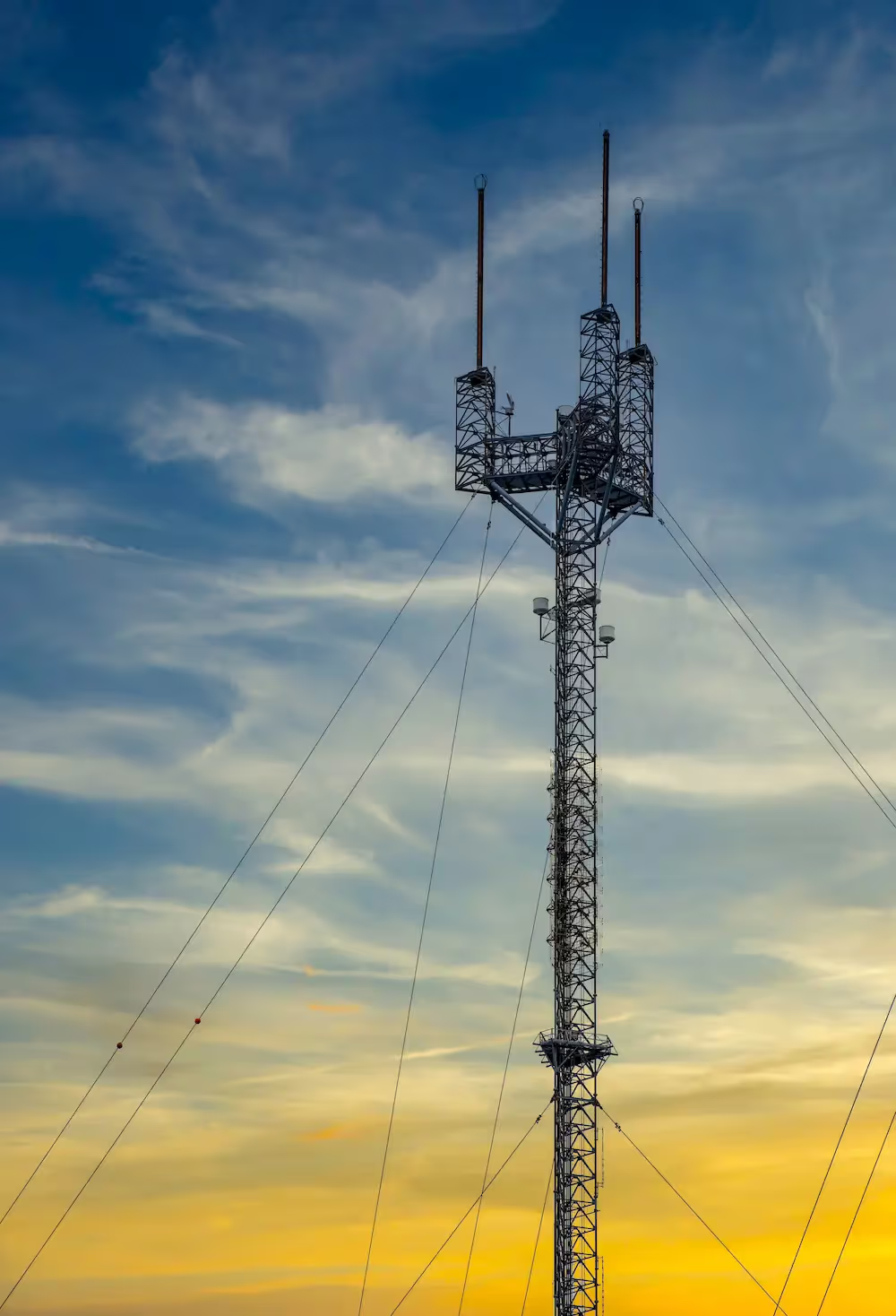
As telecommunications and fiber optic networks expand to encompass the entire United States, they require additional infrastructure support. Whether you’re installing a new small cell network to tackle capacity and density issues, or erecting freestanding cellular towers to support more antennas and bandwidth, there are important safety issues you have to take into account.
For example, while small cell sites bring coverage to areas with line of sight or data density issues, their dependence on fiber optic lines also brings serious concerns regarding directional drilling usage and safety.
Erecting additional large cell towers is a necessity to ensure nationwide data coverage. Erecting those towers safely, and maintaining them, create their own concerns. According to the Occupational Safety and Health Administration (OSHA), 147 people have perished while working on cellular towers between 2003 and 2022.
However, in virtually every major natural disaster, and sometimes just from the perils of age, cellular towers degrade, crumple, and collapse (fail), taking down what has become a critical piece of national communications infrastructure. To help cellular tower operators keep the network up and running, the Federal Emergency Management Agency (FEMA) issued a Fact Sheet in 2022 for Communication Towers, Masts, and Antennas, stating that its goal is to “improve the resilience of communications towers, masts and antennas that support vital communications functions.”
What is the first mitigation source listed in FEMA’s table? An Anchor. Adding bracing & guy wires is number two.
In the three decades since cellular phones became viable, their network has exploded to 142,100 large cell towers, and 452,200 small cell sites in the U.S. (as of 2022). A majority of those 142,100 large cellular towers require a sturdy foundation, guy wires, and anchors to keep them upright and safe. They also require inspection and certification at least once every three years to be sure the anchors and guy wires are intact, free of rust, and corrosion.
What Are Guy Wire Anchors?
A guy wire anchor is a metal anchor that provides a point of contact and stabilization for the attachment of a guy wire from structures like telecom towers. While there are a variety of anchors available, and some companies prefer what’s known as an “earth anchor” to support their structure, guy wire anchors are most often set into a concrete anchor block and buried into the soil outside the tower compound.
Why is Concrete Used for Anchor Blocks?
The short answer is protection.
Electricity and chemical reactions among the metal, soil, and air all lead to guy wire and anchor corrosion. Corrosion is an electrochemical process that breaks down refined steel. For corrosion to take place, it requires an anode, cathode, electrolyte, and a pathway for electricity to travel. In the case of guy wire anchors, the anchor shaft acts as the anode, the tower’s ground rod acts as the cathode, the soil becomes the electrolyte, and the electricity travels the path of least resistance.
When an anchor is installed directly into the soil, it is immediately subject to corrosion. Depending on the variety of the soil and its resistivity, that corrosion can be very swift.
The soil’s moisture, its pH level, stray electrical currents, and how closely the anchor is located to dissimilar metals all contribute to corrosion.
Soil resistivity – the ability for the soil to resist instead of conduct corrosive chemical reactions – is very important when considering tower and guy wire anchor installations.
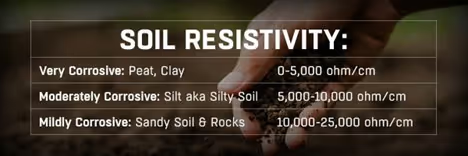
- Very corrosive soil structure would include peat and clay soils in wet climate conditions
- Moderately corrosive soil, often called silts or silty soils, are made up of loose sedimentary material (usually quartz or particulate rock)
- Mildly corrosive soils are usually found in dry climate conditions and are composed of sands and/or rocks
So, protecting the anchor shaft from direct contact with the soil – and the corrosion that follows – is very important. That’s where concrete comes into play. Concrete has extremely high electrical resistivity, insulating the anchor shaft from the anode/cathode relationship required for corrosion to take place. Plus, in locations without a rock or bedrock area in which to anchor, the concrete anchor block can provide additional reinforcement.
The other popular corrosion insulator for guy wire anchors is epoxy, which can certainly be applied to the soil-submerged area of the anchor shaft that is not encased in concrete, and is used to coat earth anchors. However, according to the National Association of Tower Erectors (NATE), any inconsistencies in the application, or even in the transportation of the epoxy, can leave openings through which corrosion can gain entry.
How Deep Do You Need to Bury a Concrete Guy Wire Anchor Block?
Guy wires are generally installed at a 45-degree angle from the tower and at intervals of 120 degrees apart outside of the tower compound. The height and weight of the tower are utilized in some basic geometric calculations to determine the depth at which the guy wire anchor needs to be installed. In most cases, that depth is 90 feet or greater. It is inefficient to encase the entire anchor shaft in concrete at that depth, so the remaining anchor that will come in contact with the surrounding soil is usually epoxy coated to retard corrosion.
What Are the Risks to Burying Guy Wire Anchors?
Regardless of the anchor type, sinking any piece of metal 90 feet into the ground comes with inherent risk. As mentioned above, the overarching risks include time and corrosion, but there is another, more immediate and dangerous risk to anchoring cellular tower guy wires – underground utility strikes.
While it is true that the utility infrastructure outside the tower compound is less crowded than the utilities inside, it is crucial to identify every subsurface feature you can prior to anchoring. That way, you can be sure you avoid severing another critical piece of utility infrastructure, which could not only cause expensive damages, but could endanger workers with a potential gas line explosion or electrocution.
GPRS Intelligently Visualizes the Built World® for the telecom industry. Our 99.8% accurate subsurface utility locating & mapping help customers avoid mistakes and utility strikes when installing towers, and we provide pre and post-cross bore inspections for small cell site fiber optic line installations to ensure your directional boring installations don’t compromise existing utilities. All your utility maps and inspection reports are digitally delivered via SiteMap®, our infrastructure management platform. Every GPRS customer receives a complimentary SiteMap® Personal subscription, so you can access your data from anywhere 24/7 via your computer or our SiteMap® mobile app.
What can we help you visualize?