Processing 3D laser scan data involves several key steps to transform raw point cloud data into usable deliverables, such as 3D models or 2D drawings. A structured workflow ensures 3D laser scan data is accurate, reliable, and ready for use in planning, design, or construction.
The workflow for delivering accurate and reliable GPRS data involves a meticulous process. From on-site 3D laser scanning to the final project delivery, a coordinated team effort ensures every step aligns with client needs and expectations.
Adam Silbaugh, GPRS 3D CAD Technician, helped us understand the processing of 3D laser scan data, workflows, and methodologies utilized by the Mapping & Modeling Team to ensure accurate data registration and precise deliverables. Below, we explore key aspects of this workflow, including data registration, deliverables, and delivery methods.
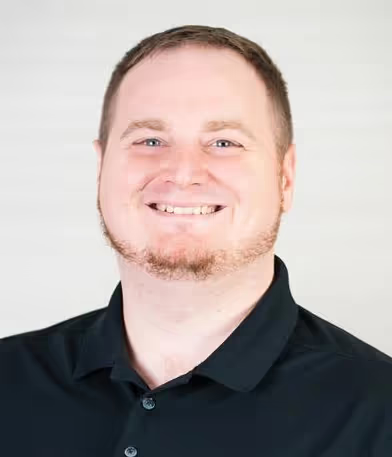
How is 3D laser scan data processed?
After 3D laser scanning a project site, the next step is to process the raw point cloud data by registering the individual scans together, cleaning up any noise, and then converting it into a usable format like a 3D model or 2D drawing. The processing of point cloud data can be for tasks ranging from simple visualization to detailed 3D modeling, depending on the project's requirements.
The GPRS processing workflow was developed with an understanding of the importance of precision, collaboration, and planning in architecture, engineering, and construction projects. By leveraging 3D laser scanning equipment and software and a well-structured team approach, GPRS ensures efficient project execution and high-quality deliverables tailored to each client’s needs.
How do we confirm pre-project planning and scope definition?
Clear and precise scope definitions are vital for a project’s success. Understanding the area to be scanned, the purpose of scanning, deliverables needed, and level of detail required ensures the delivery of successful 3D laser scanning projects that meet client expectations. Before creating deliverables, we review the project with our team.
- Sales to Execution Transition: The project scope is reviewed by the GPRS Sales and Mapping & Modeling Team. This step clarifies ambiguities and outlines site and deliverable requirements.
- Flagging Special Conditions: Specific project needs, such as higher resolution scans for reflected ceiling plans or survey control integration, are flagged early.
- Scanning Requirements: For example, distinguishing between color and grayscale scans ensures the correct mode is used on-site, avoiding the need for rescanning.
Do we need to place targets during 3D laser scanning?
Black and white targets on fixed-height tripods are often placed at control points, benchmarks, or magnails so that they can be easily identified and scanned by the laser scanner. The scanner records the locations of these targets, and software later uses this data to correct and align the scans.
Silbaugh outlined that GPRS Project Managers primarily use targetless scanners, though they deploy targets in specific scenarios:
- Survey Control: Targets are used when tying into survey control provided by the client.
- Integration of Multiple Equipment: For instance, when integrating data from the NavVis VLX with other laser scanners, targets help align multiple datasets.
Targets allow laser scan data to be aligned with survey control points or a global coordinate system and aid in registering (aligning) data from multiple 3D laser scanners accurately.
How is 3D laser scan data registered?
The registration process is a collaborative effort. Registering a 3D laser scan point cloud involves aligning multiple scans of the same area taken from different positions into a single, coherent point cloud. This typically involves using specialized software like Autodesk Recap to import the data and align the scans. The Mapping & Modeling Team uses the software to find overlapping areas between different scans where the same physical features are captured from slightly different angles, allowing the software to identify corresponding points.
Silbaugh says unwanted “noise” can be cleaned or deleted from the point cloud. Autodesk Recap software can isolate and delete extraneous data or noise, such as reflections, moving objects, or background clutter, leaving behind a refined point cloud representing the desired project area. Proper registration ensures that measurements taken from the 3D laser scans are accurate and the data can be exported for use in CAD or BIM applications like Revit or AutoCAD.
“Some clients desire only the registered point cloud. They do their own modeling, so they will ask us to scan something, register the point cloud, and deliver the data,” says Silbaugh.
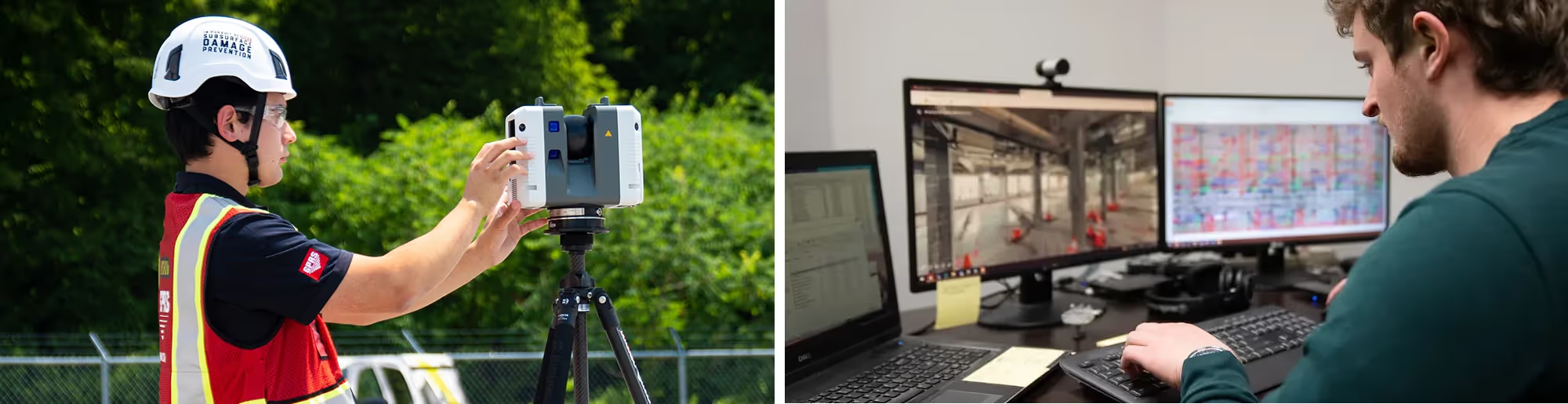
How are deliverables defined in projects?
A crucial part of any 3D laser scanning project is understanding the deliverables. Silbaugh explained that before site teams begin their work, a detailed scope of work is established.
Silbaugh emphasized the importance of understanding what the client truly needs. “Sometimes clients request a model without knowing exactly what it entails. We guide them through their options and conduct review meetings to manage expectations.” These review meetings often occur after scanning but before modeling, allowing clients to see preliminary data and refine their requirements.
During review meetings, the client's needs are translated into actionable tasks for the registration and modeling teams. For example, if a client requests a reflected ceiling plan, the team clarifies what specific details they need: beams, piping, lighting, ducts, vents, sprinkler lines, and other ceiling features. “This ensures that we’re not over-modeling or including unnecessary details, helping us tailor the deliverables and costs to the client’s exact needs,” Silbaugh noted.
The GPRS workflow contains clear task statuses to ensure the Mapping & Modeling Team can proceed without delays. Deliverables are prepared per client specifications, ensuring alignment with project goals.
Should clients utilize 2D CAD or 3D Modeling?
The question of whether to create 2D sheets directly from point clouds or rely on 3D modeling often arises. Silbaugh highlighted the advantages of 3D modeling, particularly for quality control (QC). “QC is much harder with 2D drawings because ensuring they match the point cloud data is challenging,” he said. By using a 3D model, the team can ensure accuracy and provide a foundation for other potential uses, like exporting 2D sheets or further 3D integration. However, he acknowledged exceptions for clients requiring native CAD drawings.

What software do clients utilize?
Revit and AutoCAD dominate client preferences, with Silbaugh estimating that 90–95% of clients request deliverables in these formats. ArchiCAD, though less common, poses additional complexities due to software interoperability. Silbaugh explained, “Clients using ArchiCAD often require virtual site visits because their tools may not support traditional viewing formats like TrueView.” MicroStation, Rhino, and SketchUp are sometimes requested by clients for projects. These programs are generally not the primary platforms used for processing or creating designs from 3D laser scan data. Instead, they are used as secondary tools for specific tasks, often requiring add-on software to visualize or manipulate the designs created elsewhere.
What if the client already has 3D laser scan data?
Clients typically fall into two categories: those with no as-built data and those with existing data that needs verification. According to Silbaugh, most clients start from scratch or come with inaccurate data.
“A small percentage have existing data, but often it’s unreliable. In those cases, we’re careful to avoid pointing fingers and focus on delivering accurate scans,” Silbaugh says. When clients provide existing scan data, GPRS evaluates it before use. If deemed usable, the team models from it but includes disclaimers noting the data’s unverified status to avoid liability.
Through a combination of advanced 3D laser scan technology and coordinated client-team effort, the process of delivering GPRS data has become a refined art, delivering accurate point clouds, 2D CAD drawings, and 3D BIM models for every project.
How is the data delivered?
Clients’ needs vary widely, from point clouds to intelligent 3D BIM models. Silbaugh notes that some clients handle their own modeling and only require raw scan data, while others depend on GPRS for complete solutions.
“We tailor our deliverables based on client requirements,” Silbaugh explains. “For example, smaller jobs might only require scanning, but larger projects often involve 2D plans and 3D BIM models.”
Data is efficiently transferred to clients via SiteMap®, GPRS’ digital storage software and app, Sharefile, Cloud platforms, or mailed on a hard drive. We can offer technical support to assist the client in working with the scan data, especially if it’s their first time handling point clouds or 3D models.
Deliverables often include:
- Point Cloud Data
- 2D CAD Drawings
- 3D BIM Models
- 3D Mesh Models
- TruViews
- 3D Virtual Tours
- Advanced Analysis and Calculations
What is the value of 3D laser scanning?
3D laser scanning offers immense value by providing precise, high-resolution data that enhances accuracy and efficiency across various industries. By capturing detailed spatial information in the form of point clouds, it enables architects, engineers, and construction professionals to create accurate as-built documentation, streamline design processes, and identify potential issues early in a project. This technology reduces errors, minimizes rework, and supports better decision-making, ultimately saving time and costs while improving project outcomes.
The 3D laser scanning and modeling of buildings brings excitement and value to clients, offering unparalleled insights into their projects. “Seeing their buildings digitally is a game-changer for many clients. It’s incredibly rewarding to deliver such impactful solutions.”
Through a combination of advanced 3D laser scan technology and coordinated client-team effort, the process of delivering GPRS data has become a refined art, delivering accurate point clouds, 2D CAD drawings, and 3D BIM models for every project.
Frequently Asked Questions
What is 3D laser scanning, and how does it work?
3D laser scanning is a technology that uses laser beams to capture accurate measurements of an object or space, creating a detailed digital representation called a point cloud. The scanner emits laser pulses, which bounce off surfaces, and measures the time it takes for the light to return, calculating precise distances and spatial relationships.
What are the benefits of using 3D laser scanning in construction and design?
3D laser scanning improves accuracy, saves time, and reduces costs by providing precise as-built documentation, enabling early clash detection, and supporting efficient design modifications. It also enhances collaboration by allowing teams to visualize and share models in real-time.
What types of deliverables can be generated from 3D laser scan data?
Deliverables include point clouds, 2D CAD drawings, and 3D BIM models. These outputs can be tailored to specific project needs, such as detailed floor plans, reflected ceiling plans, virtual walkthroughs, or 3D BIM models integrated into software like Revit or AutoCAD.