The construction and operation of buildings account for nearly 40% of global carbon emissions, highlighting the need for sustainable practices.
Whole-Building Life Cycle Assessments (WBLCA) have emerged as a powerful tool for evaluating the environmental impact of buildings from cradle to grave. A WBLCA provides an in-depth look at the carbon footprint of a structure throughout its entire lifespan—offering essential insights for architects, developers, and policymakers aiming to minimize emissions and environmental harm.
What is a Whole-Building Life Cycle Assessment?
A WBLCA evaluates the environmental impact of a building across its entire life cycle, from material extraction to demolition and disposal. Unlike traditional assessments that focus only on operational energy use (like heating and cooling), WBLCA captures both embodied carbon and operational carbon. This broader view allows stakeholders to make informed decisions that reduce emissions not only during a building’s use phase but also throughout the construction and end-of-life phases.
The life cycle of a building generally involves several key stages:
- Material extraction and production – Mining, refining, and manufacturing building materials.
- Construction – Transporting materials to the site and assembling the building.
- Operation and maintenance – Energy and resource consumption throughout the building's life.
- Renovation – Emissions from periodic upgrades, repairs, or material replacements.
- Demolition and disposal – Emissions from dismantling the building and managing construction waste.
By covering all these phases, WBLCA offers a more comprehensive view of the environmental impact of a building, enabling strategies to reduce emissions at every stage.
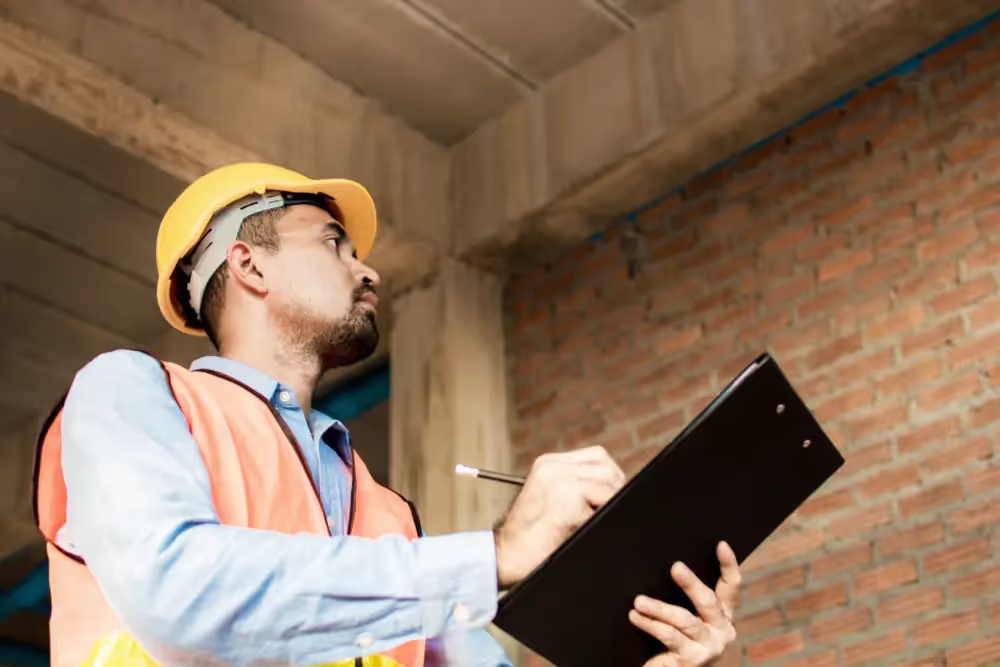
Key Components of a WBLCA
1. Embodied Carbon Analysis
- Embodied carbon refers to the emissions generated from material extraction, manufacturing, and construction activities. For many modern buildings, a significant portion of carbon emissions occurs before the building is even occupied. Cement, steel, and aluminum, common building materials, are highly carbon intensive
2. Operational Carbon Assessment
- This component analyzes energy consumption during the building’s operational phase. It includes emissions from heating, cooling, electricity, and water use. With advances in energy-efficient technologies, operational emissions are becoming easier to control, but they remain a crucial part of the building’s environmental footprint
3. Material Reuse and Recycling Potential
- A WBLCA examines the potential for reusing or recycling building components at the end of the structure’s life. Incorporating recyclable materials and designing for easy disassembly can significantly reduce end-of-life emissions
Why Conduct a WBLCA?
A WBLCA is essential for achieving sustainable construction. Here are some of the key reasons why architects and developers increasingly rely on it:
1. Identify Carbon Hotspots
- WBLCA reveals which materials or processes contribute the most to a building’s carbon footprint. This insight allows stakeholders to focus on reducing emissions where it matters most, such as by substituting high-carbon materials with greener alternatives
2. Optimize Design for Sustainability
- WBLCA supports eco-friendly design decisions. For example, it may encourage the use of mass timber instead of steel or the incorporation of renewable energy systems. It also helps determine whether retrofitting an existing building is more sustainable than constructing a new one
3. Meet Green Building Standards
- Many certification programs, such as LEED (Leadership in Energy and Environmental Design) and BREEAM (Building Research Establishment Environmental Assessment Method), require WBLCA as part of their criteria. WBLCA aligns building projects with these certifications, making them more attractive to investors and tenants focused on sustainability
4. Future-Proofing Buildings
- As regulations tighten around carbon emissions, WBLCA helps developers comply with future policies. With cities moving toward carbon-neutral building requirements, conducting a life cycle assessment ensures that buildings remain in compliance with evolving regulations
How to Put WBLCA into Practice on Your Project
A thorough WBLCA follows several structured stages to provide actionable insights:
1. Goal and Scope Definition
- At this initial stage, stakeholders determine the purpose of the assessment and what phases of the building’s life cycle to include. Some assessments may focus solely on embodied carbon, while others aim to capture both operational and embodied emissions
2. Inventory Analysis
- This step involves gathering data on all materials, energy, and processes involved in constructing, operating, and decommissioning the building. It covers materials like concrete, steel, wood, and glass, as well as energy sources used during operation
3. Impact Assessment
- Using specialized software tools, such as One Click LCA or Tally, the environmental impacts of the building are quantified. This analysis can evaluate a variety of metrics, such as global warming potential (GWP), water use, and resource depletion
4. Interpretation and Recommendations
- The final stage involves analyzing the results and providing recommendations for improvement. This could include switching to low-carbon materials, improving energy efficiency, or extending the building's lifespan
Challenges in Conducting a WBLCA
Despite its many benefits, conducting a WBLCA can be complex and requires careful planning. Some of the challenges include:
- Data Availability and Quality: Reliable data on the carbon content of materials or construction processes is not always accessible, which can limit the accuracy of the assessment
- Software and Expertise: WBLCA requires specialized tools and expertise, making it a more demanding process compared to traditional energy audits
- Time and Cost Constraints: Conducting a WBLCA adds time and cost to the design phase, which may be challenging for developers working on tight schedules
However, many of these challenges can be mitigated with the growing availability of databases and streamlined software tools, along with the increasing familiarity of design teams with WBLCA principles.
Examples of WBLCA in Action
Several projects have successfully integrated WBLCA into their design process, demonstrating its value:
- Bullitt Center, Seattle: Dubbed the greenest commercial building in the world, the Bullitt Center used WBLCA to minimize embodied carbon using sustainable materials and a design focused on long-term durability
- The Edge, Amsterdam: This office building uses energy-efficient systems and smart technologies, guided by WBLCA insights, to maintain a low carbon footprint over its lifetime
These examples highlight how a commitment to life cycle assessment can lead to innovative designs that balance sustainability and functionality.
The Future of WBLCA in the Building Industry
As the building sector faces mounting pressure to reduce emissions, WBLCA will play a pivotal role in shaping future construction practices. Several trends are emerging that may drive wider adoption:
- Integration with Digital Tools: Building Information Modeling (BIM) systems are increasingly incorporating WBLCA modules, making it easier to conduct assessments during the design phase
- Regulatory Support: Governments are beginning to mandate life cycle assessments for new construction, especially in urban areas aiming for net-zero emissions by 2050
- Focus on Circular Economy: WBLCA supports the transition toward a circular economy by encouraging the reuse of materials and reducing waste through better design
How GPRS Services Support WBLCA
Whole-Building Life Cycle Assessments offer a comprehensive approach to understanding and minimizing the environmental impact of buildings. By capturing emissions across all stages—from construction to demolition—WBLCA provides critical insights that enable developers and architects to make sustainable design choices. While challenges remain in terms of data availability and complexity, the growing emphasis on carbon reduction and green building certifications ensures that WBLCA will become a standard part of the design and construction process.
As the construction industry moves toward a more sustainable future, WBLCA serves as a vital tool for reducing carbon footprints and aligning building projects with global climate goals. Through thoughtful implementation, it enables the creation of buildings that are not only environmentally responsible but also economically viable and resilient for generations to come.
GPRS existing conditions documentation services support WBLCA, ensuring you and your team stay on time, on budget, and safe. We offer 2-4mm accurate 3D laser scanning and BIM services to visualize the built world both above and below ground, giving you a complete and accurate picture what your job site.
What can we help you visualize?
Frequently Asked Questions
What is the difference between a design intent and as-built model?
DESIGN INTENT – deliverables will be shown as a "best fit" to the point cloud working within customary standards, such as walls being modeled 90 degrees perpendicular to the floor, pipes and conduit modeled straight, floors and ceilings modeled horizontal, and steel members modeled straight. This will produce cleaner 2D drawings and will allow for easier dimensioning of the scan area. The deliverables will not exactly follow the scan data to maintain design intent standards. Most clients will want this option for their deliverables.
AS-BUILTS – deliverables will be shown as close as possible to actual field capture. If walls are out of plumb, pipes and conduit show sag, floors and ceilings are unlevel, steel members show camber, etc., this will be reflected in the model. This will produce reality-capture deliverables, but 2D drawings may show “crooked” or out of plumb lines, floors will be sloped or contoured, steel members may show camber, twisting or impact damage. Dimensioning will not be as easy due being out of plumbness/levelness, etc. This option should be used when the exact conditions of the scan area is imperative. Clients using the data for fabrication, forensic analysis, bolt hole patterns, camber/sag/deformation analysis, and similar needs would require this option.
What deliverables can GPRS provide when conducting 3D laser scanning services?
We can provide 3D modeling in many formats such as:
- Point Cloud Data (Raw Data)
- 2D CAD Drawings
- 3D Non-Intelligent Models
- 3D BIM Models
- JetStream Viewer
Customizable Deliverables Upon Request include:
- Aerial Photogrammetry
- Comparative Analysis
- Deformation Analysis
- Digital Drawings of GPR Markings
- Floor Flatness Analysis/Contour Mapping
- New Construction Accuracy Analysis/Comparative Analysis
- Point Cloud Modeling Training Webinars
- Reconciliation of Clients 2D Design Drawings
- Reconciliation of Clients 3D Design Model
- Structural Steel Shape Probability Analysis
- Template Modeling
- Volume Calculations
- Wall Plumb Analysis