What is Survey Control in 3D Laser Scanning?
Survey control in 3D laser scanning is the use of accurately positioned reference points, marked with reference targets, positioning targets, or scanning targets to ensure that the LiDAR scanned data aligns precisely within a spatial coordinate system. These control points are determined using traditional surveying techniques, for example GPS or total stations, and serve as fixed anchors for aligning, registering, and geo-referencing the 3D laser scans across large or complex areas. Tying the laser scan data to these known survey control points improves the accuracy and consistency of the 3D BIM models and 2D CAD drawings required for the project.
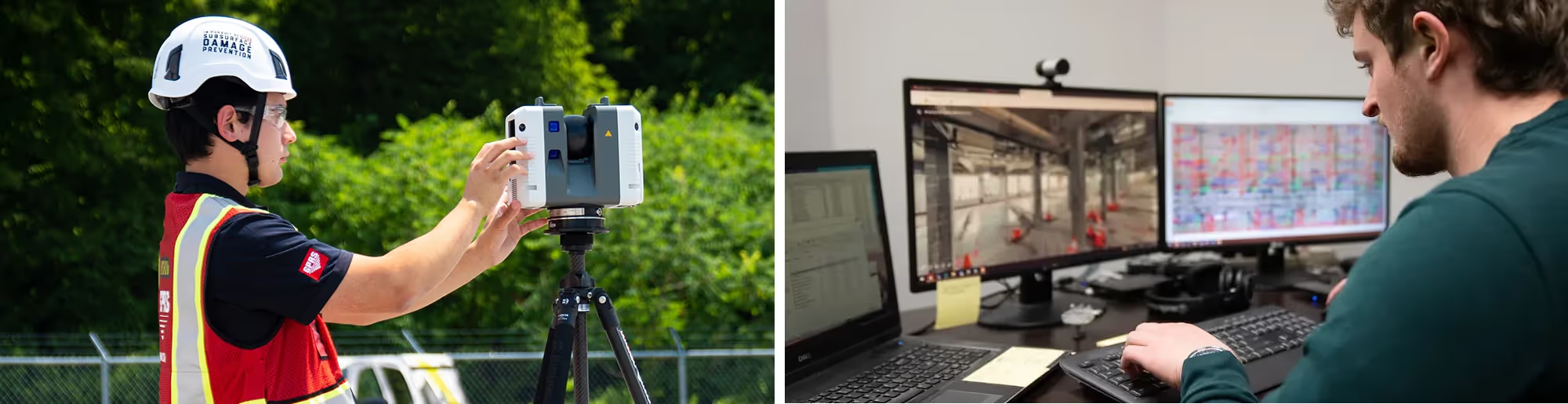
Why is Survey Control Important?
Survey control in 3D laser scanning is the foundational framework that provides accurate, real-world context to the laser scan data, ensuring that the final 3D models and measurements are both precise and reliable. Given the crucial role of surveying control points in the construction process of some jobs, any inaccuracies can lead to costly mistakes and project delays.
Why is Survey Control Important in 3D BIM Models?
Without control points, BIM data can’t be matched accurately to the physical site. Survey control is essential in 3D BIM models because it provides the exact location and orientation of the virtual model, ensuring the digital design aligns perfectly with the real site. This prevents costly construction errors, keeps everything correctly positioned, and allows for smooth coordination between design teams within the BIM model.
What Are the Key Requirements of Survey Control in 3D Laser Scanning?
Establish Control Points:
These are physical markers or targets placed at known, pre-measured locations in the survey area. The positions of these points are typically determined using traditional surveying techniques such as GPS or total stations. The laser scanner references these points to accurately locate itself within the environment.
Define Coordinate Systems:
Survey control defines the coordinate system in which the laser scan data will be placed. This could be a global system (such as geographic coordinates) or a local system (site-specific grid). Control points help tie the laser scan spatial data set to this system so that it aligns with 2D CAD drawings, 3D BIM models, and other deliverables.
Place Targets:
Black and white targets on fixed-height tripods are often placed at control points, benchmarks, or magnails so that they can be easily identified and scanned by the laser scanner. The scanner records the locations of these targets, and software later uses this data to correct and align the scans.
Pro Tip: You will need at least three reference points (we like to use five) on each project to enable accurate registration. Select locations that aren’t likely to move, because that could negatively impact the coordinate system. Place the fixed height tripods around the scan area to best tie in benchmark locations to the point cloud.
Establish Global and Local Control:
Depending on the project’s needs, survey control can be on a global scale. Global Navigation Satellite Systems (GNSS) and Real-Time Kinematic (RTK) systems offer satellite-based positioning systems that provide real time, highly accurate coordinates, enabling surveyors to determine control points and carry out other surveying tasks with precision. Global control points help ensure accurate alignment across multiple scans and projects.
Register and Align the Point Cloud Data:
After scanning, the raw point cloud data is registered to the control points. This process, called "registration," aligns the scan data with the real-world coordinate system. The use of control points ensures that the different scans fit together precisely and are geographically accurate.
Quality Assurance:
Control points act as benchmarks that can be checked to validate the accuracy of the laser scan. By comparing the scanned coordinates of these points against their known positions, surveyors can assess the accuracy of the laser scanning process and correct any misalignments or deviations.
What are the Benefits of Using Survey Control in 3D Laser Scanning?
Survey control is critical in laser scanning because it ensures the accuracy, precision, and reliability of the data collected.
Here are the benefits of using survey control in 3D laser scanning.
Accurate 3D Model:
Survey control points provide precise, fixed references, minimizing alignment errors and improving the overall accuracy of the 3D model.
Alignment Across Large Projects:
In large projects where multiple scans are needed from different locations or at different times, survey control ensures that each scan is correctly aligned with others.
Improved Georeferencing:
Survey control points allow laser scan data to be accurately tied to a specific geographic coordinate system. This ensures that the scanned data can be integrated with other spatial datasets or design models, such as CAD, GIS, and BIM.
Saves Time:
By eliminating the need for repeated adjustments, survey control saves time, especially in projects requiring extensive scans or data from various sources.
Better Collaboration:
Consistently aligned, geo-referenced data makes it easier for teams to collaborate, share, and integrate data across different platforms and phases of a project.
Are There Instances When Establishing Survey Control Points Is Not Necessary?
For smaller scale projects, manually aligning the point cloud with the BIM model or CAD drawing can be an alternative to using control points. This is often the case with residential buildings or interior fit outs, which are less complex than commercial and industrial projects.
Surveying control points may not be required if a client is comparing dimensions within the point cloud. For example, when verifying door or window measurements, clients can measure the openings directly from the point cloud and compare them to the design drawings. The focus on the specific elements captured within the point cloud does not need a tie to survey control.
Also, establishing survey control may not be necessary during the initial stages of a project, when the focus is on understanding the overall layout and conditions of the site, rather than capturing precise measurements.
Pro Tip: If a client has an existing topographical survey, GPRS can tie into that using the control points set by the surveyor.
Why Choose GPRS 3D Laser Scanning Services?
When required on a jobsite, we establish survey control to deliver a the highest degree of 3D Laser Scan and Scan-to-BIM accuracy to our clients. Our Project Managers incorporate control points into the 3D laser scanning process, allowing the surveyed conditions to be accurately aligned with design BIM models or computer aided design (CAD) drawings. This helps to streamline project coordination for architects, engineers, design teams, general contractors and everyone involved with the construction project.
GPRS’s experience in LiDAR scanning, use of survey-grade lasers, and dedication to providing accurate data have made us the leading provider of 3D laser scanning services for the architecture, engineering and construction industries. With a dedicated GPRS team, quick and accurate scanning, and detailed deliverables, our clients can trust that their sites are properly documented and modeled.
To request a quote from GPRS contact us here.