Post tension cables are a critical component in modern construction, offering enhanced strength and flexibility to concrete structures.
This technology allows engineers to build longer spans, thinner slabs, and more complex designs than would be possible with traditional reinforced concrete.
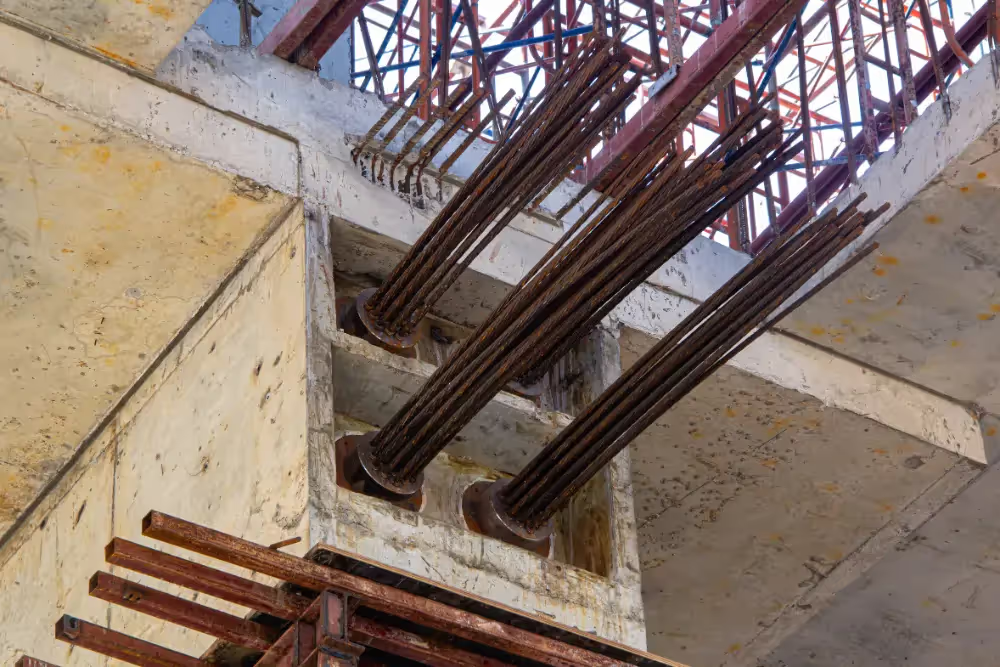
What are Post Tension Cables?
Post tension cables, also known as tendons, are steel cables that are used to reinforce concrete. Unlike traditional rebar, which is embedded in concrete before it hardens, post tension cables are tensioned (tightened) after the concrete has been cast and has gained sufficient strength. This process imparts a compressive force (a physical force pressing inward on an object, causing it to be compacted) to the concrete, counteracting the tensile (stretching) forces that the structure will experience during use.
The Mechanics of Post Tensioning
Pre-Tensioning vs. Post-Tensioning
To understand post-tensioning, it's essential to distinguish it from pre-tensioning. In pre-tensioning, steel tendons are tensioned before the concrete is poured. The tension is released after the concrete has set, transferring the compressive force to the concrete. This method is commonly used in precast concrete products, such as beams and slabs.
In post-tensioning, the steel cables are placed within ducts or sleeves in the concrete formwork. After the concrete has cured and achieved a specified strength, the cables are tensioned using hydraulic jacks and then anchored in place. This technique allows for on-site application and greater flexibility in design and construction.
The Post-Tensioning Process
1. Design and Planning: Engineers design the post-tensioning system based on the structural requirements of the project. This includes determining the number, placement, and tensioning force of the cables.
2. Placement of Cables: Steel cables, encased in plastic or metal ducts, are arranged within the concrete formwork according to the design specifications. These ducts are often curved to follow the optimal stress paths within the concrete.
3. Concrete Pouring: Concrete is poured into the formwork, encapsulating the ducts and cables. Care is taken to ensure that the concrete is well-compacted and that the ducts are properly positioned.
4. Curing: The concrete is allowed to cure and gain sufficient strength, typically over a period of several days to weeks, depending on the project specifications and environmental conditions.
5. Tensioning: Hydraulic jacks are used to tension the cables. The jacks pull the cables to the required force, stretching them within the ducts. This process imparts a compressive force to the surrounding concrete.
6. Anchoring: Once the desired tension is achieved, the cables are anchored at both ends using specialized hardware. The anchors hold the cables in place, maintaining the compressive force within the concrete.
7. Grouting (optional): In some cases, the ducts are filled with grout to protect the cables from corrosion and to improve the bond between the cables and the concrete.
Why Contractors Use Post Tension Cables
Increased Load Capacity
Post tension cables significantly enhance the load-bearing capacity of concrete structures. The compressive force introduced by the tensioned cables counteracts tensile stresses, reducing the likelihood of cracking and increasing the overall strength of the structure.
Design Flexibility
Post-tensioning allows for greater design flexibility compared to traditional reinforced concrete. Engineers can create longer spans, thinner slabs, and more intricate shapes, making it possible to achieve architectural designs that would be challenging or impossible with conventional methods.
Material Efficiency
The use of post tension cables can reduce the amount of concrete and steel required for a given project. Thinner slabs and longer spans mean less material is needed, leading to cost savings and a smaller environmental footprint.
Reduced Maintenance
Structures reinforced with post tension cables tend to have fewer cracks and require less maintenance over their lifespan. The compressive force helps to keep the concrete in compression, reducing the risk of damage from tensile stresses.
Applications of Post Tension Cables
Bridges and Overpasses
Post-tensioning is widely used in the construction of bridges and overpasses, where long spans and high load capacities are essential. The technique allows for the creation of slender, elegant structures that can withstand heavy traffic loads and harsh environmental conditions.
High-Rise Buildings
In high-rise construction, post-tension cables enable the creation of thinner floor slabs and longer spans between columns. This reduces the overall weight of the building and allows for more flexible interior layouts.
Parking Structures
Parking structures benefit from post-tensioning due to the need for long, column-free spans and durable, crack-resistant surfaces. The technique helps to maximize usable space and extend the lifespan of the structure.
Industrial Floors and Slabs
Post-tensioning is also used in the construction of large industrial floors and slabs, where heavy loads and minimal cracking are crucial. The technique provides a durable, high-performance surface capable of withstanding the demands of industrial operations.
Post Tension Cable Limitations
While post-tensioning offers many advantages, it also presents some challenges and considerations. Proper design and installation are critical to ensure the success of a post-tensioning system. Engineers and contractors must be trained and experienced in post-tensioning techniques to avoid issues such as improper tensioning, duct alignment problems, or inadequate anchoring.
Additionally, post-tensioned structures require careful inspection and maintenance to ensure the integrity of the cables and anchors over time. Corrosion protection, regular inspections, and timely repairs are essential to maintaining the long-term performance of post-tensioned systems.
Post tension cables have revolutionized the field of construction, offering enhanced strength, flexibility, and efficiency to concrete structures. By understanding the mechanics of post-tensioning and its benefits, engineers and builders can leverage this technology to create innovative and resilient designs. As the construction industry continues to evolve, post-tensioning will remain a vital technique for meeting the demands of modern infrastructure projects.
GPRS Protects Your Post-Tensioned Slabs
Mapping the post-tensioned support grid in your concrete slab facilitates design and minimizes the risk of injuries and delays. GPRS Concrete Scanning services utilize ground penetrating radar (GPR) to locate and map the PT cable, preventing costly and potentially dangerous subsurface damage.
From skyscrapers to sewer lines, GPRS Intelligently Visualizes The Built World® to keep your projects on time, on budget, and safe.
What can we help you visualize?
Frequently Asked Questions
How is Ground Penetrating Radar Used to Identify Tendons vs. Rebar in a Post-Tensioned Slab?
In post-tensioned structures, we typically find one mat of support rebar near the base of the slab. This mat is generally consistently spaced and remains at a constant elevation. Post-tension cables are generally found above this support mat and “draped” throughout the rest of the structure. The elevation of the cable is usually high near the beams and column lines and drapes lower through the span between beams and column lines. Knowledge of these structural differences allows us to accurately differentiate between components. Our Project Managers will leave you feeling confident in our findings and in your ability to drill or cut without issue.
Can Ground Penetrating Radar the Difference Between Rebar and Electrical Conduit?
Ground penetrating radar (GPR) can accurately differentiate between rebar and electrical conduit in most cases. We have an extremely high success rate in identifying electrical lines in supported slabs or slabs-on-grade before saw cutting or core drilling.
Additionally, GPRS can use electromagnetic (EM) locators to determine the location of conduits in the concrete. If we can transmit a signal onto the metal conduit, we can locate it with pinpoint accuracy. We can also find the conduit passively if a live electrical current runs through it.
The combined use of GPR and EM induction allows us to provide one of the most comprehensive and accurate conduits locating services available.