As urbanization and infrastructure demands increase, the need for efficient underground utility installations has never been greater.
Traditional tunnel-boring methods, while effective, often face challenges related to cost, speed, and environmental impact. A cutting-edge solution that is gaining traction is plasma tunnel-boring technology. This emerging method is being spearheaded by San Francisco-based startup Earthgrid, and leverages high-energy plasma to cut through rock and soil, offering a potential revolution in underground excavation.
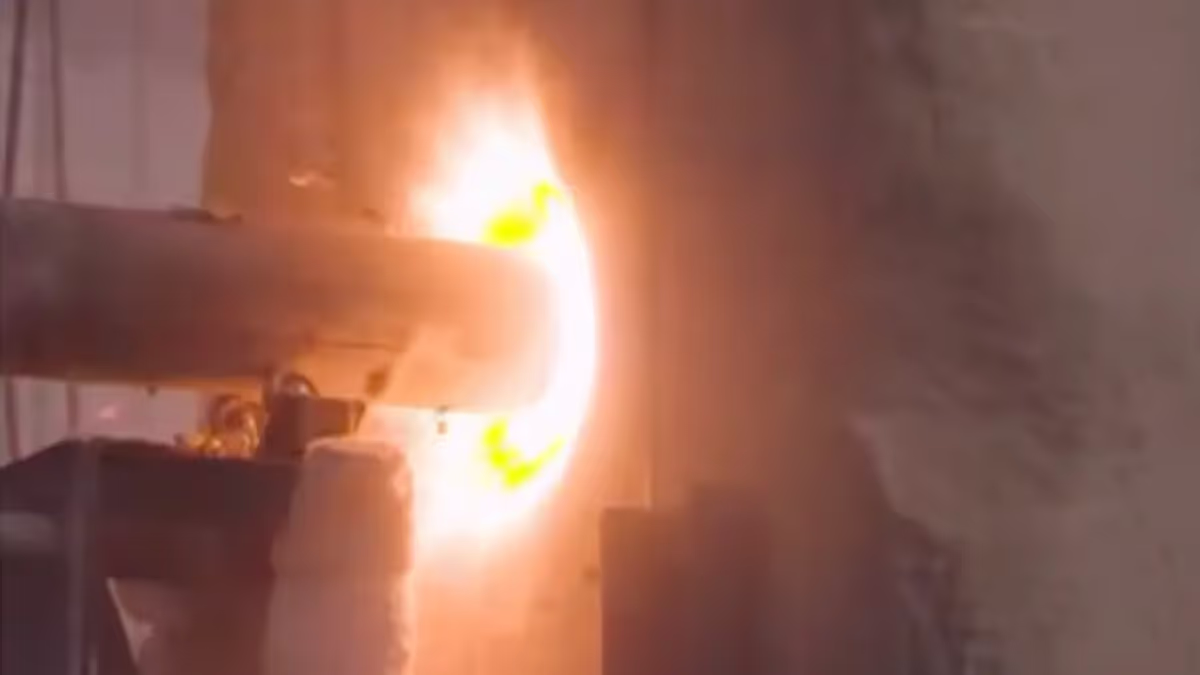
Understanding Plasma Tunnel-Boring Technology
Plasma tunnel-boring technology utilizes superheated, ionized gas—plasma—to break through rock, melting and vaporizing it rather than mechanically cutting or grinding. This process is fundamentally different from traditional mechanical tunnel-boring machines (TBMs), which rely on rotating cutting heads equipped with discs or cutters.
The plasma process works by generating extremely high temperatures, often exceeding 10,000 degrees Celsius (18,000 degrees Fahrenheit). The intense heat melts rock into a molten state, and the resulting vaporized material is either extracted via a vacuum system or allowed to solidify into a stable glass-like material.
While still in its developmental and early deployment phases, this technology has been proposed as a more efficient alternative to conventional excavation methods, particularly for hard rock tunneling.
Advantages of Plasma Tunnel-Boring Technology
Increased Tunneling Speed
One of the primary advantages of plasma tunnel-boring is its ability to significantly accelerate the excavation process. Traditional TBMs can be slow, especially when encountering particularly hard rock formations. Plasma-based boring eliminates the mechanical wear and tear associated with cutter heads, allowing for continuous operation without frequent maintenance-related downtime.
Reduced Wear and Tear
Mechanical TBMs experience wear on their cutting discs, requiring regular maintenance and replacements, which increase operational costs and project timelines. Plasma tunneling, on the other hand, does not rely on direct mechanical contact with rock, reducing equipment degradation and maintenance needs.
Lower Environmental Impact
Compared to conventional excavation methods, plasma tunneling generates less vibration and noise, making it ideal for urban environments where minimizing disturbance is critical. Additionally, because the process vaporizes rock rather than displacing it, there is less need for waste removal and storage.
Enhanced Precision and Versatility
Plasma technology allows for greater control over tunnel size and shape, enabling more precise excavations. This feature is particularly beneficial for utility installations, where specific dimensions and alignments are often required.
Potential Cost Savings
While initial investment costs for plasma tunnel-boring equipment may be high, the long-term savings from reduced labor, maintenance, and material handling could make it an economically viable option. Faster excavation times can also reduce overall project costs and lead to quicker returns on investment.
Challenges and Limitations
Despite its promising advantages, plasma tunnel-boring technology faces several challenges that must be addressed before widespread adoption.
High Energy Requirements
Generating plasma requires substantial amounts of energy. This demand raises concerns about operational costs and environmental sustainability, particularly in regions where electricity generation is carbon-intensive. Developing more energy-efficient plasma systems or integrating renewable energy sources could help mitigate this challenge.
Initial Investment and Infrastructure
The equipment required for plasma tunneling is still in the early stages of commercialization. Acquiring and deploying such technology requires significant capital investment, making it less accessible for smaller-scale projects. Additionally, specialized training and workforce development are necessary for effective operation.
Material Handling Considerations
While plasma tunneling minimizes traditional spoil generation, the melted and vaporized rock must be managed properly. If not efficiently extracted or solidified, it could pose operational risks or create unintended geological consequences. Ensuring proper containment and disposal mechanisms is crucial for safe implementation.
Limited Field Testing and Commercial Adoption
As of now, plasma tunnel-boring technology has not been widely adopted in large-scale infrastructure projects. Further field testing and real-world applications are needed to refine the technology, validate its economic feasibility, and build industry confidence.
Applications in Utility Installations
The unique capabilities of plasma tunnel-boring technology make it highly attractive for various utility installation scenarios, particularly in dense urban areas where traditional excavation methods pose challenges.
Underground Electrical and Fiber Optic Installations
With increasing demand for high-speed internet and advanced electrical grid systems, underground cabling projects require efficient tunneling methods. Plasma boring can facilitate rapid conduit installation with minimal surface disruption, making it an ideal solution for urban infrastructure expansion.
Water and Sewer Systems
Expanding or upgrading underground water and sewer pipelines often requires tunneling through difficult geological conditions. Plasma-based excavation could enhance efficiency in these projects, particularly when working in rock-heavy terrains.
Gas and Oil Pipeline Installations
The oil and gas industry frequently requires underground pipeline installations in remote or geologically challenging areas. Plasma tunneling’s ability to penetrate hard rock quickly and with minimal surface impact makes it a valuable tool for these applications.
Microtunneling and Trenchless Technologies
Trenchless utility installation methods are increasingly preferred due to their reduced surface impact. Plasma tunneling can further improve the effectiveness of microtunneling, enabling more precise and rapid underground boring with fewer environmental disruptions.
Future Outlook
As plasma tunnel-boring technology continues to develop, several key advancements are expected to drive its adoption in the utility installation sector:
- Energy Efficiency Improvements: Research into lower-energy plasma generation methods and integration with renewable energy sources could make plasma tunneling more sustainable and cost-effective
- Automation and AI Integration: Enhanced automation and artificial intelligence could optimize plasma boring operations, reducing human intervention and improving precision
- Regulatory and Industry Standardization: Widespread adoption of plasma tunneling will require clear regulations and industry standards to ensure safety, efficiency, and environmental compliance
- Expanded Pilot Projects: More large-scale pilot projects are needed to demonstrate the technology’s viability in real-world conditions and encourage investment from the private and public sectors
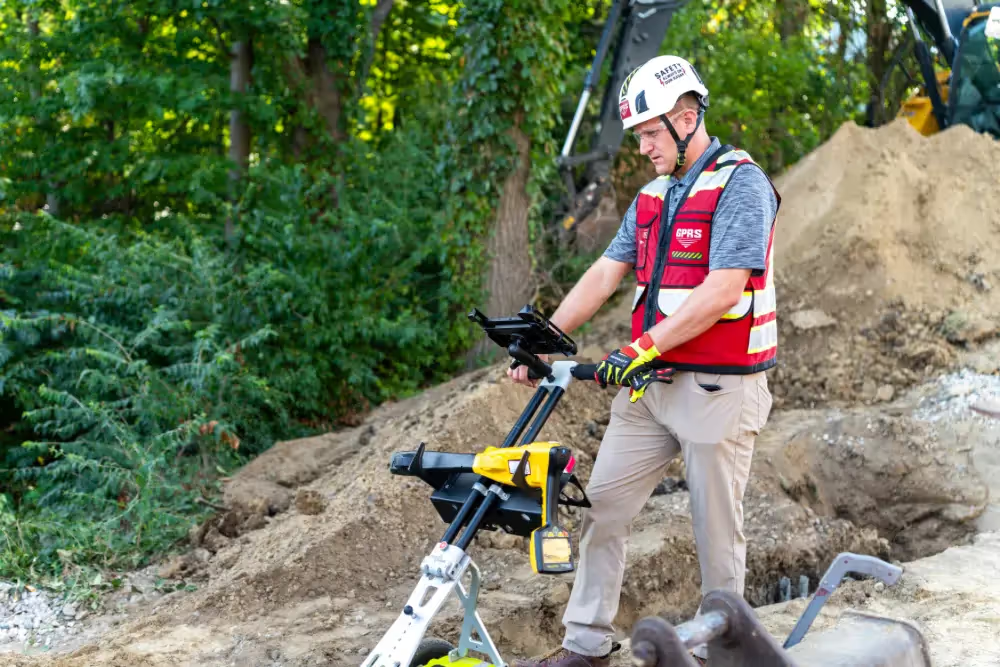
Whether you’re breaking ground with plasma, microtrenching with more traditional methods, or fully excavating a site, it’s vital to know what’s already below before you dig.
GPRS offers a comprehensive suite of subsurface damage prevention services, including precision utility locating utilizing ground penetrating radar (GPR) scanners and electromagnetic (EM) locators.
This accurate, field-verified data is always at your fingertips thanks to SiteMap® (patent pending), GPRS’ project & facility management application that provides accurate existing conditions documentation to protect your assets and people.
From skyscrapers to sewer lines, GPRS Intelligently Visualizes The Built World® to keep your projects on time, on budget, and safe.
What can we help you visualize?
Frequently Asked Questions
Is GPRS able to distinguish between different types of underground utilities?
Yes, our SIM-certified Project Managers can usually identify the utility in question without any problems. It’s not always possible, however. In cases where we can’t determine what type of utility is present, we attempt to trace the utility to a valve, meter, control box, or other signifying markers to determine the type of utility buried.
Will I need to mark out the utilities that GPRS locates?
No, GPRS will locate and mark all utilities for you. We have a variety of tools and markers we can use to highlight the locations of utilities, underground storage tanks (USTs), and whatever else may be hiding.