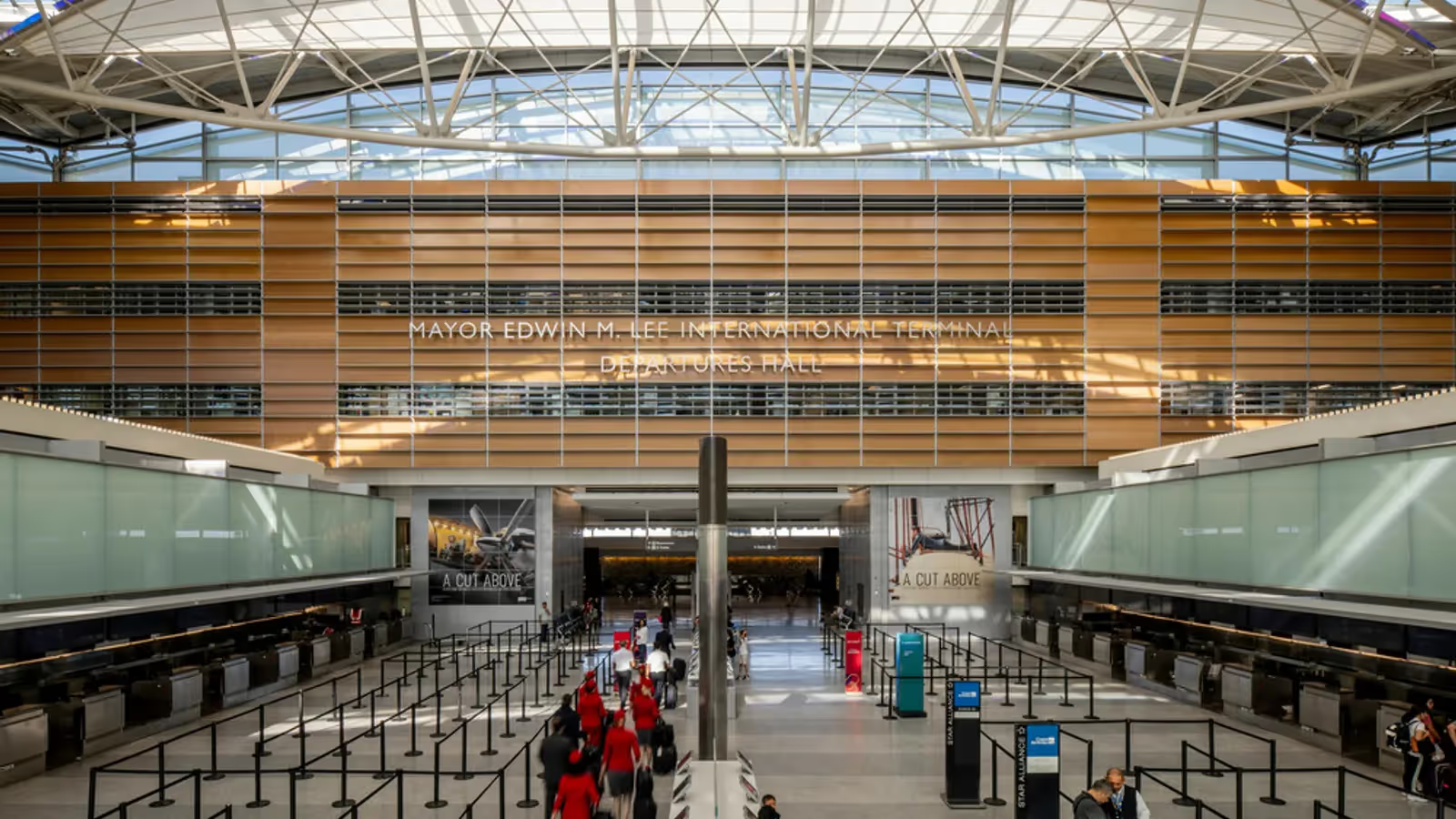
Turner is leading the design-build team alongside San Francisco-based architects Gensler and TEF Design. According to an article in Construction Dive, the project is part of the airport’s larger, 10-year expansion plan which began in 2019.
SFO is targeting LEED Platinum certification for this project, with planned sustainability features including daylight harvesting, displacement ventilation, on-site photovoltaic cells, waste heat recovery, low carbon steel and concrete, energy smart baggage handling, dynamic glazing, recycled water, hydration stations, health-friendly materials and green building education.
At its peak, the project is anticipated to employ 500-600 workers, and is targeting to award over $173 million in contracts to Local Business Enterprises (LBE).
“We are always looking for ways to continue growing our operation in the San Francisco Bay Area, so we are thrilled that these state-of-the-art improvements to airport facilities will entice even more people to visit us here,” says Lori Augustine, Vice President of Airport Operations for United’s SFO Hub. “We’ve had an incredible partnership with the airport for many decades, and our work with them on the T3 West project is a symbol of our commitment to San Francisco and the faith we have in this city as one of the most desirable places to live, work, and visit.”
About the Design-Build Process
Traditionally, construction projects follow a design-bid-build (DBB) model. In this framework, the owner first hires an architect or designer to create detailed plans. Once the design is complete, contractors bid on the project, and the selected contractor executes the construction phase. While this approach provides clear delineation between roles, it often leads to fragmented communication, cost overruns, and extended timelines.
The design-build process, on the other hand, merges design and construction into a unified workflow. A single entity—typically a design-build firm or a consortium of design and construction professionals—takes full responsibility for all aspects of the project. This streamlined structure eliminates the silos of responsibility, paving the way for more efficient and effective project delivery.
Key Benefits of the Design-Build Process
1. Streamlined Communication and Collaboration
One of the standout advantages of the design-build approach is the seamless communication it fosters between design and construction teams. With both disciplines working in tandem from the project's inception, potential conflicts or misunderstandings are addressed early in the process. This collaborative environment ensures that the design is both aesthetically pleasing and practically feasible, reducing the likelihood of costly changes during construction.
For the owner, having a single point of contact simplifies communication. Rather than coordinating between separate design and construction entities, the owner engages directly with the design-build team, creating a cohesive and transparent relationship.
2. Accelerated Project Timelines
The integration of design and construction allows for overlapping phases, a practice known as "fast-tracking." For example, site preparation and foundation work can begin while design details for upper levels are still being finalized. This overlap minimizes downtime and significantly reduces overall project duration.
Moreover, the streamlined communication inherent in the design-build model helps to avoid delays caused by design discrepancies or disputes between stakeholders. With everyone on the same team, decisions are made more swiftly, keeping the project on schedule.
3. Cost Savings and Budget Control
By aligning design and construction under one contract, the design-build process provides a more accurate estimate of costs early in the project. This holistic approach helps owners avoid the budget surprises that often plague traditional DBB projects.
The design-build team is incentivized to stay within budget because they are responsible for both the design and construction phases. Additionally, the collaborative environment allows for value engineering, where cost-effective solutions are identified and implemented without compromising quality or functionality.
4. Reduced Risk for the Owner
In traditional DBB projects, the owner assumes the risk of coordinating between designers and contractors. If conflicts arise—such as a design that is impractical or incompatible with the construction plan—the owner often bears the burden of resolving them.
In the design-build model, the design-build team assumes full accountability for the project's success. This single-source responsibility reduces the owner's exposure to risk and simplifies dispute resolution, as there is no ambiguity about who is accountable for meeting project objectives.
5. Enhanced Innovation and Flexibility
The integrated nature of design-build fosters a culture of innovation. Designers and builders collaborate from the outset, pooling their expertise to develop creative solutions to complex challenges. This synergy often results in unique design elements, improved construction techniques, and more efficient use of materials.
Furthermore, the flexibility of the design-build model allows for adjustments to be made mid-project without disrupting the workflow. Because the team is unified, changes can be quickly assessed and implemented, ensuring that the project adapts to evolving needs or unforeseen circumstances.
6. Improved Quality Control
With a single team responsible for the entire project, quality assurance is built into every stage of the process. The design-build team is motivated to deliver high-quality results because their reputation and financial incentives depend on the project's success.
Additionally, the close collaboration between design and construction professionals ensures that the final product aligns with the owner's vision and meets all performance standards.
Real-World Applications of Design-Build
The design-build approach is well-suited for a wide range of projects, from large-scale infrastructure developments to custom residential builds. Its versatility has made it a preferred choice in industries such as healthcare, education, and transportation, where complex requirements and tight deadlines are common.
For example, many municipalities use design-build to accelerate the delivery of critical infrastructure, such as bridges and water treatment facilities. Similarly, private developers often rely on this method for commercial projects, where speed to market and cost efficiency are paramount.
How GPRS Supports Design-Build Projects
The design-build process represents a transformative shift in how construction projects like SFO’s expansion are delivered. By integrating design and construction into a cohesive and collaborative workflow, this approach offers substantial benefits, including faster timelines, lower costs, and improved quality.
GPRS provides accurate as-built site data to help design-build projects move seamlessly through the design and construction process.
Our utility locating, precision concrete scanning, pinpoint leak detection, and NASSCO-certified video pipe inspection services help you prevent subsurface damage and provide you with an accurate, complete picture of the subsurface infrastructure on your job site.
And our 3D laser scanning, photogrammetry, and SiteMap® (patent pending) infrastructure mapping software provide existing conditions documentation, and construction & facilities project management services to help you plan, design, manage, dig, and ultimately build better.
What can we help you visualize?