What could it mean to mid and downstream oil & gas providers, water system managers, and power system operators if they could receive critical underground infrastructure data like temperature fluctuations, pipe strain, and acoustics, giving them real-time information to mitigate risk to their pipeline and transmission infrastructure before they become disastrous?
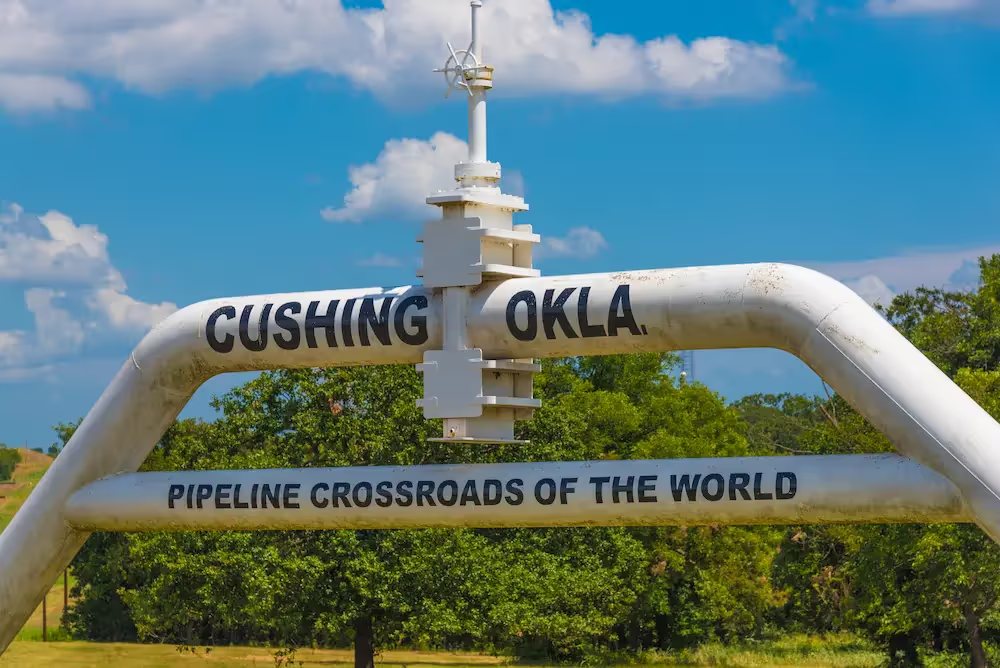
What is the Scope of the Problem for Pressurized Pipeline Leaks?
According to data compiled by the National Transportation Safety Board, 827 “high consequence” oil & gas leaks and 167 reported transmission line accidents occurred; and 1.05 million individual repairs were made to oil & gas transmission infrastructure from 2017-2022. And those are just the figures for oil & gas mid and downstream pipelines.
Pressurized water infrastructure, while less of an immediate threat to people and property than petroleum products, is arguably more valuable because delivery of clean water is vital to survival.
There are more than 2.2 million miles of transmission and distribution mains in the U.S., and one of them breaks every two minutes. Overall, it is estimated that there are a minimum of 10 active leaks for every 100 miles of pipe, spilling some 2.5 trillion gallons of water annually.
How many of those leaks, accidents, and expensive repairs could have been avoided by applying real-time sensor data to pipeline infrastructure?
What are the Best Practices for Predicting Pipeline Damages?
The Pipeline and Hazardous Materials Safety Administration has issued important risk model reporting and guidelines to assist oil and gas system managers in mitigating risk among four major risk model types:
Qualitative – Created with verbal or ordinal category inputs and outputs. The model’s logic defines output categories from calculated combinations of input categories.
Relative Assessment/Index – This model is synonymous with the risk index model and is based on a unit-less risk measurement calculated from ordinal input information, although an index model “does not attempt to adhere to the laws of probability.”
Quantitative System – Created with inputs and outputs that are both quantitative and model the physical and logical relationships of risk factors to provide quantitative outputs for the likelihood and consequences; represented as standard units of frequency, probability, and expected loss.
Probabilistic – The inputs that populate this model are quantities and/or probability distributions to calculate probability distributions. This model does attempt to adhere to the laws of probability.
Each of these models was developed and algorithmically evaluated for its ability to “support pipeline risk management decisions and regulatory requirements.”
While the PHMSA determined that Quantitative and Probabilistic models are the most flexible and offered the most ability for complexity, they reiterated that “adequate and accurate data is needed for the application of all risk model types.”
Further, they cited that “Pipeline operators should take ongoing actions to improve and update data quality and completeness over time… operators should select the best model approach and then populate the model with the best information currently available…”
How Do You Get the Most Accurate Pipeline Assessment Data?
Utilizing any of the risk mitigation models and measures recommended by the federal government all have one thing in common – the need for the most accurate, real-time data possible.
For pipeline operators that means release detection sensors and SCADA-style systems. SCADA stands for Supervisory Control and Data Acquisition – a computerized system that collects and analyzes pipeline sensor data.
It also means having accurate and up-to-date utility infrastructure maps, and regular leak detection and water loss surveys to discover potential risks before they become big, expensive, and dangerous problems.
All kinds of valve, pressure, and release sensors are available to help monitor pressurized pipelines. A new player has recently emerged on the field: VIAVI Solutions, Inc. and its NITRO Fiber Sensing technology. According to reporting from Underground Infrastructure, the NITRO system derives real-time continuous data reportage from fiber lines “deployed at strategic locations, including along power cables and pipelines… [NITRO] provides valuable infrastructure health data that can be used to drive proactive maintenance and prevent downtime.” NITRO offers Distributed Temperature Sensing, Simultaneous Temperature and Strain Sensing, and Distributed Acoustic Sensing technologies for critical oil and gas pipelines, pressurized water lines, power distribution, and data lines.
It requires a hefty investment, to be sure, for the installation of such sensitive real-time data capture. It also requires the application of directional drilling to install fiber lines near critical transmission lines. So, an accurate and comprehensive assessment of the existing conditions of all underground utilities and their locations is essential before installing this new sensor technology.
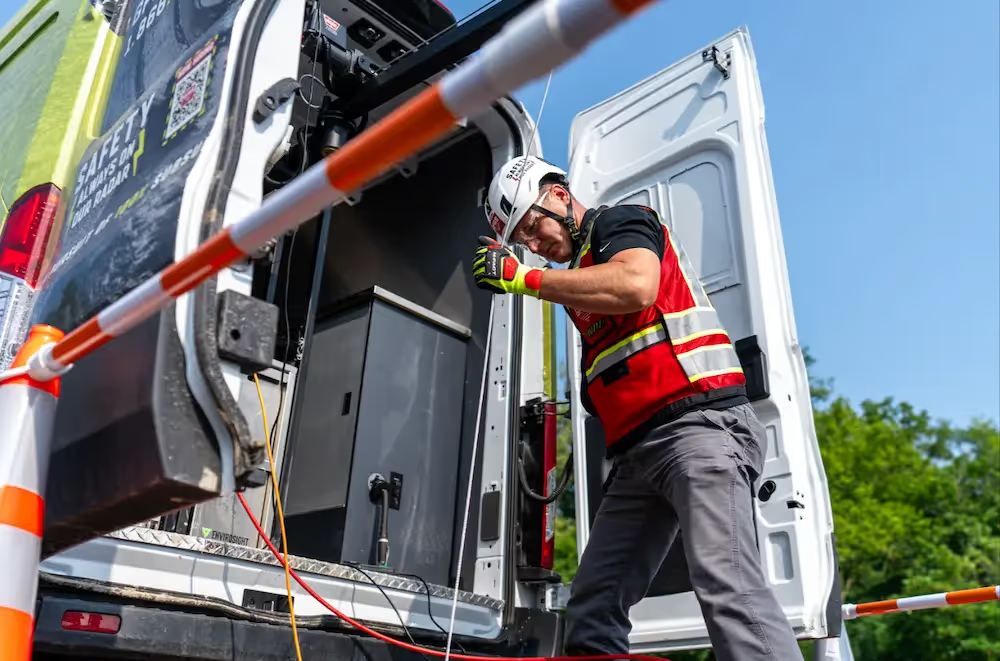
GPRS offers comprehensive pre and post-cross bore inspections for directional drilling projects nationwide, plus 99.8%+ accurate utility locating and mapping, pinpoint acoustic leak detection, and NASSCO-certified Video Pipe Inspection reporting.
We are the nation’s largest company committed to Intelligently Visualizing The Built World® for our customers. What can we help you visualize?
Frequently Asked Questions
How often do oil pipelines leak?
The frequency of oil pipeline leaks varies depending on a number of factors; maintenance, technology, and regulation all play a role in pipeline risk mitigation. In the U.S., the PHMSA reported an average of 289 significant pipeline incidents annually between 2017 and 2021. These incidents include leaks, spills, and other hazardous situations. According to a 2021 report by the Environmental Defense Fund, the U.S. experiences approximately one pipeline leak per day. Data from the International Energy Agency (IEA) indicates that while pipeline leaks are relatively rare compared to the volume transported, the environmental impact can be significant, especially when leaks go undetected for extended periods. Enhanced monitoring, improved materials, and stricter regulations have reduced the frequency of large leaks, but small leaks remain a persistent challenge.
For more information on Upstream, Midstream and Downstream pipeline risk mitigation solutions and safety planning, click here.
How often are pipelines inspected?
Oil, gas, and water pipelines are inspected regularly, though requirements vary depending on the type of pipeline, regulations, and risk factors. U.S. federal regulations mandate that oil and gas pipelines in high-consequence areas (HCAs) be inspected at least once every seven years using inline inspection tools, the most popular of these tools is known as a "smart pig." A smart pig are devices outfitted with sensors, and data recording and transmission systems, that can also clean the pipeline as needed.
According to the PHMSA, pipelines are also required to undergo additional monitoring and maintenance based on their age, material, and environmental risks. Water pipelines, governed by different standards, typically undergo inspections every one to five years, depending on the system's condition and the potential for contamination. The American Water Works Association (AWWA) recommends more frequent inspections for older or high-risk systems to ensure safety and reliability.
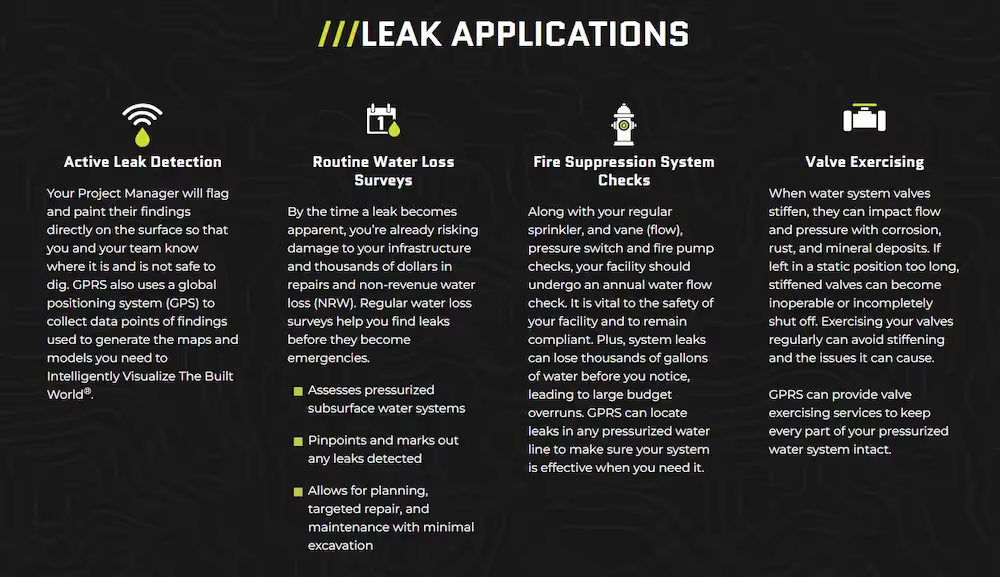
To learn more about non-destructive pipeline system mapping and leak detection, click here.