Horizontal Directional Drilling (HDD) is a trenchless construction method used to install pipelines, cables, and other utilities underground along a predefined path.
Unlike traditional trenching methods, HDD minimizes surface disruption, making it ideal for projects where infrastructure must pass beneath rivers, railways, roads, or densely populated areas. This technique reduces environmental impact while also delivering a cost-effective solution, especially for long or complex installations.
Successful HDD projects require thoughtful engineering, balancing complex geometries, geology, risk management, and contractor expertise. Let’s explore the technology of HDD and the essential steps involved in engineering and executing these projects.
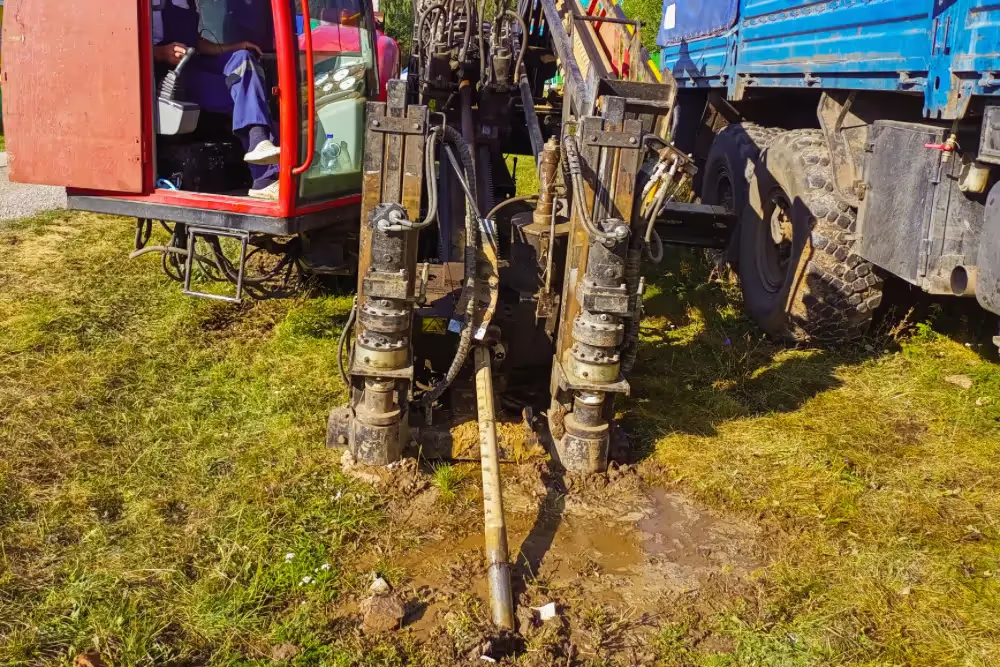
How HDD Works
The HDD process is typically divided into three primary stages:
- Pilot Hole Drilling: A pilot hole is drilled along the planned path using a steerable drill bit. During this phase, operators carefully navigate the drill head underground to follow the predetermined alignment, using guidance systems to monitor its position and orientation.
- Reaming the Borehole: Once the pilot hole is complete, the bore is enlarged to accommodate the pipe or conduit through a process called reaming. Reamers are attached to the drill string and pulled back and forth through the hole to gradually widen the bore.
- Pullback and Installation: In the final stage, the pipe or conduit is pulled through the borehole. The pipe is typically prefabricated and welded into a continuous length above ground before being installed. Bentonite drilling fluid is often used throughout the process to lubricate the borehole, remove cuttings, and stabilize the surrounding soil.
Key Engineering Considerations for HDD
Designing HDD projects involves addressing various technical, environmental, and logistical challenges. Engineers need to navigate the nuances of site conditions and project constraints while ensuring alignment with industry best practices.
- Route Selection and Design Geometry: A critical part of any HDD project is determining the alignment and geometry of the bore path. Engineers strive to avoid unnecessary complexity, such as compound curves (where horizontal and vertical bends overlap) or S-curves (opposing bends). These configurations, though sometimes necessary, can increase the pulling loads and place additional stress on the pipe. However, advancements in pilot hole locating technologies and contractor expertise have enabled engineers to execute increasingly complex paths. Compound bends, for example, are now feasible in certain scenarios, if engineers account for the reduced effective radius that occurs when horizontal and vertical curves intersect.
- Soil and Geological Conditions: A thorough geological investigation is essential for HDD planning. Different soil types—such as soft clay, sand, fractured rock, or shale—pose varying challenges. Fractured rock, for instance, can make it difficult to maintain borehole alignment due to steering difficulties. It also complicates reaming and increases the risk of bore collapse. Conversely, soft soils may require additional stabilization to prevent fluid loss.
- Risk Mitigation and Project Feasibility: HDD projects inherently carry risks, particularly in complex environments. Engineers must assess these risks through feasibility studies, balancing the project’s technical demands with the realities of the construction site. These assessments inform decisions about whether a proposed design is both achievable and advisable. One notable aspect of risk mitigation is evaluating how well the contractor’s expertise aligns with the project’s complexity. Designs that push the limits of industry practices are more likely to succeed when experienced contractors are involved early in the process.
Cross Bores
The biggest risk involved in HDD projects is the creation of cross bores: inadvertent intersections of buried utilities.
A sewer lateral compromised by a cross bore becomes a ticking time bomb. When it eventually becomes clogged and needs cleaning, the cleaning process can result in damage to the other utility line. And if that is a gas line or electrical conduit, the result can be catastrophic.
The best way to mitigate the risk of cross bores is to hire a professional private utility locating and sewer pipe inspection company to fully inspect and map any buried lines in your project area both before and after your HDD project.
Early Contractor Involvement vs. Traditional Project Delivery
The method of project delivery plays a significant role in the success of HDD installations. Early contractor involvement (ECI) allows engineers and contractors to collaborate from the design stage, ensuring that the project is tailored to the contractor's equipment and methods. This approach helps mitigate risks by aligning the design with construction realities.
In contrast, the traditional design-bid-build model limits contractor input during the design phase. This forces engineers to make conservative assumptions about contractor capabilities, potentially restricting the use of innovative designs. Although the conservative approach reduces immediate risk, it may also eliminate viable options for more efficient or cost-effective installations.
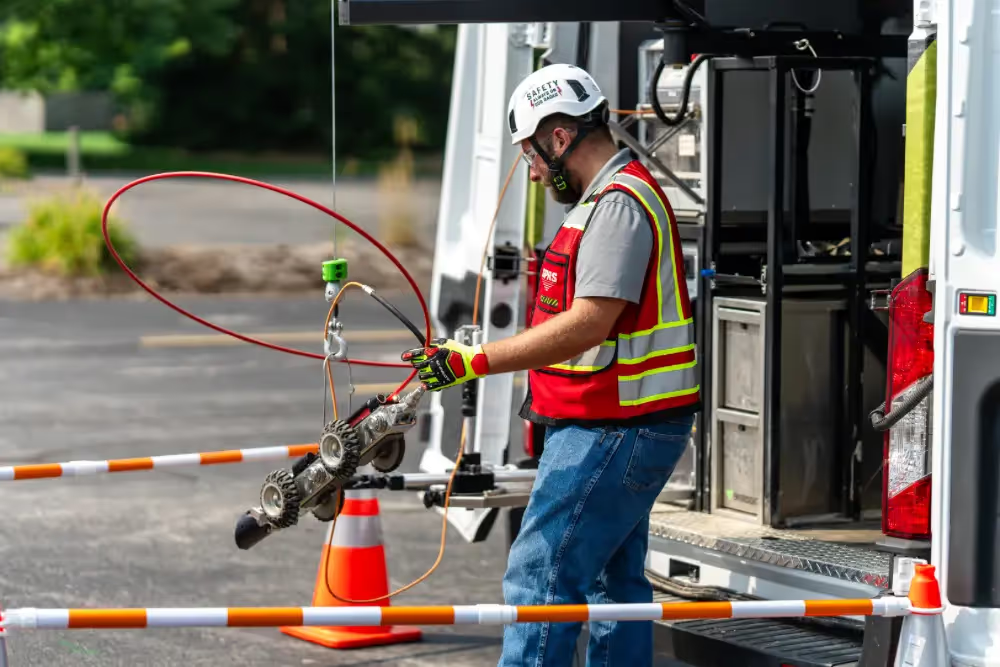
GPRS Utility Locating, Video Pipe Inspection Services Ensure Safe HDD Projects
Horizontal Directional Drilling (HDD) represents a powerful tool for installing infrastructure with minimal surface disruption. However, the success of an HDD project depends on the ability to balance innovation with risk management.
GPRS provides 99.8%+ accurate utility locating, and NASSCO-certified video inspection services to ensure the safety and success of your HDD projects.
Utilizing ground penetrating radar (GPR) and electromagnetic locating, we accurately locate and map the buried utilities in your project area. And our remote-controlled sewer inspection rover and push-fed sewer scopes can inspect the integrity of your buried sewer lines to ensure there are no pre-existing problems, such as cross bores, and inspect them again after your project has completed to ensure no new problems were created because of the work.
All this accurate, complete infrastructure data is available 24/7 thanks to SiteMap® (patent pending), GPRS’ facility & project management application that provides accurate existing conditions documentation to protect your assets and people.
From sewer lines to skyscrapers, GPRS Intelligently Visualizes The Built World® to keep your projects on time, on budget, and safe.
What can we help you visualize?
Frequently Asked Questions
What size pipes can GPRS inspect?
Our NASSCO-certified Video Pipe Inspection (VPI) Project Managers can inspect pipes from 2” in diameter and up.
What deliverables does GPRS offer when conducting a VPI?
GPRS is proud to offer WinCan reporting to our Video Pipe Inspection clients. Maintaining sewers starts with understanding sewer condition, and WinCan allows GPRS Project Managers to collect detailed, NASSCO-compliant inspection data. GPRS Project Managers not only inspect the interior condition of sewer pipes, laterals, and manholes – they can also provide a map of their location. The GPRS Mapping & Modeling Department can provide detailed GPS overlays and CAD files. Our detailed WinCan/NASSCO reports contain screenshots of the interior condition of the pipe segments that we inspect, as well as a video file for further evaluation, documentation, and/or reference.