Large-scale construction projects, whether they involve infrastructure, commercial buildings, or residential developments, are complex undertakings that require meticulous planning and execution.
Despite best efforts, delays are a common occurrence in these projects, leading to increased costs, extended timelines, and often significant frustration for all parties involved. Research by machine learning startup nPlan found that delays to large-scale construction projects more than doubled during the Covid-19 pandemic, according to an article on NewCivilEngineer.com.
Understanding the primary reasons behind these delays can help stakeholders anticipate potential problems and implement strategies to mitigate them. Let’s look at eight of the top reasons why large-scale construction projects experience delays:
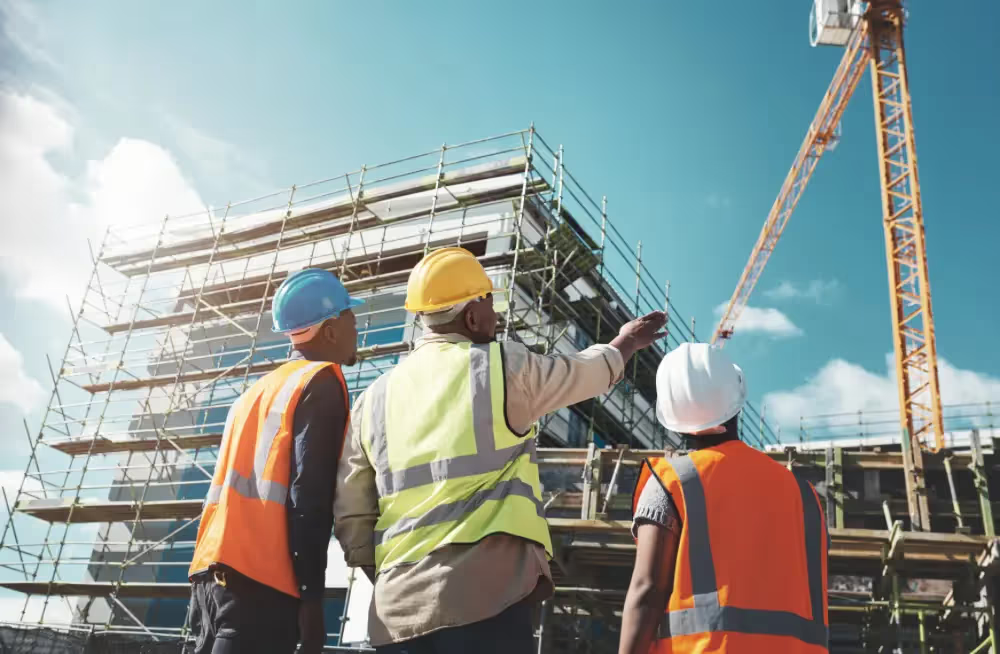
1. Inadequate Planning and Scheduling
Effective planning and scheduling are the cornerstones of any successful construction project. However, large-scale projects often suffer from inadequate planning, leading to significant delays.
- Unrealistic Timelines: Setting overly ambitious timelines without considering the project's complexity can lead to inevitable delays. Realistic scheduling must account for every phase, from design and procurement to construction and finishing.
- Poor Sequencing: Mismanagement of the sequence in which tasks are performed can cause bottlenecks. Proper sequencing ensures that each task is completed in the right order, preventing idle time and resource wastage.
- Insufficient Contingency Planning: Failing to account for potential risks and uncertainties can leave projects vulnerable to unforeseen issues. Effective contingency planning involves anticipating possible setbacks and developing strategies to address them promptly.
2. Design Changes and Scope Creep
Design changes and scope creep are significant contributors to construction delays. These issues can arise from various sources, including clients, architects, and regulatory bodies.
- Client-Induced Changes: Clients may request modifications to the original design or additional features, which can disrupt the workflow and necessitate rework. Clear communication and strict change management procedures are essential to minimize such disruptions.
- Inadequate Initial Design: Incomplete or flawed initial designs often lead to revisions during the construction phase. Ensuring thorough and accurate design work at the outset can reduce the need for costly and time-consuming changes later.
- Scope Creep: Gradual expansion of the project scope without corresponding adjustments to the schedule and budget can lead to delays. Establishing clear project boundaries and adhering to them is crucial to maintaining timelines.
3. Permitting and Regulatory Approvals
Navigating the regulatory landscape is a critical aspect of large-scale construction projects. Delays in obtaining necessary permits and approvals can significantly impact project timelines.
- Complex Regulatory Requirements: Large projects often involve multiple regulatory agencies and a complex web of requirements. Delays can occur if any necessary permits or approvals are overlooked or not obtained in a timely manner.
- Changes in Regulations: Changes in local, state, or federal regulations during the project can require adjustments to comply with new standards, causing delays.
- Inspection Delays: Regulatory inspections are necessary at various stages of construction. Scheduling and passing these inspections can be time-consuming, especially if issues are identified that require remediation.
4. Supply Chain Issues
The construction industry relies heavily on a robust supply chain for materials and equipment. Disruptions in this supply chain can cause significant delays.
- Material Shortages: Shortages of critical materials, such as steel, concrete, or lumber, can halt construction progress. These shortages can be due to increased demand, production issues, or logistical challenges.
- Delayed Deliveries: Timely delivery of materials and equipment is essential. Delays in transportation or customs clearance can disrupt the project schedule.
- Quality Issues: Receiving substandard materials can lead to rework and delays. Ensuring quality control throughout the supply chain is crucial to maintaining project timelines.
5. Labor Shortages and Productivity Issues
The availability and productivity of skilled labor are vital to the timely completion of large-scale construction projects.
- Skilled Labor Shortage: A shortage of skilled workers can slow down construction progress. This issue is particularly prevalent in regions with high demand for construction services.
- Labor Strikes: Strikes and labor disputes can halt construction activities entirely, leading to significant delays.
- Productivity Variations: Variations in labor productivity, due to factors such as adverse weather conditions, worker fatigue, or inadequate supervision, can impact the project schedule.
6. Financial Constraints
Financial issues can severely disrupt large-scale construction projects. Maintaining a stable flow of funds is essential for continuous progress.
- Funding Delays: Delays in securing financing or disbursements can halt construction activities. Ensuring that all financial arrangements are in place before starting the project is critical.
- Cost Overruns: Unanticipated cost increases can strain the project budget, leading to funding shortages and delays. Regular budget monitoring and effective cost control measures can help mitigate this risk.
- Payment Disputes: Disputes between contractors, subcontractors, and clients over payment terms and schedules can disrupt the project timeline.
7. Weather and Environmental Conditions
Weather and environmental factors are often beyond the control of project managers but can have a significant impact on construction schedules.
- Adverse Weather: Extreme weather conditions, such as heavy rain, snow, or high winds, can halt construction activities, particularly those conducted outdoors.
- Environmental Restrictions: Projects located in environmentally sensitive areas may face restrictions that limit construction activities during certain periods to protect wildlife or natural habitats.
8. Unforeseen Site Conditions
Unexpected conditions at the construction site can pose significant challenges and delays.
- Geotechnical Issues: Unanticipated subsurface conditions, such as unstable soil or rock formations, can necessitate redesigns and additional engineering work.
- Existing Infrastructure: Discovering existing underground utilities or structures that were not accounted for in the initial plans can lead to delays while adjustments are made.
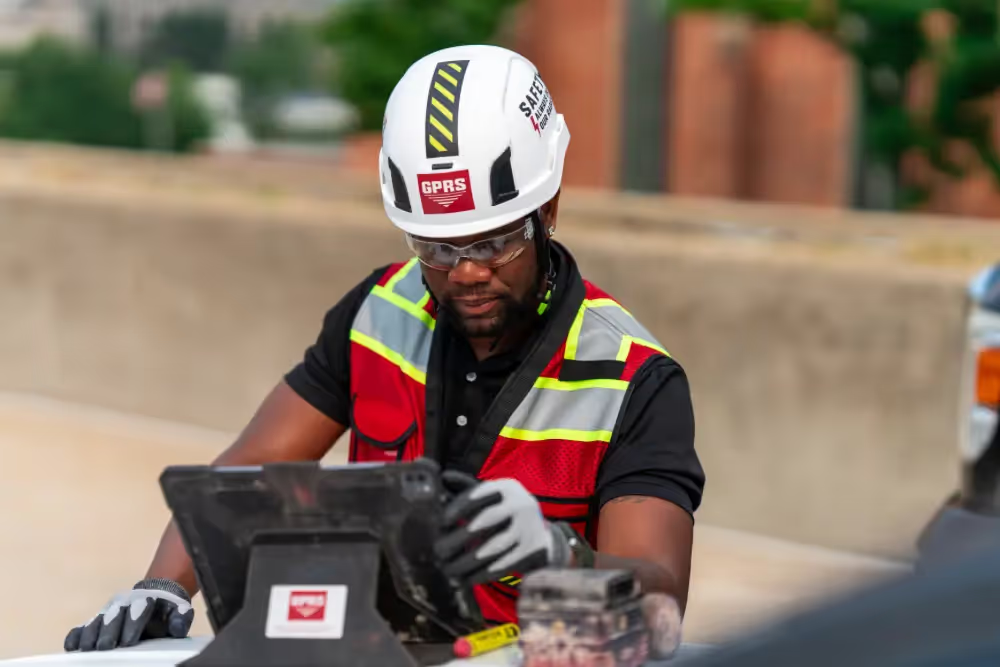
GPRS Helps Keep Your Project On Schedule
Large-scale construction projects are inherently complex, and delays can arise from a myriad of sources. By prioritizing thorough planning, maintaining open communication, ensuring regulatory compliance, and managing resources effectively, stakeholders can mitigate many of the risks that lead to delays.
GPRS helps keep your projects not only on time, but on budget and safe, through our comprehensive suite of subsurface damage prevention, existing conditions documentation, and construction & facilities project management services.
Our concrete scanning, utility locating, video pipe inspection and leak detection offerings prevent the costly and potentially dangerous utility strikes that could derail your budget and schedule. 3D laser scanning and photogrammetry captures your site with 2-4mm accuracy to assist in efficient planning. And SiteMap® (patent pending), our GIS-based infrastructure mapping solution, eliminates the mistakes caused by miscommunications.
From skyscrapers to sewer lines, GPRS Intelligently Visualizes The Built World®. What can we help you visualize?
Frequently Asked Questions
What industries does GPRS serve?
GPRS has become a trusted partner to hundreds of clients for 3D laser scanning and modeling services. Our team works with integrity, passion and professionalism, upholding the highest standards in 3D laser scanning and modeling services. The foundation of our company’s success revolves around servicing the client. We work closely with every client to deliver the highest quality point clouds, 2D CAD drawings and 3D BIM models. We offer dynamic 3D laser scanning solutions to the following industries:
- Agricultural Facilities
- Architectural Documentation
- Concrete Construction
- Construction
- Clash Detection
- Design Build
- Energy & Utilities
- Engineering
- Government, Defense & Military Sector
- Healthcare & Pharmaceutical
- Historical Documentation & Preservation
- HVAC & MEP Coordination
- Industrial, Manufacturing, Assembly & Distribution Facilities
- Mixed Reality & 3D Projection Mapping
- Office & Commercial Buildings
- Overhead Clearances
- Oil & Gas Facilities
- Power Plants & Process Plants
- Real Estate
- Stadiums, Arenas & Theatres
- Telecommunications
- Schools & Universities
- Subsurface Utility Engineering
- Virtual Design and Construction
- Water & Wastewater Treatment Plant
- Accident Reconstruction
- 3D Video Gaming & Software Development
What if my project is limited within the physical setting?
Some projects require special applications due to limitations within the physical setting. Often this is due to line-of-sight issues and when a scan must be done safely from the ground or with precautionary distance. Some of these applications would include above-ceiling MEP features in hospitals where it is necessary to maintain negative airflow or interstitial spaces that are congested with limited access. Since laser scanning is a non-contact measurement tool (i.e. we can scan from a safe distance or location) this becomes a powerful tool for solving these complex challenges.