In the construction industry, labor is one of the most significant expenses, often accounting for a large portion of a project's total cost.
Any inefficiency in labor management can have a substantial impact on a project's budget and overall profitability.
A recent Construction Dive article cited a new study which found that about half of contractors see labor inefficiencies worsening. U.S. contractors reportedly wasted between $30 billion and $40 billion in 2022 due to labor inefficiencies.
Inefficiencies in construction labor can arise from various sources, including poor planning, inadequate communication, lack of training, and ineffective use of technology. These inefficiencies not only increase costs, they also lead to delays, reduced quality, and lower worker morale.
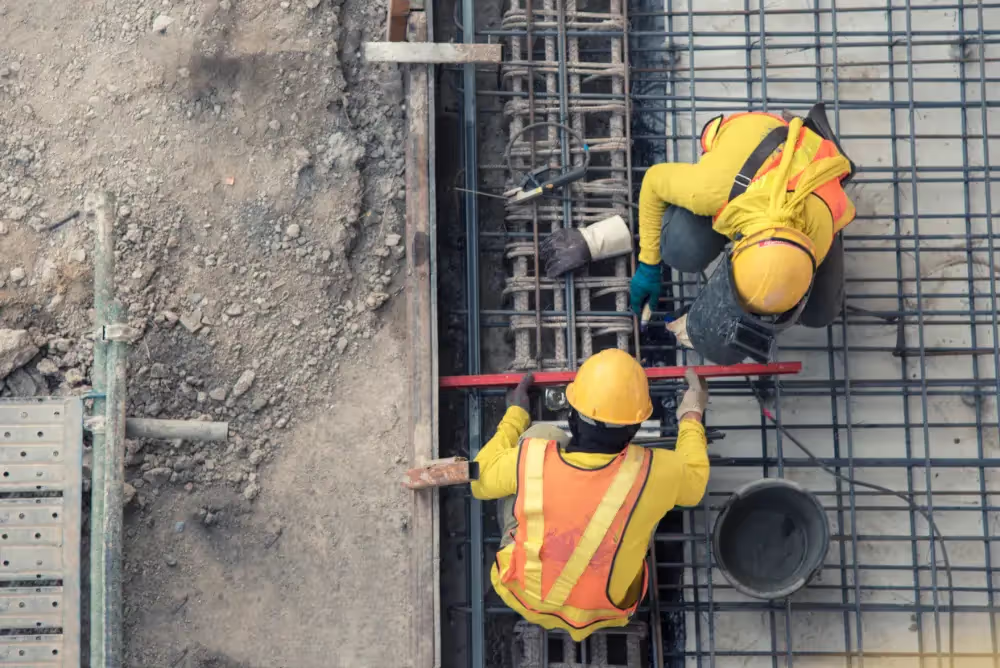
Poor Planning and Coordination
When projects are not properly planned, workers may find themselves waiting for materials, equipment, or instructions, leading to idle time and wasted labor hours. Additionally, poor coordination between different teams or subcontractors can result in overlapping tasks or rework, further increasing labor costs. Effective project management and scheduling are crucial to minimizing these inefficiencies and ensuring that labor is utilized effectively.
Inadequate Communication
Communication is key in any construction project, and a lack of clear communication can lead to misunderstandings, errors, and reworks. When workers are not fully informed about project goals, specifications, or changes, they are more likely to make mistakes that require additional time and resources to correct. Implementing regular team meetings, clear channels of communication, and accessible project documentation can help reduce these inefficiencies.
Lack of Training and Skills
The construction industry is constantly evolving, with new techniques, materials, and technologies introduced regularly. A workforce that is not adequately trained or skilled in these areas can lead to inefficiencies, as workers may take longer to complete tasks or make errors that require correction. Investing in ongoing training and professional development is essential to ensure that workers are equipped with the necessary skills and knowledge to perform their tasks efficiently.
Ineffective Use of Technology
Technology has the potential to greatly enhance efficiency in the construction industry, but only if it is used effectively. Many construction companies have been slow to adopt new technologies, such as building information modeling (BIM), project management software, and automated machinery. These tools can streamline processes, reduce errors, and improve communication, but they require an upfront investment in both equipment and training. Companies that fail to leverage technology effectively may find themselves at a competitive disadvantage, with higher labor costs and longer project timelines.
Impact on Project Costs
The impact of labor inefficiencies on project costs can be significant. Delays and rework not only increase direct labor costs but can also lead to penalties for missed deadlines, additional material costs, and increased overhead expenses. In a highly competitive industry, these added costs can erode profit margins and make it difficult for companies to remain viable.
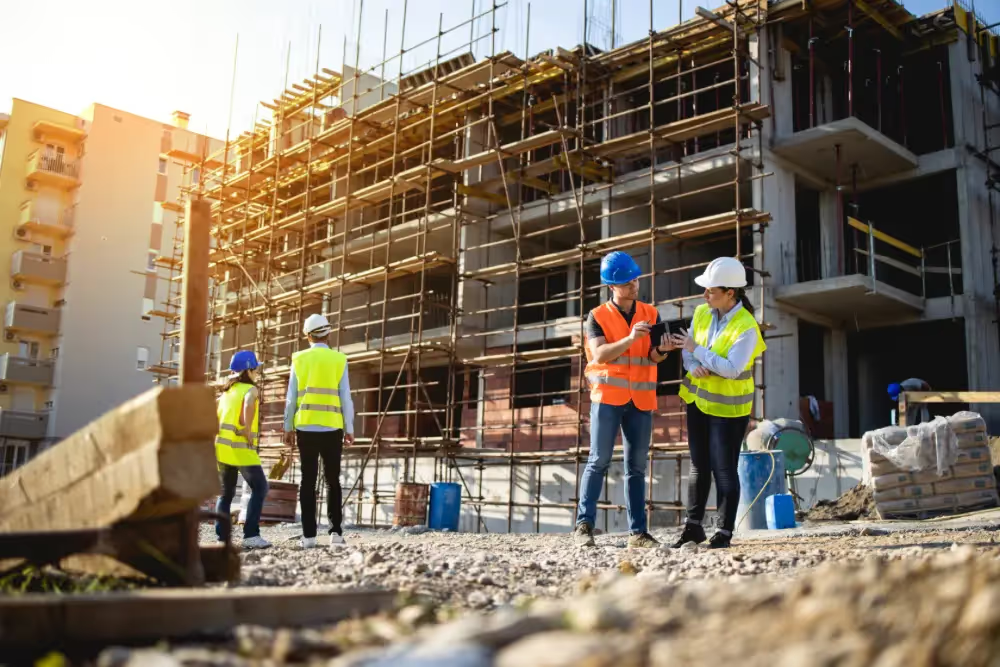
Solutions for Improving Labor Efficiency
Lean building practices, derived from the principles of lean manufacturing, can significantly improve labor inefficiencies in the construction industry. These practices focus on minimizing waste and maximizing value, leading to more efficient use of resources, including labor.
Here are some ways in which lean building practices can address labor inefficiencies:
Value Stream Mapping:
Lean building practices involve mapping out the entire construction process to identify every step that adds value and those that do not. By eliminating non-value-adding steps, such as wait time or unnecessary movement of materials, construction companies can ensure that labor is focused on productive tasks, thereby reducing inefficiencies.
Just-in-Time (JIT) Delivery:
Incorporating JIT delivery into construction projects ensures that materials are delivered exactly when needed, reducing the time workers spend waiting for materials or handling and storing excess inventory. This approach not only streamlines the construction process but also minimizes the chances of delays due to material shortages.
Pull Planning and Scheduling:
Unlike traditional push-based scheduling, lean construction uses a pull planning system, where tasks are scheduled based on the demand and readiness of the subsequent steps in the process. This approach ensures that workers are not idle waiting for the next task and reduces bottlenecks in the workflow.
Collaborative Teamwork:
Lean building practices emphasize collaboration among all stakeholders, including architects, engineers, contractors, and suppliers. This collaborative approach ensures clear communication, better coordination, and a shared understanding of project goals, leading to fewer mistakes and rework, which are major sources of labor inefficiency.
Continuous Improvement:
Lean construction encourages continuous improvement through regular reflection and learning. By analyzing past projects and identifying areas for improvement, construction teams can implement changes that enhance labor efficiency in future projects.
Standardization and Prefabrication:
Standardizing processes and using prefabricated components can significantly reduce the time and labor required on-site. Prefabrication allows for work to be done in a controlled environment, which can improve quality and reduce the need for rework, further enhancing labor efficiency.
Empowering Workers:
Lean building practices empower workers to identify inefficiencies and suggest improvements. This not only improves morale but also harnesses the collective experience of the workforce to find innovative ways to increase efficiency.
By adopting lean building practices, construction companies can address the root causes of labor inefficiencies, leading to more streamlined and cost-effective projects. These practices not only improve the bottom line but also contribute to higher quality construction, better worker satisfaction, and a more sustainable industry overall.
Investing in efficient labor practices is not only good for business but also contributes to the overall success and sustainability of the construction industry.
Frequently Asked Questions
What are the key principles of lean building?
The key principles of lean building focus on maximizing value and minimizing waste throughout the construction process. These principles include:
- Value Definition: Understanding and defining what adds value from the customer's perspective.
- Value Stream Mapping: Identifying and mapping out all the steps in the construction process to highlight value-adding activities and eliminate waste.
- Flow: Ensuring that work progresses smoothly and continuously without interruptions or delays.
- Pull Planning: Scheduling work based on demand and downstream readiness, rather than pushing tasks according to a predetermined schedule.
- Continuous Improvement: Regularly seeking ways to improve processes, reduce waste, and increase efficiency.
How do lean building principles benefit construction projects?
Lean building principles can significantly benefit construction projects in several ways:
- Reduced Waste: By focusing on value and eliminating non-value-adding activities, lean building minimizes waste in materials, time, and labor.
- Improved Efficiency: Streamlined processes and continuous improvement lead to more efficient use of resources and a faster construction timeline.
- Better Quality: Attention to detail and a focus on value result in higher quality construction and fewer defects or rework.
- Enhanced Collaboration: Lean building promotes collaboration among all stakeholders, leading to better communication, coordination, and alignment of project goals.
- Increased Customer Satisfaction: By delivering projects that meet or exceed customer expectations in terms of quality, cost, and time, lean building principles enhance overall customer satisfaction.