The Anderson Dam tunnel project recently reached a major milestone that highlights the capabilities of micro-tunnel boring.
In late 2024, Vally Water finished the final segment of a 1,736-foot tunnel adjacent to the Santa Clara County, California dam, which is the largest of the 10 Santa Clara Valley Water District reservoirs. According to an Underground Infrastructure article highlighting the completion of the tunnel, the agency is edging ever closer to its goal of enhancing water release capabilities in emergencies.
A specialized micro-tunnel boring machine (MTBM) was used to complete the final 347 feet of the tunnel. According to Underground Infrastructure, crews maneuvered this device 30 feet beneath the reservoir’s surface. Once it had completed its work, divers and construction teams carefully removed the machine from the tunnel’s endpoint using a large crane.
Micro-tunnel boring, also known as microboring, microtunneling, or micro-drilling, is an advanced construction technique used to create small-diameter tunnels or boreholes with high precision. It is widely applied in utility installations, geotechnical investigations, and trenchless construction projects.
As urban areas become increasingly congested and the demand for minimally invasive infrastructure solutions grows, microboring has emerged as a crucial method for reducing surface disruptions while ensuring the efficient installation of underground systems.
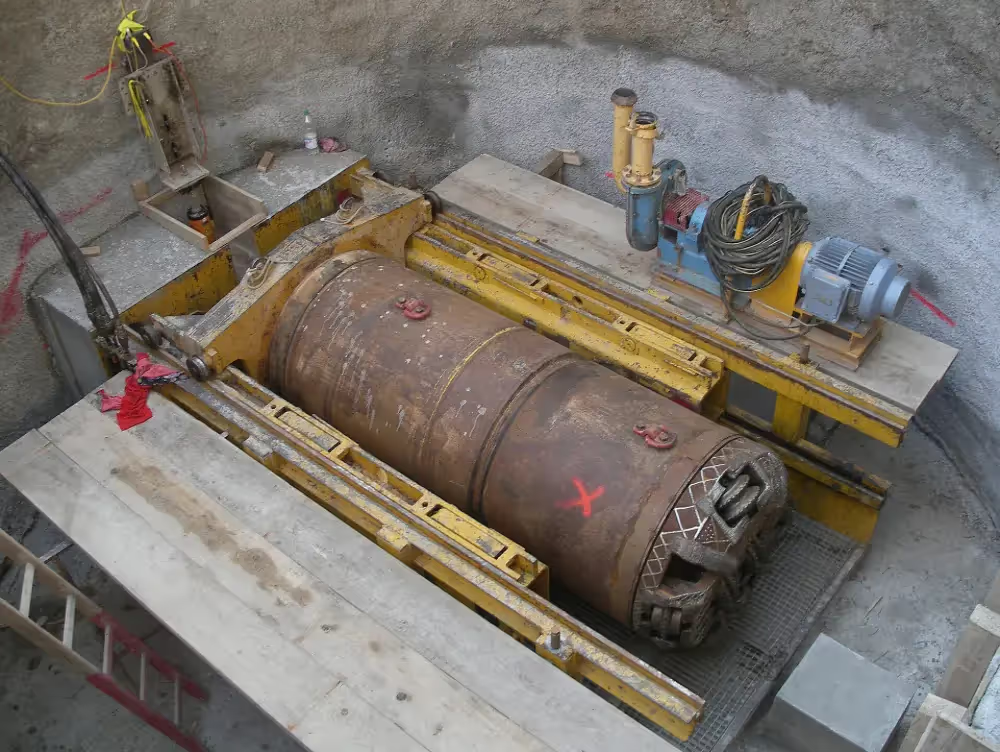
What is Micro-tunnel boring?
Micro-tunnel boring is a specialized form of boring that creates tunnels or boreholes with diameters typically ranging from a few inches to several feet. Unlike traditional boring methods, micro-tunnel boring employs remote-controlled drilling machines that operate with extreme precision. The process minimizes the need for large excavation sites, making it ideal for urban environments and sensitive ecosystems.
The technique is used in a variety of industries, including civil engineering, oil and gas, telecommunications, and water management. Depending on the project’s requirements, different types of microboring machines may be employed, such as MTBMs, directional drills, or auger boring systems.
Advantages of Micro-tunnel boring
Micro-tunnel boring offers numerous benefits over traditional excavation and tunneling methods, particularly in situations where minimizing surface disruption is essential.
Minimal Surface Disruption
One of the most significant advantages of micro-tunnel boring is its ability to install underground infrastructure with minimal impact on the surface. This makes it especially valuable in urban environments, where conventional excavation methods would cause significant disruptions to roads, sidewalks, and buildings.
Precision and Accuracy
Micro-tunnel boring systems are equipped with advanced guidance and control systems that allow for precise placement of underground utilities. This reduces the risk of accidental damage to existing infrastructure, such as gas lines, water pipes, and electrical conduits.
Reduced Environmental Impact
Traditional open-cut trenching methods can cause extensive environmental disruption, including soil displacement, deforestation, and damage to water bodies. Micro-tunnel boring minimizes these impacts by requiring fewer entry and exit points, preserving the surrounding environment.
Cost Efficiency in Certain Applications
While the initial setup cost for micro-tunnel boring can be high, it often proves to be cost-effective in the long run by reducing labor costs, minimizing delays caused by traffic rerouting, and decreasing restoration expenses for roads and landscapes.
Increased Safety
By eliminating the need for deep excavation, micro-tunnel boring enhances worker safety. Trench collapses, falling debris, and exposure to hazardous underground conditions are significantly reduced, making microboring a safer alternative to traditional excavation methods.
Drawbacks of Micro-tunnel boring
Despite its numerous advantages, microboring is not without its challenges. Here are some of the primary drawbacks associated with this technique:
High Initial Cost
Micro-tunnel boring requires specialized equipment and skilled operators, which can lead to higher initial costs compared to traditional trenching methods. Small-scale projects may find it difficult to justify the expense of microboring.
Complex Planning and Setup
Successful micro-tunnel boring operations require detailed planning, including soil analysis, underground utility mapping, and equipment calibration. Any miscalculations or unforeseen subsurface conditions can cause delays and cost overruns.
Limited Diameter Capabilities
While micro-tunnel boring is excellent for small to medium-sized tunnels, it is not suitable for large-scale tunneling projects. For projects requiring tunnels larger than a few meters in diameter, traditional tunnel boring machines (TBMs) or conventional excavation techniques are more appropriate.
Challenging in Unstable Soil Conditions
Micro-tunnel boring can be difficult in unstable or highly variable soil conditions. Loose sands, high groundwater levels, and mixed soil strata can complicate the process and require additional stabilization measures, increasing costs and project timelines.
Applications of Micro-Tunnel Boring in Construction
Micro-tunnel boring is widely used across various sectors of the construction industry. Its ability to create precise underground passages with minimal surface disruption makes it ideal for a range of applications.
Utility Installations
Micro-tunnel boring is frequently used to install underground utilities such as water and sewer lines, electrical conduits, fiber optic cables, and gas pipelines. The method allows utilities to be placed beneath roads, railways, and waterways without requiring disruptive open-cut trenches.
Trenchless Sewer and Water Line Rehabilitation
Aging sewer and water lines often require rehabilitation or replacement. Micro-tunnel boring allows for the installation of new pipelines within or adjacent to existing infrastructure without causing significant surface disruption. This is particularly beneficial in densely populated urban areas where traditional excavation would be impractical.
Geotechnical Investigations
Before undertaking major construction projects, engineers must assess subsurface conditions. Micro-tunnel boring is commonly used to collect soil and rock samples for geotechnical analysis, helping construction teams design foundations, retaining walls, and other structural components based on accurate subsurface data.
Drainage and Stormwater Management
Efficient stormwater drainage systems are essential for preventing flooding and erosion. Micro-tunnel boring facilitates the installation of underground drainage pipes, culverts, and stormwater management systems in areas where open excavation would be too disruptive or costly.
Microtunneling for Transportation Infrastructure
Micro-tunnel boring is used in transportation infrastructure projects, such as the installation of underground conduits beneath highways, airports, and railways. This allows for the expansion and maintenance of critical infrastructure without causing major traffic disruptions.
Industrial Applications
In industrial settings, micro-tunnel boring is used to install pipelines for transporting chemicals, oil, and gas. The technique is especially valuable in environments where surface disruptions could interfere with ongoing operations or pose safety hazards.
The Future of Micro-Tunnel Boring
As construction technology continues to advance, micro-tunnel boring is expected to become even more precise, cost-effective, and adaptable to a wider range of conditions. Innovations such as real-time soil monitoring, automated guidance systems, and improved drilling materials will further enhance the efficiency and accuracy of micro-tunnel boring operations.
With urbanization on the rise and the increasing need for sustainable infrastructure solutions, micro-tunnel boring will play a crucial role in shaping the cities of the future. Its ability to install essential underground utilities with minimal disruption makes it an indispensable tool for modern infrastructure development.
How GPRS Helps Ensure the Safety of Your Micro-Tunnel Boring Project
Even minimal surface disruption creates a risk of damaging existing subsurface infrastructure. While MTBMs are extremely precise and come equipped with technology designed to help them avoid buried utilities, underground storage tanks (USTs) and other subsurface obstructions, the only way to truly eliminate this risk is to hire a professional utility locating company like GPRS to provide you with complete and accurate data about the built world beneath your project site.
Our specially trained Project Managers utilize the latest subsurface investigation technology, including ground penetrating radar (GPR) scanners; electromagnetic (EM) locators, and CCTV camera-equipped sewer inspection crawlers and push-fed sewer scopes.
We visualize what you can’t see, giving you the data you need to avoid creating costly and potentially dangerous subsurface damage.
All this data is always at your fingertips thanks to SiteMap® (patent pending), GPRS project & facility management application that provides you with accurate existing conditions documentation to protect your assets and people.
Securely accessible 24/7 from any computer, tablet, or smartphone, SiteMap® allows you and your team to plan, design, manage, dig, and ultimately build better by serving as a single source of truth for the data you need to get the job done right.
From skyscrapers to sewer lines, GPRS Intelligently Visualizes The Built World® to keep your projects on time, on budget, and safe.
What can we help you visualize?
Frequently Asked Questions
Does GPRS offer lateral launch services?
Yes, we offer lateral launch services as part of our standard Video Pipe Inspection service.
Will I need to mark out the utilities that GPRS locates?
GPRS locates and marks all utilities for you, using a variety of tools and markers to highlight the locations of utilities, underground storage tanks (USTs) and whatever else may be hiding below your job site.