Sustainable, reliable food production requires agile, automated processing plants—a goal that can only be achieved by starting with accurate digital as-built data captured with laser scanning.
Mergers and acquisitions are a fundamental way to grow a business in the food processing industry. A single acquisition can double production capabilities and diversify a brand, allowing a company to be nimble and competitive. Instead of rebranding or retooling to meet changing consumer demands, a company can purchase an existing entity that has plants already equipped to meet the needs of the market.
But staying agile requires knowing exactly what is in the acquired facilities. Inaccurate, incomplete or missing design drawings hamper efforts to evaluate equipment, upgrade existing production lines, install new equipment and make other ongoing site modifications necessary to keep plants modern and efficient. Over the last several years, food processing companies had already begun turning to 3D laser scanning to quickly, accurately and safely document existing plant conditions. Today, with the need to accelerate innovation and minimize risk, laser scanning is proving to be the ideal solution.
GPRS, a Toledo, OH-based company that provides laser scanning services throughout the U.S., has scanned numerous food and beverage production facilities in addition to other power, process, and plant applications. A recent project at a food processing plant in San Antonio, Texas, illustrates the potential of laser scanning to transform the industry.
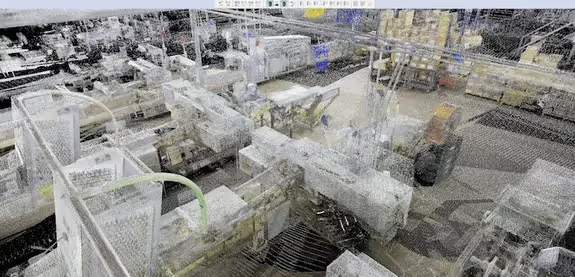
Laser Scanning Solves Plant Design Challenges
The plant was part of an acquisition that had been completed years earlier by a global operation. In an ongoing initiative to renew facilities and improve technology and infrastructure, the plant was due for upgrades to existing production lines. The service provider designing the facility upgrades was located outside of the U.S.
As is often the case in acquired plants, the existing 2D drawings were inaccurate and incomplete. Plant managers recognized that they would need new as-built data to evaluate the equipment, add electrical boxes for new equipment and design modifications to the site, but timing was a concern. The production system included a complicated network of conveyors, mechanical equipment, piping layouts (2 inches and larger), pipe supports, structural steel and platforms. A scheduled production shutdown would give them a window of just three hours to collect new data. Asking the designers to travel to the site from overseas was not a viable option.
The company contacted GPRS Texas Regional Manager David Sauceda, who assured them that he could provide an optimal solution. As a service provider with an unwavering commitment to excellence, GPRS uses industry-leading survey-grade Leica Geosystems laser scanners to capture accurate, comprehensive point cloud data. For example, the high-speed Leica RTC360 laser scanner completes a full scan in as little as 26 seconds, enabling an entire facility to be documented rapidly with a single operator working alone. The scanner captures measurements in hard to reach or hazardous locations while keeping workers out of harm’s way. Scanning is completed safely from the ground without the need for harnesses, lifts or cranes. In addition to fast scanning speed, the scan data can be registered and viewed in real-time to ensure all relevant data is captured, reducing or even eliminating return trips. The resulting point cloud can be used directly in 3D CAD software for plant design.
Because laser scanning captures all data from a distance, it can even be used while production lines are in full operation. Although engineers decided to move forward during the scheduled shutdown time on the San Antonio project, GPRS’s expertise, combined with the accuracy, speed, reliability and noncontact operation of their technology, gave them confidence that laser scanning was the right approach.
Digital Remote Management Promotes Agility
Sauceda completed the scans well within the required time frame, capturing precise dimensions of the entire multi-line production system in a comprehensive 3D colorized point cloud that was quickly delivered to the design team for use as the basis of all designs and renovations moving forward. The team will be able to use this visual, accessible, dimensionally accurate dataset to measure and plan equipment installation before they mobilize to the field work phase, which will accelerate project completion and minimize the risk of rework.
The comprehensive point cloud also provides another key benefit: With a complete digital replica of the facility, stakeholders now have remote access for easy collaboration and communication on this project as well as future operations and maintenance requirements and ongoing retrofits. With the TruView Viewer, a free browser-based viewer that doesn’t require licensing or installation, users can access ultra-high-speed renderings of point cloud data for virtual plant walkthroughs. The viewer instantly opens and displays an unlimited number of points as the user navigates the dataset, making it easy to take measurements and view panoramic imagery.
“Laser scan technology was the best solution for obtaining accurate data on this facility,” says Sauceda. “The colorized point cloud data is invaluable for designing plant upgrades. As new questions arise, designers, engineers and other stakeholders can refer to the dataset to get answers without having to visit the site.”
As food and beverage producers continue to face volatility and uncertainty, laser scanning can provide a competitive advantage.
“Accurate data empowers facility owners and vendors to make precise decisions,” said Nate Baker, Director of 3D Laser Scanning Services. “Whether building their brand through mergers and acquisitions or renovating existing plants, companies recognize that having a complete digital record of their facility is essential to maximize capacity utilization and agility. The ability to capture accurate existing conditions information quickly and safely, without affecting production, makes laser scanning an integral part of a sustainable growth strategy for the food and beverage industry.”
To find out how to transform your plant with digital data or request a consultation, contact GPRS 3D Laser Scanning Services today.
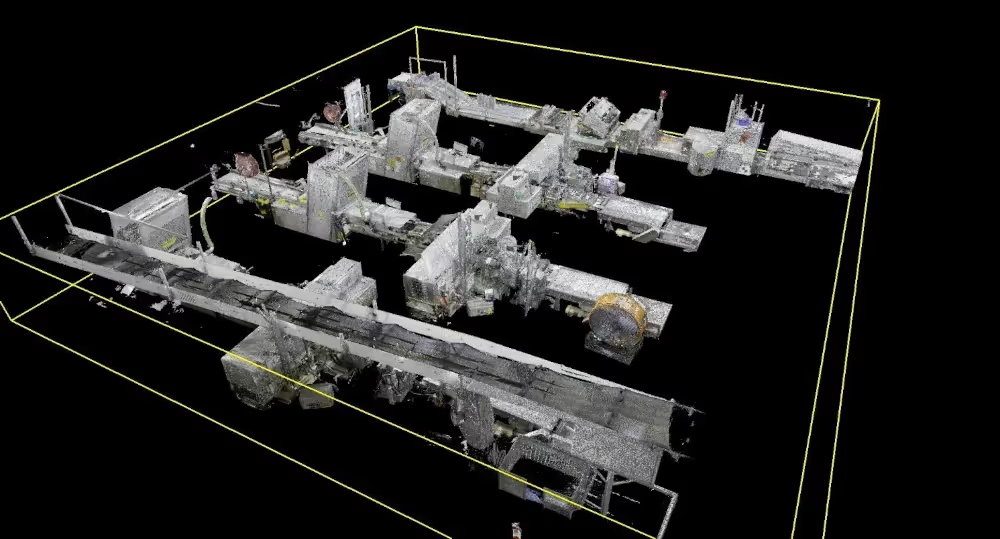
About the Author:
Bruce Bowditch has more than 35 years of experience working with 3D laser scanning. He successfully pioneered and managed a laser scanning group for an engineering firm in the 1990s and early 2000s before moving into the role of industrial plant solutions specialist for Leica Geosystems in 2005. A technology advocate and pragmatic problem solver, Bowditch is a trusted advisor to scanning service providers, EPCs and owner/operators involved in food & beverage processing, automotive manufacturing, and other industrial plant applications.
By: Bruce Bowditch, Industrial Plant Solutions Sales Manager - Eastern US at Leica Geosystems, Inc.
Thank you to Bruce Bowditch and Leica Geosystems, Inc. for allowing us to re-publish this article.
As Built Surveys | Digital Remote Management | Digital Remote Manufacturing | Digital Twin | Plant Retrofit | 3D Laser Scanning