Every year since 2015, the Prix Versailles awards have celebrated outstanding achievements in architecture and design on a global scale.
AECOM and luis vidal + architects’ striking Terminal E expansion at Boston Logan International Airport was one of six projects recognized in the Prix Versailles list of the World’s Most Beautiful Airports for 2024 for their aesthetic qualities and impact on the travel experience of users.
Existing Conditions, a GPRS Company, proudly supported this project with our architecture-grade 3D laser scanning and modeling services, meticulously documenting the airport’s existing mechanical, electrical, and plumbing (MEP) systems and a conveyor system, and verifying the flatness and levelness of a newly poured concrete floor.
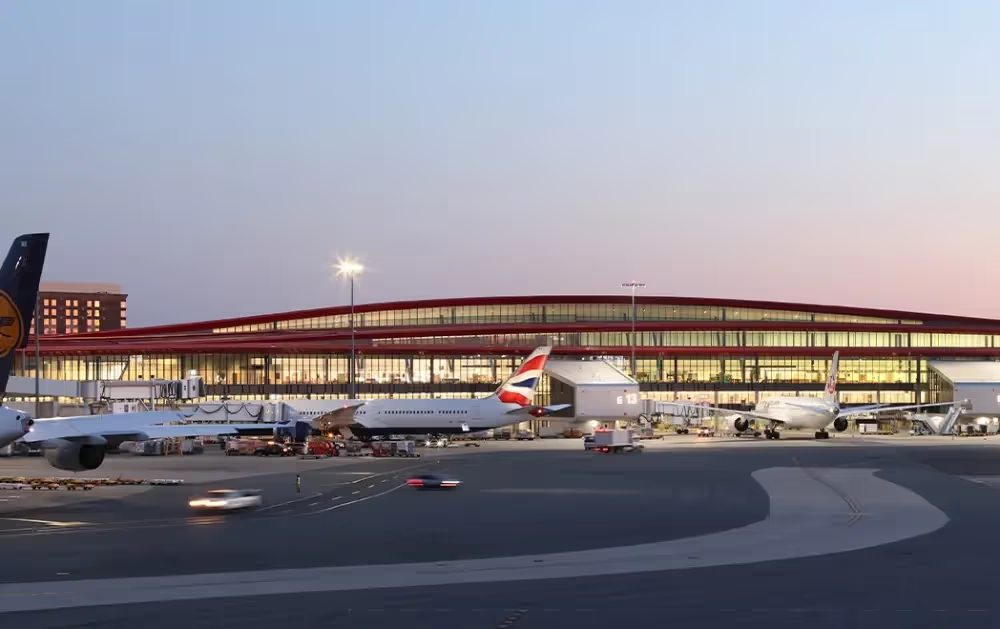
Compared to a ruby-red, intergalactic spaceship due to its prismatic red roof that subtly changes color depending on the light, Terminal E features four additional gates, restaurants, a duty-free shop, and one of Delta Air Lines’ posh Sky Clubs: lounges reserved for Delta’s first or business class passengers and those flying on partner airlines.
Beyond its distinctive aesthetic, the terminal integrates green technologies like photovoltaic glass, which converts ultraviolet and infrared light into electricity, and uses recycled materials to help reduce greenhouse gas emissions. Key infrastructure is elevated above the floodplain for added resilience, while the roof and envelope are engineered to exceed code requirements, withstanding heavy snow, ice, rainwater, and the extreme winds of a 500-year storm. Additionally, the building’s design functions as a noise barrier, lessening sound from planes and airport activities for nearby East Boston residents.
AECOM’s website notes that the terminal’s energy-efficient features resulted in a 25% reduction in energy consumption, exceeding Massachusetts Energy Code standards.
“Massport (Massachusetts Port Authority) conceived the new Terminal E as a modern, iconic, international terminal that elevates Logan Airport’s reputation for providing an enhanced passenger experience,” AECOM Principal Architect and Senior Vice President Terry Rookard told Engineering News-Record.
Suffolk Construction, the pre-construction and construction management firm on the project, initially contracted Existing Conditions to perform 3D laser scanning and create a 3D Revit model of a basement area housing the airport’s baggage conveyor belts. The challenge was that the scanning had to be completed while the airport remained operational, and in a work area densely packed with not just the conveyor belts, but also MEP lines.
Our Project Managers used the compact BLK360 laser scanner to navigate these tight spaces.
Following this initial phase, Suffolk enlisted Existing Conditions for several additional stages of work. In Phase 2, we scanned above the main concourse ceiling to map MEP lines. Next, we conducted further scanning near the original basement area to locate all existing MEP lines, ensuring new lines could be installed without interference.
In Phase 4, Suffolk asked Existing Conditions to scan the new construction after MEP lines were installed but before sheetrock, meeting a Massport requirement for precise as-built documentation. Existing Conditions also deployed a P50 scanner to verify the levelness of a concrete floor prior to the installation of terrazzo flooring on top. Lastly, we scanned a mechanical area above the terminal where equipment was set for demolition and replacement.
“There weren’t any surprises to the data that we captured,” explained Brian Ely, GPRS Service Line Leader for Reality Capture. “But the speed of our work, ease of working with both the construction company’s timeline and interfacing with the airport and their security teams led to more and more work at this project. It started with a very small area that we scanned in the basement and led to us scanning the entirety of the new terminal.”
3D laser scanning employs LiDAR technology to gather spatial data by emitting laser beams toward an object or structure and measuring the return time of the laser pulses. This timing, combined with angular data, allows the scanner to calculate the precise distance and orientation of each point on the object’s surface. Scans are taken from various angles to generate a dense collection of 3D coordinates, forming a point cloud representation of the site. This point cloud can then be transformed into 3D Building Information Modeling (BIM) and 2D CAD drawings.
Accurate and comprehensive as-built data is a valuable tool for architects and engineers because it offers a detailed record of the building’s current state prior to renovations and expansions.
3D laser scanning captured highly detailed and accurate digital measurements of Terminal E’s infrastructure to assist with the safe and successful expansion of the structure. Suffolk Construction and its partners were able to reference this accurate site data as they completed their work, and it will be preserved for future O&M purposes.
From skyscrapers to sewer lines, GPRS and Existing Conditions Intelligently Visualize The Built World® to keep your projects on time, on budget, and safe.
What can we help you visualize?
Frequently Asked Questions
What are the benefits of 3D laser scanning?
- Millions of real-world data points—A single laser can capture up to a million 3D data points per second, providing incredibly rich detail of every aspect of your project
- Eliminate error—Individual measurements acquired by tape measures or hand-held devices are subject to errors. Laser scanning is the most accurate form of measurement available, delivering accuracy of a few millimeters or less
- Answers unanticipated questions—How many times have you left the job site only to discover you need a few more measurements? A 3D BIM scanning will capture extra data, eliminating the need to return to the project to answer unanticipated questions
- Reduce change orders and waste—The cost of a laser scan pales in comparison to the cost of change orders and construction delays. Incorporating a laser scan into the design of your project assures accurate and complete information, avoiding costly headaches, clashes and wasted material during the construction phase
- Minimize shut-down times—Laser scanning is quick, safe and non-intrusive – eliminating or minimizing operational shutdowns and client inconvenience
- Increase safety—3D scanning can obtain measurements in hazardous locations while keeping workers out of harm’s way