General contractors, plumbers, electricians, facility managers, and others routinely utilize ground penetrating radar (GPR) to visualize the interior of cast-in-place, slab on grade, post-tension, and pan deck concrete.
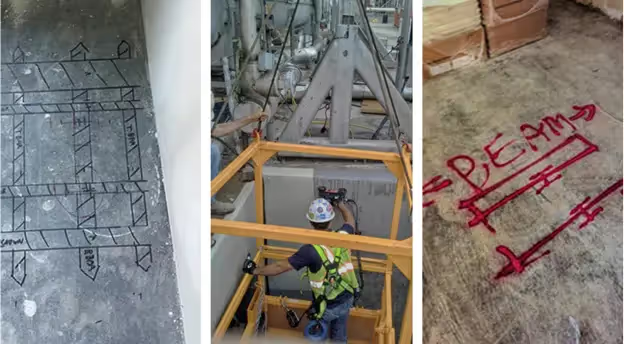
Because cutting or coring concrete without identifying embedments can have dire consequences to your schedule, your budget, and the safety of your crew. For instance, a single snapped post-tension (PT) cable can cost upwards of $20,000 to repair/replace, extreme damage can occur if you hit a water or sewer line, and slicing through an electrical conduit or gas line endangers the saw operator, the crew, and the building itself.
Each concrete imaging job is different because the methodology used to scan for rebar, PT cable, conduit and other primary and secondary utilities varies depending on the type of concrete construction and the customer’s needs.
What are the Various Kinds of Concrete Slabs in Construction?
There are six main varieties of concrete slabs in construction:
- Cast-in-place
- Ribbed/Waffle
- Slab-on-grade
- Pan/Metal Decking
- Hollow Core
- Post Tension
As previously mentioned, each one requires the GPRS Project Manager to utilize equipment and assess its infrastructure in different ways. Other factors, like the age of the concrete – how dry it may be – and obvious surface features, along with the customer’s needs, determine how the PM investigates and images the slab.
One of the most obvious differences in slab types is comparing pan deck concrete slab to post tension concrete slab. Pan decking is an industry jargon holdover for a type of corrugated metal base over which the concrete is poured. When planning to run conduit, reinforcements, etc. in a pan deck slab, the contractors generally place their embedments along the the “lows” of the corrugated base because it has the most space. In a PT slab, conduit would be placed so as not to intersect the post tension cables, each of which carries 33,000 pounds of load.
Understanding the layout of various slab infrastructures is only one part of the puzzle to an accurate concrete scan.
The age and dryness of the concrete can determine what dielectric value the PM uses to calibrate their equipment, and even that is influenced by the type of slab. For instance, they would not use the same dielectric value when assessing a six month old elevated slab as they would a six month old slab-on-grade.
What is a Dielectric Value?
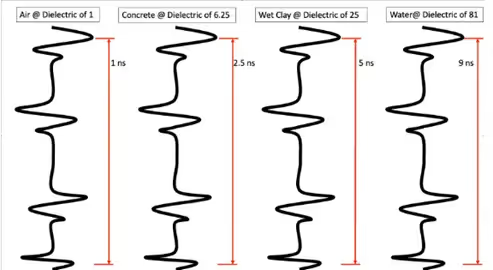
Dielectric values are ratio numbers without units like meters per second that represent a velocity in relationship to the speed of light to make discussing varying velocities easier.
299,792,458 meters per second is the speed of light, so we give it the dielectric value of 1.
Water, by comparison, travels at 1/9 the speed of light – 33,310,279 meters per second – so it is assigned the dielectric value of 81; because the square root of 81 is 9 and water’s velocity is 1/9 that of air/light.
All dielectric numbers work the same way – speed of light/square root of the dielectric – or speed = c/√k with c = speed of light and k = the dielectric constant.
Why it matters in concrete construction scanning & imaging is because GPR cannot determine how far a signal traveled, just the time and amplitude of the signal reflection. So, to gauge depth, you must know what speed the signal travels at through various materials.
SIM – How GPRS Maintains 99.8% Accuracy Nationwide
As you can probably guess by now, it takes an analytical mind and a lot of training to be able to properly assess the interior of concrete slabs. You cannot just rent or buy a GPR unit near you and understand what you’re seeing. The size, shape, thickness, and color of the signal readings – which present as hyperbolas – all carry data that helps a GPRS Project Manager “see” inside your concrete slab.
And at 99.8% accuracy on over 500,000 GPR jobs, this elite team of 500 PMs visualizes what’s underneath very well. The secret to their success is Subsurface Investigation Methodology, or SIM.
This industry-leading training is required for every GPRS Project Manager. It consists of 80 hours of classroom education and 320 hours of mentored field training – ensuring that each PM is an expert in utilizing multiple complementary technologies and methods to find what is inside your concrete.
It’s how GPRS Project Managers continue to maintain our 99.8% accuracy rate and is just part of “The GPRS Difference.” It’s our job to Intelligently Visualize The Built World® for your projects. When your PM marks out a green “clear” box on your concrete scan, GPRS backs it up with our Green Box Guarantee. If you cut or core within the green box and strike conduit, PT cables, rebar, etc., GPRS will pay the material cost to repair it.
What can we help you visualize?
Frequently Asked Questions
What is the difference between concrete testing and concrete scanning?
Concrete testing is a catchall term that covers various types of destructive and non-destructive techniques for assessing the strength and structural integrity of concrete. Concrete scanning and imaging can provide a snapshot of any reinforcements and embedments in a slab, but cannot find defects like honeycombing or cold joints. Learn more here.
Can GPR assess the structural integrity of concrete?
To assess the structural integrity of concrete, you require either ultrasonic pulse velocity testing (UPV) or tomography. GPR can find conduit, rebar, PT cables, and embedments, but cannot find structural defects. Learn more here.