National Resilience Inc., a San Diego-based biomanufacturer, is set to invest $225 million in West Chester Township, Ohio, transforming a former AstraZeneca plant into a state-of-the-art biomedical manufacturing facility.
This investment will create 274 new full-time jobs and is expected to bolster Ohio’s life sciences sector, making it a hub for medical research and pharmaceutical production, according to an article in the Journal-News. The project, supported by a tax incentive, reflects broader trends in the U.S. healthcare infrastructure, as the demand for advanced manufacturing and research facilities continues to grow.
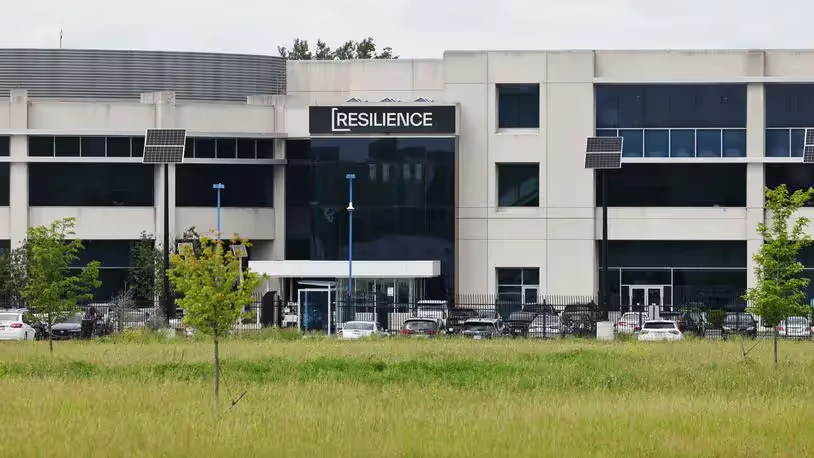
Overview of the Current Landscape
The construction of medical facilities in the United States is experiencing a transformative period, driven by the increasing demand for healthcare services, advancements in medical technology, and the expansion of life sciences sectors.
Medical facility construction spans a diverse range of projects, from traditional hospitals and outpatient centers to specialized research facilities and manufacturing plants for pharmaceuticals and medical devices. This growth is propelled by several key factors, including an aging population, the rising prevalence of chronic diseases, and the need for innovation in drug development and healthcare delivery. As a result, the sector has become a significant driver of economic activity in many regions, providing jobs and stimulating local economies.
Key Trends in Medical Facility Construction
1. Increased Investment in Life Sciences and Biomanufacturing Facilities:
The investment by Resilience in West Chester Township is part of a broader trend where biopharmaceutical companies are expanding their infrastructure to enhance drug development and production capabilities. The shift toward biomanufacturing facilities is evident as companies seek to strengthen the domestic supply chain and reduce dependency on foreign manufacturers.
2. Focus on Flexibility and Scalability:
Medical facility construction is no longer just about building larger spaces. Modern facilities are being designed with flexibility and scalability in mind, allowing them to adapt to changes in medical technologies and treatment protocols.
3. Emphasis on Sustainable and Efficient Design:
Environmental, social, and governance (ESG) policies are becoming a core component of new medical facility projects. Design strategies include using energy-efficient materials, incorporating renewable energy sources, and creating layouts that optimize patient and staff flow. These elements not only reduce operational costs but also contribute to a healthier environment for patients and healthcare professionals.
4. Regional Hubs for Health Innovation:
The availability of skilled labor, proximity to research institutions, and supportive state policies make locations like the Midwest and Northeast attractive for medical facility investments. The establishment of these hubs fosters collaboration and accelerates advancements in healthcare technologies.
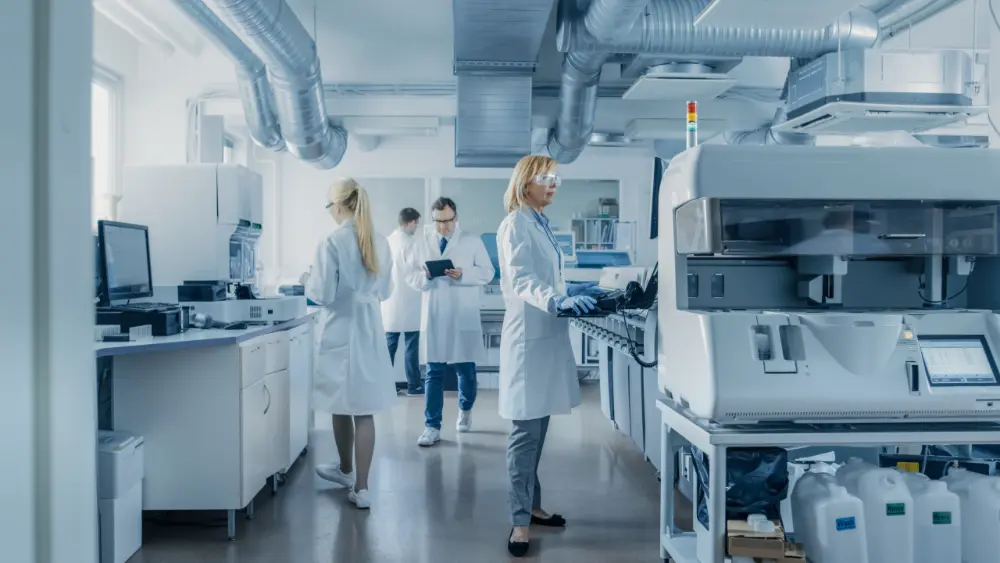
Challenges Facing the Industry
Despite the growth, the medical facility construction sector faces several challenges:
Rising Construction Costs:
Costs for labor and materials have been increasing, putting pressure on project budgets and timelines. The industry is adopting strategies such as prefabrication and modular construction to mitigate these expenses, but the challenge remains significant for many projects.
Regulatory Hurdles:
Medical facilities must comply with stringent regulations at both federal and state levels. Navigating these regulations can be time-consuming and costly, impacting project timelines and design flexibility. Companies must work closely with regulators to ensure compliance while maintaining their construction schedules.
Supply Chain Disruptions:
The global supply chain issues that emerged during the COVID-19 pandemic continue to affect medical facility construction. Delays in obtaining critical materials can slow down project completion, particularly for complex facilities that require specialized equipment and components.
The Role of Technology in Shaping Medical Facility Construction
Technology plays a pivotal role in overcoming many of the challenges in medical facility construction. Digital tools, such as Building Information Modeling (BIM), are used to optimize design and construction processes, enhance collaboration among stakeholders, and reduce errors. Additionally, technologies like 3D printing and robotics are being explored to streamline construction and create more precise components.
Telemedicine and remote patient monitoring have also influenced how new medical facilities are being designed. With the increase in virtual care options, some facilities are being reimagined to support these services, incorporating telehealth suites and digital infrastructure to connect patients and healthcare providers seamlessly.
Regional Insights: Ohio’s Role in Medical Facility Development
The investment by Resilience in Ohio is not an isolated case but part of a broader trend of increasing medical facility development in the Midwest. Ohio has become an attractive destination for biopharmaceutical and healthcare companies due to its strong workforce, proximity to major research institutions, and supportive state policies.
The Ohio Tax Incentive Authority’s decision to approve a 1.9%, 10-year Job Creation Tax Credit for Resilience underscores the state's commitment to fostering growth in the life sciences sector. Projects like this contribute to regional economic development by creating high-paying jobs, attracting further investments, and establishing Ohio as a leader in health innovation.
Ohio’s expanding medical and research facilities, coupled with investments from both private and public sectors, have positioned it as a key player in the U.S. healthcare landscape. The development of hubs like West Chester Township signals a shift in how medical research and production are distributed across the country, potentially reducing dependency on traditional biopharmaceutical centers like Boston or San Francisco.
Future Outlook
The future of medical facility construction in the United States is promising, with several emerging trends poised to shape the industry:
Integration of AI and Robotics:
Automation and artificial intelligence (AI) are expected to play a larger role in both construction processes and the operation of medical facilities. Robotics can assist in construction, while AI can help optimize the management of facilities once they are operational.
Continued Expansion of Biomanufacturing:
The demand for biopharmaceuticals is set to rise, spurring the need for more biomanufacturing facilities. Companies will continue to invest in expanding their capacities, as seen with Resilience, to meet the growing needs of the healthcare industry.
Shift Toward Outpatient and Ambulatory Care Centers:
With advancements in medical technologies and procedures, there is a shift from inpatient to outpatient care. This trend is influencing the design and construction of new facilities, which are being built to support minimally invasive procedures and shorter patient stays.
The current state of medical facility construction in the United States reflects a dynamic and rapidly evolving sector. Projects like Resilience’s investment in Ohio are emblematic of a broader push toward expanding the nation’s healthcare infrastructure, ensuring it meets future demands while supporting innovation and economic growth.
GPRS supports construction projects across industries, from hospitals to stadiums and beyond. Our subsurface damage prevention, existing conditions documentation, and construction & facilities project management services ensure your projects stay on time, on budget, and safe.
What can we help you visualize?
Frequently Asked Questions
What type of informational output is provided when I hire GPRS to conduct a utility locate?
Our Project Managers flag and paint our findings directly on the surface. This method of communication is the most accurate form of marking when excavation is expected to commence within a few days of service.
GPRS also uses a global positioning system (GPS) to collect data points of findings. We use this data to generate a plan, KMZ file, satellite overlay, or CAD file to permanently preserve results for future use. GPRS does not provide land surveying services. If you need land surveying services, please contact a professional land surveyor. Please contact us to discuss the pricing and marking options your project may require.
Can you find PVC piping and other non-conductive utilities?
GPR scanning is exceptionally effective at locating all types of subsurface materials. There are times when PVC pipes do not provide an adequate signal to ground penetrating radar equipment and can’t be properly located by traditional methods. However, GPRS Project Managers are expertly trained in multiple methods of utility locating.