A historic “factory boom” is driving economic growth across the U.S. However, an increased construction pace requires increased risk mitigation for general contractors.
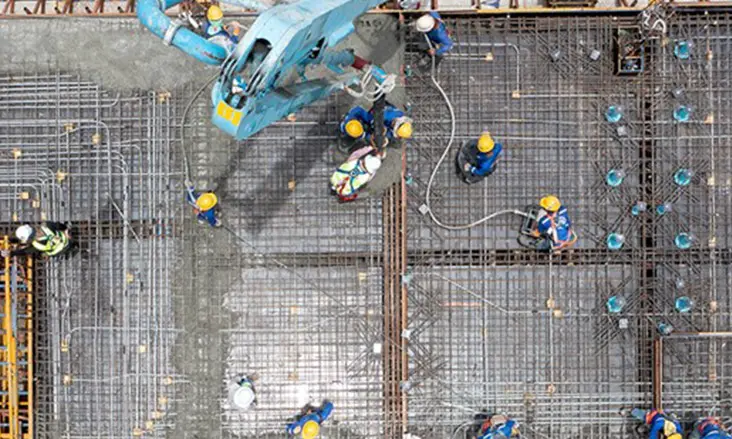
Since the passage of the CHIPS Act in August of 2022, manufacturing construction has seen more than 100 multi-million and multi-billion-dollar projects announced throughout the U.S.
Construction Dive has created an interactive map tracking the largest manufacturing construction jobs in the country. You can view it here.
The cash infusion provided by $52 billion in CHIPS funding, paired with some $628 billion in private investments, is fueling the speediest factory and manufacturing sector build-out in decades.
According to the U.S. Census Bureau, as reported by Yahoo News, you have to go back to 1993 to find such a significant increase in manufacturing in the construction sector. Further, data shows that manufacturing jobs rose to 406,000 newly “reshored” jobs (jobs that are returning to the U.S. from overseas) in 2023 – which is more than four times the last reported rate in 2019.
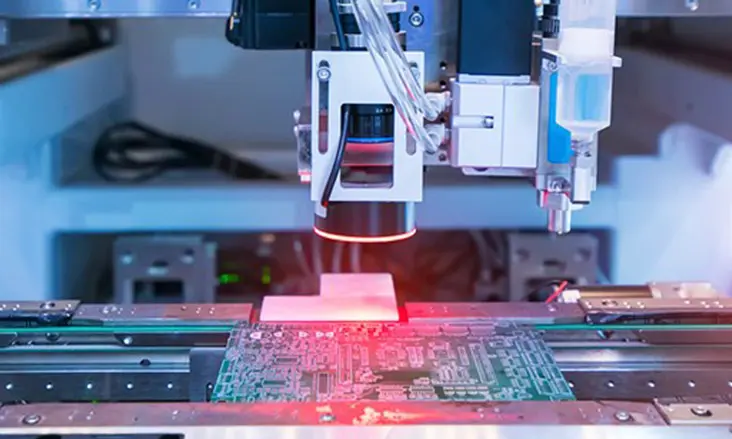
the factory boom.
Everywhere you look in manufacturing, the outlook is one of strong growth; infrastructure development, green energy, and semiconductors are just a few of the sectors leading the way.
Why Does Expanded Manufacturing Present a Risk for General Contractors?
When construction spending in manufacturing increases by 71% as it did in 2022-23, that means a lot of companies are pushing to build immediately to be among the first to market with their goods.
When everyone everywhere wants their job to be your company’s number one priority, the pressure to deliver can lead to cut corners, skipped steps, and the kinds of mistakes that can set projects back millions of dollars, months of waiting, and can lead to severe injuries and death.
In 2022, well before the manufacturing spending boom in construction had filtered to individual projects, excavation accidents and trenching-related deaths were rising quickly enough for OSHA to issue enhanced enforcement guidelines that included urging states to criminally charge parties who flout trench safety regulations.
Recent data from the Common Ground Alliance shows a disturbing trend: utility strike damages caused by excavation have increased every year for the last three years. There are now more than two reported excavation utility strikes every minute in the United States.
The damages from these accidents range from service interruptions to water contamination, electrocutions, and in some cases, death…
In addition to subsurface damages and trenching safety issues, the cost overruns and delays that can be caused by inaccurate measurements for off-site prefabrication, or relying on outdated as builts and structural drawings can stop a jobsite in its tracks.
For example, severing a single post-tension cable buried in concrete can require $20,000- $30,000 to repair/replace and can impact the structural integrity of a building.
And designing expansions or new construction without taking into account the existing subsurface infrastructure can increase the cost of a project by as much as 40%.
Mitigating Risk From The Ground Up For Your Team’s Safety
There are some simple and cost-effective steps that general contractors, subcontractors, and stakeholders can take to mitigate safety and material risk on jobsites. The cost to implement these measures is often less than 2% of an entire project budget and could achieve a cost savings of 9%-40%.
- Update & implement a Ground Disturbance Policy that requires the use of Subsurface Investigation Methodology to greatly reduce or eliminate excavation-caused utility strikes.
Subsurface Investigation Methodology, otherwise known as SIM, is the gold standard in certification for utility locating and concrete scanning. It requires 10 times the training and field work of an NDT Level 1 certification and is why GPRS Project Managers have consistently maintained a 99.8% accuracy rating on over 500,000 jobs nationwide.
- Locate and designate all underground utilities at SUE QL-B or higher to Intelligently Visualize The Built World® of your subsurface infrastructure
An ROI (return on investment) study from Penn State concluded that infrastructure construction projects that utilize subsurface utility location and designation at QL-B or higher saw $11.39 in savings for every $1.00 spent on accurate utility locating over those that did not utilize SUE QL-B or QL-A standards. GPRS supports QL-B SUE standards and has a nationwide team of SIM-certified professionals, most of whom can be on site within 24 hours.
- Require updated as builts and progress capture reporting throughout the project life-cycle
With money pouring in and timelines becoming more critical than ever, documenting each phase of your project – from updating existing subsurface and aboveground as builts to monthly progress capture – allows architects, engineers, designers, off-site prefabricators, on-site crews, and stakeholders to know what they’re working with, and whether each phase of a project is proceeding as planned. It also provides accountability and a proven record for potential liability and safety purposes. Learn how you can get a full site scan or a Jobsite+ agreement with GPRS here.
- Capture your underground utility maps and above and below ground construction project data in a secure, accessible cloud-based software platform so that you can streamline workflows, communications, and mitigate risk across the board for your project and your team.
While gathering all that important data is crucial to a project, one of the biggest issues facility managers, site supervisors, and general contractors face is how to corral and cross-reference it all so that it is immediately accessible and useable by the boots on the ground and the people in the boardroom. SiteMap® (patent pending), powered by GPRS, provides a single source of truth for project data, so that you can put the right information into the right hands, exactly when they need it.
SiteMap® can house all your project data – from a NASSCO-certified video pipe inspection report to layered utility maps, GPR concrete imaging data, and full 3D BIM model walkthroughs, all in one easy-to-use interface that allows you to secure and share your data to get the job done right
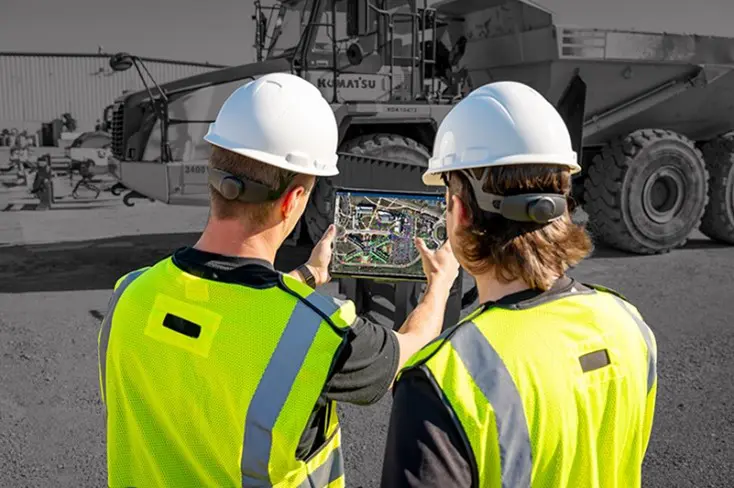
GPRS Intelligently Visualizes The Built World®, above and below ground, for the construction, engineering, architectural, and related industries to keep projects on time, on budget and safe.
Protect your project and your reputation & mitigate risk by calling GPRS.
Frequently Asked Questions
What is the concept of utility mapping?
In theory utility mapping is the process of accurately locating and digitally mapping the precise location of underground utilities. The purpose of a utility map is to provide a comprehensive record of the subsurface infrastructure of a facility. Read more about the pros and cons of utility mapping here.
What are the methods of utility survey?
SUE, Subsurface Utility Engineering, requires specific quality controls to accurately locate and map underground utilities. The technologies used for utility mapping are ground penetrating radar (GPR), electromagnetic (EM) locators, and can also include CCTV video pipe inspection for locating sanitary sewer lines with cameras, rodders, and sondes, among others. Learn more here.
What is 3D underground utility mapping?
To accurately map subsurface infrastructure data so that it can be utilized for design, engineering, and maintenance purposes, it must be processed into 3D objects. GPRS does this by accurately mapping the subsurface with GPR and EM locators, marking out the site surface with that information, then capturing those markouts with 3D photogrammetry or 3D laser scanning to create a useable 3D BIM model or conceptual site model (CSM) of the location. You can learn more about translating 3D GPR data into useable objects, here.