More than 200 designers, architects, and engineers came together in Chicago, Illinois May 1-2, 2024, for the LCI Lean In Design Forum, to explore how design can benefit from Lean thinking and practices. The main goal of Lean management is to improve efficiency and effectiveness by reducing the time spent on non-value-added activities to optimize workflows.
Total Lean Management is a process developed by Toyota which aims to reduce waste in all areas of an organization. A model was developed from this process to help organizations identify the key “pain points” in their operation and work to eliminate waste in all areas – not just manufacturing.
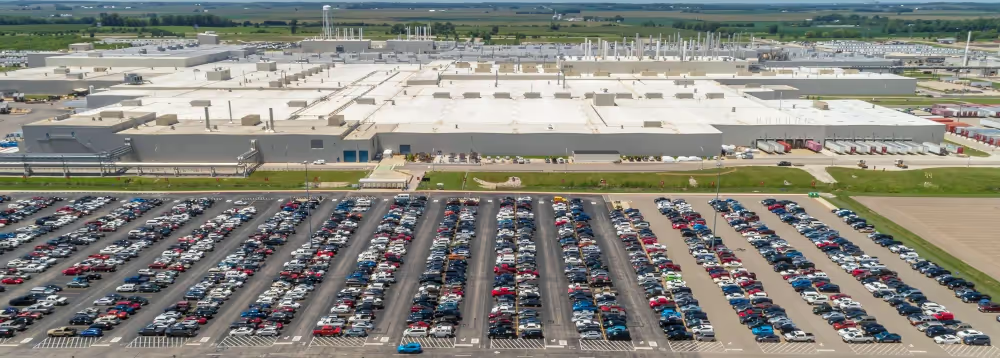
How Does a Unified Team Help Lean Construction Practices?
Matt Mikolajczyk, GPRS’ Market Segment Leader for SiteMap®, attended the LCI Design Forum for GPRS. He shared that, “The vast majority of construction projects utilize design-bid-build mentality, which separates the various parties of a project into smaller, separate projects. Lean is a way of thinking and managing the processes that is different. The focus is to create an efficient design by working closely together as a team through the entire conception, design, fabrication, and construction process.”
Lean construction practices align the owner, design team, and construction team (as well as any additional contractors) into a unified team, where every party becomes contractually involved in each step of the design and construction process. The entire team will be in a “Big Room” during the design stage and the designers will remain involved throughout the project’s construction.
During the forum discussions, the “Big Room” idea was tested, where major design, construction, and owners were co-located in the same room to work together through increased communication and collaboration. They prioritized value generation, continuous improvement, and optimizing workflows, with an emphasis on respect for all parties involved on the team.
Mikolajczyk said, “I certainly noticed the respect for all parties in attendance as everyone I met was happy to talk with me and open up about what Lean means to them.”
The Lean design examples presented were almost “common sense” to Mikolajczyk, adding value to the design in the most efficient and effective way possible.
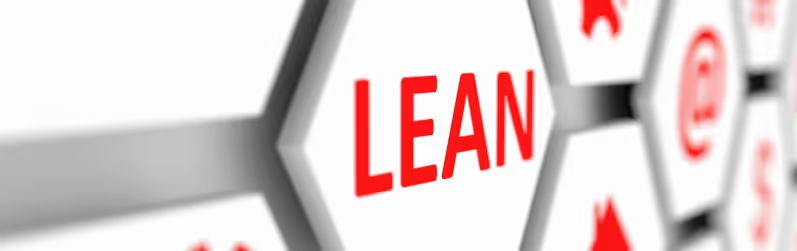
Lean and Target Value Delivery Management Practice
Mikolajczyk also participated in a session on Lean and Target Value Delivery. Target Value Delivery (TVD) is a management practice used throughout all phases of design and construction to deliver projects within a fixed budget, while meeting the operational needs and values of the client.
The steps involved planning and validating a business case before forming a team, organizing the “Big Room,” and finally beginning the constant and iterative process of project planning, cost modeling, cost estimating, and conceptual design.
Mikolajczyk said, “The heavy work and focus is up front prior to getting to production design and construction.”
During the TVD session, participants first had to design and construct a “tower” using traditional design methodology. There was no communication allowed at the table, except through written RFIs. Much of the information was lost in translation. The cost of materials was unknown. Stress was placed on the design team to complete the design quickly, and the construction team to build quickly.
“At the end of the day, we constructed a tower, but everyone was stressed, and the tower was very expensive to build.”
The exercise was then repeated using the “Big Room” approach. Historical costs were known, and everyone was part of the design thinking (owner, designer, and contractor). The tower was designed together, and the team was always involved and moving forward. “The design was much less expensive, and everyone had fun doing it,” said Mikolajczyk.
“I was very impressed with how Lean construction practices were able to streamline so many processes, yet it wouldn’t have worked so well without a team working closely together in complete alignment.”
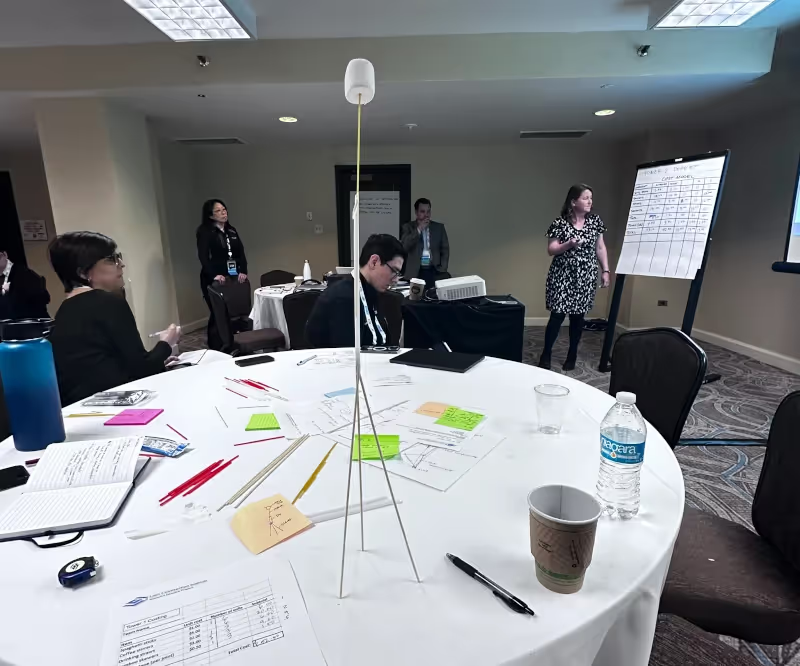
How Can GPRS Add Value to Lean Design?
So, what were Mikolajczyk’s key learnings for GPRS?
“My main goal of attending the LCI Design Forum was to learn how GPRS can help our clients meet their target value delivery goals. GPRS is not a member of the design team, nor are we present in the ‘Big Room.’ We can add value to all members of the team by providing accurate as-built data up front on both brown and greenfield sites.”
GPRS delivers a comprehensive array of services for subsurface damage prevention, existing conditions documentation, and management of construction and facility projects.
We provide utility locating, concrete scanning, video pipe inspection, and leak detection services to help prevent subsurface damage during excavation, or when drilling or coring through concrete. Our Project Managers utilize cutting-edge tools like ground penetrating radar (GPR), electromagnetic (EM) locating, and remote-operated sewer pipe inspection rovers to deliver detailed information of a site’s subsurface infrastructure.
3D laser scanning and 3D photogrammetry services utilize LiDAR technology to capture millions of three-dimensional data points of a space. Each data point is converted into a pixel with an X,Y,Z coordinate. Millions of data points are captured and processed, creating an accurate 3D as-built data set of the site. Data is then compiled into custom utility maps, 2D CAD drawings, 3D BIM models, 3D meshes, 3D virtual tours, digital twins, floor plans, and more by our in-house Mapping and Modeling Team. All data, drawings, maps, and models are delivered digitally via SiteMap®, GPRS’ free cloud-based software.
GPRS Delivers Accurate As-Builts Prior to Design and Construction
Many times, GPRS is called to a project site after the design is completed, right before breaking ground.
It is typically the contractor’s responsibility to verify that existing plans and utility locations are accurately shown on the design plans. They are also typically responsible for repairing all damages that occur during construction.
Many building professionals can benefit from Lean construction practices:
- Architects, engineers, and designers
- Owners, owners’ reps, and general contractors
- Trade partners engaged in Design/Build and Design/Assist
- Preconstruction managers
- Design managers
- Estimators
- BIM/VDC managers
GPRS can provide all architectural, structural, and MEP system layout and dimensions, plus utility and concrete markings prior to design and construction.
“We help project teams verify that all discoverable utilities have been found, gravity sewers have had CCTV records pre and post construction, leaks in fire suppression and other water systems are discovered, concrete embedment and thicknesses are identified, and that all as-built conditions are documented so that accurate 2D plans and 3D models can be created. We can also help the construction team verify that a design is constructable and safe to proceed,” said Mikolajczyk.
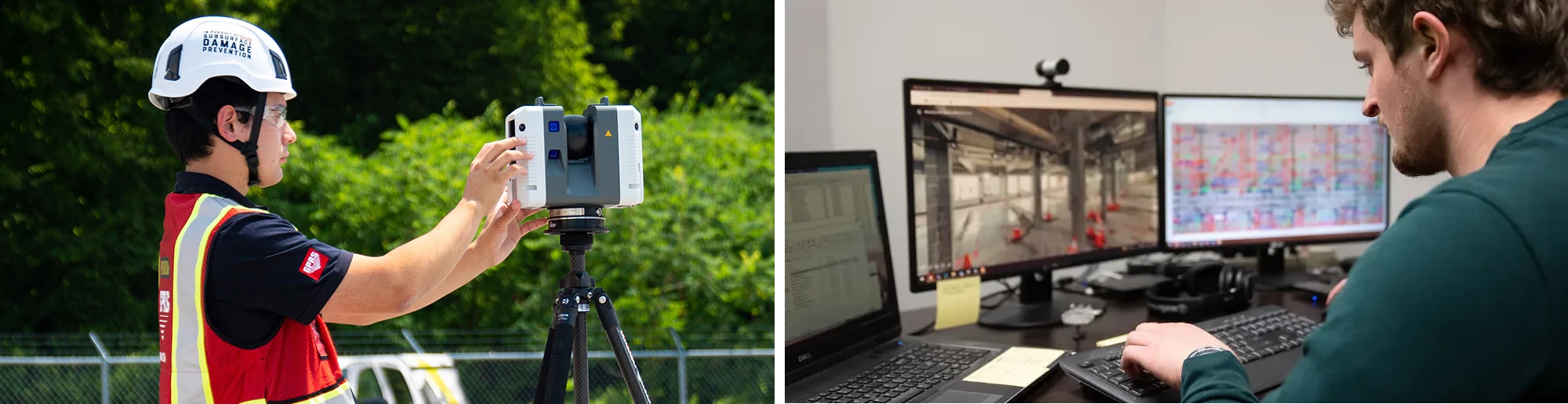
Who Can Benefit From Lean Construction Practices?
GPRS can add value, save time, and minimize risk for teams who are working off bad data. As-built data collected after design planning can lead to delays, damages, and redesigns that can be costly.
“So many times, we have seen that creating a true as-built of the existing above and below infrastructure upfront through our locating, scanning, and modeling services has helped teams be more successful and reduce the unknown on projects,” said Mikolajczyk.
“We have helped project sites stay safe by keeping updated and centralized subsurface as-built records of utility lines as they go in the ground using our CAD team and SiteMap® platform. We can provide exact dimensions, locations, and layout of a building, facility, or site, including walls, doors, windows, rooms, architectural and structural features, and more to allow team members to collaborate with comprehensive site data. This takes the burden off the contractor to develop their own as-builts at the start or end of a project.”
GPRS can help design teams start off on the right foot with accurate as-built data and also help maintain a single source of truth throughout the life of a project with our SiteMap® platform, as well as our mapping and modeling services.
Any step toward Lean thinking to eliminate waste, increase communication, and streamline processes will certainly help projects be completed on time, under budget, safe, and help maintain the reputation of all parties involved.
This is in complete alignment of the value proposition of GPRS and SiteMap®.
What can we help you visualize?
Frequently Asked Questions
How does lean construction work?
Lean construction is a project delivery process that uses Lean methods of maximizing stakeholder value while reducing waste by emphasizing collaboration between teams on a project. The goal of Lean construction is to increase productivity, profits, and innovation in the industry.
What is SiteMap®?
SiteMap® is an all-inclusive, cloud-based facility, construction & infrastructure management software that uses the data collected on-site by GPRS’ Project Managers to create up-to-date as-built drawings, 3D models, virtual walk-throughs, and comprehensive, layered utility maps. It can also house historical infrastructure data for construction sites, facilities, campuses, or a company’s distributed assets.
What is Target Value Delivery?
Target value delivery focuses on prioritizing customer value instead of cost, eliminating many inefficiencies that come with a siloed approach. It starts with understanding what’s most valuable to the owner and the project’s constraints. Target value delivery essentially flips the traditional design and delivery process upside down—instead of the design determining the cost, the project’s scope informs the budget, which, in turn, determines the design.