Cleanrooms are critical for industries ranging from pharmaceuticals to electronics. Maintaining a pristine cleanroom environment is not just about cleanliness. It’s also about ensuring the safety and quality of products and processes. This includes obtaining accurate measurements as efficiently as possible in these environments.
Industrial Safety & Hygiene News (ISHN) recently outlined effective strategies for achieving and sustaining a cleanroom's high standards.
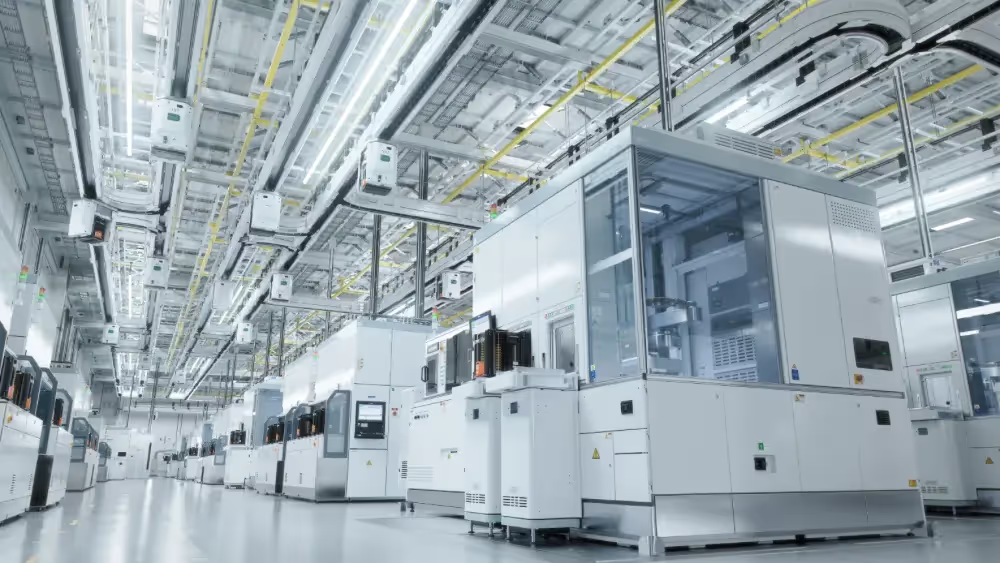
Understanding Cleanroom Standards
Cleanrooms are specialized environments where particulate contamination is strictly controlled. The cleanliness of a cleanroom is often categorized by the ISO standard, which ranges from ISO Class 1 (the cleanest) to ISO Class 9. These classes are defined by the maximum allowable particle count per cubic meter of air, making the maintenance of a pristine cleanroom crucial for meeting industry-specific requirements.
Key Contamination Control Strategies
1. Design and Construction
a. Layout and Material Selection:
The design of a cleanroom must prioritize the control of contamination sources. The layout should minimize areas where particles can accumulate. Surfaces should be smooth, non-porous, and easily cleanable. Materials like stainless steel, epoxy-coated walls, and specialized cleanroom flooring can help in maintaining hygiene and durability.
b. Airflow Systems:
Proper air handling is essential. Cleanrooms use High-Efficiency Particulate Air (HEPA) or Ultra-Low Particulate Air (ULPA) filters to remove contaminants from the air. Airflow systems must be designed to prevent air from becoming stagnant and to ensure that filtered air circulates effectively throughout the cleanroom.
2. Gowning and Personal Hygiene
a. Proper Gowning Procedures:
Personnel entering a cleanroom must follow strict gowning procedures. This typically includes wearing cleanroom suits, gloves, face masks, and shoe covers. Gowning should be done in a controlled area, known as a gowning room, where contamination is minimized.
b. Personal Hygiene:
Employees should adhere to rigorous hygiene practices before entering the cleanroom. This includes thorough handwashing with antiseptic agents and ensuring that personal items are not brought into the cleanroom.
3. Cleaning Protocols
a. Regular Cleaning Schedules:
Cleaning protocols should be clearly defined and followed meticulously. This includes regular cleaning of surfaces, equipment, and floors using approved cleaning agents that do not leave residues or generate particles.
b. Cleaning Equipment:
The tools used for cleaning should be specifically designed for cleanroom environments. For instance, mop heads and wipes should be made from non-shedding materials and should be regularly replaced to prevent contamination.
4. Monitoring and Testing
a. Environmental Monitoring:
Regular monitoring of the cleanroom environment is essential for ensuring that contamination levels remain within acceptable limits. This includes measuring particulate counts, microbial contamination, and assessing the efficiency of air filtration systems.
b. Data Analysis:
Data collected from environmental monitoring should be analyzed to identify trends or potential sources of contamination. This helps in preemptively addressing issues before they escalate into more significant problems.
5. Maintenance of Equipment
a. Routine Maintenance:
Equipment used in cleanrooms must be maintained regularly to ensure optimal performance. This includes calibrating instruments, checking for wear and tear, and replacing parts as necessary.
b. Validation and Verification:
Regular validation and verification of cleanroom systems and equipment are crucial. This ensures that all systems are functioning as intended and that they meet the required cleanliness standards.
6. Training and Awareness
a. Staff Training:
Personnel should receive comprehensive training on cleanroom protocols and contamination control. This includes understanding the impact of their actions on cleanroom conditions and the importance of adhering to procedures.
b. Continuous Education:
Keeping staff updated on the latest industry practices and technological advancements helps maintain high standards of cleanliness and contamination control.
7. Incident Management
a. Immediate Response:
In the event of a contamination incident, immediate action is required. This involves isolating the affected area, identifying the cause, and implementing corrective measures to restore the cleanroom to its required standards.
b. Root Cause Analysis:
A thorough investigation should be conducted to determine the root cause of contamination. Addressing the underlying issue helps in preventing future occurrences and improving overall cleanroom management.
Challenges and Solutions
Maintaining a pristine cleanroom environment comes with its set of challenges. Common issues include particle contamination from external sources, human error, and equipment malfunction. Addressing these challenges requires a multi-faceted approach:
- Particle Contamination: External sources such as construction activities or nearby manufacturing processes can introduce contaminants. Solutions include proper air filtration, controlled access to the cleanroom, and using barriers to minimize the introduction of particles
- Human Error: Mistakes made by personnel, such as improper gowning or lapses in cleaning procedures, can lead to contamination. Continuous training and adherence to strict protocols are key to mitigating human errors
- Equipment Malfunction: Regular maintenance and validation of equipment are crucial to prevent failures that could compromise cleanroom integrity.
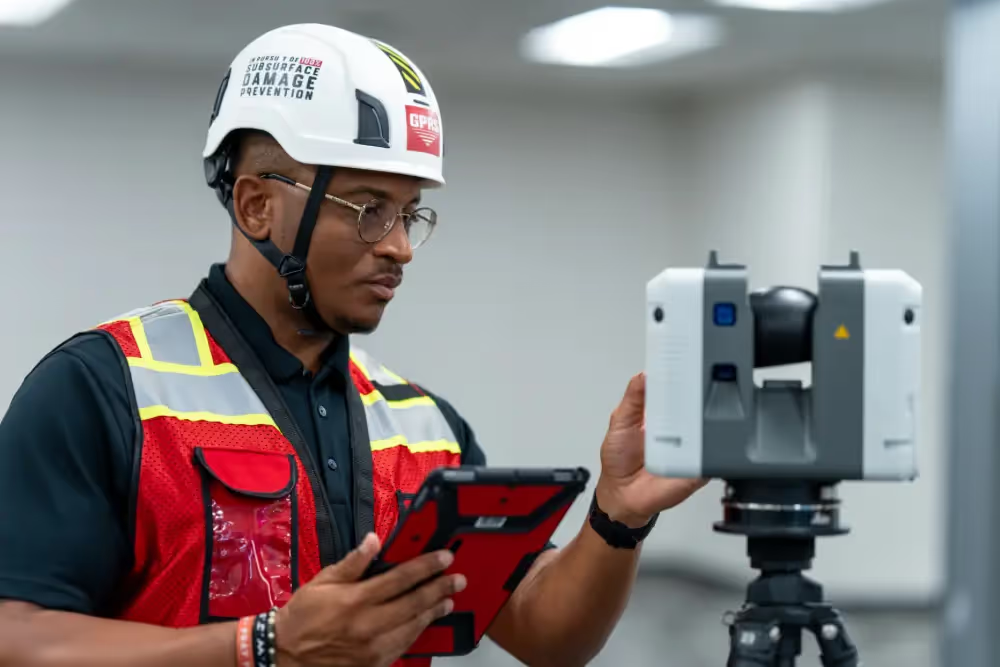
GPRS Captures Accurate Data in Cleanrooms
When you need to conduct operations & maintenance in a cleanroom environment, speed and efficiency are critical.
GPRS 3D Laser Scanning services provide precise as-built documentation for buildings, facilities, and sites. Our expert Project Managers use Leica scanners, Autodesk and Bentley software, and advanced scan-to-BIM processes to deliver 2-4mm accurate LiDAR point clouds, 2D floor plans, CAD drawings, 3D BIM models, 3D mesh models, 3D photogrammetry, 3D virtual tours, and more for effective project planning and collaboration across disciplines.
While the amount of space we can scan in a day can vary widely depending on the complexity of the environment being scanned, our highly trained Project Managers can typically scan a vacant spaces or smaller rooms in one day, and larger facilities within a few days depending on how densely packed equipment is. So, we’ll get the most accurate data possible as quickly as possible, ensuring your cleanroom stays clean.
GPRS created SiteMap® (patent pending) to ensure your entire project team can access this accurate, field-verified data from anywhere at any time. This project & facility management application provides accurate existing conditions documentation to protect your assets and people. And you’ll be able to share it with your entire team, and access it from any computer, tablet, or smartphone.
What can we help you visualize?
Frequently Asked Questions
Is 3D laser scanning right for my project?
Almost any project that requires as-built information can benefit from 3D laser scanning services. Talk with our experts and start your 3D laser scanning survey project today.
What is a digital twin?
A digital twin is highly complex virtual model that is the exact counterpart (or twin) of a physical object. GPRS uses 3D laser scanners to collect real-time data for a building or facility and create a digital duplicate. Data can be easily visualized, measured and analyzed. Digital twins can be used to improve efficiencies, optimize workflows and detect problems before they occur.
What is the difference between a design intent and an as-built model?
DESIGN INTENT – deliverables will be shown as a "best fit" to the point cloud working within customary standards, such as walls being modeled 90 degrees perpendicular to the floor, pipes and conduit modeled straight, floors and ceilings modeled horizontal, and steel members modeled straight. This will produce cleaner 2D drawings and will allow for easier dimensioning of the scan area. The deliverables will not exactly follow the scan data to maintain design intent standards. Most clients will want this option for their deliverables.
AS-BUILTS – deliverables will be shown as close as possible to actual field capture. If walls are out of plumb, pipes and conduit show sag, floors and ceilings are unlevel, steel members show camber, etc., this will be reflected in the model. This will produce reality-capture deliverables, but 2D drawings may show “crooked” or out of plumb lines, floors will be sloped or contoured, steel members may show camber, twisting or impact damage. Dimensioning will not be as easy due being out of plumbness/levelness, etc. This option should be used when the exact conditions of the scan area is imperative. Clients using the data for fabrication, forensic analysis, bolt hole patterns, camber/sag/deformation analysis, and similar needs would require this option.
What if my project is limited within the physical setting?
Some projects require special applications due to limitations within the physical setting. Often, this is due to line-of-sight issues and when a scan must be done safely from the ground or with precautionary distance. Some of these applications would include above-ceiling MEP features in hospitals where it is necessary to maintain negative airflow or interstitial spaces that are congested with limited access. Since laser scanning is a non-contact measurement tool (i.e. we can scan from a safe distance or location) this becomes a powerful tool for solving these complex challenges.