Concrete cutting and coring are integral operations in the construction industry, enabling modifications and installations within existing structures.
But these tasks come with inherent risks that necessitate a comprehensive safety strategy to protect workers and maintain project integrity.
Emphasizing hazard identification and protective measures and adhering to industry-best practices will help you reduce the safety risks of cutting or coring concrete.
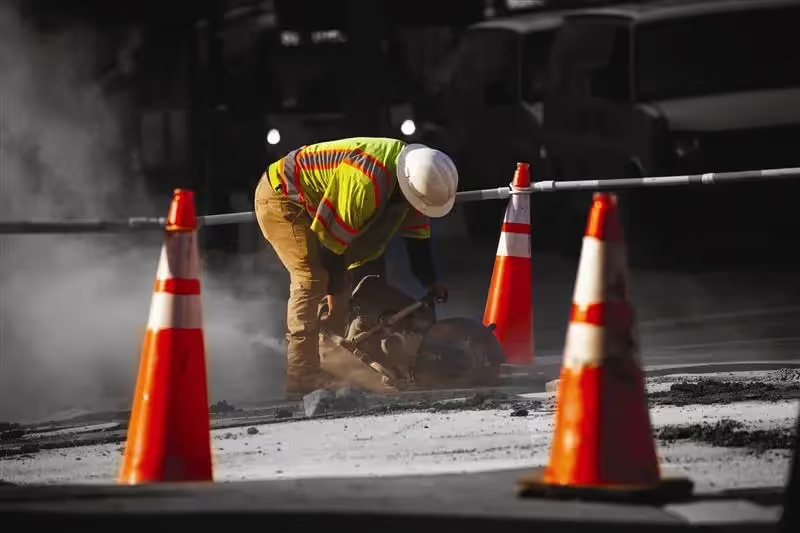
Understanding the Risks
Before implementing safety protocols, it's crucial to recognize the specific hazards associated with concrete cutting and coring:
- Silica Dust Exposure: Cutting or drilling concrete releases respirable crystalline silica, which can lead to silicosis, lung cancer, and other respiratory diseases. The Occupational Safety and Health Administration (OSHA) mandates a permissible exposure limit (PEL) of 50 micrograms per cubic meter of air over an 8-hour shift.
- Equipment-Related Injuries: The use of powerful tools like saws and drills can result in cuts, lacerations, or amputations if not handled properly.
- Electrical Hazards: Accidentally cutting into live electrical conduits embedded within concrete can cause electrocution or severe burns.
- Structural Damage: Interfering with structural elements embedded within a concrete slab, like rebar or post tension cables (PT cables) can compromise the integrity of a building, leading to potential collapse or costly repairs.
- Noise-Induced Hearing Loss (NIHL): Prolonged exposure to high-decibel noise from cutting equipment can lead to permanent hearing damage.
Implementing a Safer Strategy
To address these hazards effectively, consider the following components in your safety strategy:
1. Comprehensive Hazard Assessment
- Site Evaluation: Conduct thorough assessments to identify potential hazards such as embedded utilities, structural reinforcements, and environmental factors that may affect safety.
- Utility Location: Hire a professional concrete scanning company that utilizes ground penetrating radar (GPR) scanning to detect hidden utilities and structural elements within concrete structures before commencing work.
2. Engineering Controls
- Dust Suppression: Implement wet cutting techniques and local exhaust ventilation systems to minimize airborne silica dust. These methods help maintain air quality and reduce respiratory risks.
- Noise Control: Utilize equipment designed to operate at lower noise levels and establish barriers or enclosures to contain noise, protecting workers from NIHL.
3. Administrative Controls
- Training Programs: Provide comprehensive training on equipment operation, hazard recognition, and emergency response procedures. Regular refresher courses ensure that workers remain informed about the latest safety practices.
- Work Scheduling: Plan tasks to limit exposure to hazardous conditions, such as scheduling cutting activities during times when fewer workers are present to reduce potential exposure.
4. Personal Protective Equipment (PPE)
- Respiratory Protection: Equip workers with N95 respirators or higher-grade masks to protect against silica dust inhalation.
- Hearing Protection: Provide earplugs or earmuffs to safeguard against excessive noise levels.
- Eye and Face Protection: Use safety goggles or face shields to prevent injuries from flying debris.
- Hand and Foot Protection: Ensure the use of heavy-duty gloves and steel-toed boots to protect against cuts, lacerations, and falling objects.
5. Emergency Preparedness
- First Aid Availability: Maintain accessible first aid kits on-site, equipped to handle injuries specific to concrete cutting and coring activities.
- Emergency Response Plans: Develop and communicate clear procedures for responding to incidents, including evacuation routes and emergency contact information.
6. Regular Equipment Maintenance
- Routine Inspections: Schedule regular checks of all equipment to identify and address wear and tear, ensuring tools are in optimal working condition.
- Proper Storage: Store equipment in conditions that prevent damage and exposure to harmful elements, prolonging their lifespan and reliability.
Promoting a Culture of Safety
Beyond implementing these measures, fostering a culture that prioritizes safety is essential:
- Safety Meetings: Conduct regular discussions to review safety protocols, share experiences, and address concerns. Engaging workers in these conversations reinforces the importance of safety.
- Access to Information: Provide easy access to safety guidelines, equipment manuals, and emergency procedures, ensuring that all workers are informed and prepared.
- Encourage Reporting: Create an environment where workers feel comfortable reporting hazards or unsafe practices without fear of retribution, enabling proactive hazard mitigation.
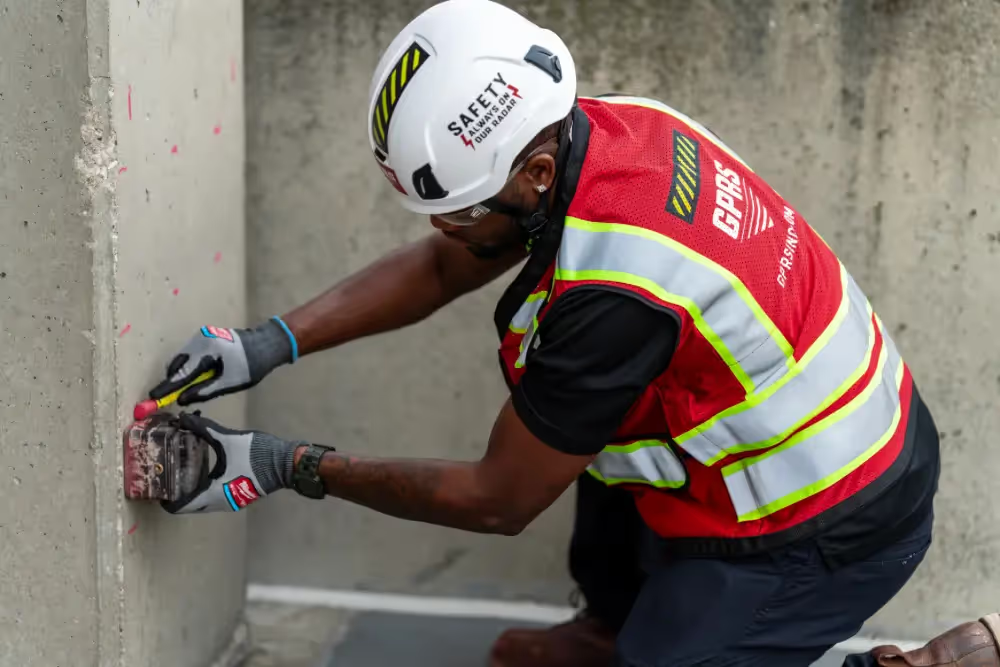
How GPRS Helps Ensure Safe Cutting & Coring Projects
At GPRS, safety is always on our radar. That’s why we offer precision concrete scanning services designed to protect your team from the costly and potentially dangerous consequences of damaging electrical conduit, post tension cable, or rebar embedded within concrete slabs.
Our SIM-certified Project Managers use ground penetrating radar (GPR) scanners to visualize what you can’t see within the concrete, so you know where you can and can’t safely cut or core that slab.
We have an industry-leading 99.8% rate of accuracy when conducting concrete imaging. We’re so confident in our results that we introduced the Green Box Guarantee, which states that when a GPRS Project Manager places a Green Box within a concrete scanning layout prior to you cutting or coring that slab, we guarantee that the area within that box will be free of obstructions.
If we’re wrong, we agree to pay the cost of the damage.
At GPRS, we’re committed to Intelligently Visualizing The Built World® to keep your projects on time, on budget, and safe.
What can we help you visualize?
Frequently Asked Questions
How is ground penetrating radar used to identify tendons vs. rebar in a post-tensioned slab?
In post-tensioned structures, GPRS typically finds one mat of support rebar near the base of the slab.
This mat is generally consistently spaced and remains at a constant elevation. Post tension cables are generally found above this support mat and “draped” throughout the rest of the structure. The elevation of the cable is usually high near the beams and column lines and drapes lower through the span between beams and column lines. Knowledge of these structural differences allows us to accurately differentiate between components.
Our Project Managers will leave you feeling confident in our findings and in your ability to drill or cut without issue.
Can GPR determine the difference between rebar and electrical conduit?
Ground penetrating radar (GPR) can accurately differentiate between rebar and electrical conduit in most cases. We have an extremely high success rate in identifying electrical lines in supported slabs or slabs-on-grade before saw cutting or core drilling.
Additionally, GPRS can use electromagnetic (EM) locators to determine the location of conduits in the concrete. If we can transmit a signal onto the metal conduit, we can locate it with pinpoint accuracy. We can also find the conduit passively if a live electrical current runs through it.
The combined use of GPR and EM locating allows us to provide one of the most comprehensive and accurate conduits locating services available.