Concrete is the second-most massively consumed material in the world behind only water.
Cement is one of the primary ingredients in concrete, and it accounts for about 7% of total greenhouse-gas (GHG) emissions – one of the largest sectoral carbon footprints on the planet.
More than 140 countries, including China, the United States, India, and the European Union, have set a target year to achieve net-zero carbon emissions, but experts say bold, immediate steps are required to reach the international community’s stated goal of achieving net zero by 2050.
So, how do you decarbonize concrete when its main ingredient has one of the largest carbon footprints of any known substance?
As you read this, industry thought leaders are seeking to answer that question. And already today, buildings are being constructed using greener concrete production methods.
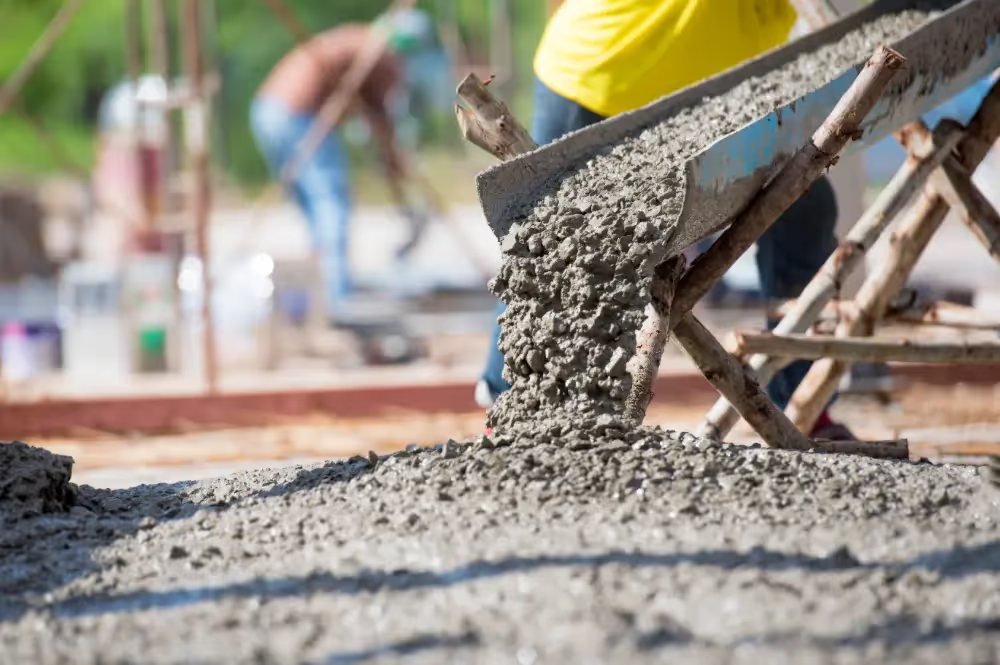
The Science Behind the Problem
Today, concrete is typically created by mixing cement and water to make a paste, then mixing that paste with aggregates such as sand, gravel, or crushed stone.
Cement – sometimes called Portland cement – is the main culprit for the global CO2 emissions attributed to concrete. Most of those emissions, however, result from the creation of the cement, rather than the concrete itself.
A primary ingredient of cement is clinker, a material created by heating limestone and silica (shale and sand) to high temperatures (around 1,400 degrees Celsius) in a kiln to cause a chemical reaction. 90% of emissions from cement making are a result of this process, and 60% of those emissions are process emissions – coming from the chemical decomposition of limestone in the kiln. The rest are a result of the combustion of fossil fuels necessary to reach the high temperatures required for the process.
According to the U.S. Office of Energy Efficiency & Renewable Energy (EERE), tackling the challenge of decarbonizing the cement industry will require research and development in the areas of next-generation cement/concrete formulations and production routes, low-carbon fuels, and carbon-capture technologies.
“Demand for cement and concrete is likely to continue to increase due to the expanding need for infrastructure construction, including to provide a strong foundation to withstand the severe weather events that are predicted due to changes in climate,” EERE wrote on its website.
Overcoming Hurdles
A recent Bloomberg Quicktake video highlighted Boston, Massachusetts-based start-up, Sublime Systems’ efforts to develop new technology to make low-carbon cement that requires no limestone and no fossil fuels.
Instead, Sublime uses an electrochemical approach that extracts calcium from minerals at ambient temperature.
“There’s a number of different, calcium-bearing minerals that we can digest and process electrochemically to make a cement powder that ultimately goes to make the same hardened concrete that we’ve been using for a millennia,” explained Sublime Systems CEO & Co-Founder, Leah Ellis. “Sublime cement is designed to be a form-fit-function replacement for Portland cement. So, it comes as a powder, just like today’s Portland cement you add water to it in the same ratios that you use today, mix it, and it has the same strength, set time, flow, and durability as today’s cement.”
Sublime still must prove their two-step cement can work at scale. And as the Bloomberg video highlights, anyone looking to decarbonize concrete and cement must figure out how to convince the infamously change-adverse construction industry to adopt a new, unproven replacement to an affordable, easy-to-obtain, and time-tested building material.
“The biggest hurdle for Sublime Systems will be the time and money needed to scale up,” Ellis said. “So, we measure our impact in the amount of cement produced and sold and replacing the carbon-intensive version that’s out there today. That is a massive undertaking... We’re going to need time to get to that scale, and then also money. The cost of cement is very important. Today’s cement is very inexpensive with an average price of around $130 a ton. We have to achieve that cost if we’re going to have that swift and massive impact.”
Other companies are exploring less drastic solutions to cement and concrete’s carbon problem.
As detailed in a May 2023 article in Architectural Record, Halifax, Nova Scotia-based CarbonCure Technologies has commercialized a process for using concrete to store CO2. Their process involves injecting waste CO2 from industrial gas suppliers into raw concrete, where it chemically bonds with cement and creates limestone, increasing the mix’s compressive strength and, as a result, reducing the total amount of cement needed.
“On average, the technique cuts CO2 by 25 pounds per cubic yard of concrete, according to CarbonCure,” the article reads. “To date, the company has licensed its technology to more than 700 customers in more than 30 countries.”
About 90% of the concrete used in Amazon’s new headquarters in Virginia, which was designed by architectural firm ZGF, incorporates CarbonCure’s process.
“Introducing waste CO2 into the mix achieves a modest reduction, but combine it with other approaches, and the benefits all add up,” Michael Cropper, a vice president at Thornton Tomasetti, the project’s structural engineer, told Architectural Record.
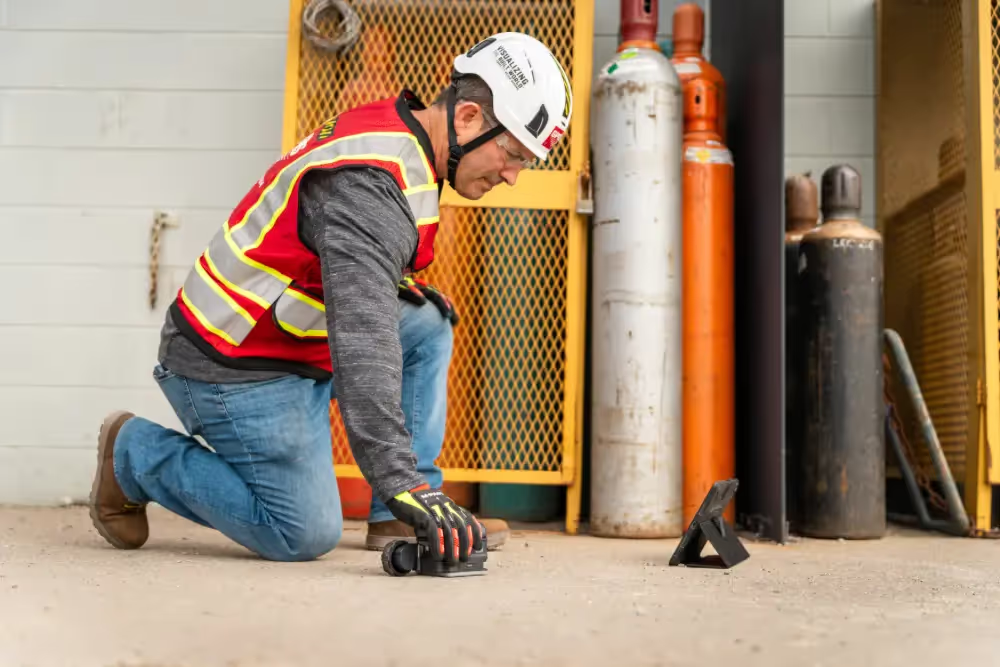
GPRS Provides Precision Concrete Scanning & Imaging
No matter how cement and concrete are produced, GPRS will be there to help prevent subsurface damage when you need to cut or core it.
Our precision concrete scanning services utilize ground penetrating radar (GPR) and electromagnetic (EM) locating technologies to provide you with a comprehensive understanding of the infrastructure embedded within your concrete slabs. We’ve achieved and maintained an industry-leading 99.8%+ accuracy rating on the over 500,000 concrete scanning and utility locating jobs that our SIM-certified Project Managers have completed since our founding in 2001. So, when you hire GPRS, you’re getting a professional concrete scanning company that you can trust to keep your projects on time, on budget, and safe.
What can we help you visualize?
Frequently Asked Questions
What are the benefits of concrete scanning?
Hiring a professional concrete scanning company like GPRS prior to cutting or coring through a concrete slab helps mitigate the risk of damaging any subsurface infrastructure when you do cut or core. This helps keep your project on time, on budget, and safe.
What is the difference between scanning an elevated concrete slab, and a concrete slab-on-grade?
Elevated concrete slab scanning involves detecting embedded electrical conduits, rebar, post tension cables, and other subsurface impediments before core drilling a hole through the slab. Performing precision concrete scanning on a concrete slab-on-grade typically involves scanning a trench line for conduits before conducting saw cutting and trenching to install a sanitary pipe, water line, or other, similar utility.
You can learn more here.