The construction industry is changing, due to 3D printing making it cheaper and faster to construct buildings and other structures.
According to Grand View Research, the North American market for 3D printed construction is projected to reach $816.8 million by 2030, with a 104.4% annual growth rate from 2025 to 2030.
According to the report, 3D printing in construction expedites the prefabrication of building components and production of infrastructure such as modular housing, advanced utility systems, and adaptable public spaces. General contractors, engineers, architects, and developers are recognizing the benefits of integrating 3D printing into their workflows. By experimenting with new design methodologies and leveraging the flexibility of 3D printing, AEC professionals are able to differentiate themselves in a competitive market.
What are the Benefits of 3D Printing in Construction?
3D printing creates three-dimensional objects, and this advanced printing method is used in many sectors around the world due to its versatility, speed of production, and ability to prototype any object. 3D printing is a construction technique that uses digital models to create objects layer by layer. It can be used to prefabricate entire buildings, components, and infrastructure. This technology offers advantages such as lower material waste, faster construction times, and the ability to produce complex architectural designs with intricate details.
3D printing has greatly increased construction productivity, reduced manual labor dependency, and offered architects greater flexibility in designing projects. It offers several benefits, including reduced material waste, faster construction times, and lower labor costs. 3D printing is used to build houses, bridges, and even commercial buildings, making construction more efficient, sustainable, and cost-effective.
What Materials are Used for 3D Printing in Construction?
3D printing in construction uses a variety of materials, including concrete, mortar, plastic, metal, and local natural materials, such as mud and even waste from rice production. The material chosen depends on the project. 3D printing in construction uses a layer-by-layer deposition of materials to prefabricate structures or components. Concrete and mortar are the most used materials for 3D construction.
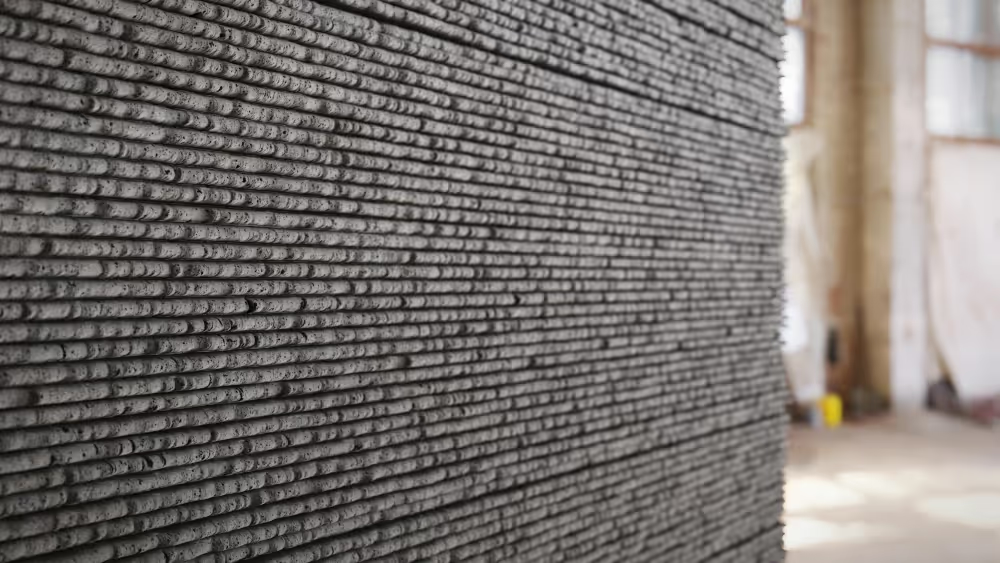
What is 3D Concrete Printing?
3D concrete printing technology uses large-scale printers to layer concrete or similar building materials to create structures. 3D concrete printing is a manufacturing approach where concrete or cement is printed using a special type of mortar that forms a monolithic structure without the use of traditional formwork. A monolithic structure is a building or object that is constructed from a single, solid piece of material. This process is guided by computer-aided design (CAD) models, allowing for precise, automated construction with minimal waste.
How does 3D Concrete Printing Work?
A 3D concrete printer can print out an object using different methods, depending on the materials and type of printer used. The nozzle in a 3D concrete printer is the most important component that dispenses the mortar used for the printing. The 3D concrete printer’s method is similar to traditional 2D inkjet printing. A layering method is used to create the object. Working from the bottom-up, the 3D printer piles on the concrete layer by layer till the object is completely built. This 3D-printed object is then checked and tested before use. Cement equipment and materials must all work together to achieve a successful print. There are numerous types of mixers, pumps, and robotics on the market.
What is the 3D Concrete Printing Process?
Design & Modeling: A digital 3D model of the structure is created using BIM (Building Information Modeling) or CAD software, such as Sketchup, TinkerCAD, or Fusion360. Complex construction components undergo simulation testing to identify and resolve potential structural issues before printing.
Slicing: Next, the 3D model is broken down into many layers with a slicing software such as Astroprint. This slicing process must take place because the 3D printer cannot conceptualize a 3D BIM model. The slicing software also tells the printer where to fill the lattices and add support columns for extra stability. After the 3D model is fully sliced, each layer of the model is scanned and the data is sent to the 3D printer.
Printer Setup: The 3D concrete printer is prepared, including loading the mortar and verifying system functionality. Calibration ensures accurate layer deposition before initiating the printing process.
Printing: A 3D concrete printer acts the same way as a traditional inkjet printer. Its nozzle moves up and down as well as back and forth to dispense the mortar. The old layer of mortar is dried before the printer continues to repeat the process on a new layer. It will essentially add thousands of layers on top of one another to create the 3D object.
Quality Inspection: The completed structure is evaluated for defects, ensuring structural integrity and adherence to design specifications before being approved for use.
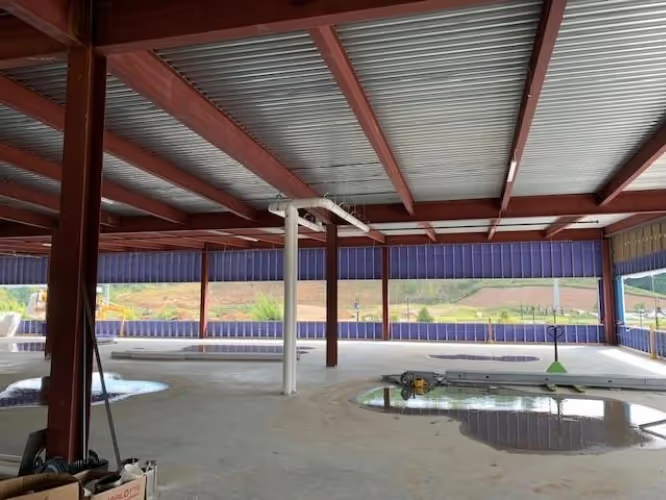
What Type of Objects Can Be 3D Printed?
The possibilities are endless when it comes to 3D concrete printing. The technology allows for the prefabrication of custom objects not feasible with traditional concrete casting methods. They can be smaller components like façade elements, architectural walls, stairs; or large-scale, fully-printed modular buildings and civil infrastructure.
Architectural Concrete Can Be Used for All Types of Structures
- Commercial Buildings: Parking garages, internal and external architectural elements, and facades
- Residential Buildings: Driveways, sidewalks, internal and external architectural elements, facades, and balconies
- Academic Buildings: Parking garages, sidewalks, internal and external architectural elements, and facades
- Transportation and Infrastructure: Roads, bridges, tunnels, and airports
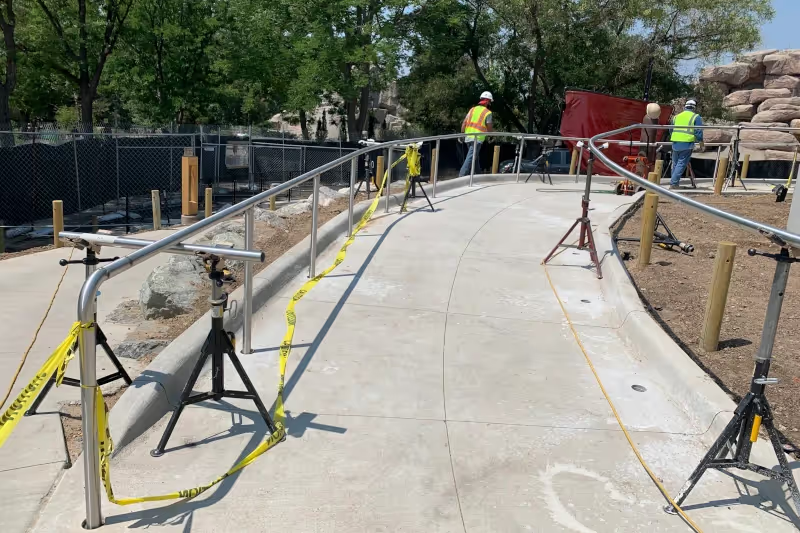
Examples of 3D Concrete Printing in Construction
Walmart Supercenter in Athens, Tennessee
Walmart partnered with Colorado-based Alquist 3D to construct an 8,000-square-foot, 20-foot-high expansion at its Athens, Tennessee retail store, marking its first large-scale use of 3D printed concrete. This addition, designed to expand online pickup and delivery space, is among the largest freestanding 3D printed commercial concrete structures in the U.S.
According to a September 10, 2024 news release, Walmart claims its decision to use 3D construction printing in this expansion aligns with its broader goals of becoming more environmentally friendly, leveraging cutting-edge technology to attract customers and accelerating the construction process.
Printed Farms Luxury Equestrian Facility in Florida
Called the world’s largest 3D-printed building, the 10,105-square foot equestrian facility was reportedly built at a cost of $3.3 million on a 5-acre property that is owned by Wendy Dixon of Nantucket Sport Horses.
According to a COBOD press release, the luxury barn, which is concrete-based and “designed to endure the extreme weather challenges of the hurricane-prone region,” is “almost 50% larger than the previous record-holder in the Middle East.”
Wapakoneta, Ohio Home
Sustainable Concrete Innovations built the state's first 3D-printed home. The home was made with a concrete mixture that makes it resistant to fires and tornadoes.
“Due to the housing shortage, home values in the Columbus area increased by an average of nearly 40 percent in 2023. Now instead of having a crew of four to six guys to build a house, two guys are printing the home," said owner John Smoll, Sustainable Concrete Innovations.
Miami Florida Seawall
Miami-based KindDesigns used a CyBe RC to print concrete seawalls that protect the shores from flooding and sea-level rise. The CyBe RC (Robot Crawler) is a mobile 3D printer that can transport to any location and maneuver over any terrain. The seawall was produced in large sections, with the crawler’s robot arm sculpting a 10-foot long segment out of concrete in just an hour.
It’s faster, less expensive and green – its a win, win, win,” said Patrick Murphy, a former Florida congressman and general contractor with Coastal Construction. “If we’re going to be serious about climate change, which is something I’m passionate about, the construction industry is a big piece of that that flies under the radar.”
3D Printing is Transforming the Construction Industry
3D printing is transforming the construction industry by offering faster, cost-effective, and sustainable building solutions. Using concrete, mortar, and other materials, 3D printing enables the efficient production of modular homes, commercial buildings, infrastructure, and architectural elements with minimal waste and labor.
Frequently Asked Questions
How can a 3D BIM model be used to create 3D printing in construction?
A 3D BIM (Building Information Modeling) model serves as the digital blueprint for 3D printing in construction, enabling precise and automated fabrication of structures. By integrating BIM with 3D printing, architects, engineers and construction professionals achieve greater accuracy, reduced material waste, and enhanced project efficiency, streamlining the entire design-to-construction workflow.
How can I do feasibility studies to compare 3D concrete printing to traditional construction methods for my project?
Costs associated with 3D concrete printing are best discussed with equipment suppliers. The cost of traditional construction methods depends on the costs of materials and labor in your geographical area. A local general contractor can possibly assist you to make the comparison.
What is concrete scanning or concrete imaging?
Concrete scanning, or concrete imaging, is used to locate rebar, post tension cables, electrical conduits, voids, and more when preparing to cut, core, or drill into a concrete structure. This process primarily involves the use of ground penetrating radar (GPR) technology. This non-destructive detection and imaging method involves sending a radio signal into a structure and reading the “bounce” that occurs when the signal encounters a material. An experienced GPR technician interprets this reading to determine the type of material located.