Prefabricated components are becoming increasingly popular on design-build jobsites throughout the construction industry. Unlike modular homes or other factory-built components manufactured by prefabricated construction companies, design-build projects are incorporating prefabricated components into their projects to speed construction, avoid weather-related delays, and mitigate risk.
“Whatever we can do in the factory, we move to the factory because it’s a much more controlled environment,” Amit Haller, CEO of modular construction firm Veev, recently shared with Construction Dive in an article focused on the ways prefab components can potentially make jobsites safer.
However, the speed and convenience of incorporating prefabricated components requires extreme precision. Measurements and existing conditions documentation must be as accurate as possible to avoid clashes, reworks, and delays. Because the successful integration of traditional construction methods and prefabricated components hinges entirely on precise measurements.
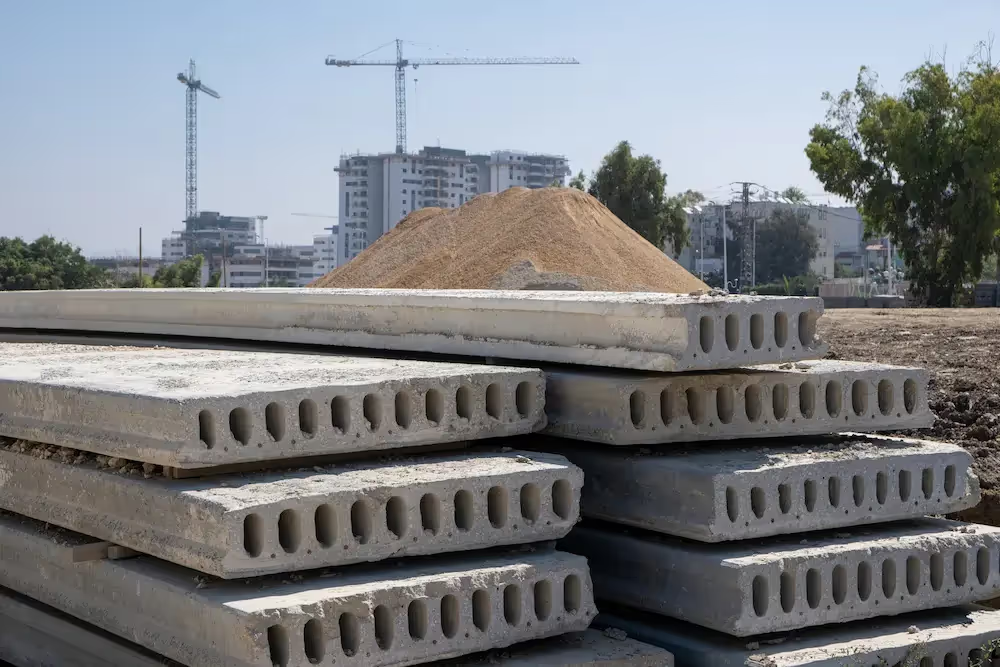
What Are the Most Commonly Used Prefabricated Components?
What kind of prefabricated components you use in construction depends on your needs. Everything from floor or roof trusses and concrete slabs to modular office buildings, to complex wind turbines can be premade to spec when your measurements are accurate:
Bridges – With the explosion in infrastructure projects in the U.S., prefab girders, beams, pier caps, and even full deck components can be built remotely, shipped in, and installed
Paving/Roads – In the same vein as the bridge components, entire pavement segments can be prefabricated and delivered to a road project for quick installation
Drainage & Sewer – Water and Wastewater managers can save time and money by utilizing prefabricated concrete pipes, boxes, and culverts, especially when they need to route flow to avoid other infrastructure
Buildings – There are a wide variety of preconstructed/prefabricated materials in use for design-build projects. Some of these include:
• Steel framing
• Load-bearing roof & floor trusses
• Walls (interior & exterior)
• Staircases & railings
There are many more examples of prefabricated components – like wind turbines and telecommunications towers – but those listed above are the most common and sought after.
Why Accurate Measurements Matter
In prefabricated construction, components are designed to fit together with minimal adjustment on-site. This demands precision in both the manufacturing of the components and the measurements taken on-site where they will be assembled.
Enhancing Efficiency and Reducing Waste
Accurate measurements prevent the expense and delays of clashes, rework, and change orders. Misaligned or poorly fitting components can undermine the efficiency that integrating prefabricated components aims to achieve. When prefabricated components are manufactured to precise specifications and those specifications match the on-site measurements, installation is streamlined.
Ensuring Structural Integrity
The structural integrity of prefabricated buildings relies on the precise alignment and fit of each component. Any discrepancy between the design and the actual measurements can compromise the building’s safety and performance. While true of all construction, this is particularly important in public infrastructure projects like roads and bridges that have to support hundreds of thousands of vehicles annually. Accurate measurements ensure that all parts align correctly, maintaining the intended load paths and structural behavior.
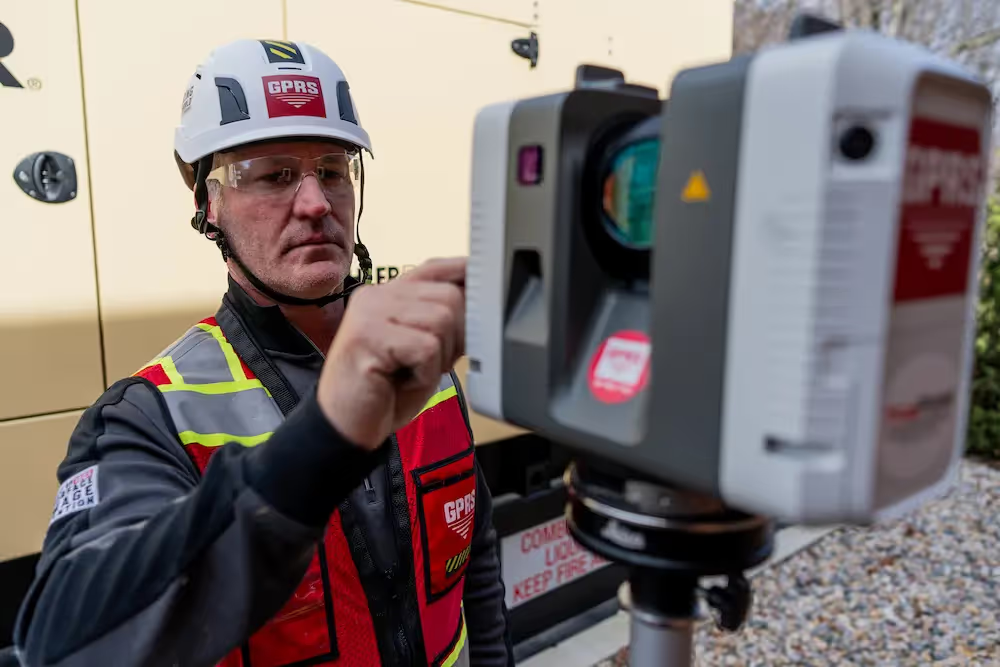
The Vital Role of As-Built Drawings
As-built drawings, also referred to as plan views, record drawings, or existing conditions documentation are intended to be comprehensive records that reflect the actual conditions of a project after completion, including all deviations from the original plans. The accuracy of these documents is indispensable for several reasons:
- Facilitating Future Renovations & Maintenance:
As-built drawings provide a precise map of a building’s current state, crucial for any future renovations or maintenance. They allow engineers and contractors to understand the exact placement and specifications of existing elements, reducing the risk of damaging essential components or systems during modifications.
- Legal & Compliance Issues:
As-built drawings may serve as a legal document that verifies the completed work aligns with regulatory requirements and contractual obligations. This can be essential in resolving disputes, securing final approvals, and ensuring compliance with building codes and standards.
- Emergency Preparedness and Risk Mitigation:
Accurate as-builts can serve as the basis for accurate floor plans that provide crucial escape routes, gathering points, and shelter-in-place locations for staff and facility visitors, and can provide a roadmap to first responders in an emergency situation. Providing accurate emergency planning documents can assist insurers for your facility and prove your commitment to safety.
- Preventing Clashes and Errors:
One of the primary uses of as-built drawings is to avoid clashes between different building systems. For example, they show the precise routing of electrical conduits, plumbing, and HVAC systems. This detailed documentation is critical in prefabricated construction, where components designed off-site must integrate perfectly with on-site systems. Misalignments can lead to significant project delays and increased costs due to the need for rework or redesign.
Impacts of Clashes and Inaccuracies
In prefabricated construction, any clash between components can have a ripple effect, causing delays and escalating costs. Inaccuracies in measurements and as-built documentation can impact a project in several ways:
Delays and Increased Costs
Clashes require immediate resolution, often involving redesign and re-manufacture of components, leading to project delays and increased costs. According to industry insights, such delays can add up to 10-20% to the project costs and extend timelines by several weeks or even months.
Safety Risks
Inaccurate as-builts can pose serious safety risks. If components do not fit as intended, it can lead to structural weaknesses or the failure of safety systems. Accurate documentation ensures that all parts of the building comply with safety standards and function as designed.
Compromised Quality
Quality in prefabricated construction is highly dependent on precision. Any deviation from the specified measurements or plans can compromise the quality of the finished building. Ensuring high-quality outcomes requires accurate and up-to-date as-built drawings that reflect every change made during construction.
Before making the decision to include prefabricated components in your design-build project, it’s suggested that you run a cost-benefit analysis to determine whether prefabrication is a trend your project needs to jump on. If you decide to utilize modular or prefab components on your job, it is mission-critical that you hire a professional infrastructure visualization company to produce accurate as-builts, so you can be sure what’s built remotely will slide into place on site without issue.
GPRS specializes in Intelligently Visualizing The Built World® for customers nationwide. What can we help you visualize?
Frequently Asked Questions
What is precast construction and how does it differ from traditional construction methods?
Precast construction is another name for prefabrication and involves casting building components, such as walls and beams, in a controlled factory environment before transporting them to the construction site for assembly, which contrasts with traditional construction where components are typically built on-site. This method enhances quality control and reduces on-site labor and construction time. Learn how you can remove bottlenecks and speed project timelines, here.
How does the timeline for a project differ when using precast/prefabricated components compared to traditional methods?
According to some construction experts, using precast or prefabricated components can significantly shorten the project timeline, as manufacturing of components can occur simultaneously with site preparation, leading to faster assembly on-site and reducing overall construction time by up to 50% compared to traditional methods. Learn more about how GPRS can provide 2-4mm accurate measurements, here.