Whether you are a general contractor or facility manager planning renovations or modifications, or an architect or engineer who requires precise project data, GPRS provides accurate existing conditions documentation, reality capture, and scan-to-BIM services to bring your design and construction projects in on time, and on budget.
When you need accurate architectural, structural, and MEP system dimensions, locations, and layouts for design, prefabrication, clash detection, facility modifications, or asset management, call GPRS. 3D laser scanning minimizes shutdowns and disruptions, eliminates the need for site revisits, and provides accurate as-built data to reduce risk and increase project efficiency.
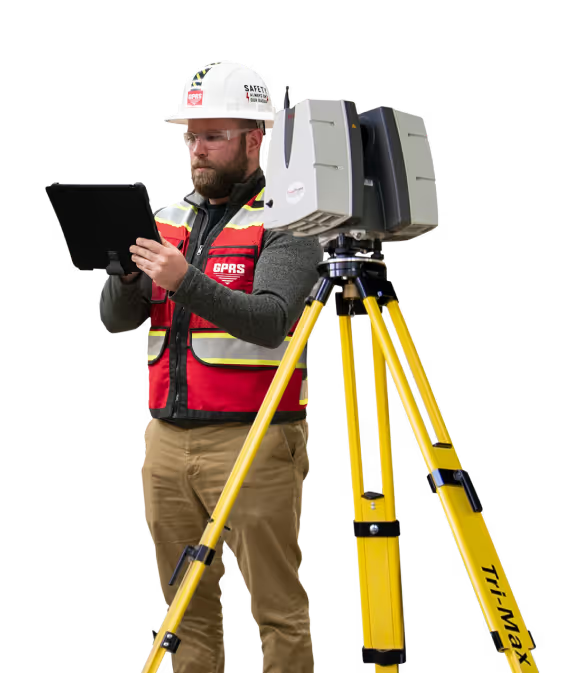
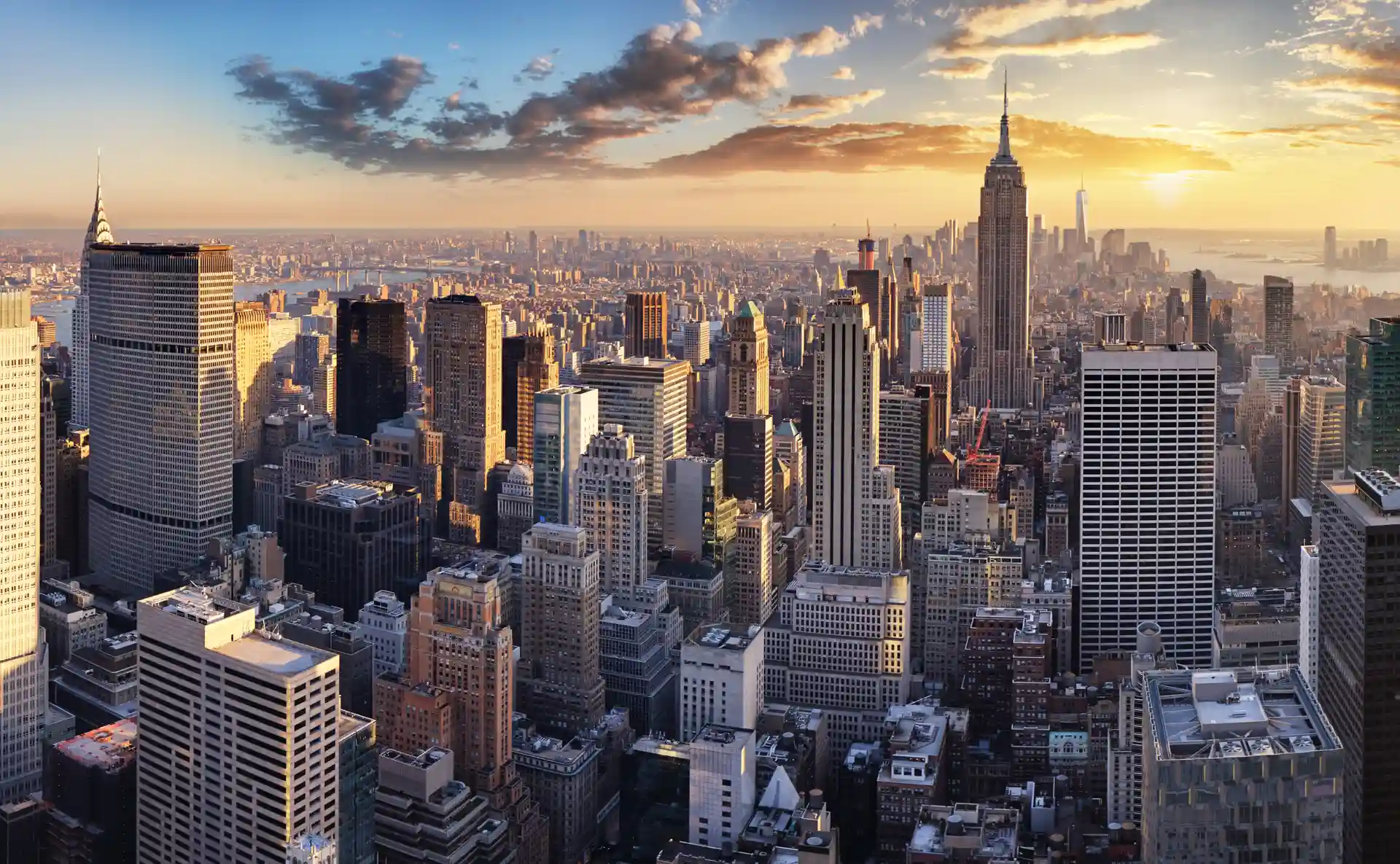
GPRS Project Managers
.avif)
.avif)
.avif)
GPRS Mapping & Modeling Team
Construction drawings and models streamline planning, visualization, and coordination on your project because they provide a single source of truth for designers, architects, engineers, and contractors. GPRS’ in-house Mapping & Modeling Team can customize as-built data, 2D CAD drawings, 3D BIM models, 3D mesh models, virtual tours via WalkThru 3D, digital twins, floor plans via FLRPLN, and more to ensure you have all the information you need to get the job done right, delivered via GPRS’ SiteMap® digital storage software and app.
Maps and models can be produced at any level of detail in a variety of formats such as Revit, AutoCAD, ReCap, Navisworks, Civil 3D, BIM360, A360, Bentley, Leica Cyclone, Cintoo, and more. We have optimized workflows for importing data, registration, creating deliverables, quality checks, and transferring data to clients.
Not sure what you need? Not a problem. Our experienced Project Managers will work closely with you to define the project scope and use the right equipment and software to accurately map and model your project to accomplish your goals.
WHY CHOOSE US?
THE GPRS DIFFERENCE.
GPRS 3D Laser Scanning Services can bring these benefits to your project:
- Collect up to two million data points per second with the highest-quality survey-grade laser scanners
- Capture exact dimensions and measurements of your project site
- Expedite planning and design with accurate as-builts
- Eliminate site disruption and revisits
- Receive precise point clouds, 2D drawings, and 3D models to improve collaboration and coordination
- Tour the location, add digital notes, and even measure with a virtual tour
- Reduce project risks, change orders, delays, accidents, and costs
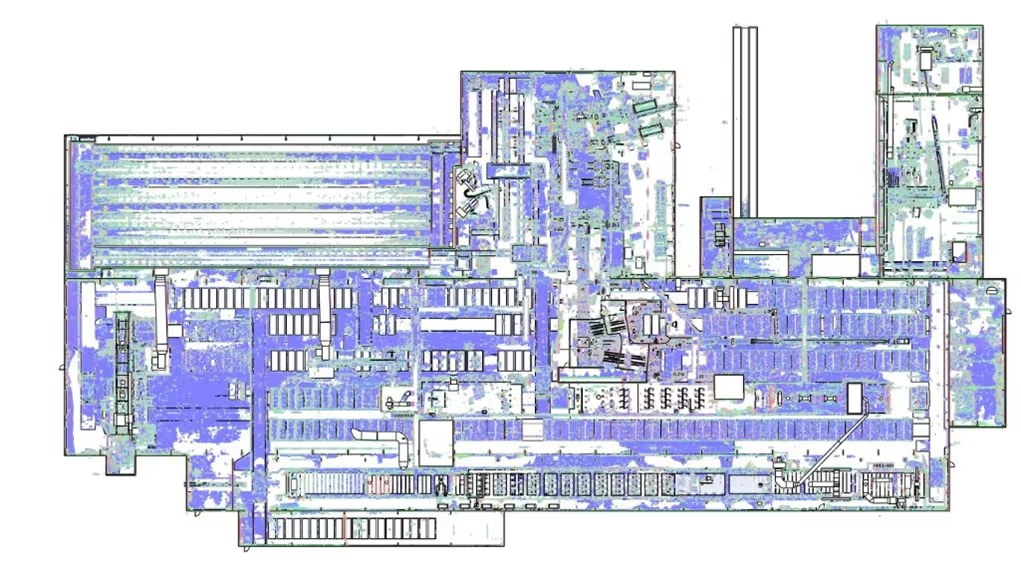
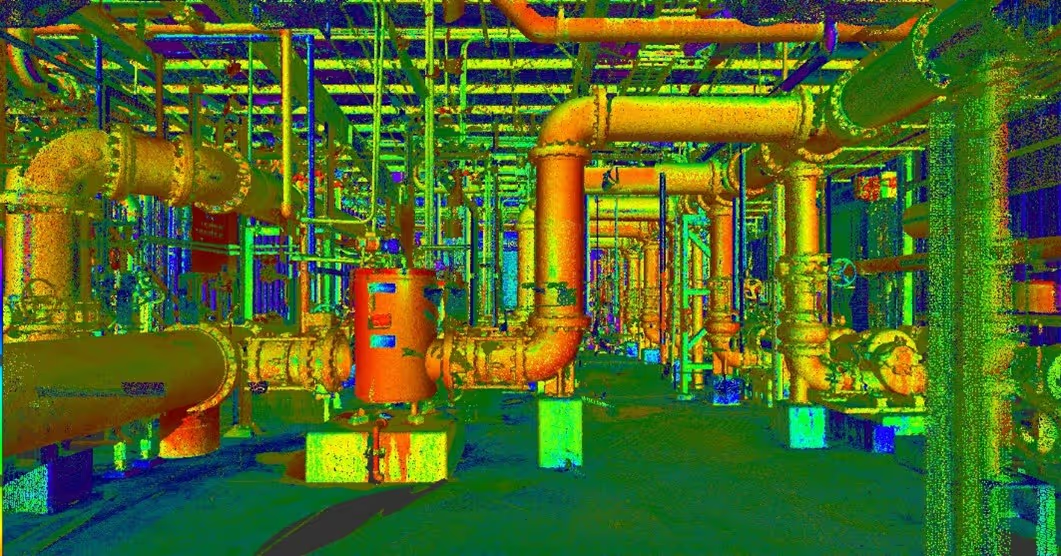
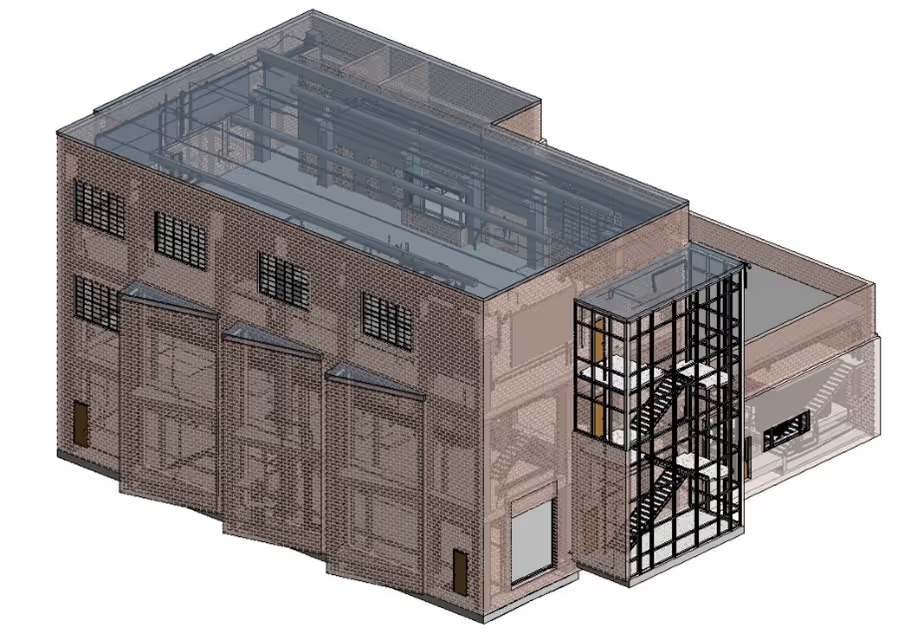
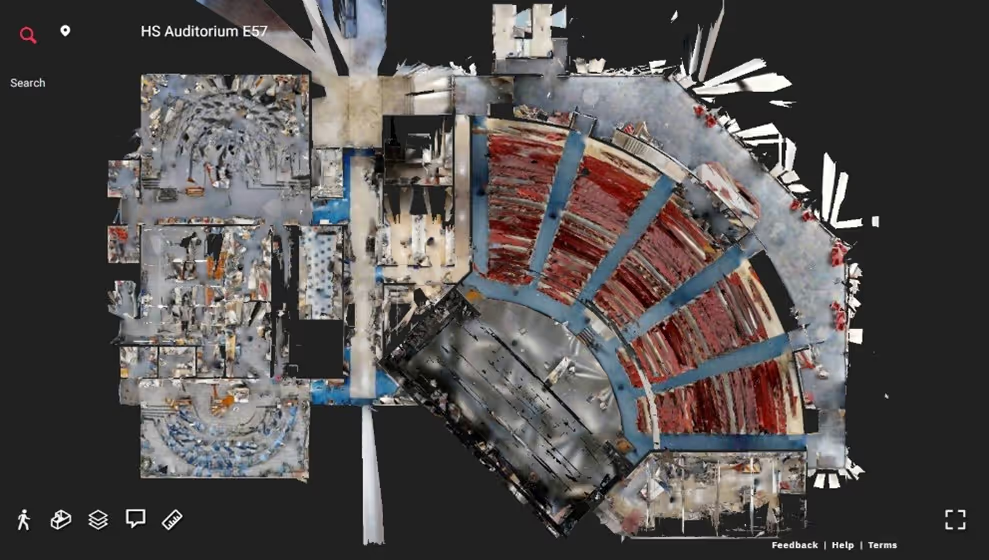
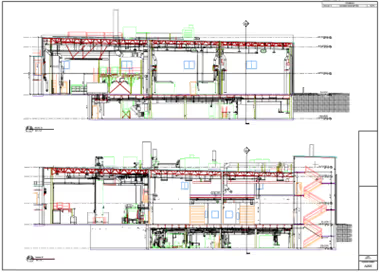
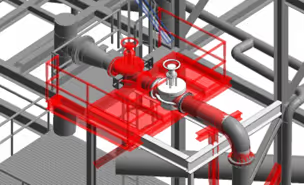
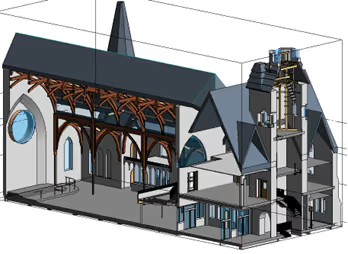
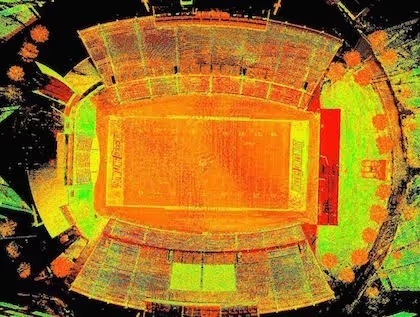
- Kings County
- Queens County
- New York County
- Suffolk County
- Nassau County
- Bronx County
- Westchester County
- Erie County
- Monroe County
- Richmond County
- New York City, New York
- Hampstead Town, New York
- Brookhaven, New York
- Islip, New York
- Oyster Bay, New York
- Buffalo, New York
- North Hampstead, New York
- Babylon Town, New York
- Rochester City, New York
- Yonkers, New York