GPRS’ 3D Laser Scanning, and Mapping & Modeling services are typically used to ensure the safety and success of projects in the architecture, engineering, and construction (AEC) industries.
But every so often, we’re asked to tackle more unique challenges – like creating a 3D mesh model of the largest animal that ever walked the earth.
GPRS Project Manager Stanley Jones recently laser scanned a sauropod skeleton that’s under the care of Fossilogic, a company that specializes in the preparation and mounting of fossils for display. Jones traveled to Fossilogic’s facility in Pleasant Grove, Utah, to scan the prehistoric creature for a company called Research Casting International, which specializes in the creation of museum exhibit projects and commissions.
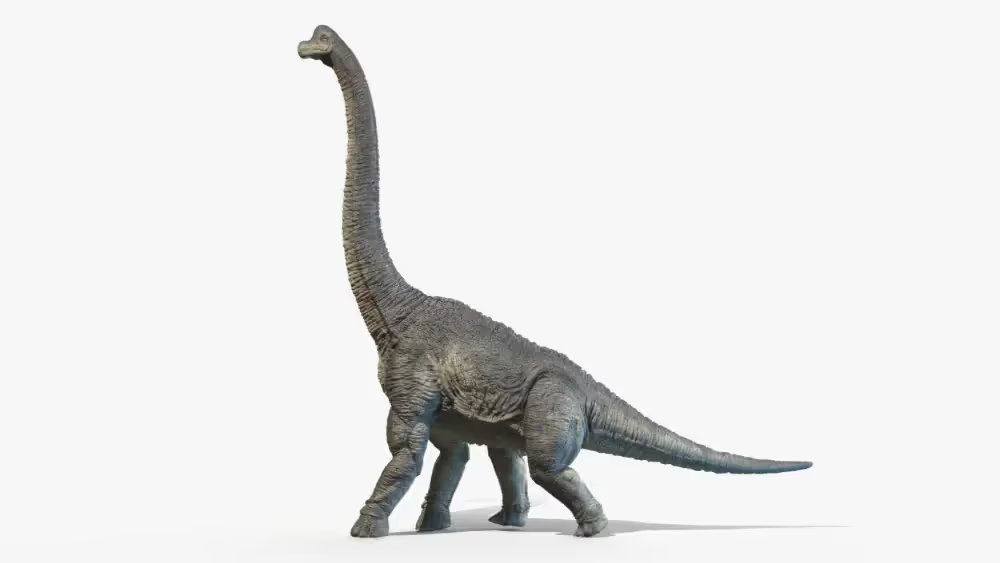
Sauropods are from the dinosaur subgroup Sauropoda, the largest of all dinosaurs and the largest land animals that have ever lived. These four-legged herbivores are known for having small heads, and long necks and tails. Hollywood has made household names of sauropod species such as the Apatosaurus and Brachiosaurus through film franchises such as Jurassic Park and Land Before Time.
Research Casting was preparing to have their sauropod skeleton and its display moved from Fossilogic’s facility to a museum in Abu Dhabi, but they needed an engineer to verify the display stand’s structural integrity prior to shipping. Rather than incur the cost and delays inherent in having the engineer travel to Fossilogic’s facility to evaluate the display in person, Research Casting turned to GPRS to collect the data needed for the engineer to complete their work remotely.
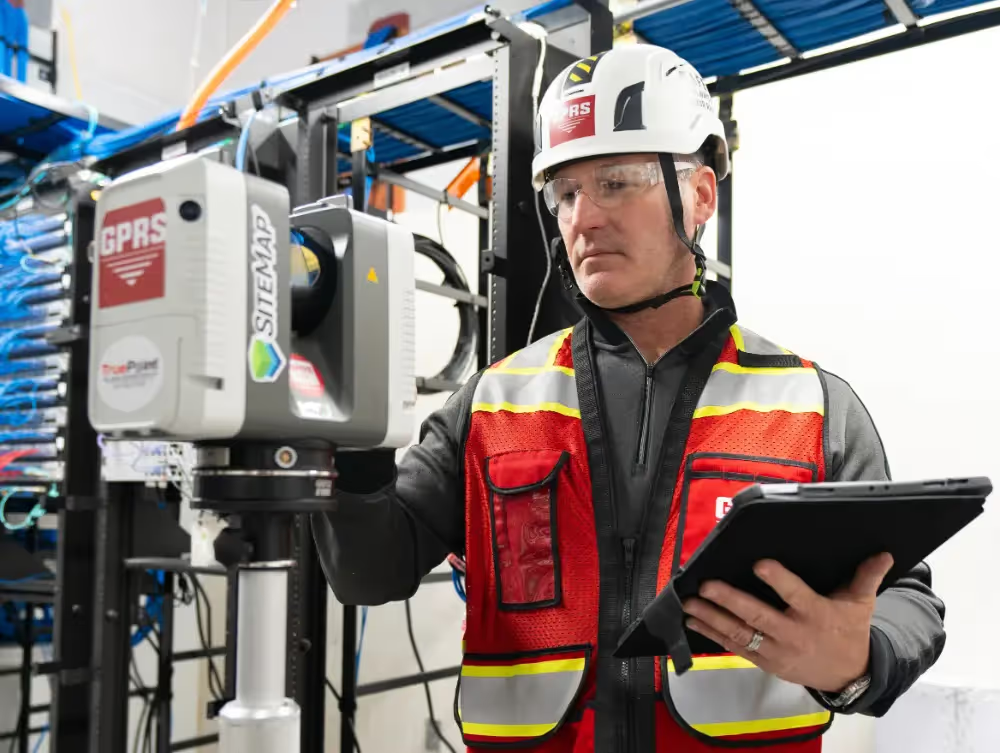
3D laser scanners use LiDAR (light detection and ranging) to measure and record precise locations and distances, ultimately producing a point cloud file. These lightweight and mobile scanners produce highly accurate digital measurements and images quickly and easily for use in construction and engineering projects. That data is invaluable in design, prefabrication, asset management, and facility modifications.
GPRS’ in-house Mapping & Modeling Team can take the data collected on-site by our Project Managers and use it to create custom deliverables to suit our clients’ individual needs. This includes virtual tours, 2D and 3D as-built drawings, and digital twins: computer models that accurately represent a physical object, process, or system.
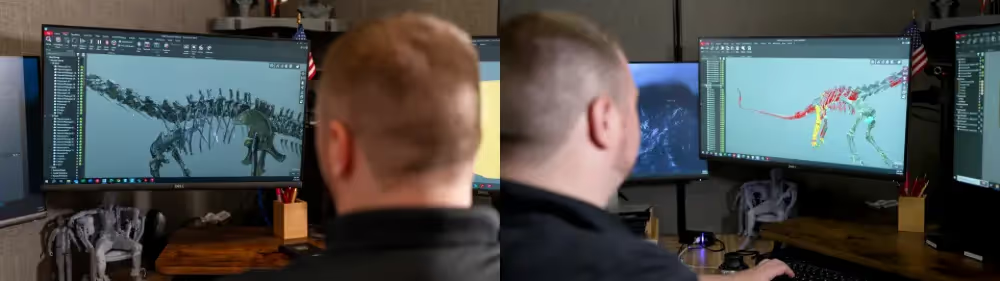
“Clean laser scanning point cloud data can be turned into a mesh to make a lighter-weight data set by extracting a surface model representing all surfaces, edges and openings, intricately and accurately, in a true as-built condition,” said GPRS Mapping and Modeling Manager Michelle Colella. “Literally everything visible to the line of sight of the scanner is captured in the data.”
Despite its unique size and shape, Jones said that scanning the sauropod skeleton and its display was fairly similar to scanning a building or other structure.
“My biggest challenge was capturing the top of the skeleton,” he said. “There was a staircase on one side of the warehouse, which allowed me to get a general overview, but probably not the level of detail they were looking for. Luckily, I had an extending tripod with me in my truck. I was able to utilize that to capture a few more scans around the skeleton to make sure I was capturing all the smaller bones and display structure that were tucked away.”
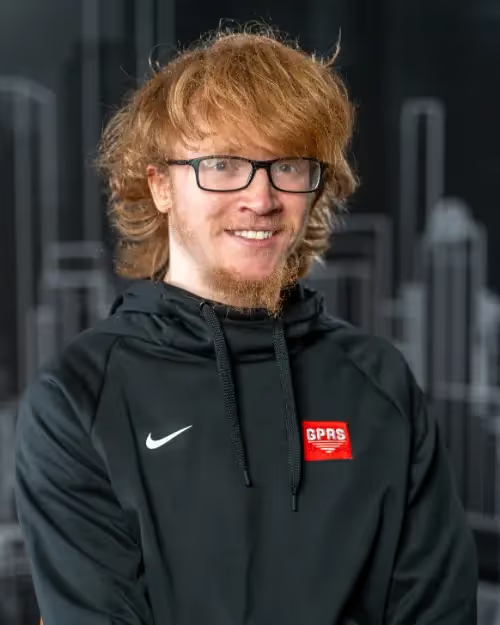
GPRS Project Engineer Adam Knapp was part of the team that took Jones’ scans and created a 3D mesh model of the fossilized skeleton, which may also be used in the future to create replicas for other museums. Over a few weeks, the team modeled every bone of the mammoth creature.
“So, first it went through our Registration Team, they got the point cloud [from Stanley], but it doesn’t yet have any solid parts to it,” Knapp said. “It’s just a bunch of dots. And my job was to break all those dots into the individual bones and then turn those bones into solid pieces... It was 240ish [bones].”
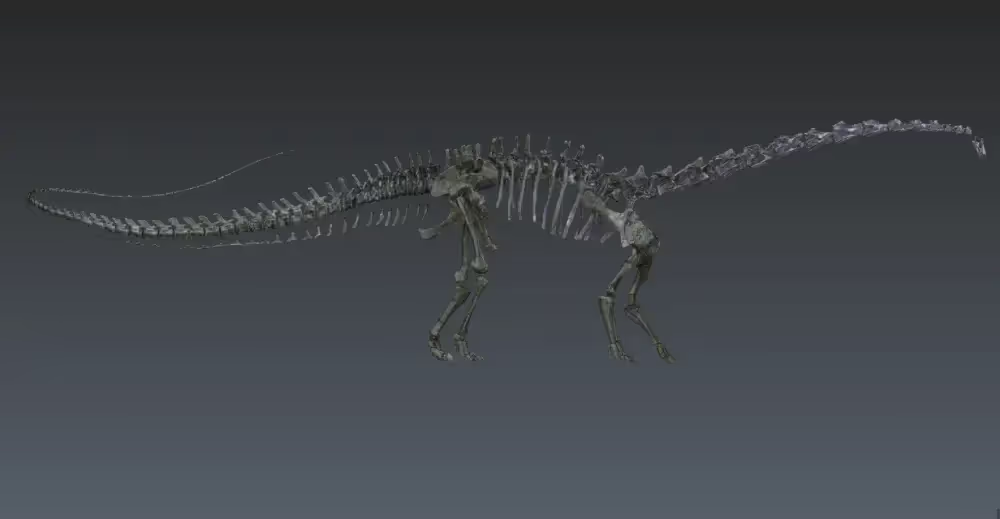
To model the sauropod’s bones, Knapp utilized Leica’s Cyclone 3DR program, which specializes in replicating uneven surfaces or other objects that don’t conform to typical shapes. Here, it was used to model the irregular surfaces of the sauropod’s bones.
“It’s a program that’s better for [more organic shapes],” Knapp said. “The computer kind of builds a decent [version] of [the bones], and then my job would be to tweak that and make it look more like it’s supposed to.”
GPRS’ 3D Laser Scanning and Mapping & Modeling services intelligently visualized the fossilized sauropod skeleton so that it could safely complete the 7,841-mile journey from Utah to Abu Dhabi. And so that replicas of this spectacular display can educate and amaze generations of future museum visitors around the world.
What can we help you visualize?
Frequently Asked Questions
What is the difference between LiDAR (Time-of-Flight) and Phase-Based Scanning?
LiDAR stands for Laser Imaging, Detection, and Ranging (commonly called Light Detection and Ranging). LiDAR is based on a principle referred to as time-of-flight, which uses a pulsed laser that emits the beam, a mirror that deflects the beam towards the scan area, and an optical receiver which detects the laser pulse and reflects it back to the scanner from the object. Time-of-flight refers to using the known speed of light with the amount of time it takes the laser pulse to be emitted, bounce off an object, and return to the scanner to determine the distance the object is from the scanner (Distance = (Speed of Light x Time of Flight) / 2). LiDAR scanning collects data at a slower rate than phase-based scanners but can be used at greater distances.
Phase-based scanners emit a constant laser beam into multiple phases and compare the phase shifts of the returned laser energy. The scanner then uses phase-shift algorithms to determine the distance, based on the unique properties of each individual phase (Time of Flight = Phase Shift / (2π x Modulation Frequency)). Although phase-based scanners collect data at a much higher rate than time-of-flight scanners, their effective distance is much shorter. Additionally, phase-based scanners tend to have more "noise," or false data, than time-of-flight scanners.
What is SLAM?
SLAM stands for Simultaneous Localization & Mapping. SLAM's purpose is to move through a given space to create a digital map of that space that users can refer to.
For a better understanding, let's break down the term. Localization is to find the location of an object with reference to its surroundings. Mapping is to map the layout and framework of the environment.
In 3D scanning, a SLAM algorithm uses the LiDAR sensor to track a precise estimate of the point cloud scanner’s position as it moves through a space. The mapping software, in turn, uses this data to align your point cloud properly in space.