What is Horizontal Directional Drilling?
Horizontal directional drilling (HDD) is a trenchless method used for installing underground utilities, such as pipes, cables, or conduits, without the need for traditional open excavation. It involves the use of a directional drilling machine, to accurately drill along a horizontal bore path underground, then expand the hole to the desired diameter to allow the installation of the utility. The construction technique is commonly used to install water, sewer, gas, and telecommunication lines across obstacles like roads, rivers, or existing infrastructure. Horizontal directional drilling machines and drill rigs minimize soil disturbance and the environmental impact of utility installation projects.
Horizontal Directional Drilling in Telecom
Horizontal directional drilling is used in the Telecom industry as a cost-effective, efficient, and minimally invasive method for ensuring reliable connectivity without disrupting underground utilities. Telecom projects that utilize horizontal directional drilling include fiber optic cable installation, 5G network expansion, rural broadband deployment, smart city infrastructure, IoT network connectivity, and data center connections.
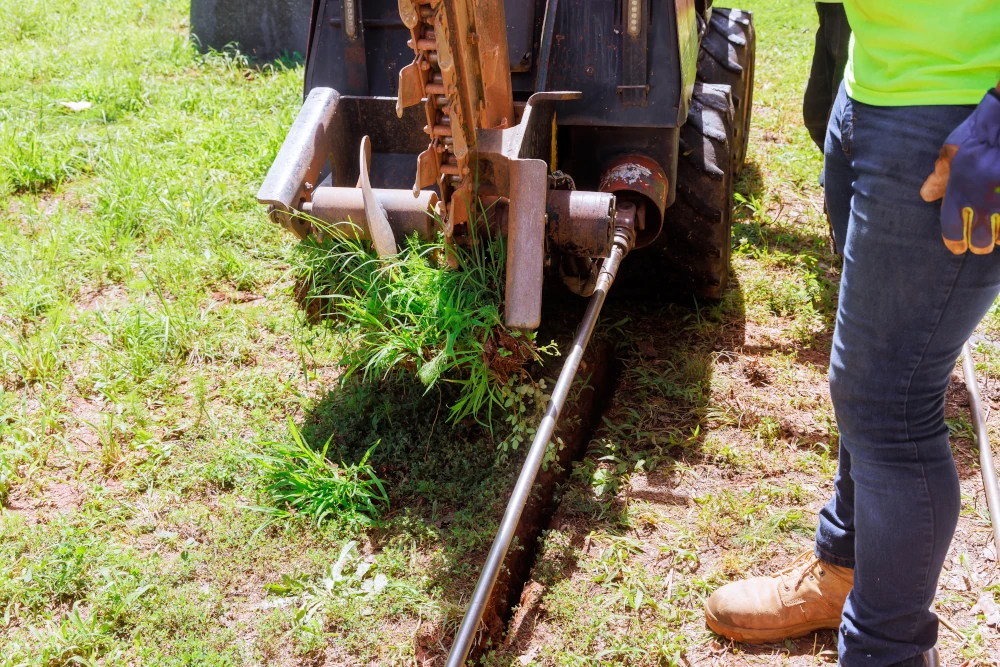
What are the Benefits of Horizontal Directional Drilling
Horizontal directional drilling is preferred over fiber trench for its efficiency and cost effectiveness, offering a smoother installation process for pipes, cables, conduits, and other materials compared to traditional drilling methods. Horizontal directional drilling is highly accurate and requires less post-drill cleanup, enabling teams to restore the ground to its pre-drill condition quickly and with minimal effort.
What are Best Practices for Pre and Post Directional Drilling Installations?
Following these best practices for pre and post directional drilling installations will minimize risk, maintain regulatory compliance, protect workers from hazards, and safeguard surrounding utilities, leading to safe and effective drilling with minimal environmental impact.
Pre Drilling Best Practices
Site Assessment and Planning
- Contact GPRS to locate and map the buried utilities in your project area, utilizing ground penetrating radar (GPR) and electromagnetic locating, ensuring they are marked and depth verified before drilling to avoid hitting underground infrastructure.
- Confirm that all overhead power lines in the drilling area have been marked.
- Verify soil conditions through geotechnical investigations by testing the soil’s type, density, and stability to determine the right drilling methods, equipment, and fluids, ensuring a stable bore path and safe, efficient operation.
- Expose and verify all underground utilities within construction limits using hand digging or vacuum excavation, ensuring adequate clearance and preventing damage.
- Confirm sewer laterals are properly located through electromagnetic locates or physical inspection to ensure sufficient clearance from the bore path. GPRS CCTV inspections can inspect the integrity of your buried sewer lines to ensure there are no pre-existing problems, such as cross bores, and inspect them again after your project has completed to ensure no new problems were created because of the work.
- Walk intended route of the directional bore, reviewing the site, and confirming that all utilities have been properly identified and located.
- Plan bore paths to minimize environmental disruption and avoid existing utilities.
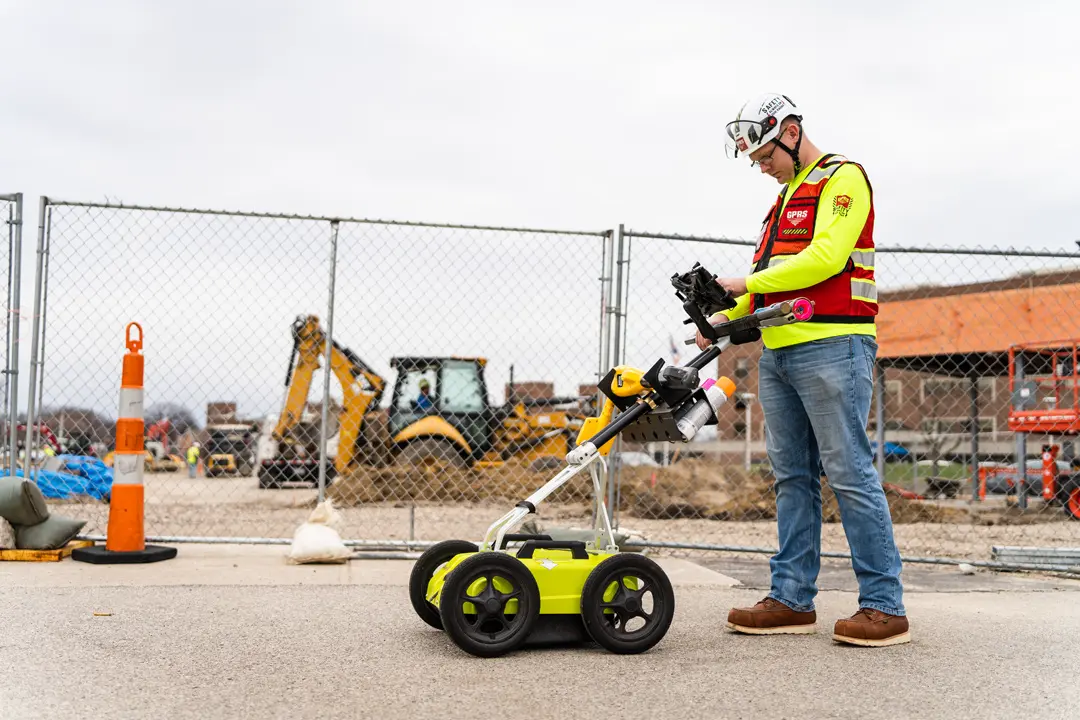
Pre-Operational Equipment Inspection
- Verify drilling fluid, hydraulic fluid, engine oil, coolant, and fuel levels. Ensure proper lubrication of moving parts to prevent overheating and mechanical failure.
- Conduct a visual inspection of the drilling rig to identify leaks, worn components, and potential hazards, checking hoses, belts, fittings, and electrical connections for damage to prevent costly breakdowns.
- Replace or repair critical components, such as drill pipe connections, hydraulic seals, or tracking sensors to prevent unexpected failures that could delay the project or compromise borehole integrity.
- Confirm that safety guards, emergency shut offs, and alarms are functional to prevent workplace injury.
Permits and Regulatory Compliance
- Obtaining local, state, and federal permits for drilling activities, including environmental and excavation permits.
- Perform all operations in compliance with OSHA, EPA, DOT, and local regulatory agency guidelines. These guidelines address safe excavation practices, ensuring proper excavation depths, protective systems (like trench shoring or shielding), and measures to prevent accidents, protect the environment, and ensure public safety during the drilling process.
- Ensure compliance with environmental guidelines to minimize soil disturbance, protect water sources, and prevent contamination. This includes following EPA regulations related to waste disposal and fluid containment.
- Wear appropriate personal protective equipment (PPE) as required by the task being performed and as required per OSHA regulations.
- Ensure that all utilities are accurately marked and verified to prevent damage to existing infrastructure during drilling, in compliance with local utility regulations.
- Follow specific regulations for the protection of high-consequence utilities (such as gas, water, or electrical lines), including maintaining safe clearance distances and providing verification through hand digging or excavation. Maintain a minimum five-foot clearance from natural gas distribution lines and high consequence utilities, and a ten-foot clearance from transmission gas or hazardous liquid pipelines.
- Provide required as-built drawings, inspection reports, and other documentation to regulatory agencies to confirm compliance and track the installation process.
Equipment Selection and Calibration
- Use the appropriate drilling rig, drill bits, and drilling fluids for the soil conditions.
- Calibrate locating and tracking systems for accurate bore path control.
Directional Drilling Installation
- Maintain clear communications with local authorities, utility companies, and property owners.
- Set up equipment maintaining the minimum requirement of clearance between the equipment and facilities.
- Appoint a spotter if there are overhead power lines, underground utilities, or tight working conditions.
- Cap or cover exposed pipe ends with waterproof, secure materials to prevent debris, moisture, and contamination.
- Inspect excavation walls for stability, especially in loose or wet soil conditions.
- Establish a contingency plan for unforeseen obstructions or environmental challenges.
Post Drilling Best Practices
Site Protection and Access Control
- Secure all open excavations with fencing, barricades, or signage to prevent unauthorized entry and reduce the risk of falls or accidents.
Bore Path Verification
- Use tracking technology to confirm that the installed bore path aligns with design specifications.
- Pressure test pipelines or fiber optic cables to confirm they can handle expected pressure and prevent leaks or failures, confirming the infrastructure is secure before use.
Stability and Site Restoration
- Properly backfill and seal the entry and exit points to prevent ground settling and water intrusion.
- Backfill the gap between the drilled hole and the installed pipe with suitable material, such as grout or drilling mud, to maintain stability, prevent shifting, and avoid future ground settlement.
- Monitor for any ground settlement or surface heaving. Conduct periodic inspections to detect potential shifts, leaks, or structural failures.
- Restore disturbed areas to pre-installation conditions, including landscaping and roadway repairs.
As-Built Documentation
- Update records with accurate as-builts that include the final position and depth of the bore path, along with GPS coordinates and any deviations from the original plan. This report may also include any changes or issues encountered during the drilling process.
- Submit reports to regulatory authorities for compliance, including permit applications, utility locate reports, environmental impact assessments, drilling fluid management plan, progress reports, site restoration reports, field inspection and testing reports, and safety compliance reports.
By following these best practices, directional drilling projects can be executed efficiently, minimizing risks and ensuring long-term performance.
GPRS Services Ensure Successful Horizontal Directional Drilling Projects
Utility locating and sewer inspection services play a critical role in pre and post installation investigations for horizontal directional drilling projects.
GPRS Utility Locating Services
GPRS Project Managers utilize ground penetrating radar (GPR) and electromagnetic (EM) locators to identify, mark, and map existing utilities, including gas, water, electricity, telecommunications lines, and sewer laterals before a directional drilling project begins.
By identifying and verifying the location and depth of buried infrastructure, GPRS minimizes the risk of accidental damage, costly repairs, safety hazards, and project delays.
GPRS has achieved and maintained a better than 99.8% accuracy rating on utility locates due to our commitment to the Subsurface Investigation Methodology, or SIM.
Through the SIM program, GPRS Project Managers complete 320 hours of field training and 80 hours of classroom training, where they encounter real-world scanning scenarios in a safe and structured environment that allows them to create consultative solutions to unique problems.
This training ensures that GPRS Project Managers can accurately interpret the readings provided by GPR, EM locators, and other infrastructure visualization technologies.
Read the Article: Updated utility maps accurately captured existing underground utilities to allow for the safe installation of new power distribution lines in a community.
Utility Locating Services Prior to Telecom Installations
Prior to telecom installations, utility locating services can be used to complete a telecom site survey, site assessment, subsurface mapping, bore path planning, permitting, and soil analysis to receive accurate subsurface infrastructure information, plan for a successful telecom installation, and mitigate risks.
Before telecom installation in Multi-Dwelling Units (MDU), utility locating is essential to identify existing underground utilities, preventing damage to water, gas, and electrical lines during fiber trenching or conduit placement.
Also, before constructing a telecom tower compound, utility locating is critical to ensure safe, efficient, and compliant installation of foundations, fiber backhaul, and power infrastructure.
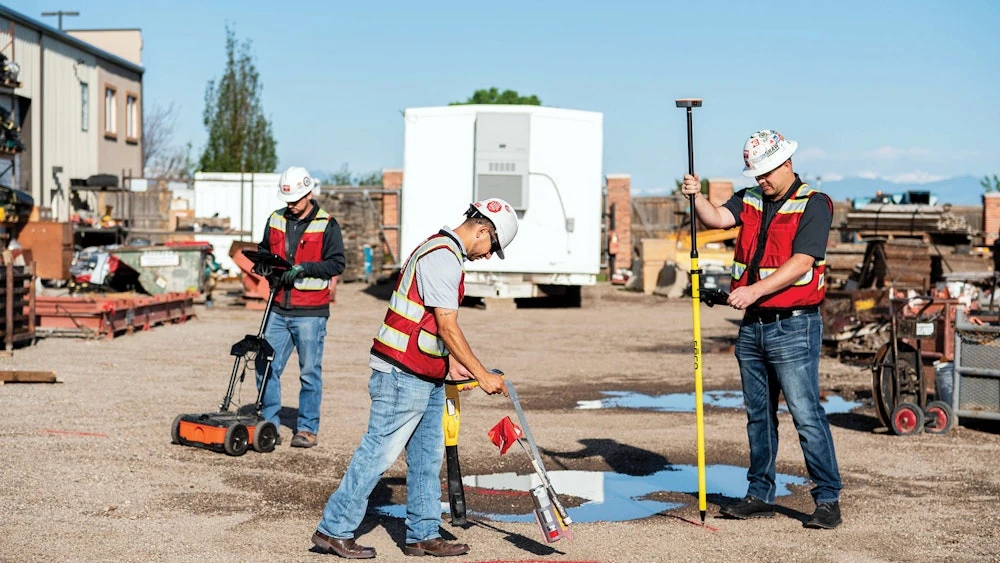
GPRS Sewer Inspection Services
For sewer lines, GPRS also offers CCTV inspection services, assessing sewer laterals before and after drilling. These inspections identify potential issues like blockages or damage and ensure that no harm is done to the existing infrastructure during the drilling process.
While there are CCTV pipe inspection companies throughout the U.S., there is only one company with Project Managers that are certified in both Subsurface Investigative Methodology (SIM) and National Association of Sewer Services Companies (NASSCO) specifications, and located in every major market throughout the United States.
GPRS’ nationwide team of Video Pipe Inspection Project Managers are equipped with the industry’s best training, technology, and methodology to give our customers the most accurate and comprehensive cross bore inspection services in the country.
Municipalities Mandate Pre and Post Verification of Proper Installation
Many municipalities now mandate pre and post project verification of proper installation with video pipe inspection (VPI) to prevent and detect cross bores, which occur when new utility lines unintentionally intersect existing underground infrastructure.
Pre-Project Verification of Proper Installation with Video Pipe Inspection
- Ensures that no existing cross bores are present before starting directional drilling.
- Identifies potential conflicts with gas lines, water mains, sewer lines, and other utilities.
- Helps in adjusting bore paths to avoid hazardous intersections.
Post-Project Verification of Proper Installation with Video Pipe Inspection
- Confirms that the new telecom or utility installation did not result in any cross bores.
- Utilizes CCTV sewer inspections, ground-penetrating radar (GPR), and other technologies to verify proper placement.
- Provides documentation to municipalities and utility providers for regulatory compliance.
Key Benefits of Municipal VPI Requirements
- Public Safety: Prevents dangerous gas or utility line strikes that could lead to explosions, service disruptions, or contamination.
- Regulatory Compliance: Ensures contractors meet local safety codes and avoid potential legal issues.
- Reduced Liability: Protects telecom providers and contractors from costly damage claims due to unintentional cross bores.
- Infrastructure Protection: Safeguards existing underground utilities, reducing the risk of costly repairs and downtime.
As more municipalities recognize the risks associated with cross bores, VPI is becoming a standard requirement in horizontal directional drilling (HDD) projects, especially in urban and high-density utility areas.
Read the Case Study: Cross Bore Inspection After Fiber Installation
Read the Article: The City of Fremont, California requires that all contractors performing directional drilling work within its boundaries obtain a video (CCTV) pipe inspection of any sewer lines near the job site both before and after their work is completed.
Read the Article: A sinkhole left one Texas community with a massive repair bill after it caused significant damage to the municipality’s main sewer line.
Every one of our sewer inspection services is backed by our 99.8+% utility locating accuracy on over 500,000 projects completed. So you can be confident that your sewer lines will be accurately mapped and marked to give you the best above and below ground imagery of your existing lines.
Contact us today for GPRS utility locating and sewer inspection services.
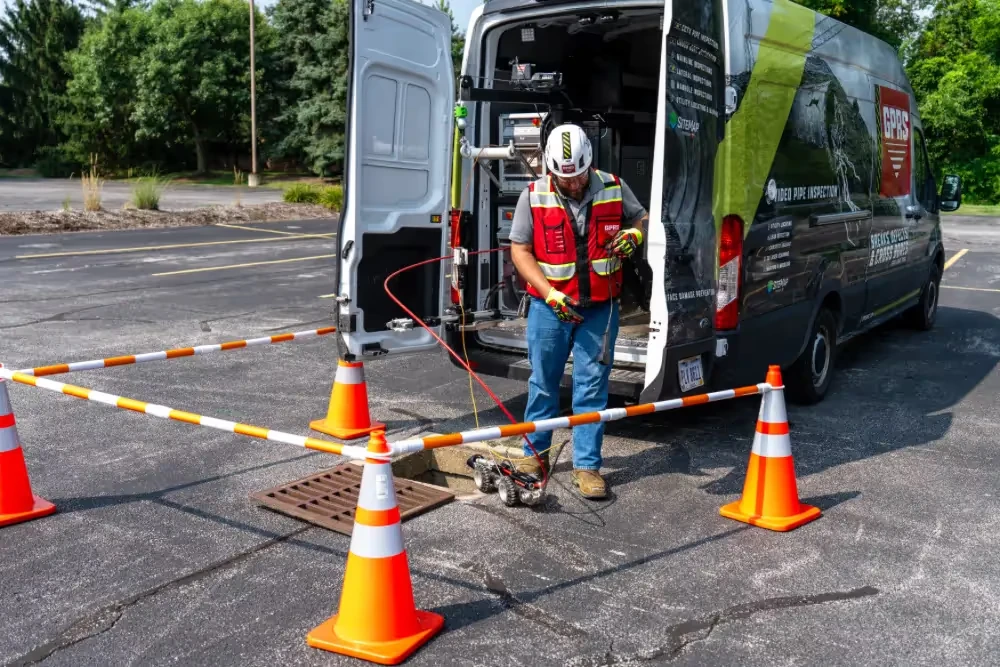
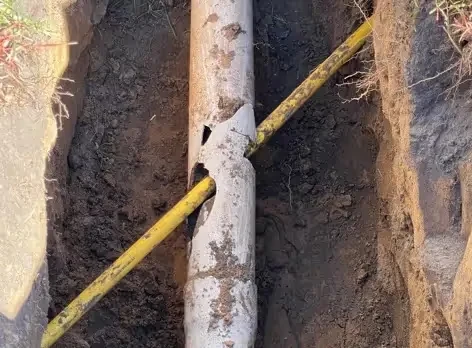
Frequently Asked Questions
What is utility locating?
Utility locating is the detection of underground utilities and other subsurface findings using ground penetrating radar (GPR) and other tools. Utilities and other findings can be located and marked out in a safe, non-destructive manner. Electric, steam, telecommunications, water pipes, gas & oil pipes, sewer pipes & storm sewer lines, and many other primary and secondary utility services can be located.
What equipment is used for utility locating?
Ground penetrating radar and electromagnetic locators are the primary tools used by utility locators such as GPRS to locate and map underground utilities. Professional utility locating technicians use a variety of tools, including electromagnetic (EM) locators, to locate and map underground utilities.
How much does utility locating cost?
The cost of a private utility locate varies depending on the size and specifics of the site being scanned, as well as other factors. Utility locates are not cheap, but as mentioned above they are a vital service and significantly less expensive than the cost – both financial and otherwise – of striking a utility line.
What is a cross bore?
A cross bore as stated by the Cross Bore Safety Association is “an intersection of an existing underground structure by a second utility resulting in direct contact between the transactions of the utilities that compromise the integrity of either utility or underground structure”. The presence of an undetected cross bore in a sewer line can result in backups in the line, compromise the structural integrity of the sewer pipes, cause contamination, and damage the overall sewer system.