In the best-case scenario, critical safety communication on a job site or in a facility takes place face-to-face in real time. It’s why general contractors and facilities large and small employ safety teams and managers, so that when they encounter a worker at risk, be it from exposure to a hazardous material, a work environment that requires extra safety measures, or unsafe work behavior, it can be addressed and corrected. That way, everyone involved experiences straight-line communication: where a message is given, received, and acknowledged. This provides a safer site for everyone.
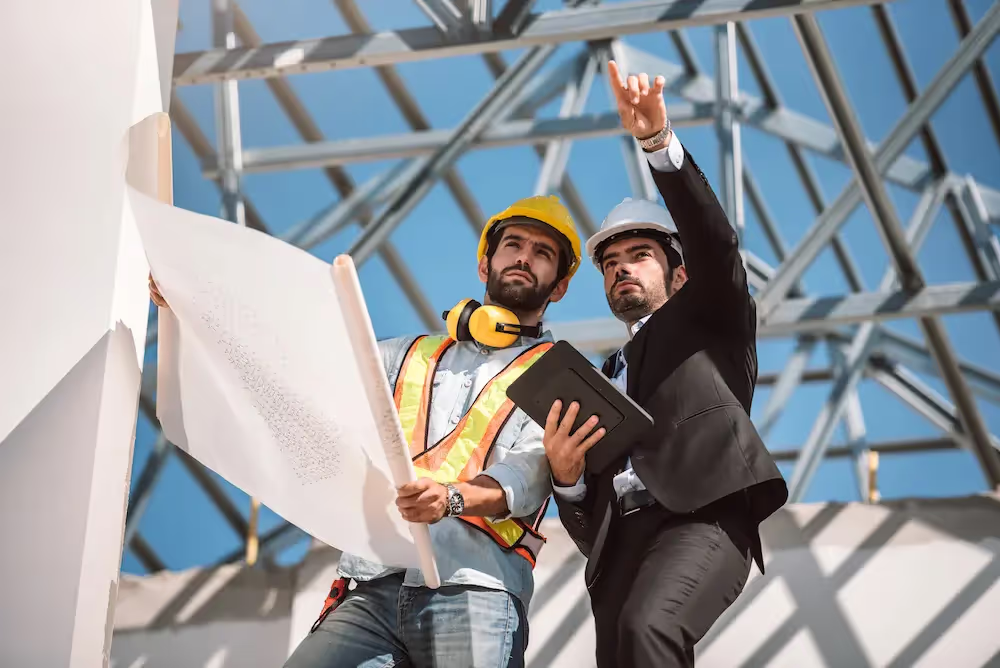
But what if the communication isn’t to correct an obvious safety issue? What if the communication needs to be among subcontractors and tradespeople about key scheduling and workflow – so that your team can avoid mistakes, clashes, costly reworks, or worse – an accident? As soon as the straight-line communication breaks into multiple streams, the message, so easy to comprehend in that one-on-one scenario, gets muddy. Much like a game of telephone, by the time your message reaches the people who need it most, it may look nothing like what you meant to convey.
So, how do you avoid “playing telephone” when millions of dollars and people’s lives are at stake? Especially with more and more project management and oversight happening remotely?
Why Remote Construction Management is on the Rise
Prior to the Covid-19 pandemic, remote risk and project management had little foothold in the construction industry. The necessity of additional layers of safety and a dwindling pool of skilled construction workers required many general contractors and facility managers to rethink how they supervised projects, and many of those innovations have proven to have staying power in the post-pandemic economy.
The construction industry is still struggling to fill some 500,000 jobs across the U.S., so exceptional project planning and communication are vital to a successful and safe project outcome. New infrastructure mapping and communication software platforms are striving to meet construction project management needs, some more successfully than others.
The Components of a Successful Remote Communications Structure in Construction
Most industry experts agree that three software types are necessary to a solid comms platform: project management software, conferencing software, and scheduling software. While those components address scheduling and workflow communications, there is another crucial data need that none of those listed above address – accurate existing conditions/as-built information.
Why? Because every planned workflow, every material delivery, excavation, and crew, from architectural and engineering through MEP and finish work, cannot do their jobs safely and well without accurate as-builts. You cannot put a bucket in the ground, core through a post-tensioned slab, or lay a pipe-run, unless your team has the data they need to dig, cut, or install safely, without fear of clashes, rework, or risk.
On a large-scale project, how you collect, curate, and communicate that as-built information – accurately – can be the difference between a successful project and a series of critical mistakes. GIS platforms like Esri or even Google Earth, provide the ability to upload as-builts, but you have to do it yourself, which puts you at a communication deficit in multiple ways.
1- Someone must be tasked with aggregating information and ensuring it’s available as needed to those who need it
2- You are limited by the accuracy of what is available, which is usually at best, out of date, and at worst, inaccurate
3- Consistently updating existing conditions information requires continual monitoring, measuring, and reporting for subsurface utility & facilities, structural planning & execution, and construction progress
4- The consistency and accuracy of your as-builts is only as good as the subcontractors providing them. Most GCs and facility managers utilize multiple subcontractors to gather this information, which adds another layer of complexity and makes quality control more difficult, which can severely hamper communication
5- In the case of platforms like Google Earth, your data is not cloud-based or portable – it must be housed on a single machine and cannot be easily shared among teams or on site
How to Achieve Consistent, Updated, and Shareable Existing Conditions Information
As noted above, GIS platforms can help to corral your as-built information, but limit you by requiring you do the work of updating and uploading your existing conditions yourself, which adds time and money to the project, and requires you to coordinate the work of a host of subcontractors if you want to receive comprehensive site visualization.
GPRS has stepped up to lead the charge in Intelligently Visualizing The Built World® and provides a host of accurate, consistent, and easy-to-use tools to take the headache out of having up-to-date as-builts at your fingertips, 24/7, from anywhere, to give you the data control you need.
JobSite Plus is a project-based product that allows you to receive the most accurate subsurface utility locates, full site utility mapping and aboveground structural data capture, including 3D laser scanning and complete BIM modeling, construction progress reporting via ProCap Progressive Capture, and floorplans via FLRPLN – all utilizing GPRS’ industry-leading 99.8% accurate utility locates and concrete scans, NASSCO-certified video pipe inspection (VPI) reporting, and more, structured to meet your specific project needs.
The JobSite Plus package also includes a SiteMap® Project subscription, which enables you to control the quality of your subsurface and as-built data – because GPRS provides it all in a single source of truth, easily accessible and securely shareable to those who need it most via our cloud-based GIS platform.
Every piece of your site or facility data is captured by GPRS, uploaded by GPRS, and available at your fingertips in a layered, geolocated map that houses every data point, including your sewer scope reports and concrete scans inside SiteMap® for the duration of your project. SiteMap® also provides data portability to other GIS platforms, should you desire to integrate your information with existing software you may use.
Nothing can replace the importance and immediacy of your safety team for on-site interactions. But when you can’t be there in person, providing accurate, up-to-date and aggregated site information – above and below-ground – to those who need it most, is one of the most important tools in your arsenal to control your jobsite. It can also help to limit costly site visits and provide progress reporting/data to stakeholders, insurers, and regulators to help keep your project on time, on budget, and most importantly safe.
What can we help you visualize?
Frequently Asked Questions
What is SiteMap®?
SiteMap® is GPRS’ proprietary, cloud-based site and facility mapping platform with a GIS component that allows us to directly deliver all data collected by our project managers and deliverables like maps, models, and CAD drawings to our customers. Every GPRS customer receives a complimentary SiteMap® Personal Subscription, and there are additional subscription levels to meet project, facility, and national portfolio needs. Learn more about SiteMap®, here.
How does GPRS maintain 99.8% accuracy?
All GPRS Project Managers are required to be SIM-certified, meaning they must be experts in Subsurface Investigation Methodology – the most rigorous subsurface locating and mapping protocol in the world for concrete imaging and utility locating. SIM requires 80 hours of classroom work and 320 hours of mentored field training to achieve 101 certification, and additional education for levels 201 & 301. Our Project Managers also receive additional training in 3D laser scanning, leak detection, video pipe inspection, and other complementary technologies so that they can act as consultants to you in the field to meet your needs.
What is the Green Box Guarantee?
Just like our 99.8% accuracy in utility mapping, GPRS maintains a verified 99.8% accuracy rate in concrete scanning and imaging. If a GPRS Project Manager marks a green box with “clear” inside it, we guarantee that it is free of obstructions and reinforcements so that you can cut or drill with confidence. If we get it wrong, we’ll pay the material cost for your repair. Learn more here.