The Basics of MEP Installation
Mechanical, electrical, and plumbing (MEP) installation involves a series of highly coordinated steps performed by contractors to integrate their systems into a building's structure. Throughout the installation process, contractors prioritize safety, quality, and code compliance to ensure that MEP system installations are performed safely, function properly, and are reliable for the life of the building.
Before installation begins, a general contractor would need up to date as-builts to develop MEP design plans. If existing conditions documentation does not exist or is not up to date, then the contractor would reach out to a 3D laser scanning company to scan the site and deliver accurate as-builts. Precise building layouts, dimensions, elevations, and distances ensure the successful planning and installation of MEP systems.
A general contractor would also need the locations of underground utilities (e.g. gas lines, water pipes, electrical cables, etc.) for planning and safety purposes. They would reach out to a utility locating company to conduct on-site investigations and receive up-to-date utility maps.
They will utilize comprehensive site information to plan MEP routes and coordinates with trades. Once planning is complete, the trade contractors will prepare the construction site for MEP installation by clearing obstacles and double checking that MEP systems are routed around utilities to ensure a safe working environment. They may also install temporary supports or scaffolding as needed.
Next, they will rough-in the basic framework and components of MEP systems before finishing materials are applied. Rough-in installation includes:
- HVAC Mechanical: Ductwork, air handlers, vents, and other HVAC components are installed according to the design layout.
- Electrical: Conduit, wiring, panels, and distribution equipment are installed to deliver power throughout the building.
- Plumbing: Pipes, fixtures, valves, and pumps are installed to supply water, gas, and drainage systems.
Throughout the installation process, contractors coordinate closely with other trades to ensure that MEP systems integrate seamlessly with structural elements, architectural features, and other building systems.
Once the rough-in installation is complete, contractors conduct tests and inspections to verify the functionality of MEP systems. After passing inspections, contractors complete the final installation of MEP components and make any necessary adjustments.
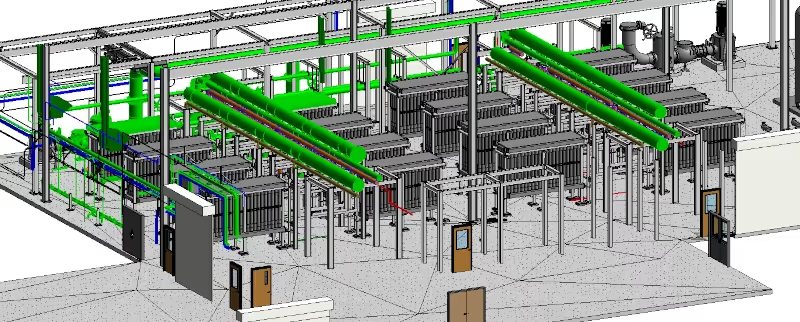
How Do Contractors Capture Existing Site Conditions?
Having accurate as-builts prior to MEP design planning will ensure smooth integration and installation of MEP systems with the existing building design. This is accomplished by 3D laser scanning the site.
3D laser scanners use LiDAR (light detection and ranging) technology to capture millions of three-dimensional data points of a space. Each data point is converted into a pixel with an XYZ coordinate. Millions of data points are captured and processed into a point cloud, creating an accurate 3D as-built data set of the site. The technology delivers highly accurate digital layouts and dimensions for construction professionals.
What Benefits Can 3D Laser Scanning Provide for MEP Contractors?
3D laser scanning captures as-built site conditions, assists with clash detection, optimizes spatial planning and layout, verifies system installation, and provides progressive documentation for MEP contractors.
Accurate As-Built Documentation: Laser scanning accurately captures the existing conditions of a building or site, providing detailed as-built documentation. This information ensures that MEP systems are designed and installed to fit precisely within the existing structure, minimizing clashes and rework.
Clash Detection: Laser scanning produces point clouds that can be overlaid on top of MEP design models. This provides data for general contractors to perform clash detection and identify conflicts between MEP systems and other structural and architectural building elements. By detecting clashes early in the design phase, costly on-site conflicts and revisions are minimized.
Spatial Planning and Layout Optimization: Laser scanning provides precise measurements of available space, enabling MEP engineers to optimize the layout of systems for efficient use of space and minimal interference with other building elements. This optimization can lead to more cost-effective designs and streamlined installation processes.
Upgrades or Modifications: 3D laser scanning captures precise details of existing equipment and MEP features so that upgrades or modifications can be tied into existing systems and installed with confidence, fitting seamlessly into the existing space.
Construction Verification: During construction, laser scanning can be used to verify that MEP systems are being installed according to design specifications. By comparing scan data with the design models, any deviations or discrepancies can be quickly identified and addressed.
Progress Monitoring and Documentation: Laser scanning can be used to monitor construction progress over time, providing a visual record of MEP installation at various stages of construction. This documentation can be valuable for project management, quality assurance, and ongoing maintenance.
3D laser scanning enhances the efficiency, accuracy, and coordination of the MEP installation process, improves construction workflows, and increases the quality of MEP systems.
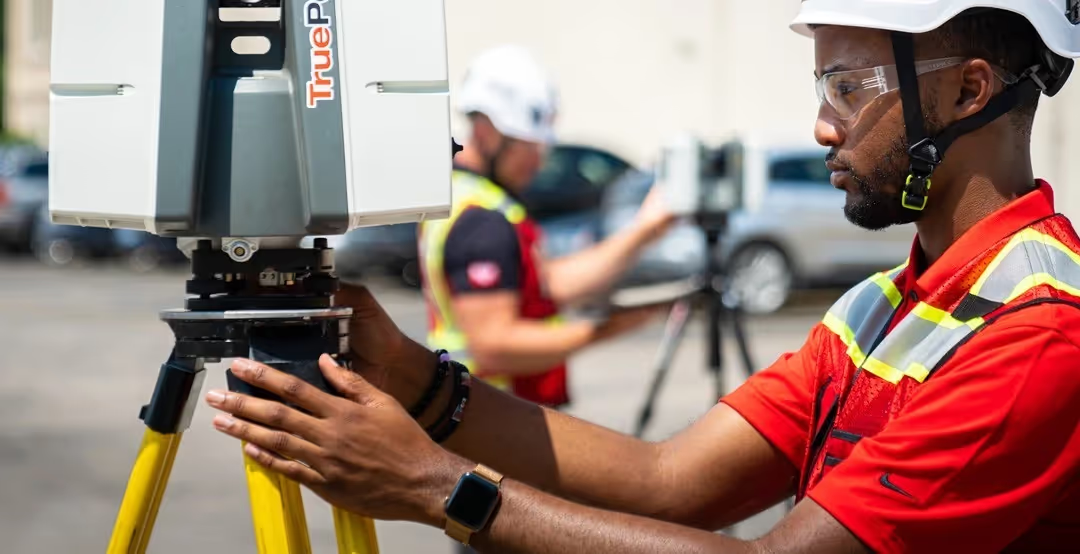
How is a 3D Building Information Model/Building Information Management Model (BIM) Created?
Once a site is 3D laser scanned, a 3D building information model (BIM) can be created from the point cloud data. A 3D BIM model provides a geometrically accurate model of a building or site, capturing spatial relationships, infrastructure and manufacturer details, property and layer information, and other pertinent aspects of the site. A 3D BIM model provides general contractors with the ability to break down building parts by elements or layers and see how they fit into a single finalized structure. General contractors can isolate walls, columns, windows, doors, etc., and plan for MEP installation.
What Benefits Can BIM Models Provide for MEP Contractors?
A BIM model can provide these benefits for MEP system installation.
Design Planning: 3D laser scan data can be used to create detailed 3D BIM models of MEP building systems, including ductwork, piping, conduit, and electrical systems. These models provide a clear visual representation of how MEP components will fit within the existing building structure.
Clash Detection: Clash detection tools within BIM software help identify conflicts between MEP systems and other building elements, enabling early resolution of clashes to prevent costly rework during installation.
Coordination: A 3D BIM model provides a digital twin that improves communication and collaboration between different disciplines involved in the construction process, including architects, structural engineers, MEP engineers, and contractors. By working within a shared BIM environment, the project team can collaborate more effectively, share information, and coordinate their efforts to ensure that MEP systems integrate seamlessly with the overall building design.
Quantity Takeoff and Cost Estimation: BIM software can generate accurate quantity takeoffs and cost estimates for MEP components based on the 3D model. This helps MEP contractors plan and budget their installations more effectively, reducing the risk of cost overruns and ensuring that materials are ordered in the appropriate quantities.
Prefabrication: BIM enables MEP engineers to design systems for prefabrication off-site. With detailed BIM models, engineers can accurately plan the fabrication of MEP components in a controlled environment, improving quality control and reducing installation time and labor costs on-site.
Construction Sequencing: BIM can be used to aid construction sequencing for MEP system installation. By visualizing the MEP installation design plan in a virtual environment, contractors can optimize their workflows, ensure workers’ safety, and identify issues before installation.
Facilities Management: BIM models can be leveraged for facilities management purposes after construction is complete. By incorporating information about MEP systems into the BIM model, facility managers can access valuable data about equipment location, and maintenance schedules, streamlining operations and maintenance activities throughout the building's lifecycle.
Finish Drawings: A 3D BIM model can provide a record of the final state of the project, documenting any changes or deviations from the original plans or specifications that occurred during the construction process. This provides a reference for building owners, facility managers, and maintenance personnel to understand the layout, configuration, and components of the completed structure. This information is valuable for ongoing maintenance, repairs, and future renovations.
3D BIM models are revolutionizing MEP system installation, adding intelligence, efficiency, and safety to project execution.
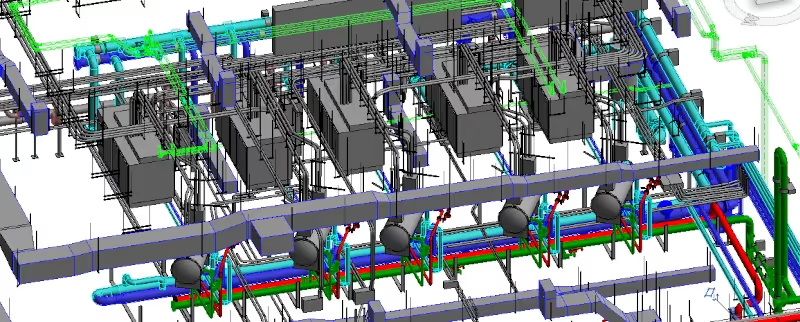
The GPRS Difference. Why Choose GPRS?
As the leading provider of 3D laser scanning and BIM modeling services, we revolutionize mechanical, electrical, and plumbing (MEP) design processes. Our laser scanning captures precise measurements of existing structures, while our BIM modeling integrates this data for accurate visualization and coordination of MEP elements. This ensures optimal spatial layouts, enhances efficiency, and minimizes errors and rework, delivering superior results for our clients' projects.
GPRS supports MEP installation projects nationwide, with extensive experience in 3D laser scanning and utility locating. Our elite Project Managers utilize Leica laser scanners, ground penetrating radar, and electromagnetic locators to gather as-built site conditions. Data is then compiled into custom utility maps, 2D CAD drawings, and 3D BIM models by our in-house Mapping and Modeling Team and delivered via SiteMap®. SiteMap® is a free cloud-based software that delivers georeferenced utility data, CAD files, BIM Models, all in one platform.
What can we help you visualize?
Frequently Asked Questions
How Long Does 3D Laser Scanning Take?
An individual scan usually takes between 1-2 minutes. The Project Manager will set up the scanner in multiple positions around the building or site. Most building scanning projects can be laser scanned in as little as a couple of hours or larger sites in a few days. Entire facilities or campuses can take several weeks to capture the entire site, but most projects are scanned in a few hours or one day.
How Much Does 3D Laser Scanning Cost?
The cost of 3D laser scanning a building or site depends on the size and complexity of what is being scanned. 3D BIM modeling costs are based on the size of the area being modeled, level of detail, and features needing to be included. 3D laser scanning can bring tremendous cost savings to a project. Quality data can lead to a faster design process and fewer change orders, ultimately saving time and money.
Is BIM Just for Large Projects?
No. Building Information Modeling (BIM) should not be restricted to large and complex projects. Comprehensive site information brings value to every project. BIM management will expedite planning, improve workflows, and increase collaboration — which means that implementing BIM laser scanning will lead to cost and time savings, regardless of the project scale and complexity.